Visual Inspection
Visual inspection is the most basic and straightforward method of testing PCBs. It involves examining the board with the naked eye or using magnifying tools to identify any visible defects or irregularities. Some common issues that can be detected through visual inspection include:
- Incorrect component placement
- Solder bridges or shorts
- Insufficient or excessive solder
- Damaged or missing components
- Contamination or foreign objects on the board
While visual inspection is a quick and cost-effective method, it is not foolproof and may miss some subtle defects. Therefore, it is typically used in conjunction with other testing methods for more comprehensive coverage.
Automated Optical Inspection (AOI)
Automated Optical Inspection (AOI) is a more advanced version of visual inspection that uses high-resolution cameras and image processing software to scan the PCB for defects. AOI systems can quickly and accurately detect a wide range of issues, such as:
- Component misalignment or rotation
- Solder defects (e.g., bridges, voids, insufficient or excessive solder)
- Incorrect or missing components
- Lifted or tombstoned components
- Damaged or contaminated pads or traces
AOI is particularly useful for high-volume production, as it can inspect boards at a much faster rate than manual methods. However, it may struggle with certain types of defects, such as those hidden under components or within connectors.
X-Ray Inspection
X-ray inspection is a non-destructive testing method that uses X-rays to create images of the internal structure of the PCB. This allows for the detection of defects that may not be visible on the surface, such as:
- Voids or cracks in solder joints
- Misaligned or shifted components
- Broken or damaged traces or vias
- Foreign objects or debris inside the board
X-ray inspection is particularly useful for examining ball grid array (BGA) packages and other components with hidden solder joints. However, it requires specialized equipment and trained operators, making it more expensive than other testing methods.
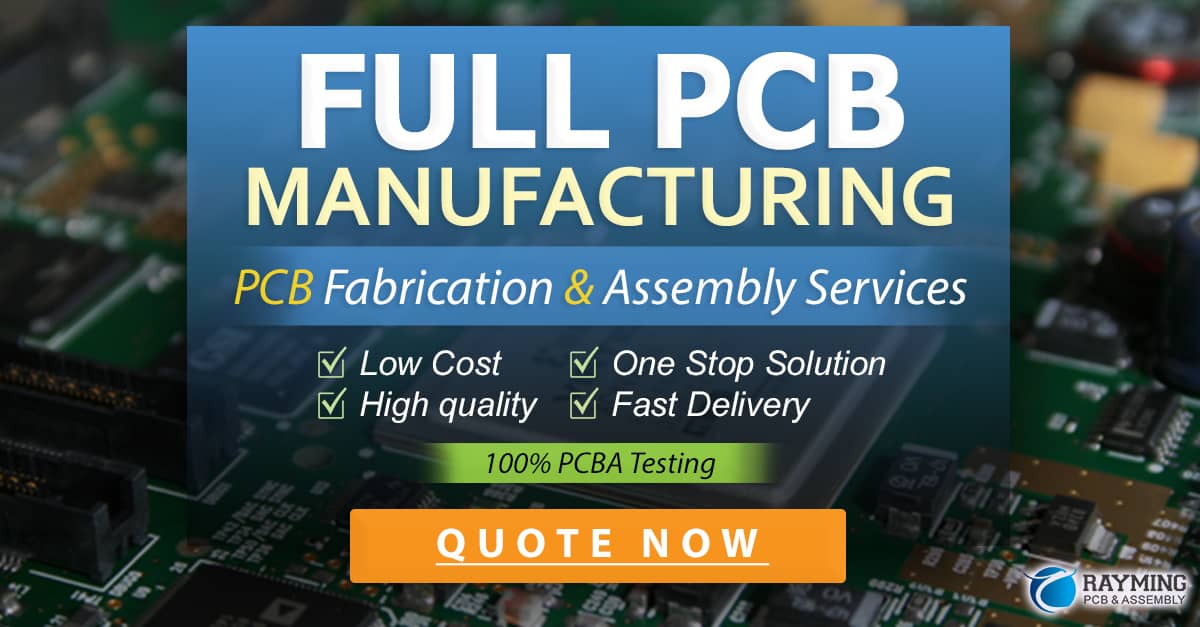
In-Circuit Testing (ICT)
In-Circuit Testing (ICT) is a method that uses a bed-of-nails fixture to make direct electrical contact with the PCB’s test points. This allows for the measurement of various electrical parameters, such as:
- Resistance
- Capacitance
- Inductance
- Diode and transistor functionality
- Short circuits and open circuits
ICT can quickly identify defects in individual components and interconnections, making it an effective method for detecting manufacturing defects. However, it requires the design of a custom test fixture for each PCB, which can be time-consuming and expensive.
Flying Probe Testing
Flying probe testing is an alternative to ICT that uses movable test probes instead of a fixed bed-of-nails fixture. The probes can be programmed to make contact with any point on the PCB, allowing for more flexibility in testing. Flying probe testing can perform many of the same measurements as ICT, such as:
- Continuity testing
- Resistance measurement
- Capacitance measurement
- Diode and transistor testing
Flying probe testing is particularly useful for low-volume production or prototypes, as it does not require the design and fabrication of a custom test fixture. However, it is generally slower than ICT and may not be suitable for high-volume production.
