Introduction to BOM and Its Significance in PCB Manufacturing
A Bill of Materials (BOM) is a comprehensive list of all the components, parts, and materials required to manufacture a product. In the context of Printed Circuit Board (PCB) manufacturing, a BOM plays a crucial role in ensuring the smooth and efficient production of high-quality PCB assemblies. This article will delve into the importance of BOM in the PCB manufacturing process, highlighting its key benefits and the consequences of an inaccurate or incomplete BOM.
What is a Bill of Materials (BOM)?
A Bill of Materials (BOM) is a detailed document that lists all the components, parts, and materials needed to manufacture a product. It serves as a blueprint for the manufacturing process, providing a clear and organized structure for procuring, assembling, and tracking the various elements that make up the final product.
In the realm of PCB manufacturing, a BOM typically includes the following information:
- Component names and descriptions
- Manufacturer part numbers
- Quantities required for each component
- Reference designators (e.g., R1, C2, U3)
- Component package types (e.g., SMD, through-hole)
- Any special instructions or notes related to the components
A well-crafted BOM ensures that all stakeholders in the PCB manufacturing process, from designers and procurement specialists to assembly technicians and quality control personnel, have access to the same accurate and up-to-date information.
The Role of BOM in PCB Manufacturing
The BOM serves as the foundation for the entire PCB manufacturing process. It is the primary document that guides the procurement of components, the assembly of the PCB, and the quality control checks throughout the production cycle. Without a comprehensive and accurate BOM, the PCB manufacturing process can quickly become chaotic, leading to delays, errors, and ultimately, subpar products.
Here are some of the key roles that a BOM plays in PCB manufacturing:
-
Procurement: The BOM provides a clear list of the components and materials needed for the PCB assembly. This information is essential for the procurement team to source the required components from reliable suppliers in a timely and cost-effective manner.
-
Assembly: The BOM acts as a roadmap for the assembly process. It helps the assembly technicians identify the correct components, their quantities, and their placement on the PCB. A well-structured BOM minimizes the chances of assembly errors and ensures a smooth production flow.
-
Quality Control: The BOM serves as a reference for quality control checks throughout the manufacturing process. By comparing the assembled PCB against the BOM, quality control personnel can verify that the correct components have been used and that they have been placed accurately on the board.
-
Inventory Management: The BOM helps in managing inventory levels by providing a clear picture of the components required for each PCB assembly. This information allows manufacturers to maintain optimal stock levels, minimizing the risk of component shortages or excess inventory.
-
Documentation: The BOM is a critical part of the PCB documentation package. It provides a historical record of the components used in a specific PCB assembly, which can be invaluable for future reference, especially in case of repairs, upgrades, or troubleshooting.
The Consequences of an Inaccurate or Incomplete BOM
An inaccurate or incomplete BOM can have far-reaching consequences in the PCB manufacturing process. Some of the potential issues that can arise include:
-
Component Shortages: If the BOM is missing critical components or specifies incorrect quantities, it can lead to component shortages during the assembly process. This can cause production delays and increase manufacturing costs.
-
Assembly Errors: An inaccurate BOM can lead to assembly errors, such as using the wrong components or placing them incorrectly on the PCB. These errors can result in functional issues, reduced reliability, and even complete product failure.
-
Quality Control Challenges: Without a reliable BOM, quality control checks become more difficult and time-consuming. This can lead to a higher risk of defective products reaching the end-users, damaging the manufacturer’s reputation and leading to costly returns and repairs.
-
Inventory Mismanagement: An inaccurate BOM can cause inventory mismanagement, leading to overstocking of unnecessary components or understocking of critical parts. This can tie up working capital, increase storage costs, and cause production bottlenecks.
-
Delayed Time-to-Market: Inaccuracies in the BOM can lead to production delays, which can significantly impact the time-to-market for the final product. In today’s fast-paced, competitive market, such delays can result in lost opportunities and reduced market share.
Best Practices for Creating and Maintaining an Accurate BOM
To ensure the accuracy and completeness of a BOM, PCB manufacturers should follow these best practices:
-
Collaborate with Design Teams: Encourage close collaboration between the design and manufacturing teams to ensure that the BOM is accurate and complete from the early stages of product development.
-
Use Standardized Templates: Develop and use standardized BOM templates that include all the necessary information fields. This helps maintain consistency and reduces the risk of errors.
-
Implement Version Control: Use version control systems to manage BOM revisions and track changes over time. This ensures that all stakeholders are working with the most up-to-date information.
-
Conduct Regular Audits: Perform regular audits of the BOM to identify and correct any discrepancies or inaccuracies. This can be done by comparing the BOM against the actual components used in the assembly process.
-
Leverage Automation: Use automated tools and software to generate and manage BOMs. These tools can help reduce manual errors, improve efficiency, and ensure data consistency across different systems.
-
Provide Training: Ensure that all relevant personnel, including design engineers, procurement specialists, and assembly technicians, are trained on the importance of accurate BOMs and the best practices for creating and maintaining them.
