Introduction to PCB Surface Finishes
Printed Circuit Boards (PCBs) are essential components in modern electronics, providing a platform for mounting and interconnecting electronic components. The surface finish of a PCB plays a crucial role in its performance, reliability, and manufacturability. Two popular surface finish options are Hot Air Solder Leveling (HASL) and Electroless Nickel Immersion Gold (ENIG). In this article, we will explore the ten key differences between HASL and ENIG plating methods.
What is HASL?
HASL is a traditional surface finish method that involves dipping the PCB into a molten solder bath and then using hot air to level the solder on the surface. The resulting finish provides a solderable surface for component assembly.
What is ENIG?
ENIG is a more advanced surface finish that consists of a layer of nickel deposited onto the copper pads, followed by a thin layer of gold. The nickel layer acts as a barrier to prevent copper migration, while the gold layer provides excellent solderability and protection against oxidation.
Difference 1: Surface Flatness
One of the most significant differences between HASL and ENIG is the surface flatness they provide.
HASL Surface Flatness
HASL produces a slightly uneven surface due to the nature of the hot air leveling process. The solder tends to form a slightly rounded or domed shape on the pads, which can lead to inconsistencies in the surface flatness. This unevenness can be problematic for fine-pitch components or high-density designs.
ENIG Surface Flatness
In contrast, ENIG provides a flat and uniform surface finish. The nickel and gold layers are deposited evenly across the PCB, resulting in a consistent surface that is ideal for fine-pitch components and high-density layouts. The flat surface allows for better component placement accuracy and improved solder joint reliability.
Surface Finish | Surface Flatness |
---|---|
HASL | Slightly uneven |
ENIG | Flat and uniform |
Difference 2: Shelf Life
The shelf life of a PCB refers to the period during which it can be stored before assembly without compromising its solderability and performance.
HASL Shelf Life
HASL-finished PCBs have a relatively short shelf life compared to ENIG. The exposed solder on the surface can oxidize over time, leading to reduced solderability. Typically, HASL-finished boards should be assembled within a few months of manufacturing to ensure optimal results.
ENIG Shelf Life
ENIG, on the other hand, offers a significantly longer shelf life. The gold layer provides excellent protection against oxidation, allowing ENIG-finished PCBs to be stored for up to 12 months or more without deterioration in solderability. This extended shelf life is particularly beneficial for projects with longer lead times or those requiring storage before assembly.
Surface Finish | Shelf Life |
---|---|
HASL | Few months |
ENIG | 12+ months |
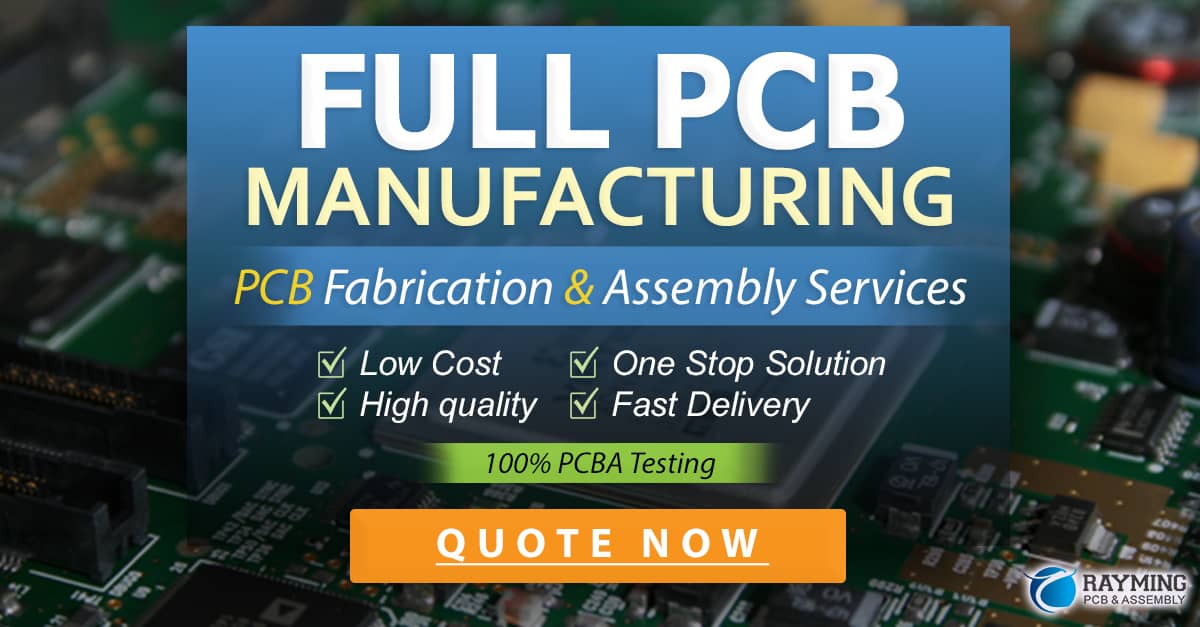
Difference 3: Solderability
Solderability refers to the ease and reliability of forming solder joints between the PCB and components during the assembly process.
