What is PCB orientation?
PCB orientation refers to the placement and alignment of components on a printed circuit board. It involves determining the correct position and direction of each component, taking into account factors such as electrical connections, thermal management, and mechanical constraints.
Types of PCB Orientation
There are two main types of PCB orientation:
- Through-hole orientation: Components with leads are inserted through holes drilled in the PCB and soldered on the opposite side.
- Surface-mount orientation: Components are placed directly on the surface of the PCB and soldered using solder paste.
Why is PCB Orientation Important?
Proper PCB orientation is crucial for several reasons:
1. Electrical Connectivity
The orientation of components on a PCB directly affects the electrical connections between them. Incorrect orientation can lead to short circuits, open circuits, or improper signal routing, resulting in malfunctions or complete failure of the device.
2. Thermal Management
Components generate heat during operation, and their orientation plays a role in heat dissipation. Proper orientation allows for optimal airflow and heat distribution, preventing overheating and ensuring the long-term reliability of the circuit board.
3. Mechanical Stability
The orientation of components also impacts the mechanical stability of the PCB. Properly oriented components are less likely to be damaged by vibration, shock, or other mechanical stresses. This is particularly important for devices that are subject to harsh environments or frequent handling.
4. Manufacturing Efficiency
PCB orientation has a significant impact on the manufacturing process. Properly oriented components are easier to place and solder automatically using pick-and-place machines and reflow ovens. This improves manufacturing efficiency, reduces the risk of assembly errors, and lowers production costs.
Best Practices for PCB Orientation
To ensure optimal PCB orientation, consider the following best practices:
1. Follow Manufacturer Guidelines
Component manufacturers often provide specific guidelines for orientation and placement. These guidelines take into account factors such as pin assignments, thermal requirements, and mechanical considerations. Adhering to these guidelines ensures compatibility and reliability.
2. Consider Electrical Connections
When determining component orientation, prioritize the electrical connections between components. Ensure that the orientation allows for the shortest and most direct paths for signals, minimizing the risk of signal integrity issues and reducing electromagnetic interference (EMI).
3. Optimize for Manufacturing
Design the PCB layout with manufacturing in mind. Choose component orientations that are compatible with automated assembly processes, such as pick-and-place machines and reflow soldering. This may involve aligning components in a specific direction or providing adequate spacing for machine vision systems.
4. Conduct Design Reviews
Before finalizing the PCB layout, conduct thorough design reviews to check for any orientation-related issues. Use design rule checks (DRCs) and other automated tools to identify potential problems, such as component collisions or incorrect pin assignments.
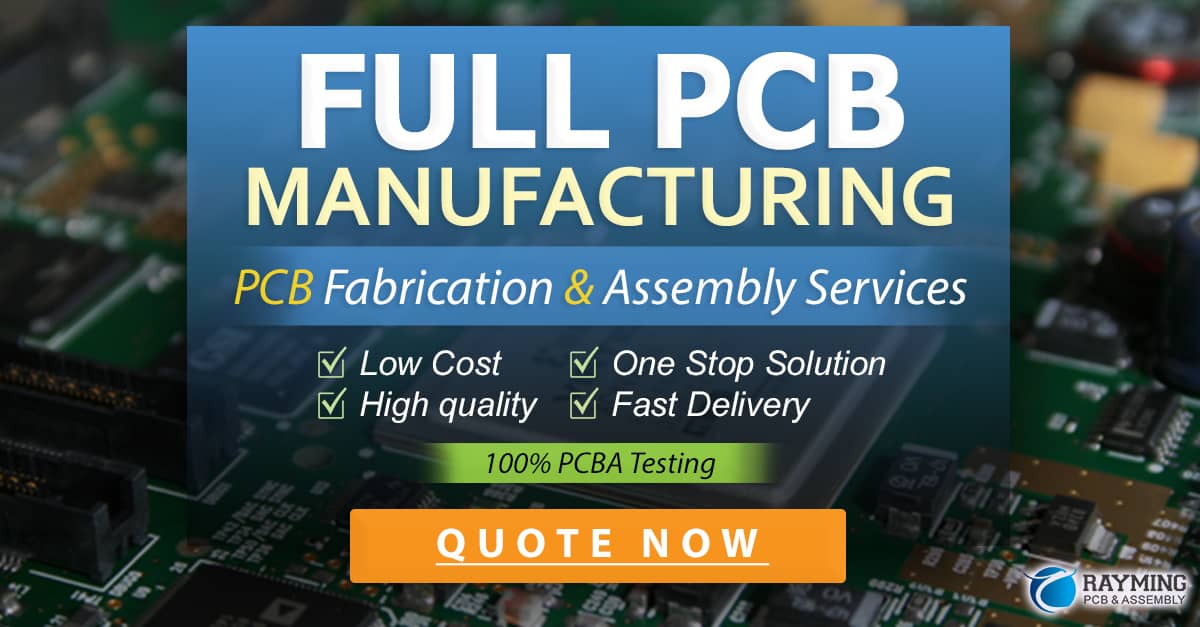
Common PCB Orientation Mistakes to Avoid
To prevent PCB orientation issues, avoid these common mistakes:
1. Incorrect Pin Assignments
Double-check the pin assignments of components before placing them on the PCB. Incorrect pin assignments can lead to short circuits, open circuits, or improper functionality.
