Introduction
Printed Circuit Boards (PCBs) are the backbone of modern electronics, connecting components and enabling the functionality of devices we use every day. However, the complex manufacturing process of PCBs can lead to various defects that impact the board’s performance, reliability, and overall quality. In this article, we’ll explore ten common reasons for PCB manufacturing defects and discuss strategies to eliminate them, ensuring the production of high-quality PCBs.
Reasons for PCB Defects
1. Incorrect Design
Design Errors
One of the primary reasons for PCB defects is incorrect design. Design errors can include:
- Incorrect component placement
- Inadequate clearance between components
- Improper trace routing
- Insufficient copper thickness
- Incorrect drill hole sizes
These errors can lead to short circuits, open circuits, and signal integrity issues, compromising the PCB’s performance and reliability.
How to Eliminate Design Errors
To minimize design errors, consider the following:
- Use PCB design software with built-in design rule checks (DRC) to identify and correct errors before manufacturing.
- Follow industry-standard design guidelines and best practices.
- Collaborate with experienced PCB designers and engineers to review and validate designs.
- Conduct thorough design reviews and simulations to identify potential issues.
2. Contamination
Sources of Contamination
Contamination during the PCB manufacturing process can lead to defects such as:
- Shorts between traces
- Poor solderability
- Delamination
- Reduced insulation resistance
Common sources of contamination include:
- Dust and debris
- Oils and greases from handling
- Chemical residues from cleaning processes
- Airborne particles in the manufacturing environment
Eliminating Contamination
To reduce contamination-related defects:
- Maintain a clean and controlled manufacturing environment with proper air filtration and particle control.
- Use clean room protocols, including personal protective equipment (PPE) and regular cleaning of equipment and surfaces.
- Implement strict handling procedures to minimize exposure to contaminants.
- Use high-quality, contaminant-free materials and chemicals in the manufacturing process.
3. Incorrect Material Selection
Material Properties
Using incorrect materials can lead to PCB defects such as:
- Delamination
- Warping
- Reduced thermal and electrical performance
- Decreased reliability
Key material properties to consider include:
- Dielectric constant
- Glass transition temperature (Tg)
- Coefficient of thermal expansion (CTE)
- Moisture absorption
- Flame retardancy
Selecting the Right Materials
To avoid material-related defects:
- Choose materials that meet the specific requirements of the application, considering factors such as operating temperature, humidity, and mechanical stress.
- Work with reputable material suppliers to ensure the use of high-quality, consistent materials.
- Follow the manufacturer’s recommendations for processing and handling materials.
- Conduct material testing and qualification to verify performance and compatibility.
4. Manufacturing Process Variations
Process Control
Variations in the manufacturing process can introduce defects such as:
- Inconsistent etching
- Uneven plating thickness
- Misregistration of layers
- Inconsistent hole drilling
These defects can impact the PCB’s electrical performance, signal integrity, and reliability.
Controlling Process Variations
To minimize process variations:
- Implement statistical process control (SPC) to monitor and control critical process parameters.
- Use automated equipment with closed-loop feedback control to maintain consistent process conditions.
- Regularly calibrate and maintain manufacturing equipment to ensure optimal performance.
- Train operators on proper equipment usage and process control techniques.
5. Inadequate Testing and Inspection
Quality Control
Insufficient testing and inspection during the manufacturing process can allow defects to go undetected, leading to:
- Reduced yield
- Increased rework and scrap
- Potential field failures
Common testing and inspection methods include:
- Automated optical inspection (AOI)
- X-ray inspection
- Electrical testing (e.g., flying probe, in-circuit testing)
- Visual inspection
Improving Testing and Inspection
To enhance testing and inspection:
- Implement a comprehensive quality control plan that includes multiple inspection points throughout the manufacturing process.
- Invest in advanced testing and inspection equipment, such as 3D AOI and X-ray systems.
- Develop detailed inspection criteria and train personnel on defect identification and classification.
- Conduct regular audits and reviews of testing and inspection processes to identify areas for improvement.
6. Incorrect Handling and Storage
Environmental Factors
Improper handling and storage of PCBs can lead to defects such as:
- Warping
- Cracking
- Oxidation
- Delamination
Environmental factors that can impact PCBs include:
- Temperature
- Humidity
- Electrostatic discharge (ESD)
- Mechanical stress
Proper Handling and Storage
To minimize handling and storage-related defects:
- Follow industry-standard guidelines for PCB Handling and storage, such as IPC-1601.