Boundary Scan Testing
Boundary scan testing, also known as JTAG (Joint Test Action Group) testing, is a method that uses a special test access port (TAP) built into the PCB’s components to test the interconnections between them. The TAP allows for the input and output of test signals, which can be used to verify the functionality of the board’s interconnects and detect issues such as:
- Short circuits
- Open circuits
- Stuck-at faults
- Delay faults
Boundary scan testing is particularly useful for testing complex boards with high-density interconnects, such as those used in smartphones and other portable devices. However, it requires the components to have built-in boundary scan capabilities, which may not be available in all cases.
Functional Testing
Functional testing involves powering up the PCB and testing its functionality under real-world operating conditions. This can include:
- Applying input signals and measuring output responses
- Running software or firmware tests
- Verifying communication interfaces (e.g., USB, Ethernet, HDMI)
- Testing user interface elements (e.g., buttons, switches, displays)
Functional testing is essential for ensuring that the PCB performs as intended and meets the required specifications. However, it may not detect all manufacturing defects, as some issues may not manifest themselves under normal operating conditions.
Burn-In Testing
Burn-in testing involves subjecting the PCB to elevated temperatures and voltages for an extended period to identify any early-life failures or weaknesses. This can help to weed out defective components or manufacturing defects that may cause premature failure in the field. Burn-in testing typically involves:
- Placing the PCB in a temperature-controlled chamber
- Applying power and input signals to the board
- Monitoring the board’s functionality and performance over time
Burn-in testing is particularly important for mission-critical applications, such as aerospace, military, or medical devices, where reliability is paramount. However, it can be time-consuming and expensive, as it requires specialized equipment and extended testing periods.
Environmental Testing
Environmental testing involves subjecting the PCB to various environmental conditions to ensure its robustness and reliability. This can include:
- Temperature cycling: Exposing the board to alternating high and low temperatures to test its thermal stability
- Humidity testing: Subjecting the board to high humidity levels to test its resistance to moisture
- Vibration testing: Applying mechanical vibrations to the board to test its structural integrity
- Shock testing: Subjecting the board to sudden impacts or drops to test its durability
Environmental testing is essential for PCBs that will be used in harsh or demanding environments, such as outdoor applications, industrial settings, or transportation systems. However, it requires specialized equipment and facilities, which can be costly to set up and maintain.
Electromagnetic Compatibility (EMC) Testing
Electromagnetic Compatibility (EMC) testing involves measuring the PCB’s electromagnetic emissions and susceptibility to ensure that it does not interfere with other electronic devices or be affected by external electromagnetic fields. This can include:
- Radiated emissions testing: Measuring the electromagnetic fields emitted by the PCB
- Conducted emissions testing: Measuring the electromagnetic noise conducted through the board’s power and signal lines
- Radiated immunity testing: Subjecting the board to external electromagnetic fields to test its susceptibility
- Conducted immunity testing: Injecting electromagnetic noise into the board’s power and signal lines to test its immunity
EMC testing is critical for PCBs that will be used in environments with strict electromagnetic compatibility requirements, such as medical, automotive, or aerospace applications. It requires specialized test equipment and facilities, as well as expertise in electromagnetic compatibility standards and regulations.
Accelerated Life Testing (ALT)
Accelerated Life Testing (ALT) is a method of predicting the long-term reliability of a PCB by subjecting it to elevated stress levels for a shorter period. This can involve:
- Applying higher-than-normal temperatures, voltages, or currents
- Increasing the frequency or duration of thermal or mechanical stress cycles
- Introducing environmental stressors, such as humidity or corrosive atmospheres
By analyzing the PCB’s performance and failure modes under these accelerated conditions, engineers can estimate its expected lifetime under normal operating conditions. ALT is particularly useful for products with long expected lifetimes, such as industrial equipment or infrastructure systems, where real-time testing would be impractical.
Design for Testability (DFT)
Design for Testability (DFT) is not a testing method per se, but rather a set of design principles and techniques that make a PCB easier to test and diagnose. Some common DFT techniques include:
- Adding test points or pads for probing
- Incorporating boundary scan capabilities into components
- Using built-in self-test (BIST) or built-in self-diagnosis (BISD) features
- Designing modular or hierarchical architectures that can be tested independently
By incorporating DFT principles into the PCB design process, engineers can reduce the time and cost of testing, improve test coverage, and facilitate easier debugging and repair.
Combining Multiple Test Methods
No single test method can guarantee the complete functionality and reliability of a PCB. Each method has its strengths and limitations, and may be more or less suitable depending on the specific requirements and constraints of the application. Therefore, a comprehensive PCB Testing strategy typically involves a combination of different methods, such as:
- Visual inspection and AOI for detecting surface-level defects
- X-ray inspection for examining hidden solder joints
- ICT or flying probe testing for verifying component functionality and interconnections
- Boundary scan testing for high-density interconnects
- Functional testing for ensuring overall system performance
- Environmental and EMC testing for reliability and compatibility
By using a multi-layered approach, manufacturers can achieve a high level of confidence in the quality and reliability of their PCBs, while balancing the costs and time requirements of testing.
