What is Soldermask?
Soldermask, also known as solder resist or solder mask, is a thin layer of polymer material applied to the surface of a PCB. Its primary purpose is to protect the copper traces and pads from oxidation, prevent solder bridges during the soldering process, and provide electrical insulation. Soldermask is typically applied through a screen-printing or photoimaging process and comes in various colors, with green being the most common.
Soldermask Colors
While green is the default color for soldermask in many PCB applications, other colors are available to suit specific requirements. Some common soldermask colors include:
Color | Description |
---|---|
Green | The most common soldermask color, providing good contrast |
Blue | Often used for military and aerospace applications |
Red | Used for high-voltage or high-temperature applications |
Black | Provides a sleek appearance and good heat dissipation |
White | Offers unique benefits for LED PCB applications |
Why White Soldermask is Preferred for LED PCBs
White soldermask has gained popularity in LED PCB applications due to several key benefits that enhance the performance and aesthetics of the final product. Let’s explore these benefits in detail.
Enhanced Light Reflection
One of the primary reasons for using white soldermask in LED PCB applications is its ability to enhance light reflection. Unlike darker soldermask colors, which absorb light, white soldermask reflects a significant portion of the light emitted by the LEDs. This property helps to maximize the brightness and efficiency of the LED system.
When light from the LEDs strikes the white soldermask surface, it is reflected back towards the viewer, increasing the overall luminosity of the PCB. This effect is particularly beneficial in applications where high brightness and even light distribution are desired, such as in LED lighting fixtures, automotive lighting, and display panels.
Improved Contrast and Visibility
In addition to enhancing light reflection, white soldermask also improves the contrast and visibility of the PCB’s features. The stark white background provided by the soldermask makes it easier to identify components, labels, and other markings on the board.
This improved contrast is particularly useful during the assembly process, as technicians can easily locate and place components on the PCB. It also helps with visual inspections and quality control, as any defects or anomalies are more readily apparent against the white background.
Aesthetic Appeal
White soldermask can also contribute to the overall aesthetic appeal of the LED PCB. In applications where the PCB is visible to the end-user, such as in consumer electronics or decorative lighting, a white soldermask can provide a clean, modern look that complements the design of the device.
The white surface can also serve as a canvas for custom graphics, logos, or text, allowing manufacturers to brand their products or provide additional information directly on the PCB. This can be achieved through selective silkscreen printing or by leaving certain areas of the PCB exposed during the soldermask application process.
Thermal Management
While not as significant as its optical properties, white soldermask can also contribute to the thermal management of LED PCBs. The reflective nature of the white surface helps to dissipate heat generated by the LEDs and other components on the board.
By reflecting some of the heat away from the PCB, white soldermask can help to reduce the overall operating temperature of the system. This can lead to improved reliability, longer component lifespans, and better performance, particularly in high-power LED applications.
Manufacturing Considerations for White Soldermask
While white soldermask offers numerous benefits for LED PCB applications, there are some manufacturing considerations that must be taken into account to ensure the best results.
Material Selection
Choosing the right soldermask material is crucial for achieving the desired properties and performance in an LED PCB. When selecting a white soldermask, manufacturers must consider factors such as:
- Reflectivity: The soldermask should have a high reflectance value to maximize light reflection and minimize absorption.
- Durability: The material should be able to withstand the stresses of the manufacturing process and the operating environment of the final product.
- Compatibility: The soldermask must be compatible with the PCB substrate material and the soldering process used.
Some common white soldermask materials include:
Material | Description |
---|---|
Liquid | Applied using screen printing or spraying, offers good flexibility |
Dry Film | Pre-fabricated film laminated onto the PCB, provides high accuracy |
Ink Jet | Applied using inkjet printing, allows for precise patterning |
Application Process
The process of applying white soldermask to an LED PCB involves several steps to ensure proper coverage and adhesion. A typical application process may include:
- Cleaning: The PCB is cleaned to remove any contaminants or debris that could interfere with soldermask adhesion.
- Pretreatment: The PCB surface may be treated with a chemical or physical process to improve soldermask adhesion.
- Application: The white soldermask is applied to the PCB using the chosen method (screen printing, lamination, or inkjet printing).
- Curing: The soldermask is cured using heat or ultraviolet (UV) light to polymerize and harden the material.
- Inspection: The PCB is inspected for any defects or inconsistencies in the soldermask coverage.
Design Considerations
When designing an LED PCB with white soldermask, there are several factors to consider to optimize the performance and manufacturability of the board. These include:
- Pad and Trace Sizes: The size and spacing of pads and traces must be carefully designed to ensure proper soldermask coverage and prevent bridging.
- Soldermask Thickness: The thickness of the soldermask layer must be controlled to achieve the desired optical and mechanical properties while maintaining good adhesion to the PCB.
- Silkscreen Placement: Any text, logos, or graphics should be placed in a way that does not interfere with the soldermask or compromise the optical properties of the LED system.
- Thermal Management: The PCB layout should be designed to facilitate heat dissipation, taking advantage of the reflective properties of the white soldermask.