- Use ESD-safe packaging and handling procedures to prevent damage from static discharge.
- Store PCBs in a controlled environment with stable temperature and humidity levels.
- Minimize mechanical stress during handling and transportation, using appropriate packaging and support materials.
7. Inadequate Documentation and Communication
Information Flow
Poor documentation and communication can lead to PCB defects by:
- Causing misinterpretation of design intent
- Leading to incorrect process setup and execution
- Hindering effective problem-solving and root cause analysis
Key documentation and communication elements include:
- Design files and specifications
- Manufacturing process instructions
- Quality control plans and inspection criteria
- Change management procedures
Improving Documentation and Communication
To enhance documentation and communication:
- Establish clear and comprehensive documentation standards for design, manufacturing, and quality control.
- Use version control systems to manage design files and ensure all stakeholders are working with the latest information.
- Implement a robust change management process to communicate and track changes throughout the product lifecycle.
- Foster open communication channels between design, manufacturing, and quality teams to facilitate problem-solving and continuous improvement.
8. Insufficient Supplier Management
Supplier Quality
Issues with suppliers can introduce PCB defects through:
- Inconsistent material quality
- Delays in material delivery
- Inadequate process control at the supplier’s facility
Supplier management factors to consider include:
- Supplier selection and qualification
- Quality agreements and specifications
- Supplier audits and performance monitoring
- Incoming material inspection and testing
Strengthening Supplier Management
To minimize supplier-related defects:
- Develop a rigorous supplier selection and qualification process, considering factors such as quality systems, process capabilities, and track record.
- Establish clear quality agreements and specifications with suppliers, outlining requirements for material properties, process control, and documentation.
- Conduct regular supplier audits and performance reviews to ensure ongoing compliance and continuous improvement.
- Implement incoming material inspection and testing to verify the quality of supplied materials before use in production.
9. Lack of Training and Expertise
Skills and Knowledge
A lack of training and expertise among personnel can lead to PCB defects due to:
- Incorrect operation of manufacturing equipment
- Misinterpretation of design intent and specifications
- Inadequate problem-solving and root cause analysis skills
Key areas for training and expertise development include:
- PCB design principles and best practices
- Manufacturing process fundamentals
- Quality control and inspection techniques
- Problem-solving and root cause analysis methodologies
Enhancing Training and Expertise
To improve the skills and knowledge of personnel:
- Develop a comprehensive training program that covers all aspects of PCB design, manufacturing, and quality control.
- Encourage cross-functional collaboration and knowledge sharing between teams to foster a culture of continuous learning.
- Invest in ongoing professional development opportunities, such as workshops, seminars, and certification programs.
- Implement a mentorship program to transfer knowledge from experienced personnel to new hires and less experienced team members.
10. Insufficient Process Monitoring and Control
Process Variability
Insufficient process monitoring and control can lead to PCB defects by:
- Allowing process parameters to drift outside of acceptable ranges
- Failing to detect and correct process issues in a timely manner
- Hindering the identification and elimination of root causes
Key process monitoring and control elements include:
- Statistical process control (SPC)
- Real-time process monitoring and data collection
- Automated feedback and control systems
- Root cause analysis and corrective action procedures
Enhancing Process Monitoring and Control
To improve process monitoring and control:
- Implement a comprehensive SPC program to monitor critical process parameters and detect variations.
- Invest in real-time process monitoring and data collection systems to provide visibility into process performance.
- Use automated feedback and control systems to maintain process stability and minimize human error.
- Establish a robust root cause analysis and corrective action process to identify and eliminate the underlying causes of defects.
Frequently Asked Questions (FAQ)
1. What are the most common PCB manufacturing defects?
Some of the most common PCB manufacturing defects include shorts and opens, poor solderability, contamination, delamination, and misregistration of layers. These defects can be caused by various factors, such as design errors, process variations, contamination, and incorrect material selection.
2. How can PCB design errors be minimized?
PCB design errors can be minimized by using PCB design software with built-in design rule checks (DRC), following industry-standard design guidelines and best practices, collaborating with experienced PCB designers and engineers, and conducting thorough design reviews and simulations.
