The Importance of Via Filling in PCB Manufacturing
Via filling plays a vital role in the production of high-quality, reliable PCBs. Some of the key benefits of via filling include:
- Improved electrical conductivity
- Enhanced mechanical strength
- Reduced signal interference
- Better heat dissipation
- Increased reliability and durability
Without proper via filling, PCBs would be less efficient, more prone to failures, and have limited functionality. As electronic devices continue to become smaller, more compact, and more powerful, the importance of via filling in PCB manufacturing will only continue to grow.
The Via Filling Process
The via filling process typically involves several steps, which may vary depending on the specific requirements of the PCB and the manufacturing facility. However, the general process can be outlined as follows:
-
Drilling: Small holes (vias) are drilled through the PCB Layers using a specialized drill bit. The size and location of the vias are determined by the circuit design.
-
Cleaning: The drilLED PCB is cleaned to remove any debris or contaminants that may have accumulated during the drilling process. This step is crucial to ensure proper adhesion of the conductive material.
-
Plating: The vias are plated with a thin layer of conductive material, usually copper, using an electroplating process. This step creates a conductive lining within the vias, which will later be filled with a solid conductive material.
-
Filling: The plated vias are filled with a conductive material, such as copper paste or resin. This is typically done using a screen printing process, where the conductive material is forced into the vias using a squeegee.
-
Curing: The filled vias are then cured using heat or UV light, depending on the type of conductive material used. This step hardens the filling material, ensuring a solid, reliable connection between the PCB layers.
-
Planarization: After curing, the PCB surface is planarized, or leveled, to remove any excess filling material and ensure a smooth, even surface. This is typically done through a combination of sanding and polishing techniques.
-
Inspection: The filled vias are inspected for quality and consistency using various methods, such as visual inspection, x-ray imaging, or electrical testing. Any defects or inconsistencies are identified and corrected at this stage.
The following table summarizes the key steps in the via filling process:
Step | Description |
---|---|
Drilling | Small holes (vias) are drilled through the PCB layers |
Cleaning | PCB is cleaned to remove debris and contaminants |
Plating | Vias are plated with a thin layer of conductive material |
Filling | Plated vias are filled with a conductive material |
Curing | Filled vias are cured using heat or UV light |
Planarization | PCB surface is leveled to remove excess filling material |
Inspection | Filled vias are inspected for quality and consistency |
Types of Via Filling
There are several types of via filling methods used in PCB manufacturing, each with its own advantages and disadvantages. The choice of via filling method depends on various factors, such as the PCB application, the required level of conductivity, and the manufacturing cost.
Some of the most common types of via filling include:
Conductive Paste Filling
Conductive paste filling involves filling the plated vias with a conductive paste material, typically made of copper or silver particles suspended in a resin. This method is relatively inexpensive and easy to implement, making it a popular choice for many PCB Manufacturers.
Advantages:
– Low cost
– Easy to implement
– Good electrical conductivity
Disadvantages:
– Limited heat dissipation
– Potential for voids or inconsistencies in the filling
– May require additional processing steps, such as curing and planarization
Electroplating
Electroplating involves filling the vias with a solid conductive material, such as copper, using an electroplating process. This method provides excellent electrical conductivity and mechanical strength, making it suitable for high-performance applications.
Advantages:
– Excellent electrical conductivity
– High mechanical strength
– Good heat dissipation
– Consistent and reliable filling
Disadvantages:
– Higher cost compared to conductive paste filling
– Longer processing time
– Requires specialized equipment and expertise
Conductive Ink Filling
Conductive ink filling involves filling the vias with a conductive ink material, which is typically made of metal particles suspended in a liquid carrier. This method is relatively new and offers some unique advantages, such as the ability to fill very small vias and create intricate patterns.