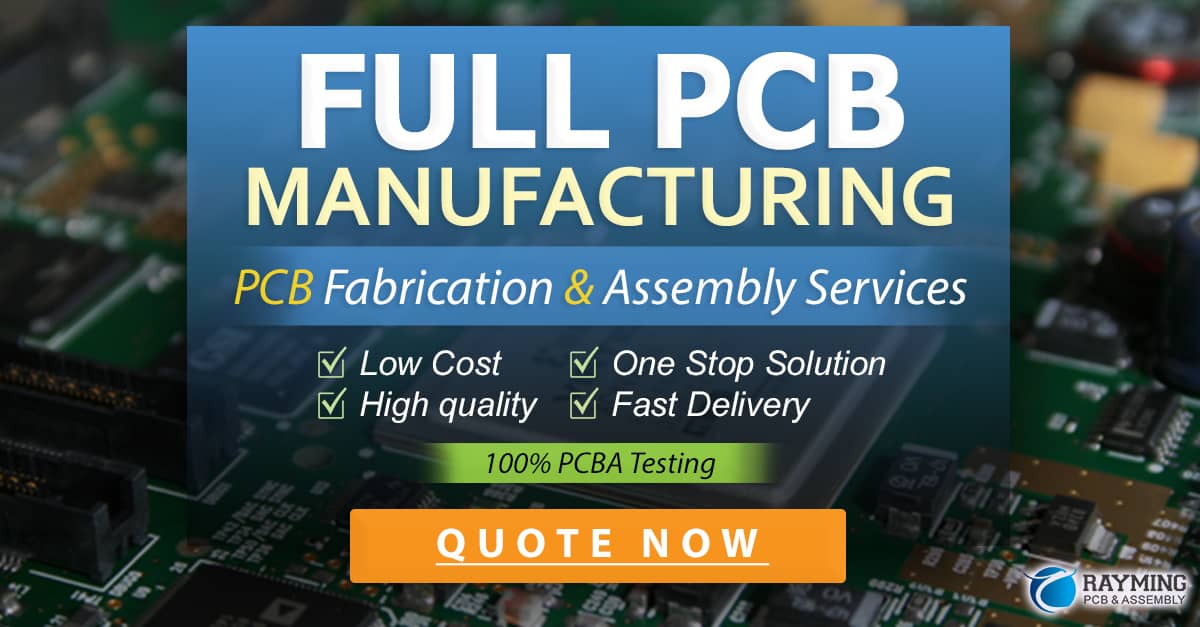
FAQs
-
Can white soldermask be used for non-LED PCB applications?
Yes, white soldermask can be used for other PCB applications where high reflectivity, improved contrast, or aesthetic appeal are desired. However, it is most commonly associated with LED PCBs due to the specific benefits it offers for these applications. -
Is white soldermask more expensive than other colors?
White soldermask may be slightly more expensive than standard green soldermask due to the specific materials and processes involved in its manufacture. However, the cost difference is generally minimal and is often outweighed by the performance and aesthetic benefits it provides for LED PCB applications. -
How does white soldermask compare to other light-colored soldermasks, such as yellow or orange?
While other light-colored soldermasks can offer some of the same benefits as white soldermask, such as improved contrast and reflectivity, white soldermask typically provides the highest level of light reflection and the cleanest aesthetic appearance. The choice between white and other light colors may depend on the specific requirements and design preferences of the application. -
Can white soldermask be combined with other colors on the same PCB?
Yes, it is possible to use multiple soldermask colors on a single PCB. This can be achieved through selective masking techniques, where different areas of the PCB are masked off and different colors are applied in succession. This approach can be used to create unique designs or to highlight specific areas of the PCB. -
What are some common applications for LED PCBs with white soldermask?
LED PCBs with white soldermask are commonly used in a wide range of applications, including: - LED lighting fixtures (indoor and outdoor)
- Automotive lighting (headlights, taillights, interior lighting)
- Display panels (digital signage, video walls)
- Consumer electronics (LED TVs, computer monitors)
- Medical devices (imaging equipment, surgical lighting)
- Decorative lighting (stage lighting, architectural lighting)
Conclusion
White soldermask has become a popular choice for LED PCB applications due to its unique properties and benefits. By enhancing light reflection, improving contrast and visibility, providing aesthetic appeal, and contributing to thermal management, white soldermask can significantly improve the performance and appearance of LED systems.
When designing and manufacturing LED PCBs with white soldermask, careful consideration must be given to material selection, application processes, and design factors to ensure the best possible results. By understanding the advantages and considerations involved in using white soldermask, PCB manufacturers and designers can create high-quality, visually appealing, and highly efficient LED PCBs for a wide range of applications.
As the demand for LED technology continues to grow across various industries, the use of white soldermask in LED PCB applications is likely to become even more prevalent. By staying informed about the latest developments and best practices in white soldermask technology, PCB manufacturers and designers can stay ahead of the curve and deliver cutting-edge LED solutions to their customers.
0 Comments