3. What role does testing and inspection play in ensuring PCB Quality?
Testing and inspection are critical for ensuring PCB quality by detecting defects and preventing them from reaching the end-user. A comprehensive quality control plan should include multiple inspection points throughout the manufacturing process, using advanced testing and inspection equipment such as automated optical inspection (AOI), X-ray inspection, and electrical testing.
4. How can supplier management help reduce PCB defects?
Effective supplier management can help reduce PCB defects by ensuring consistent material quality, timely delivery, and adequate process control at the supplier’s facility. This can be achieved through rigorous supplier selection and qualification, clear quality agreements and specifications, regular supplier audits and performance monitoring, and incoming material inspection and testing.
5. What are the benefits of implementing statistical process control (SPC) in PCB manufacturing?
Implementing statistical process control (SPC) in PCB manufacturing can help minimize process variations and improve overall quality by monitoring critical process parameters, detecting variations, and enabling timely corrective actions. SPC can also facilitate the identification and elimination of root causes, leading to continuous process improvement.
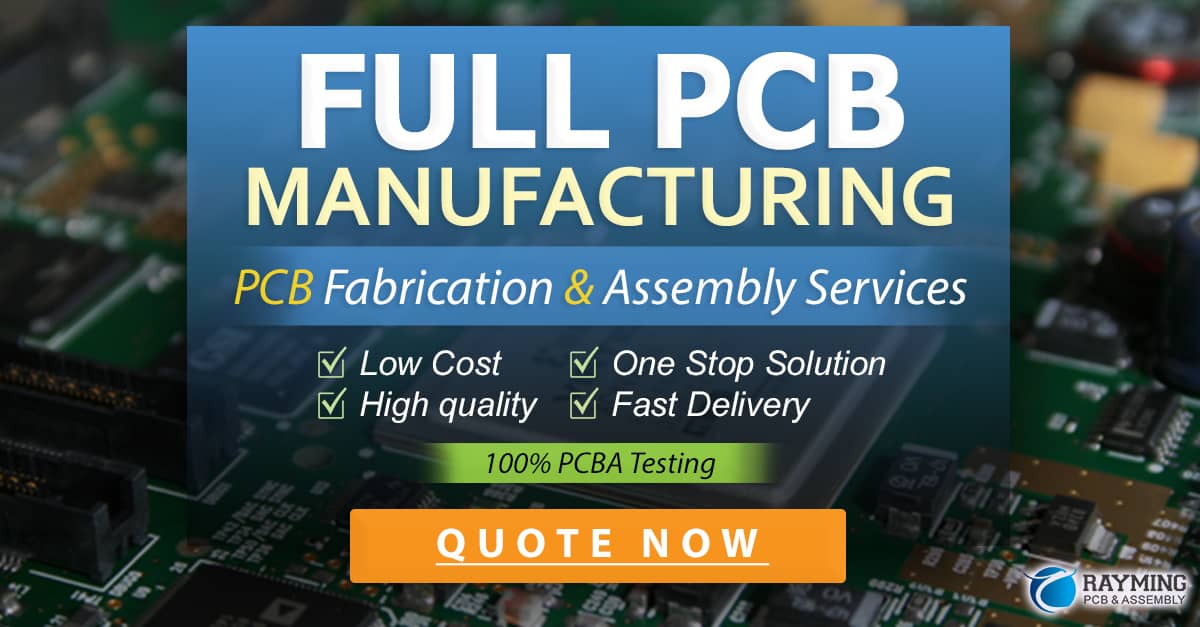
Conclusion
PCB manufacturing defects can have a significant impact on the performance, reliability, and overall quality of electronic devices. By understanding the common reasons for these defects and implementing strategies to eliminate them, manufacturers can produce high-quality PCBs that meet the demands of today’s complex electronic systems.
Key strategies for reducing PCB defects include:
- Ensuring accurate and error-free PCB designs
- Maintaining a clean and controlled manufacturing environment
- Selecting appropriate materials and following proper handling and storage procedures
- Implementing robust testing and inspection processes
- Fostering effective documentation and communication practices
- Strengthening supplier management and incoming material quality control
- Investing in training and expertise development for personnel
- Enhancing process monitoring and control through SPC and automated systems
By adopting these strategies and continuously improving their processes, PCB manufacturers can minimize defects, increase yield, and deliver high-quality products to their customers.
0 Comments