Introduction to Soldering PCB inspection
Soldering PCB (Printed Circuit Board) inspection is a critical process in electronics manufacturing to ensure the quality and reliability of the final product. Defects in soldering can lead to malfunctions, reduced performance, and even safety hazards. Therefore, it is essential to have a thorough inspection process in place to identify and rectify any soldering defects before the PCB is assembled into the final product.
In this article, we will discuss 10 helpful ways to check for defects on soldering PCB Boards. These methods range from visual inspection to advanced techniques using specialized equipment. By implementing these inspection techniques, manufacturers can improve the quality of their soldering process and minimize the risk of defects in their final products.
The Importance of Soldering PCB Inspection
Soldering PCB inspection plays a crucial role in ensuring the quality and reliability of electronic products. Here are some key reasons why soldering PCB inspection is important:
-
Identifying Defects: Soldering PCB inspection helps identify various types of defects such as bridging, insufficient solder, lifted pads, and more. By detecting these defects early in the manufacturing process, corrective actions can be taken to prevent them from affecting the final product.
-
Improving Reliability: Properly soldered connections are essential for the reliable functioning of electronic devices. Defects in soldering can lead to intermittent failures, reduced performance, and even complete device failure. By ensuring the quality of soldering through inspection, manufacturers can improve the reliability of their products.
-
Ensuring Safety: Soldering defects can also pose safety risks, especially in critical applications such as medical devices, automotive electronics, and aerospace systems. Shorts, opens, or improper connections caused by soldering defects can lead to overheating, fire hazards, or malfunctions that endanger user safety. Thorough inspection helps identify and mitigate these risks.
-
Reducing Rework and Costs: Identifying soldering defects early in the manufacturing process allows for timely rework and corrections. This prevents defective PCBs from progressing further down the assembly line, saving time and costs associated with rework at later stages or after the product is shipped to customers.
-
Meeting Quality Standards: Many industries have specific quality standards and regulations that electronic products must adhere to. Soldering PCB inspection helps manufacturers meet these standards by ensuring the consistency and quality of their soldering processes. This is particularly important for products that require certifications or approvals from regulatory bodies.
-
Continuous Process Improvement: Soldering PCB inspection provides valuable data and insights into the soldering process. By analyzing the types and frequencies of defects found during inspection, manufacturers can identify areas for improvement in their soldering procedures, equipment, or materials. This continuous process improvement helps enhance overall manufacturing efficiency and product quality.
In summary, soldering PCB inspection is a vital step in electronics manufacturing that contributes to product quality, reliability, safety, cost reduction, and compliance with industry standards. Investing in effective inspection methods and technologies is crucial for manufacturers to ensure the success and competitiveness of their products in the market.
10 Helpful Ways to Check Defects on Soldering PCB Board
1. Visual Inspection
Visual inspection is the most basic and commonly used method for checking soldering defects on PCB boards. It involves using the naked eye or magnifying lenses to examine the soldered joints for any visible abnormalities. Here are some key aspects to look for during visual inspection:
- Solder Joint Appearance: Check for uniform and shiny solder joints. Dull, grainy, or irregular surfaces may indicate poor wetting or contamination.
- Solder Amount: Ensure that the solder amount is appropriate for each joint. Insufficient solder can lead to weak connections, while excess solder may cause bridging or shorts.
- Component Placement: Verify that components are properly aligned and seated on the pads. Misaligned or tilted components can cause soldering issues.
- Solder Bridging: Look for any solder bridges or shorts between adjacent pads or traces.
- Lifted Pads or Components: Check for any lifted pads or components that may have detached from the PCB surface during soldering.
While visual inspection is a quick and accessible method, it has limitations in detecting smaller or hidden defects. It also relies on the skill and experience of the inspector to identify potential issues accurately.
2. Automated Optical Inspection (AOI)
Automated Optical Inspection (AOI) is a more advanced method that uses computer vision and image processing techniques to inspect soldering defects on PCB boards. AOI systems capture high-resolution images of the PCB and compare them against predefined templates or criteria to identify any deviations or anomalies. Here are some advantages of using AOI for soldering PCB inspection:
- High Speed: AOI systems can inspect PCBs at a much faster rate compared to manual visual inspection, making it suitable for high-volume production.
- Consistency: AOI provides consistent and objective inspection results, eliminating the variability associated with human judgment.