Conclusion
PCB testing is a critical aspect of the electronics manufacturing process, ensuring that the final product meets the required quality, reliability, and performance standards. By using a combination of visual, automated, electrical, and environmental testing methods, manufacturers can detect and eliminate defects, verify functionality, and guarantee the long-term reliability of their PCBs.
As electronic devices become increasingly complex and miniaturized, the importance of effective PCB testing will only continue to grow. By staying up-to-date with the latest testing technologies and best practices, electronics manufacturers can stay competitive in a rapidly evolving industry and deliver high-quality products to their customers.
FAQ
What are the most common defects found during PCB testing?
Some of the most common defects found during PCB testing include:
- Solder bridges or shorts
- Insufficient or excessive solder
- Component misalignment or rotation
- Missing or incorrect components
- Damaged or Lifted Pads or traces
- Voids or cracks in solder joints
How much does PCB testing cost?
The cost of PCB testing varies depending on the complexity of the board, the testing methods used, and the volume of production. In general, more advanced testing methods, such as X-ray inspection or environmental testing, tend to be more expensive than basic methods like visual inspection. However, the cost of testing should be weighed against the potential cost of defects or failures in the final product.
Can all defects be detected through testing?
While a comprehensive testing strategy can detect a wide range of defects, it is not possible to guarantee that all defects will be caught. Some defects, such as intermittent faults or design flaws, may not be detectable through standard testing methods. Additionally, some defects may only manifest themselves under specific operating conditions or after extended use. Therefore, it is important to have a robust quality control process that includes not only testing, but also good design practices, process controls, and post-manufacturing monitoring.
How long does PCB testing take?
The duration of PCB testing depends on the complexity of the board, the testing methods used, and the number of boards being tested. Simple tests, such as visual inspection or AOI, can be completed in a matter of seconds or minutes per board. More advanced tests, such as ICT or functional testing, may take several minutes to an hour or more per board. Burn-in testing and environmental testing can take several hours or even days, depending on the test conditions and requirements.
What are the benefits of incorporating Design for Testability (DFT) into PCB design?
Incorporating DFT principles into PCB design can provide several benefits, including:
- Reduced testing time and cost, as the board is designed to be easily accessible and testable
- Improved test coverage, as more test points and features are built into the board
- Easier debugging and repair, as the board is designed to be modular and easily diagnosable
- Higher quality and reliability, as potential defects or weaknesses are identified and addressed early in the design process
By considering testability from the outset, designers can create PCBs that are not only functional and reliable, but also easier and more cost-effective to manufacture and maintain.
Test Method | Strengths | Limitations |
---|---|---|
Visual Inspection | – Quick and inexpensive – Can detect obvious defects |
– May miss subtle or hidden defects – Subjective and prone to human error |
Automated Optical Inspection (AOI) | – Fast and accurate – Can detect a wide range of defects – Suitable for high-volume production |
– May struggle with hidden or obscured defects – Requires specialized equipment and software |
X-Ray Inspection | – Can detect internal defects and hidden solder joints – Non-destructive |
– Expensive equipment and skilled operators required – May not detect all types of defects |
In-Circuit Testing (ICT) | – Can quickly identify component and interconnect defects – Provides comprehensive coverage |
– Requires custom test fixtures for each PCB – May not detect all functional defects |
Flying Probe Testing | – Flexible and adaptable – No custom fixtures required – Suitable for low-volume or prototype testing |
– Slower than ICT – May not be suitable for high-volume production |
Boundary Scan Testing | – Effective for testing high-density interconnects – Does not require physical access to components |
– Requires components with built-in boundary scan capabilities – May not detect all types of defects |
Functional Testing | – Tests the PCB under real-world operating conditions – Ensures that the PCB meets functional requirements |
– May not detect all manufacturing defects – Requires the development of test cases and procedures |
Burn-In Testing | – Identifies early-life failures and weaknesses – Important for mission-critical applications |
– Time-consuming and expensive – Requires specialized equipment and facilities |
Environmental Testing | – Ensures the PCB’s robustness and reliability under various conditions – Important for harsh or demanding environments |
– Requires specialized equipment and facilities – Can be costly and time-consuming |
Electromagnetic Compatibility (EMC) Testing | – Ensures the PCB does not interfere with or be affected by electromagnetic fields – Critical for applications with strict EMC requirements |
– Requires specialized equipment and facilities – Requires expertise in EMC standards and regulations |
Accelerated Life Testing (ALT) | – Predicts the long-term reliability of the PCB – Useful for products with long expected lifetimes |
– Requires careful design and analysis of test conditions – May not fully replicate real-world conditions |
Design for Testability (DFT) | – Makes the PCB easier to test and diagnose – Reduces testing time and cost – Improves test coverage and facilitates debugging |
– Requires additional design effort and resources – May impact the PCB’s size, cost, or performance |
0 Comments