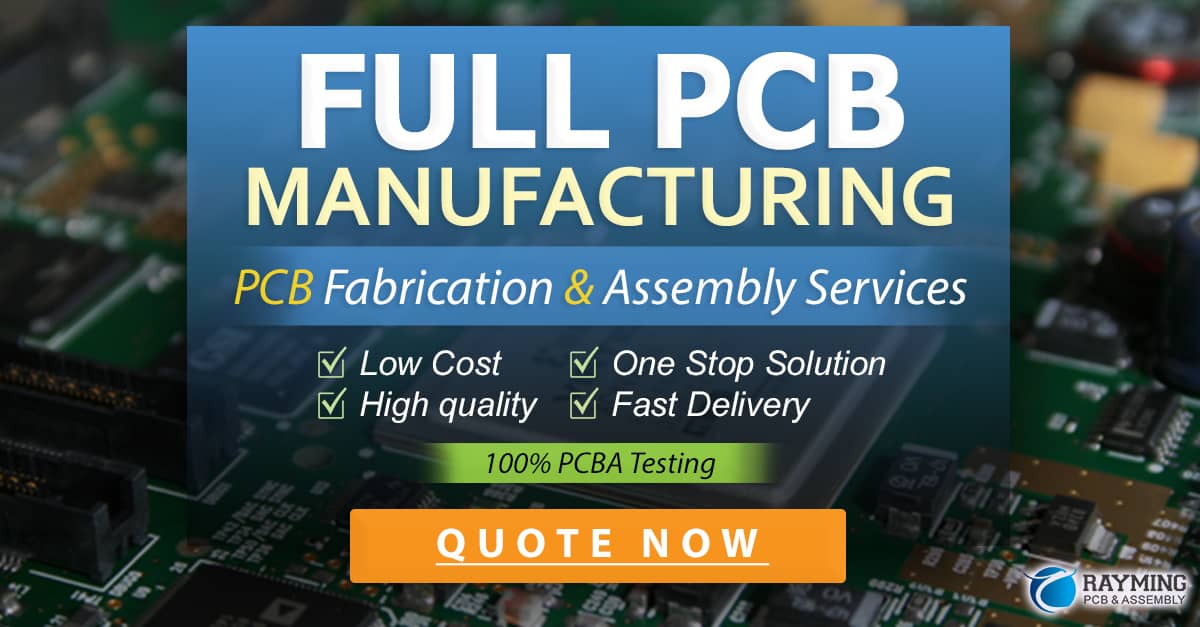
The Benefits of an Accurate and Well-Maintained BOM
An accurate and well-maintained BOM offers numerous benefits to PCB manufacturers, including:
-
Improved Efficiency: With a clear and accurate BOM, procurement, assembly, and quality control processes become more streamlined and efficient. This leads to reduced production times and improved overall productivity.
-
Cost Savings: An accurate BOM helps minimize component shortages, excess inventory, and assembly errors. This, in turn, leads to cost savings by reducing waste, minimizing rework, and optimizing inventory management.
-
Enhanced Product Quality: A well-maintained BOM ensures that the correct components are used in the PCB assembly, leading to improved product quality and reliability.
-
Faster Time-to-Market: By streamlining the manufacturing process and reducing errors, an accurate BOM helps PCB manufacturers bring their products to market faster, gaining a competitive edge.
-
Better Customer Satisfaction: Improved product quality and faster delivery times lead to higher customer satisfaction, which can translate into repeat business and positive word-of-mouth referrals.
Frequently Asked Questions (FAQ)
-
What is the difference between a BOM and a parts list?
A BOM is a more comprehensive document that includes not only the list of components but also additional information such as quantities, reference designators, and assembly instructions. A parts list, on the other hand, is a simpler document that typically only lists the components required for a product. -
How often should a BOM be updated?
A BOM should be updated whenever there are changes to the product design, components, or manufacturing process. It is essential to maintain version control and communicate any updates to all relevant stakeholders. -
Can a BOM be used for multiple PCB designs?
While some components may be common across different PCB designs, it is generally recommended to create a unique BOM for each specific design. This ensures that the BOM accurately reflects the components and quantities required for that particular PCB assembly. -
What is the role of the procurement team in relation to the BOM?
The procurement team is responsible for sourcing the components listed in the BOM from reliable suppliers. They use the BOM to ensure that the correct components are purchased in the required quantities and that they meet the specified quality standards. -
How can PCB manufacturers ensure the accuracy of their BOMs?
PCB manufacturers can ensure the accuracy of their BOMs by implementing best practices such as collaborating with design teams, using standardized templates, implementing version control, conducting regular audits, leveraging automation, and providing training to relevant personnel.
Conclusion
In conclusion, the Bill of Materials (BOM) is a critical document in the PCB manufacturing process. It serves as the backbone for procurement, assembly, quality control, and inventory management. An accurate and well-maintained BOM can lead to improved efficiency, cost savings, enhanced product quality, faster time-to-market, and better customer satisfaction.
To reap these benefits, PCB manufacturers must prioritize the creation and maintenance of accurate BOMs. By following best practices such as collaboration, standardization, version control, regular audits, automation, and training, manufacturers can ensure that their BOMs are comprehensive, up-to-date, and error-free.
Investing time and resources into maintaining accurate BOMs is a smart business decision for PCB manufacturers. It not only streamlines the manufacturing process but also helps build a reputation for quality and reliability, which is essential in today’s competitive market.
Aspect | Importance |
---|---|
Procurement | Ensures the correct components are sourced in the required quantities |
Assembly | Guides the placement of components on the PCB, minimizing errors |
Quality Control | Serves as a reference for verifying the accuracy of the assembled PCB |
Inventory Management | Helps maintain optimal stock levels and minimize component shortages |
Documentation | Provides a historical record of the components used in a specific PCB assembly |
In summary, the BOM is a vital tool that enables PCB manufacturers to navigate the complexities of the production process, ensuring that high-quality, reliable PCBs are delivered to their customers on time and within budget. By recognizing the importance of the BOM and implementing best practices for its creation and maintenance, PCB manufacturers can position themselves for success in an increasingly demanding market.
0 Comments