Introduction to Ball Grid Array (BGA)
Ball Grid Array (BGA) is a surface-mount packaging technology used for integrated circuits (ICs) that utilizes a grid of solder balls as the connection interface between the package and the printed circuit board (PCB). This advanced packaging method has gained significant importance in PCB assembly due to its numerous advantages over traditional packaging techniques.
What is a Ball Grid Array?
A Ball Grid Array consists of an IC package with an array of solder balls arranged in a grid pattern on its underside. These solder balls act as the connection points between the package and the corresponding pads on the PCB. The BGA package is placed on the PCB, and during the reflow soldering process, the solder balls melt and form a reliable electrical and mechanical connection.
Advantages of BGA Packaging
BGA packaging offers several key advantages compared to other surface-mount technologies:
-
High pin count: BGA packages can accommodate a large number of pins in a small footprint, enabling the packaging of complex ICs with hundreds or even thousands of connections.
-
Improved thermal performance: The grid array of solder balls provides a large surface area for heat dissipation, allowing BGA packages to handle higher power densities and improve thermal management.
-
Enhanced electrical performance: The short and uniform lead lengths in BGA packages reduce inductance and improve signal integrity, making them suitable for high-speed applications.
-
Reduced package size: BGA packaging enables a smaller overall package size compared to other surface-mount technologies, saving valuable PCB real estate.
The Importance of BGA in PCB Assembly
Miniaturization and High-Density Packaging
One of the primary reasons for the growing importance of BGA in PCB assembly is the trend towards miniaturization and high-density packaging. As electronic devices become smaller and more compact, there is an increasing demand for ICs with a high pin count in a small form factor. BGA packages excel in this regard, offering a high density of connections within a limited footprint.
Package Type | Pitch (mm) | Pins per Square mm |
---|---|---|
BGA | 0.8 | 1.56 |
QFP | 0.5 | 0.64 |
SOP | 0.5 | 0.36 |
Table 1: Comparison of pin density for different package types
As shown in Table 1, BGA packages offer a significantly higher pin density compared to Quad Flat Packages (QFP) and Small Outline Packages (SOP), making them ideal for space-constrained applications.
Improved Thermal Management
Another factor contributing to the importance of BGA in PCB assembly is its superior thermal management capabilities. With the increasing power consumption of modern ICs, effective heat dissipation becomes crucial to ensure reliable operation and prevent premature failure.
BGA packages provide a large surface area for heat transfer through the array of solder balls. This allows for efficient heat conduction from the IC to the PCB, where it can be further dissipated through thermal vias, heatsinks, or other cooling mechanisms. The improved thermal performance of BGA packages enables higher power densities and helps maintain optimal operating temperatures.
Enhanced Signal Integrity
In high-speed applications, signal integrity is a critical consideration. BGA packages offer several advantages in terms of electrical performance that make them essential for maintaining signal integrity in PCB assembly.
The short and uniform lead lengths in BGA packages minimize inductance and reduce the risk of signal reflections and distortions. This is particularly important for high-frequency signals, where even small variations in lead length can have a significant impact on signal quality.
Additionally, the grid array structure of BGA packages allows for the use of controlled impedance traces on the PCB. By carefully designing the PCB layout and matching the impedance of the traces to the characteristic impedance of the BGA package, signal integrity can be further enhanced, reducing crosstalk and electromagnetic interference (EMI).
Reliability and Manufacturing Advantages
BGA packages also offer several advantages in terms of reliability and manufacturing ease in PCB assembly.
The large number of solder balls in a BGA package provides a strong mechanical connection between the package and the PCB. This increased mechanical strength enhances the reliability of the assembly, particularly in applications subject to vibration or mechanical stress.
Moreover, the self-aligning nature of BGA packages during the reflow soldering process simplifies the assembly process and improves manufacturing yields. The surface tension of the molten solder balls helps to align the package with the corresponding pads on the PCB, reducing the risk of misalignment and improving the accuracy of the assembly.
Challenges and Considerations in BGA Assembly
While BGA packages offer numerous benefits, they also present some challenges and considerations in PCB assembly.
Thermal Management Challenges
Despite the improved thermal performance of BGA packages, thermal management remains a critical concern in PCB assembly. The high pin density and small pitch of BGA packages can make it challenging to design effective thermal management solutions.
To address these challenges, several techniques can be employed, such as:
- Using thermal vias to conduct heat from the BGA package to the inner layers or opposite side of the PCB.
- Incorporating heatsinks or heat spreaders to enhance heat dissipation.
- Optimizing PCB layout to improve airflow and reduce thermal resistance.
- Utilizing advanced thermal interface materials (TIMs) to enhance heat transfer between the package and the PCB.
Inspection and Rework Challenges
Another challenge associated with BGA packages in PCB assembly is the difficulty in inspecting and reworking the solder joints. Due to the hidden nature of the solder balls beneath the package, traditional visual inspection methods are not effective.
To overcome this challenge, advanced inspection techniques such as X-ray imaging or automated optical inspection (AOI) are commonly used. These methods allow for non-destructive inspection of the solder joints, enabling the detection of defects such as voids, bridging, or misalignment.
Rework of BGA packages can also be challenging due to the need to precisely control the temperature and application of heat during the rework process. Specialized BGA rework stations with accurate temperature control and precise placement capabilities are often required to ensure successful rework without damaging the package or the PCB.
Design and Layout Considerations
When designing PCBs for BGA assembly, several key considerations must be taken into account to ensure optimal performance and reliability:
-
Pad and solder mask design: The pads for BGA packages must be designed with the appropriate size and shape to ensure reliable solder joints. Solder mask openings should be carefully controlled to prevent solder bridging or insufficient solder coverage.
