Understanding the Powder Spray Process
The powder spray process is a type of coating method that uses a dry powder made from finely ground particles of pigment and resin. The powder is electrostatically charged and sprayed onto the surface of a substrate, which is typically made from metal, plastic, or wood. The coated substrate is then heated in an oven, causing the powder to melt and flow together to form a smooth, even finish.
Advantages of Powder Spray Coating
Powder spray coating offers several advantages over traditional liquid coating methods, such as:
- Environmental friendliness: Powder coatings contain no solvents and produce minimal volatile organic compounds (VOCs), making them a more eco-friendly option.
- Durability: Powder coatings provide excellent resistance to abrasion, corrosion, and UV radiation, resulting in a long-lasting finish.
- Efficiency: Powder spray coating is a highly efficient process, with minimal waste and overspray, as the excess powder can be collected and reused.
- Versatility: Powder coatings are available in a wide range of colors, textures, and finishes, allowing for greater customization and design flexibility.
The Powder Spray Process Steps
The typical powder spray process involves several key steps, which are outlined below:
1. Surface Preparation
Before the powder coating can be applied, the surface of the substrate must be thoroughly cleaned and prepared. This step is critical, as any contaminants or irregularities on the surface can affect the quality and adhesion of the final coating.
The surface preparation process typically involves the following steps:
- Degreasing: The substrate is cleaned using a degreasing agent to remove any oils, grease, or dirt from the surface.
- Rinsing: The substrate is then rinsed with water to remove any remaining degreasing agent.
- Etching: For metal substrates, an etching process may be used to create a slightly rough surface, which helps improve the adhesion of the powder coating.
- Drying: The substrate is thoroughly dried to remove any moisture from the surface.
2. Powder Application
Once the surface of the substrate is prepared, the powder coating can be applied. The powder is typically applied using a specialized spray gun, which applies an electrostatic charge to the powder particles as they are sprayed onto the surface of the substrate.
The electrostatic charge causes the powder particles to be attracted to the substrate, creating an even and uniform coating. The powder application process is typically carried out in a controlled environment, such as a spray booth, to minimize contamination and ensure consistent results.
3. Curing
After the powder has been applied to the surface of the substrate, it must be cured to create the final finish. The curing process involves heating the coated substrate in an oven to a specific temperature, typically between 350°F and 400°F (175°C and 205°C), for a set period of time, usually between 10 and 20 minutes.
During the curing process, the powder melts and flows together, creating a smooth, even finish. The heat also causes a chemical reaction to occur, which cross-links the polymer chains in the powder, resulting in a strong, durable coating.
4. Cooling and Inspection
Once the curing process is complete, the coated substrate is removed from the oven and allowed to cool to room temperature. After cooling, the finished product is inspected for any defects or irregularities, such as bubbles, cracks, or uneven coverage.
If the coating meets the required quality standards, the product is ready for use or further assembly. If any defects are found, the product may need to be stripped and recoated, or in some cases, scrapped entirely.
Powder Spray Equipment
To carry out the powder spray process, several key pieces of equipment are required, including:
Powder Spray Gun
The powder spray gun is the most critical piece of equipment in the powder coating process. It is responsible for applying the powder to the surface of the substrate and ensuring an even, uniform coating.
There are two main types of powder spray guns:
- Corona spray guns: These guns use an electrostatic charge to attract the powder to the substrate. They are the most common type of powder spray gun and are suitable for a wide range of applications.
- Tribo spray guns: These guns use friction to charge the powder particles, which are then attracted to the substrate. Tribo guns are typically used for more specialized applications, such as coating intricate or hard-to-reach areas.
Powder Coating Booth
The powder coating booth is an enclosed area where the powder is applied to the substrate. The booth is designed to contain the powder overspray and minimize contamination, ensuring a clean and consistent coating.
Powder coating booths can vary in size and configuration, depending on the specific application and the size of the substrates being coated. Some booths are equipped with automated systems for moving the substrates through the booth, while others rely on manual handling.
Curing Oven
The curing oven is used to heat the coated substrate to the required temperature for a set period of time, allowing the powder to melt and flow together to create the final finish.
Curing ovens can be gas-fired or electric and come in a range of sizes to accommodate different substrate sizes and production volumes. Some ovens are equipped with conveyor systems for moving the substrates through the oven, while others require manual loading and unloading.