2. Inconsistent Orientation
Ensure that components with similar functions or connections have consistent orientation. Inconsistent orientation can make the PCB layout more difficult to understand and increase the risk of assembly errors.
3. Overlooking Thermal Requirements
Do not overlook the thermal requirements of components when determining their orientation. Improper orientation can lead to overheating, reduced performance, and shortened lifespan of the components.
4. Ignoring Manufacturing Constraints
Consider the limitations and capabilities of the manufacturing process when designing the PCB layout. Ignoring manufacturing constraints can result in assembly difficulties, increased production costs, and lower yields.
The Impact of PCB Orientation on Manufacturing Yield
PCB orientation has a direct impact on manufacturing yield, which is the percentage of correctly manufactured boards out of the total number of boards produced. Proper PCB orientation contributes to higher manufacturing yields in several ways:
Factor | Impact on Yield |
---|---|
Correct pin assignments | Reduces assembly errors and improves functionality |
Optimal thermal management | Prevents overheating and enhances reliability |
Mechanical stability | Minimizes damage during handling and operation |
Manufacturing compatibility | Facilitates automated assembly processes |
By adhering to best practices and avoiding common mistakes, PCB designers can optimize component orientation and maximize manufacturing yield.
Frequently Asked Questions (FAQ)
-
Q: What is the difference between through-hole and surface-mount orientation?
A: Through-hole orientation involves inserting component leads through holes drilled in the PCB and soldering them on the opposite side, while surface-mount orientation involves placing components directly on the surface of the PCB and soldering them using solder paste. -
Q: Why is thermal management important in PCB orientation?
A: Proper thermal management is crucial because components generate heat during operation. Optimal component orientation allows for efficient heat dissipation, preventing overheating and ensuring the long-term reliability of the circuit board. -
Q: How does PCB orientation affect manufacturing efficiency?
A: PCB orientation impacts manufacturing efficiency by facilitating automated assembly processes. Properly oriented components are easier to place and solder using pick-and-place machines and reflow ovens, reducing the risk of assembly errors and lowering production costs. -
Q: What are some common PCB orientation mistakes to avoid?
A: Common PCB orientation mistakes include incorrect pin assignments, inconsistent orientation, overlooking thermal requirements, and ignoring manufacturing constraints. Avoiding these mistakes helps prevent issues such as short circuits, overheating, and assembly difficulties. -
Q: How can PCB designers optimize component orientation for manufacturing yield?
A: To optimize component orientation for manufacturing yield, PCB designers should follow manufacturer guidelines, prioritize electrical connections, design with manufacturing in mind, and conduct thorough design reviews. By adhering to best practices and avoiding common mistakes, designers can maximize the percentage of correctly manufactured boards.
Conclusion
PCB component orientation is a critical aspect of circuit board manufacturing that directly impacts the functionality, reliability, and manufacturability of the final product. By understanding the importance of PCB orientation and following best practices, designers can optimize the placement and alignment of components, ensuring optimal electrical connectivity, thermal management, mechanical stability, and manufacturing efficiency.
Proper PCB orientation contributes to higher manufacturing yields, lower production costs, and improved overall quality of the circuit board. By avoiding common mistakes and considering factors such as pin assignments, thermal requirements, and manufacturing constraints, PCB designers can create robust and reliable designs that meet the demands of modern electronics.
As technology continues to advance and the complexity of circuit boards increases, the importance of PCB orientation will only grow. By staying informed about best practices and emerging trends in PCB design and manufacturing, engineers and designers can stay ahead of the curve and deliver cutting-edge products that meet the highest standards of quality and performance.
0 Comments