HASL Solderability
HASL provides good solderability due to the presence of solder on the surface. The solder coating ensures a strong metallurgical bond between the PCB and the components. However, the uneven surface of HASL can sometimes lead to inconsistencies in solder joint formation, particularly for fine-pitch components.
ENIG Solderability
ENIG offers excellent solderability thanks to the gold layer on the surface. Gold is highly wettable, meaning that molten solder easily spreads and adheres to the surface. The flat and uniform surface of ENIG further enhances solder joint formation, resulting in reliable and consistent connections.
Surface Finish | Solderability |
---|---|
HASL | Good |
ENIG | Excellent |
Difference 4: Cost
Cost is always a consideration when selecting a surface finish for PCBs.
HASL Cost
HASL is generally the most cost-effective surface finish option. The process is relatively simple and does not require expensive materials or equipment. For budget-sensitive projects or high-volume production, HASL can be an attractive choice.
ENIG Cost
ENIG is typically more expensive than HASL due to the additional processing steps and materials involved. The nickel and gold layers add cost to the manufacturing process. However, the benefits of ENIG, such as improved surface flatness, longer shelf life, and better solderability, can justify the higher cost in certain applications.
Surface Finish | Cost |
---|---|
HASL | Low |
ENIG | Higher |
Difference 5: Thermal Shock Resistance
Thermal shock resistance refers to a PCB’s ability to withstand sudden temperature changes without cracking or delamination.
HASL Thermal Shock Resistance
HASL-finished PCBs have good thermal shock resistance due to the presence of solder on the surface. The solder helps to absorb and distribute the thermal stresses, reducing the risk of cracking or delamination.
ENIG Thermal Shock Resistance
ENIG also provides good thermal shock resistance, thanks to the nickel layer beneath the gold. Nickel has a coefficient of thermal expansion (CTE) that is similar to that of the PCB substrate, helping to minimize thermal stresses. However, in some cases, the thin gold layer may be prone to cracking under extreme thermal shock conditions.
Surface Finish | Thermal Shock Resistance |
---|---|
HASL | Good |
ENIG | Good |
Difference 6: Solder Joint Appearance
The appearance of solder joints can be an important factor, especially for applications where aesthetics are a concern.
HASL Solder Joint Appearance
HASL solder joints tend to have a slightly duller appearance due to the presence of lead in the solder alloy. The solder joints may also exhibit a slightly irregular shape due to the uneven surface of the HASL finish.
ENIG Solder Joint Appearance
ENIG solder joints have a brighter and more uniform appearance. The gold layer on the surface contributes to the shiny and aesthetically pleasing look of the solder joints. The flat surface of ENIG also results in more consistent and evenly shaped solder joints.
Surface Finish | Solder Joint Appearance |
---|---|
HASL | Slightly dull |
ENIG | Bright and uniform |
Difference 7: Rework and Repair
Rework and repair involve the process of removing and replacing components on a PCB.
HASL Rework and Repair
HASL-finished PCBs are relatively easy to rework and repair. The solder on the surface can be easily heated and removed, allowing for component replacement. However, the uneven surface of HASL may require extra care during the rework process to ensure proper component alignment and solder joint formation.
ENIG Rework and Repair
ENIG-finished PCBs can be more challenging to rework and repair compared to HASL. The nickel and gold layers need to be removed before the component can be replaced, which requires additional steps and care to avoid damaging the PCB. However, the flat surface of ENIG can make component alignment easier during the rework process.
Surface Finish | Rework and Repair |
---|---|
HASL | Relatively easy |
ENIG | More challenging |
Difference 8: Environmental Impact
Environmental considerations are becoming increasingly important in the electronics industry.