- Defect Detection: AOI can detect a wide range of soldering defects, including bridging, insufficient solder, lifted leads, tombstoning, and more.
- Data Collection: AOI systems generate detailed inspection data and reports, enabling traceability and process improvement analysis.
However, AOI systems require precise setup, programming, and maintenance to ensure accurate defect detection. False positives or false negatives can occur if the system is not properly calibrated or if the inspection criteria are not well-defined.
3. X-Ray Inspection
X-ray inspection is a non-destructive testing method that uses X-rays to visualize the internal structure of soldered joints on PCB boards. It is particularly useful for inspecting hidden or obscured solder joints, such as those under Ball Grid Array (BGA) packages or within multi-layer boards. Here are some benefits of X-ray inspection for soldering PCB inspection:
- Void Detection: X-ray inspection can reveal voids or air pockets within solder joints, which can compromise the strength and reliability of the connection.
- Solder Ball Inspection: For BGA packages, X-ray inspection allows for the examination of solder ball integrity, including shape, size, and alignment.
- Crack Detection: X-rays can detect cracks or fractures within solder joints that may not be visible from the surface.
- Thickness Measurement: X-ray systems can measure the thickness of solder layers, helping to ensure compliance with manufacturing specifications.
X-ray inspection requires specialized equipment and trained operators to interpret the images accurately. It may also have limitations in detecting certain types of defects, such as cold solder joints or insufficient wetting.
4. In-Circuit Testing (ICT)
In-Circuit Testing (ICT) is a functional testing method that verifies the electrical connectivity and component functionality of soldered PCBs. ICT systems use a bed-of-nails fixture that makes contact with specific test points on the PCB and applies electrical signals to check for shorts, opens, resistance, capacitance, and other parameters. Here are some advantages of using ICT for soldering PCB inspection:
- Comprehensive Testing: ICT can test for a wide range of electrical characteristics and component functionality, ensuring the overall integrity of the soldered PCB.
- Fault Isolation: ICT can pinpoint specific faults or defects, making it easier to identify and rectify issues.
- Automated Testing: ICT systems can perform tests automatically, reducing manual intervention and increasing testing speed.
- Early Defect Detection: ICT can catch soldering defects and component issues early in the manufacturing process, preventing defective boards from progressing further.
However, ICT requires the design and fabrication of specific test fixtures for each PCB, which can be time-consuming and costly. It may also have limitations in testing certain types of components or high-density PCBs with limited access to test points.
5. Boundary Scan Testing
Boundary Scan Testing, also known as JTAG (Joint Test Action Group) testing, is a method that utilizes the built-in test circuitry of integrated circuits (ICs) to test the interconnections and functionality of soldered PCBs. It involves accessing and controlling the boundary scan cells within the ICs to apply test patterns and capture the responses. Here are some benefits of boundary scan testing for soldering PCB inspection:
- Interconnect Testing: Boundary scan testing can verify the integrity of solder connections between ICs and other components on the PCB.
- Non-Contact Testing: Unlike ICT, boundary scan testing does not require physical contact with the PCB, making it suitable for testing high-density or fine-pitch components.
- Programmability: Boundary scan tests can be easily programmed and modified using software tools, allowing for flexibility in test coverage and adaptation to design changes.
- Fault Diagnosis: Boundary scan testing can provide detailed fault information, helping to isolate and diagnose specific soldering or component issues.
However, boundary scan testing requires the presence of boundary scan-compliant ICs on the PCB, which may not be available in all designs. It also has limitations in testing analog components or non-boundary scan devices.
6. Flying Probe Testing
Flying Probe Testing is a non-contact electrical testing method that uses movable probes to access and test specific points on the soldered PCB. The probes are programmed to move across the PCB surface and make contact with the desired test points to perform electrical measurements and functional tests. Here are some advantages of flying probe testing for soldering PCB inspection:
- Flexibility: Flying probe testing can adapt to different PCB layouts and designs without requiring specific test fixtures.
- High Precision: The probes can access small and fine-pitch test points accurately, making it suitable for testing high-density PCBs.
- Selective Testing: Flying probe testing allows for selective testing of specific areas or components on the PCB, saving time and resources.
- Fault Isolation: The probes can perform detailed electrical measurements to isolate and diagnose soldering defects or component issues.
However, flying probe testing may have longer test times compared to other methods due to the sequential nature of probe movement. It also requires precise probe alignment and calibration to ensure accurate and repeatable measurements.
