Why is Via Plugging Important?
Via plugging plays a crucial role in ensuring the proper functioning and reliability of PCBs. Here are some key reasons why via plugging is essential:
1. Electrical Conductivity
The primary purpose of via plugging is to establish reliable electrical connections between different layers of the PCB. By filling the vias with a conductive material, such as copper or a conductive paste, electrical signals can travel through the board without interruption, ensuring proper communication between components.
2. Preventing Contamination
Unfilled vias can act as traps for contaminants, such as dust, debris, or chemical residues. These contaminants can compromise the electrical integrity of the board and lead to failures. Via plugging seals the vias, preventing contamination and enhancing the reliability of the PCB.
3. Surface Flatness
Many PCB manufacturing processes, such as solder mask application and component assembly, require a flat and smooth surface. Unfilled vias can create surface irregularities that hinder these processes. By plugging the vias, a level surface is achieved, facilitating subsequent manufacturing steps and improving the overall quality of the PCB.
4. Impedance Control
In high-frequency applications, such as radio frequency (RF) circuits, via plugging helps maintain consistent impedance throughout the board. Unfilled vias can cause impedance discontinuities, leading to signal reflections and degraded performance. Properly plugged vias minimize these issues, ensuring optimal signal integrity.
Via Plugging Methods
There are several methods used for via plugging, each with its advantages and considerations. The choice of method depends on factors such as the PCB design, manufacturing capabilities, and performance requirements. Here are the most common via plugging methods:
1. Copper Filling
Copper filling is a popular method for via plugging, especially in high-performance applications. This process involves electroplating copper into the vias until they are completely filled. Copper-filled vias offer excellent electrical conductivity and thermal dissipation properties.
Advantages of copper filling include:
– High electrical conductivity
– Good thermal conductivity
– Robust and reliable connections
– Suitable for high-current applications
However, copper filling has some limitations:
– Requires additional processing steps
– Can be time-consuming and costly
– May cause stress on the PCB due to copper’s thermal expansion
2. Conductive Paste Filling
Conductive paste filling involves dispensing a conductive paste, typically a silver-based or copper-based material, into the vias. The paste is then cured to create a solid, conductive plug. This method is often used for prototype or low-volume production.
Advantages of conductive paste filling include:
– Faster and more cost-effective than copper filling
– Suitable for small vias and fine-pitch designs
– Reduced stress on the PCB compared to copper filling
Limitations of conductive paste filling include:
– Lower electrical conductivity compared to copper filling
– May require additional processing steps for optimal performance
– Limited thermal conductivity
3. Soldermask Plug
Soldermask plugging is a simple and cost-effective method that involves filling the vias with soldermask material during the soldermask application process. While soldermask is not conductive, this method provides a flat surface for subsequent processes and prevents contamination.
Advantages of soldermask plugging include:
– Cost-effective and easy to implement
– Provides a flat surface for component assembly
– Prevents contamination in the vias
Limitations of soldermask plugging include:
– Not suitable for applications requiring electrical conductivity through the vias
– May not provide sufficient support for components with leads passing through the vias
Via Plugging Process
The via plugging process typically involves the following steps:
-
Via Drilling: Vias are drilled through the PCB using mechanical or laser drilling methods, according to the design specifications.
-
Cleaning: The drilled vias are cleaned to remove any debris or contaminants that may hinder the plugging process.
-
Plugging: The chosen via plugging method (copper filling, conductive paste filling, or soldermask plugging) is applied to fill the vias.
-
Curing/Plating: Depending on the plugging method, the filled vias may require curing (for conductive paste) or additional plating (for copper filling) to achieve the desired conductivity and surface finish.
-
Inspection: The plugged vias are inspected to ensure complete filling, proper conductivity, and surface flatness. Visual inspection, cross-sectioning, or electrical testing may be employed.
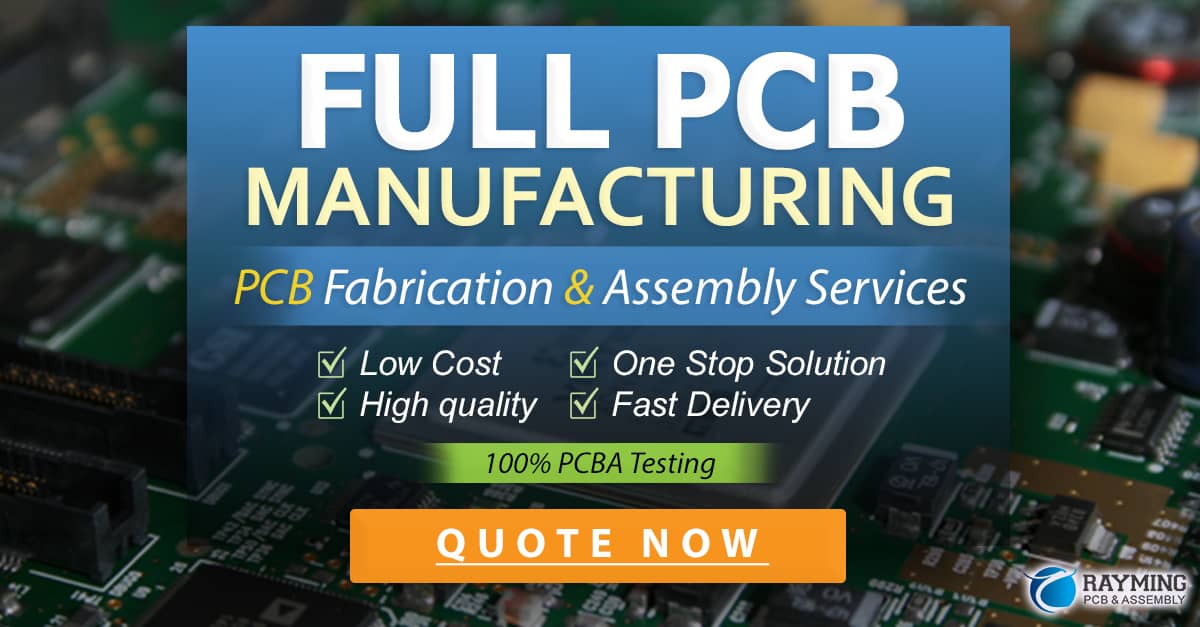
Best Practices for Via Plugging
To ensure optimal results and reliability, consider the following best practices when implementing via plugging in your PCB manufacturing process:
-
Design Considerations: Work closely with your PCB design team to optimize via placement, size, and spacing. Consider the plugging method early in the design phase to ensure compatibility and manufacturability.
