Understanding 10 Layer PCBs
What is a 10 Layer PCB?
A 10 layer PCB is a printed circuit board that consists of ten conductive layers laminated together with insulating material. These layers are interconnected through vias, which are small holes drilled through the board and plated with conductive material. The increased number of layers allows for higher component density, improved signal integrity, and better thermal management compared to PCBs with fewer layers.
Benefits of 10 Layer PCBs
- High Density: With ten layers available for component placement and routing, 10 layer PCBs enable the design of compact, high-density electronics.
- Enhanced Signal Integrity: The additional layers provide more space for power and ground planes, reducing electromagnetic interference (EMI) and improving signal quality.
- Improved Thermal Management: Multiple layers allow for better heat dissipation, which is crucial for high-power applications.
- Increased Functionality: The increased number of layers enables the integration of more complex circuitry and functionality into a single board.
Applications of 10 Layer PCBs
10 layer PCBs find applications in various industries and products, including:
- High-performance computing systems
- Telecommunications equipment
- Medical devices
- Aerospace and defense electronics
- Automotive electronics
- Industrial control systems
Factors to Consider When Choosing a 10 Layer PCB Manufacturer
1. Technical Capabilities
When selecting a 10 layer PCB manufacturer, it is essential to assess their technical capabilities. Look for manufacturers with experience in producing complex, Multi-layer Boards and a proven track record of delivering high-quality products. Consider the following aspects:
- Manufacturing Equipment: Ensure that the manufacturer has state-of-the-art equipment capable of handling the precision and complexity required for 10 layer PCBs.
- Quality Control: Inquire about the manufacturer’s quality control processes, including automated optical inspection (AOI), X-ray inspection, and electrical testing.
- Material Selection: Choose a manufacturer that offers a wide range of high-quality materials, such as FR-4, high-Tg laminates, and advanced dielectrics, to meet your specific requirements.
2. Industry Certifications and Standards
When dealing with complex PCBs, it is crucial to work with a manufacturer that adheres to industry standards and holds relevant certifications. Some key certifications to look for include:
- ISO 9001: Quality management system certification ensures that the manufacturer follows established processes to consistently deliver high-quality products.
- UL Certification: Underwriters Laboratories (UL) certification demonstrates that the manufacturer’s PCBs meet safety and performance standards.
- IPC Standards: Ensure that the manufacturer follows IPC standards, such as IPC-A-600 for acceptability of printed boards and IPC-6012 for qualification and performance specifications.
3. Design Support and Expertise
Choosing a manufacturer that offers comprehensive design support can streamline your project and help you avoid costly mistakes. Look for the following services:
- Design Review: A thorough design review process can identify potential issues early in the development cycle, saving time and resources.
- DFM Analysis: Design for Manufacturability (DFM) analysis ensures that your design can be efficiently manufactured, minimizing the risk of defects and delays.
- Technical Support: Readily available technical support from experienced engineers can help you navigate the complexities of 10 layer PCB design and manufacturing.
4. Manufacturing Capabilities and Capacity
Assess the manufacturer’s capabilities and capacity to ensure they can meet your project’s specific requirements:
- Layer Count: Confirm that the manufacturer has experience in producing 10 layer PCBs and can handle the required Layer Stack-Up.
- Board Size: Ensure that the manufacturer can accommodate your desired board size and any specific dimensional requirements.
- Minimum Feature Size: Verify that the manufacturer can achieve the required trace widths, spacing, and hole sizes for your design.
- Production Volume: Choose a manufacturer that can handle your anticipated production volumes, whether you need prototypes, small batches, or large-scale production.
5. Lead Time and Turnaround
In today’s fast-paced market, timely delivery is essential. When selecting a 10 layer PCB manufacturer, consider their lead times and turnaround capabilities:
- Standard Lead Times: Inquire about the manufacturer’s standard lead times for 10 layer PCBs and whether they can accommodate your project timeline.
- Expedited Services: If you require faster turnaround, look for manufacturers that offer expedited services without compromising quality.