7. Thermal Imaging
Thermal imaging is a non-contact inspection method that uses infrared cameras to visualize the heat distribution on soldered PCBs. It can detect thermal anomalies or hot spots that may indicate soldering defects or component issues. Here are some applications of thermal imaging for soldering PCB inspection:
- Solder Joint Evaluation: Thermal imaging can reveal uneven heat distribution or excessive heat generation at solder joints, which may indicate poor soldering or insufficient heat dissipation.
- Component Inspection: Thermal imaging can detect overheating components or abnormal thermal patterns, helping to identify potential component failures or soldering issues.
- Thermal Stress Analysis: By monitoring the thermal behavior of the PCB under different operating conditions, thermal imaging can help assess the thermal stress and reliability of soldered connections.
- Process Optimization: Thermal imaging can provide insights into the soldering process, allowing for optimization of soldering parameters, such as temperature profiles and dwell times.
Thermal imaging requires specialized infrared cameras and software for data analysis and interpretation. It is important to consider factors such as emissivity, ambient temperature, and surface conditions when interpreting thermal images accurately.
8. Cross-Sectioning
Cross-sectioning is a destructive testing method that involves cutting the soldered PCB to examine the internal structure and quality of solder joints. It provides a detailed view of the solder joint cross-section, allowing for the assessment of solder penetration, intermetallic formation, and any internal defects. Here are some aspects that can be evaluated through cross-sectioning:
- Solder Joint Geometry: Cross-sectioning reveals the shape, size, and fillets of the solder joint, helping to assess its mechanical strength and reliability.
- Intermetallic Layers: The formation and thickness of intermetallic layers between the solder and the component leads or pads can be examined to evaluate the metallurgical bonding and long-term reliability.
- Void Analysis: Cross-sectioning can expose any voids or air pockets within the solder joint, which can compromise its strength and electrical conductivity.
- Solder Penetration: The extent of solder penetration into through-holes or between component leads can be assessed to ensure proper mechanical and electrical connections.
Cross-sectioning requires careful sample preparation, including cutting, mounting, grinding, and polishing, to obtain a clear and representative view of the solder joint. It is a destructive method and is typically used for failure analysis or quality control purposes on a limited number of samples.
9. Solderability Testing
Solderability testing is a method that evaluates the ability of component leads, pads, or surfaces to be effectively soldered. It assesses the wettability, spread, and adhesion of solder to the surface, which are critical factors for achieving reliable solder joints. Here are some common solderability tests:
- Wetting Balance Test: This test measures the wetting force and time of a component lead or surface when dipped into molten solder. It provides quantitative data on the solderability characteristics.
- Spread Test: The spread test evaluates the ability of solder to spread and form a uniform coating on a surface. It can be performed by applying a controlled amount of solder and measuring the spread area.
- Dip and Look Test: In this test, the component leads or surfaces are dipped into molten solder and then visually inspected for solder coverage, wetting, and any defects.
- Edge Dip Test: This test assesses the solderability of the edges of PCBs or components by dipping them into molten solder and evaluating the solder wetting and coverage.
Solderability testing is important for ensuring the compatibility and reliability of components and surfaces before the actual soldering process. It helps identify any surface contamination, oxidation, or other factors that may hinder proper solder wetting and adhesion.
10. Microsectioning
Microsectioning is a specialized cross-sectioning technique that involves mounting, grinding, and polishing the solder joint sample to obtain a highly detailed view of its internal structure. It allows for microscopic examination of the solder joint at high magnifications, revealing fine details and defects. Here are some aspects that can be analyzed through microsectioning:
- Intermetallic Compound (IMC) Formation: Microsectioning can reveal the formation, thickness, and uniformity of IMC layers at the solder-substrate interface, which are critical for the mechanical and electrical integrity of the joint.
- Grain Structure: The grain structure of the solder can be examined to assess its mechanical properties and potential for fatigue or crack propagation.
- Solder Voids: Microsectioning can detect and measure the size, shape, and distribution of voids within the solder joint, which can affect its strength and reliability.
- Crack Analysis: Any cracks or fractures within the solder joint can be closely examined to determine their origin, propagation, and potential impact on joint integrity.
Microsectioning requires specialized equipment, such as precision cutting tools, mounting resins, grinding and polishing machines, and microscopes. It is a time-consuming and skill-intensive process that demands expertise in sample preparation and analysis.