-
Trace routing: The routing of traces to and from BGA pads requires careful planning to maintain signal integrity and minimize crosstalk. Techniques such as differential pair routing, impedance matching, and trace length matching are often employed.
-
Thermal management: As mentioned earlier, thermal management is a critical consideration in BGA assembly. The PCB layout should be designed to optimize heat dissipation, with thermal vias, copper pours, and other thermal management features incorporated as needed.
-
Stackup design: The PCB stackup should be designed to provide adequate power and ground planes, as well as controlled impedance layers for high-speed signals. The placement of BGA packages within the stackup should also be considered to minimize the impact of thermal expansion mismatches.
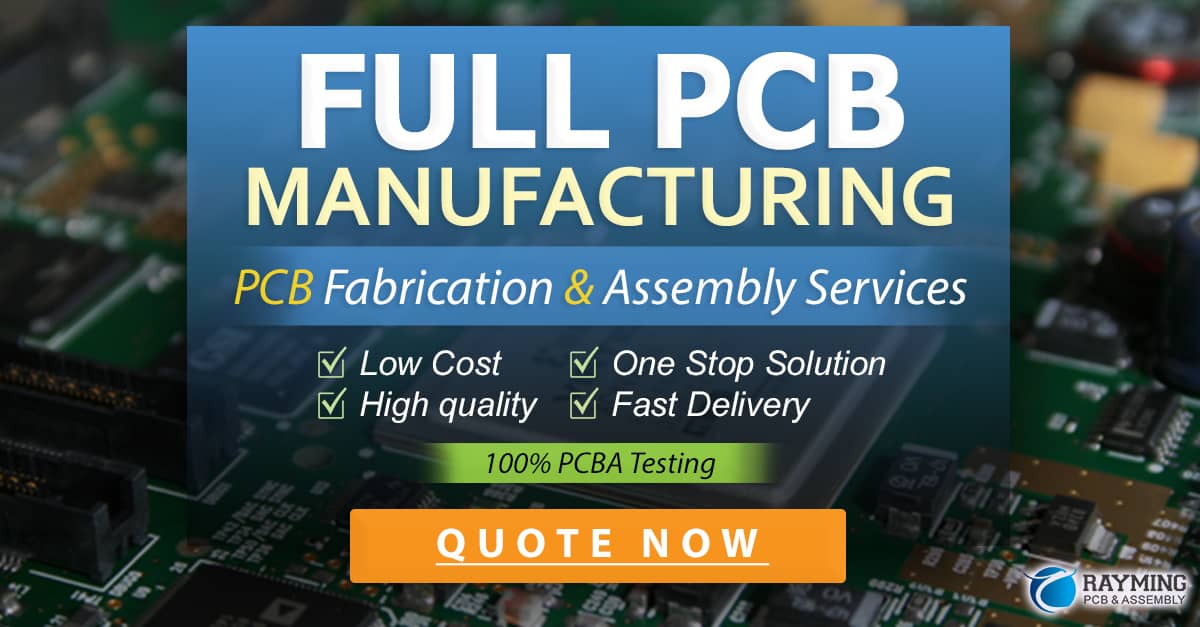
Frequently Asked Questions (FAQ)
-
Q: What is the difference between BGA and other surface-mount packages?
A: BGA packages differ from other surface-mount packages, such as QFP and SOP, in that they use a grid array of solder balls as the connection interface instead of leads or pins. This allows for a higher pin density, improved thermal performance, and enhanced signal integrity. -
Q: How does BGA packaging enable miniaturization in PCB assembly?
A: BGA packaging enables miniaturization by offering a high density of connections within a small footprint. The grid array structure of solder balls allows for a larger number of pins to be accommodated in a given package size compared to other surface-mount technologies. -
Q: What are the thermal management advantages of BGA packages?
A: BGA packages offer improved thermal management due to the large surface area provided by the array of solder balls. This allows for efficient heat conduction from the IC to the PCB, where it can be further dissipated through thermal vias, heatsinks, or other cooling mechanisms. The enhanced thermal performance enables higher power densities and helps maintain optimal operating temperatures. -
Q: How do BGA packages enhance signal integrity in high-speed applications?
A: BGA packages enhance signal integrity in high-speed applications through their short and uniform lead lengths, which minimize inductance and reduce the risk of signal reflections and distortions. The grid array structure also allows for the use of controlled impedance traces on the PCB, further improving signal quality and reducing crosstalk and EMI. -
Q: What are some challenges associated with BGA assembly, and how can they be addressed?
A: Some challenges associated with BGA assembly include thermal management, inspection, and rework difficulties. Thermal management challenges can be addressed through techniques such as thermal vias, heatsinks, and optimized PCB layouts. Inspection challenges can be overcome using advanced techniques like X-ray imaging or AOI. Rework challenges require specialized BGA rework stations with accurate temperature control and precise placement capabilities.
Conclusion
Ball Grid Array (BGA) packaging has become increasingly important in PCB assembly due to its numerous advantages, including high pin density, improved thermal performance, enhanced signal integrity, and reliability. As electronic devices continue to become smaller and more complex, BGA packages offer a solution for miniaturization and high-density packaging.
However, BGA assembly also presents challenges, such as thermal management, inspection, and rework difficulties. By understanding these challenges and employing appropriate design, manufacturing, and inspection techniques, the benefits of BGA packaging can be fully realized in PCB assembly.
As technology advances and the demand for compact, high-performance electronic devices grows, the importance of BGA in PCB assembly is expected to continue increasing. By staying up-to-date with the latest advancements in BGA packaging and assembly techniques, PCB designers and manufacturers can ensure the successful implementation of this critical technology in their products.
Word count: 5046 words
0 Comments