- On-Time Delivery: Assess the manufacturer’s track record of meeting delivery commitments to ensure your project stays on schedule.
6. Cost and Pricing
While cost is an important factor, it should not be the sole deciding criterion when choosing a 10 layer PCB manufacturer. Consider the following aspects:
- Cost-Quality Balance: Prioritize manufacturers that offer competitive pricing without compromising on quality. Cheapest options may lead to inferior products and costly rework.
- Volume Pricing: Inquire about volume pricing options if you anticipate larger production runs, as this can help you optimize your budget.
- Hidden Costs: Be aware of any hidden costs, such as tooling fees, non-recurring engineering (NRE) charges, or minimum order quantities (MOQs), which can impact your overall project cost.
7. Communication and Support
Effective communication and reliable support are essential for a successful partnership with your PCB manufacturer. Consider the following factors:
- Responsiveness: Choose a manufacturer that is responsive to your inquiries and provides timely updates on your project’s progress.
- Language Proficiency: If you are working with an international manufacturer, ensure that their team has a good command of your preferred language to avoid miscommunications.
- Customer Service: Look for manufacturers with dedicated customer service teams that can address your concerns and provide support throughout the project lifecycle.
Evaluating and Comparing 10 Layer PCB Manufacturers
Once you have a clear understanding of your project requirements and the key factors to consider, it’s time to evaluate and compare potential 10 layer PCB manufacturers. Follow these steps to make an informed decision:
- Research and Shortlist: Conduct thorough research and create a shortlist of manufacturers that meet your initial criteria, such as technical capabilities, certifications, and industry experience.
- Request Quotes and Samples: Reach out to the shortlisted manufacturers with your project details and request quotes and sample boards. This will give you a better understanding of their pricing, quality, and responsiveness.
- Evaluate Capabilities: Assess each manufacturer’s capabilities based on the factors discussed earlier, such as manufacturing equipment, quality control processes, and design support.
- Review Certifications and References: Verify the manufacturers’ certifications and request references from previous clients to gauge their reputation and reliability.
- Compare and Negotiate: Compare the quotes, capabilities, and overall value proposition of each manufacturer. Don’t hesitate to negotiate terms, such as pricing, lead times, or support services, to ensure the best fit for your project.
- Make an Informed Decision: Based on your evaluation, select the 10 layer PCB manufacturer that best aligns with your project requirements, budget, and long-term goals.
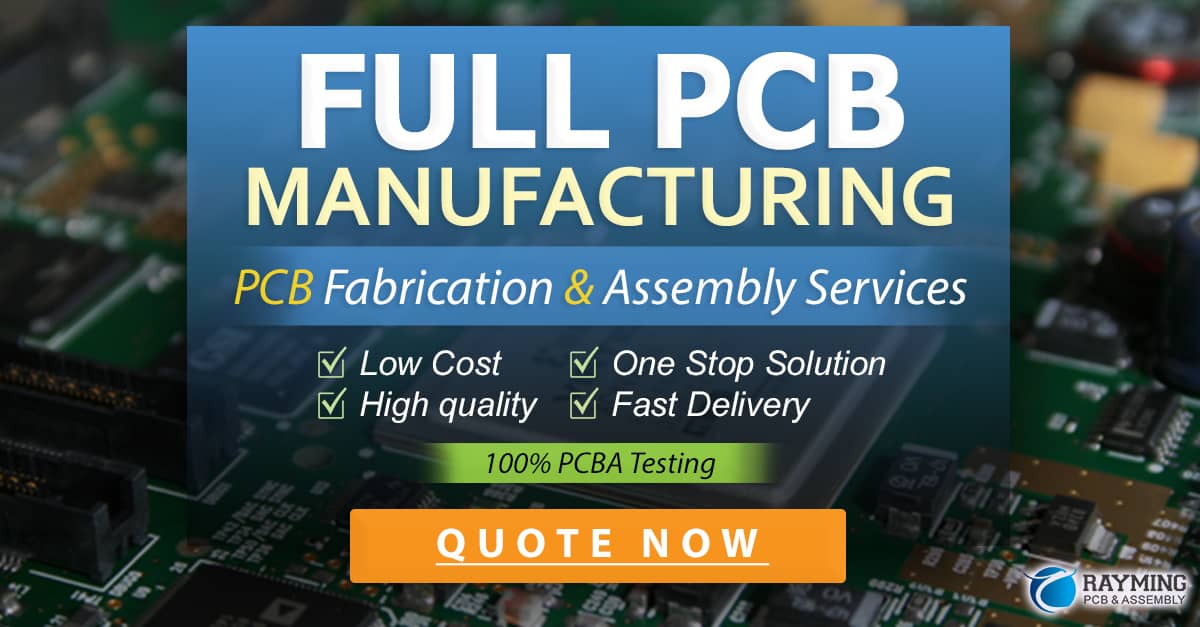
FAQs
-
What is the typical turnaround time for a 10 layer PCB Prototype?