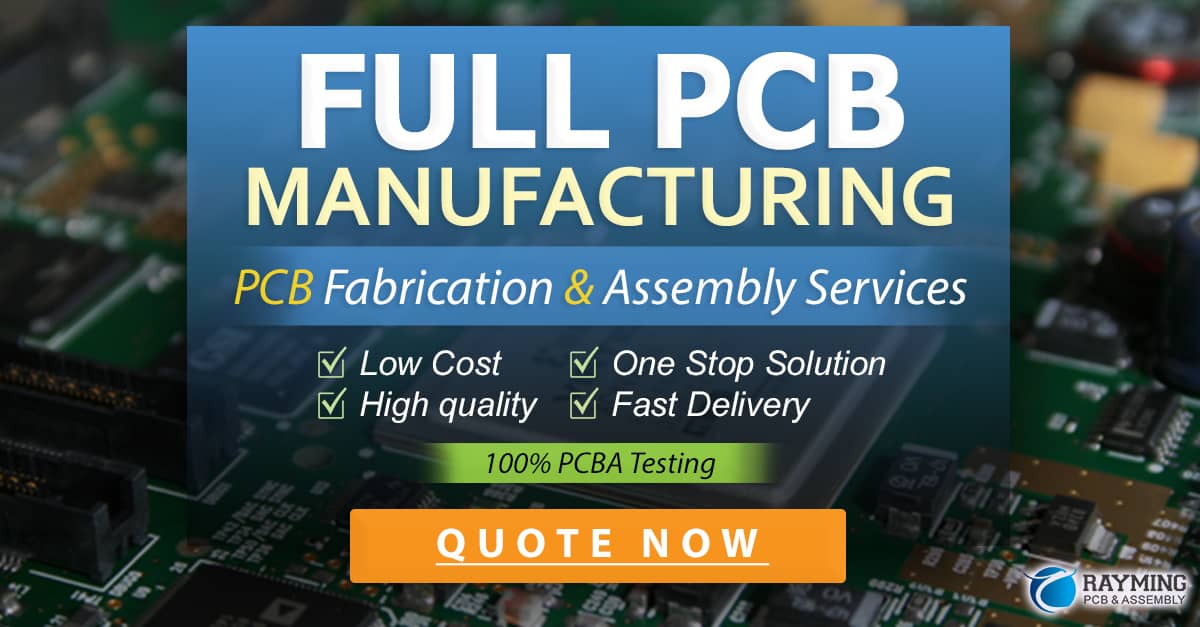
Frequently Asked Questions (FAQ)
1. What are the most common soldering defects on PCB boards?
Some of the most common soldering defects on PCB boards include:
– Bridging: Unintended connection between two or more solder joints due to excess solder.
– Insufficient solder: Lack of adequate solder, resulting in weak or open connections.
– Cold solder joints: Dull, grainy, or cracked solder joints caused by improper heating or contamination.
– Lifted pads or components: Detachment of pads or components from the PCB surface during soldering.
– Solder balls: Small, spherical solder particles that can cause shorts or unintended connections.
2. How can I prevent soldering defects on PCB boards?
To prevent soldering defects on PCB boards, consider the following practices:
– Use appropriate soldering techniques, such as proper temperature control and solder amount.
– Ensure cleanliness of the PCB surface and components before soldering.
– Follow the recommended soldering profiles and parameters for the specific components and Solder Types.
– Implement process controls, such as temperature monitoring and inspection checkpoints.
– Provide adequate training and guidelines for soldering operators to maintain consistency and quality.
3. What equipment is needed for soldering PCB inspection?
The equipment needed for soldering PCB inspection depends on the specific inspection methods used. Some common equipment includes:
– Magnifying lenses or microscopes for visual inspection.
– Automated Optical Inspection (AOI) systems for high-speed, automated visual inspection.
– X-ray inspection systems for examining hidden or obscured solder joints.
– In-Circuit Testing (ICT) systems for electrical connectivity and component functionality testing.
– Flying probe testers for non-contact electrical testing.
– Thermal imaging cameras for detecting thermal anomalies or hot spots.
– Cross-sectioning and microsectioning equipment for destructive analysis of solder joints.
4. How often should soldering PCB inspection be performed?
The frequency of soldering PCB inspection depends on various factors, such as production volume, product complexity, quality requirements, and process stability. Here are some general guidelines:
– For high-volume production, in-line inspection methods like AO
0 Comments