Advantages:
– Ability to fill very small vias
– Potential for creating intricate patterns and designs
– Good electrical conductivity
Disadvantages:
– Limited mechanical strength
– Potential for clogging or inconsistencies in the filling
– May require additional processing steps, such as curing and planarization
The following table compares the key characteristics of the different via filling methods:
Method | Conductivity | Mechanical Strength | Cost | Filling Consistency |
---|---|---|---|---|
Conductive Paste | Good | Limited | Low | Potential voids |
Electroplating | Excellent | High | High | Consistent |
Conductive Ink | Good | Limited | Moderate | Potential clogging |
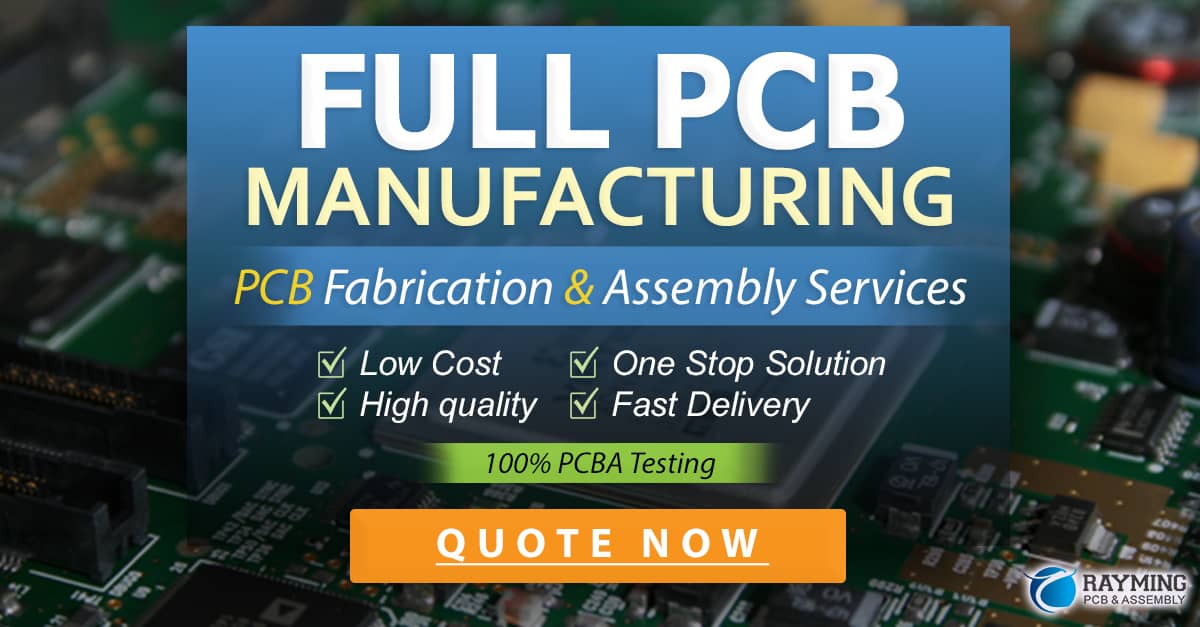
Factors Affecting Via Filling Quality
Several factors can affect the quality and consistency of via filling, which can ultimately impact the performance and reliability of the PCB. Some of the key factors to consider include:
-
Via size and aspect ratio: Smaller vias and higher aspect ratios (the ratio of via depth to diameter) can be more challenging to fill consistently, requiring specialized equipment and processes.
-
Plating quality: The quality of the Via plating, including its thickness, uniformity, and adhesion, can significantly impact the effectiveness of the filling process.
-
Filling material properties: The properties of the filling material, such as its viscosity, particle size, and conductive properties, can affect the ease of filling and the final quality of the filled vias.
-
Process parameters: The specific parameters used during the filling process, such as the filling pressure, temperature, and duration, can influence the quality and consistency of the filling.
-
PCB design and layout: The design and layout of the PCB, including the placement and spacing of the vias, can impact the effectiveness of the filling process and the overall quality of the filled vias.
By carefully considering these factors and optimizing the via filling process accordingly, PCB manufacturers can ensure high-quality, reliable via filling that meets the specific requirements of each application.
FAQ
- What is the purpose of via filling in PCB manufacturing?
Via filling is used to create electrical connections between the different layers of a PCB, allowing for the creation of complex, multi-layer circuit designs. It also provides mechanical support, improves heat dissipation, and reduces signal interference.
- What materials are commonly used for via filling?
The most common materials used for via filling are copper paste, copper plating, and conductive inks. The choice of material depends on the specific requirements of the PCB, such as the required level of conductivity, mechanical strength, and cost.
- How does via size affect the filling process?
Smaller vias can be more challenging to fill consistently, as they require more precise control over the filling process and may be more susceptible to clogging or voids. PCB manufacturers often use specialized equipment and processes to ensure high-quality filling of small vias.
- What is the difference between via filling and via plating?
Via plating refers to the process of coating the inside of the via with a thin layer of conductive material, typically copper, to create a conductive lining. Via filling, on the other hand, involves filling the plated via with a solid conductive material to create a complete, reliable electrical connection between the PCB layers.
- How can PCB manufacturers ensure the quality and consistency of via filling?
PCB manufacturers can ensure the quality and consistency of via filling by carefully controlling the various factors that affect the filling process, such as the via size and aspect ratio, plating quality, filling material properties, and process parameters. They also use various inspection methods, such as visual inspection, x-ray imaging, and electrical testing, to identify and correct any defects or inconsistencies in the filled vias.
Conclusion
Via filling is a critical process in the manufacturing of high-quality, reliable PCBs. By creating electrical connections between the different layers of the PCB and providing mechanical support, via filling enables the creation of complex, multi-layer circuit designs that power the electronic devices we rely on every day.
As PCB technology continues to advance and electronic devices become smaller, more powerful, and more sophisticated, the importance of via filling will only continue to grow. PCB manufacturers must stay at the forefront of via filling technology, continually improving their processes and materials to meet the ever-increasing demands of the electronics industry.
By understanding the fundamentals of via filling, including the different types of filling methods, the factors that affect filling quality, and the best practices for ensuring consistent, reliable results, PCB manufacturers can position themselves to succeed in this dynamic and rapidly evolving field.
0 Comments