The turnaround time for a 10 layer PCB prototype can vary depending on the manufacturer and the complexity of your design. On average, expect a lead time of 2-3 weeks for prototypes, although some manufacturers may offer expedited services for faster turnaround. -
How much does a 10 layer PCB cost compared to a 4 or 6 layer PCB?
The cost of a 10 layer PCB is generally higher than that of a 4 or 6 layer PCB due to the increased complexity and material requirements. However, the exact cost difference depends on factors such as board size, quantity, and the manufacturer’s pricing structure. It’s best to request quotes from multiple manufacturers to compare costs. -
Can I use a 10 layer PCB for high-frequency applications?
Yes, 10 layer PCBs are well-suited for high-frequency applications. The additional layers allow for better signal integrity, reduced crosstalk, and improved power distribution, which are crucial for high-frequency designs. However, it’s essential to work with a manufacturer experienced in high-frequency PCB design and manufacturing to ensure optimal performance. -
What are the common challenges in 10 layer PCB manufacturing, and how can they be addressed?
Some common challenges in 10 layer PCB manufacturing include maintaining proper layer registration, ensuring reliable via connections, and managing signal integrity. These challenges can be addressed by working with an experienced manufacturer who follows strict quality control processes, uses advanced manufacturing equipment, and provides comprehensive design support to optimize your layout for manufacturability. -
How do I ensure the reliability and longevity of my 10 layer PCB?
To ensure the reliability and longevity of your 10 layer PCB, consider the following: - Choose high-quality materials that meet your application’s requirements, such as temperature resistance and signal integrity.
- Work with a reputable manufacturer that follows industry standards and has a proven track record of producing reliable PCBs.
- Implement a robust design with proper signal integrity techniques, such as appropriate layer stack-up, ground planes, and impedance control.
- Conduct thorough testing and quality assurance processes to identify and address any potential issues before final production.
Conclusion
Choosing the right 10 layer PCB manufacturer is a critical decision that can significantly impact the success of your project. By understanding the key factors to consider, such as technical capabilities, certifications, design support, manufacturing capacity, lead times, and cost, you can make an informed choice that aligns with your project requirements and goals.
Remember to thoroughly evaluate and compare potential manufacturers, request samples and references, and prioritize a balance between quality, reliability, and cost. By partnering with the right 10 layer PCB manufacturer, you can bring your complex, high-performance electronics to life with confidence.
Factor | Key Considerations |
---|---|
Technical Capabilities | – Manufacturing equipment – Quality control processes – Material selection |
Industry Certifications | – ISO 9001 – UL Certification – IPC Standards |
Design Support and Expertise | – Design review – DFM analysis – Technical support |
Manufacturing Capabilities | – Layer count – Board size – Minimum feature size – Production volume |
Lead Time and Turnaround | – Standard lead times – Expedited services – On-time delivery |
Cost and Pricing | – Cost-quality balance – Volume pricing – Hidden costs |
Communication and Support | – Responsiveness – Language proficiency – Customer service |
By carefully considering these factors and following the evaluation process outlined in this guide, you can select a 10 layer PCB manufacturer that will be a reliable partner in bringing your complex electronics projects to fruition.
0 Comments