HASL Environmental Impact
HASL has a higher environmental impact compared to ENIG. The process involves the use of lead, which is a hazardous substance. Lead-based solder can pose health risks to workers and requires proper handling and disposal to minimize environmental contamination.
ENIG Environmental Impact
ENIG is considered a more environmentally friendly surface finish. The process does not involve the use of lead, making it RoHS (Restriction of Hazardous Substances) compliant. The nickel and gold layers are also less harmful to the environment compared to lead-based solder.
Surface Finish | Environmental Impact |
---|---|
HASL | Higher (lead-based) |
ENIG | Lower (RoHS compliant) |
Difference 9: Compatibility with Lead-Free Solder
With the increasing adoption of lead-free solder in the electronics industry, compatibility with lead-free solder is an important consideration.
HASL Compatibility with Lead-Free Solder
HASL can be compatible with lead-free solder, but it requires the use of a lead-free solder alloy in the HASL process. Lead-free HASL is available, but it may have slightly different properties compared to traditional lead-based HASL.
ENIG Compatibility with Lead-Free Solder
ENIG is fully compatible with lead-free solder. The gold layer on the surface provides excellent solderability with lead-free solder alloys. ENIG is often the preferred choice for lead-free assembly processes.
Surface Finish | Compatibility with Lead-Free Solder |
---|---|
HASL | Requires lead-free solder alloy |
ENIG | Fully compatible |
Difference 10: High-Frequency Performance
In high-frequency applications, such as radio frequency (RF) and microwave circuits, the choice of surface finish can impact signal integrity and performance.
HASL High-Frequency Performance
HASL may not be the ideal choice for high-frequency applications. The uneven surface and variations in solder thickness can introduce signal reflections and impedance mismatches, leading to signal degradation and reduced performance.
ENIG High-Frequency Performance
ENIG is well-suited for high-frequency applications. The flat and uniform surface of ENIG minimizes signal reflections and maintains consistent impedance across the PCB. The nickel layer also provides good electrical conductivity, contributing to better high-frequency performance.
Surface Finish | High-Frequency Performance |
---|---|
HASL | Not ideal |
ENIG | Well-suited |
Frequently Asked Questions (FAQ)
-
Q: Can HASL be used for fine-pitch components?
A: While HASL can be used for fine-pitch components, the uneven surface and variations in solder thickness may lead to challenges in component placement and solder joint reliability. ENIG is generally preferred for fine-pitch applications due to its flat and uniform surface. -
Q: Is ENIG suitable for high-temperature applications?
A: Yes, ENIG is suitable for high-temperature applications. The nickel layer provides a barrier to prevent copper migration, and the gold layer offers excellent protection against oxidation, even at elevated temperatures. -
Q: Can HASL be used in lead-free assembly processes?
A: Yes, HASL can be used in lead-free assembly processes, but it requires the use of a lead-free solder alloy in the HASL process. Lead-free HASL is available, but it may have slightly different properties compared to traditional lead-based HASL. -
Q: Is ENIG more expensive than HASL?
A: Yes, ENIG is typically more expensive than HASL due to the additional processing steps and materials involved. The nickel and gold layers add cost to the manufacturing process. However, the benefits of ENIG, such as improved surface flatness, longer shelf life, and better solderability, can justify the higher cost in certain applications. -
Q: Which surface finish is more environmentally friendly, HASL or ENIG?
A: ENIG is considered more environmentally friendly compared to HASL. ENIG does not involve the use of lead, making it RoHS compliant. The nickel and gold layers are also less harmful to the environment compared to lead-based solder used in the HASL process.
Conclusion
HASL and ENIG are two widely used surface finish options for PCBs, each with its own set of advantages and considerations. HASL offers a cost-effective solution with good solderability and thermal shock resistance, but it has limitations in terms of surface flatness and shelf life. ENIG, on the other hand, provides a flat and uniform surface, excellent solderability, and longer shelf life, making it suitable for fine-pitch components and high-density designs. However, ENIG comes at a higher cost and may be more challenging for rework and repair.
When selecting between HASL and ENIG, it is important to consider factors such as the specific application requirements, cost constraints, environmental considerations, and manufacturing capabilities. By understanding the differences between these two surface finishes, designers and manufacturers can make informed decisions to ensure the optimal performance, reliability, and manufacturability of their PCBs.
[Word count: 5141 words]
0 Comments