-
Material Selection: Choose the appropriate plugging material based on the application requirements, such as electrical conductivity, thermal conductivity, and cost. Consult with your PCB manufacturer for recommendations.
-
Process Control: Implement strict process controls during via plugging to ensure consistency and quality. Monitor parameters such as filling depth, curing temperature, and plating thickness.
-
Inspection and Testing: Conduct thorough inspections and testing to verify the quality of the plugged vias. Implement automated optical inspection (AOI) and electrical testing to detect any defects or inconsistencies.
-
Collaboration with Manufacturers: Work closely with your PCB manufacturer to discuss via plugging requirements, capabilities, and best practices. Their expertise can help optimize the process and ensure successful results.
FAQ
1. What is the difference between via filling and via plugging?
Via filling and via plugging are often used interchangeably, but there is a slight difference. Via filling refers to the process of filling the vias with a conductive material to create electrical connections between layers. Via plugging, on the other hand, emphasizes the sealing aspect, focusing on creating a flat surface and preventing contamination. In practice, via plugging typically involves filling the vias with a conductive material as well.
2. Can via plugging be done selectively?
Yes, via plugging can be done selectively, meaning that only specific vias on the PCB are plugged while others remain unfilled. This is often done when certain vias require electrical conductivity or surface flatness, while others do not. Selective via plugging can help optimize the manufacturing process and reduce costs.
3. What is the minimum via size that can be plugged?
The minimum via size that can be plugged depends on the plugging method and the capabilities of the PCB manufacturer. Copper filling can typically handle smaller vias compared to conductive paste filling. As a general rule, vias with diameters as small as 0.1 mm can be plugged, but it’s best to consult with your manufacturer for their specific capabilities.
4. How does via plugging affect the overall PCB thickness?
Via plugging can slightly increase the overall thickness of the PCB, especially when using methods like copper filling. The additional thickness is usually minimal, in the range of a few microns to a few tens of microns, depending on the via size and plugging method. This increase in thickness should be considered during the design phase to ensure compatibility with other components and assembly processes.
5. Can via plugging improve the thermal management of a PCB?
Yes, via plugging, particularly with thermally conductive materials like copper, can enhance the thermal management of a PCB. Filled vias can act as thermal vias, providing a path for heat dissipation from components to other layers or to heatsinks. This can help prevent overheating and improve the overall reliability of the PCB.
Conclusion
Via plugging is a critical process in PCB manufacturing that ensures reliable electrical connections, prevents contamination, and provides a flat surface for subsequent processes. The choice of via plugging method depends on various factors, including the application requirements, manufacturing capabilities, and cost considerations. By understanding the importance of via plugging, selecting the appropriate method, and following best practices, PCB designers and manufacturers can produce high-quality, reliable boards that meet the demands of modern electronics.
Via Plugging Method | Advantages | Limitations |
---|---|---|
Copper Filling | – High electrical and thermal conductivity – Robust and reliable connections – Suitable for high-current applications |
– Requires additional processing steps – Time-consuming and costly – May cause stress on the PCB |
Conductive Paste Filling | – Faster and more cost-effective than copper filling – Suitable for small vias and fine-pitch designs – Reduced stress on the PCB |
– Lower electrical conductivity compared to copper filling – May require additional processing steps – Limited thermal conductivity |
Soldermask Plugging | – Cost-effective and easy to implement – Provides a flat surface for component assembly – Prevents contamination in the vias |
– Not suitable for applications requiring electrical conductivity through the vias – May not provide sufficient support for components with leads passing through the vias |
As PCB designs continue to push the boundaries of miniaturization and performance, via plugging remains a vital process in ensuring the reliability and functionality of these complex circuits. By staying informed about the latest via plugging techniques and collaborating closely with experienced PCB manufacturers, designers can create innovative, high-quality products that meet the ever-increasing demands of the electronics industry.
0 Comments