Powder Recovery System
The powder recovery system is used to collect and recycle the excess powder that does not adhere to the substrate during the powder application process. This system typically consists of a cyclone separator, which uses centrifugal force to separate the powder from the air, and a sieve, which removes any contaminants or clumps from the recovered powder.
By recycling the excess powder, the powder recovery system helps to minimize waste and reduce the overall cost of the powder coating process.
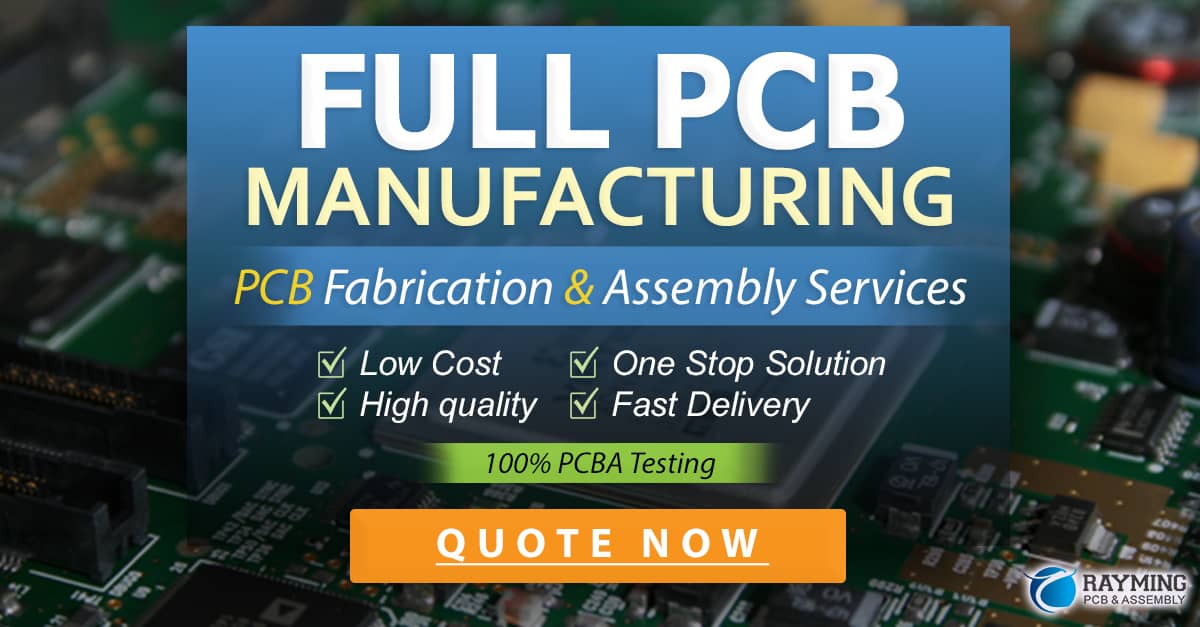
Frequently Asked Questions (FAQ)
1. What types of substrates can be powder coated?
Powder coating can be applied to a wide range of substrates, including metals (such as steel, aluminum, and brass), plastics, and even wood. However, the substrate must be able to withstand the high temperatures required for the curing process, typically between 350°F and 400°F (175°C and 205°C).
2. How durable is a powder coated finish?
Powder coated finishes are highly durable and resistant to abrasion, corrosion, and UV radiation. They typically offer better performance and longevity compared to traditional liquid coatings, such as paint.
3. Can powder coatings be applied in different colors and finishes?
Yes, powder coatings are available in a wide range of colors, textures, and finishes, including matte, gloss, and metallic. This allows for greater customization and design flexibility compared to other coating methods.
4. Is powder coating an environmentally friendly process?
Yes, powder coating is considered a more environmentally friendly process compared to traditional liquid coatings, as it contains no solvents and produces minimal volatile organic compounds (VOCs). Additionally, the ability to recycle and reuse the excess powder helps to reduce waste and minimize the environmental impact of the coating process.
5. How long does the powder coating process take?
The duration of the powder coating process can vary depending on several factors, such as the size and complexity of the substrate, the type of powder being used, and the curing time required. However, in general, the entire process can be completed in a matter of hours, making it a relatively fast and efficient coating method.
Conclusion
Powder spray coating is a versatile and efficient method for applying a durable, high-quality finish to a wide range of substrates. By understanding the key steps involved in the process, as well as the equipment and materials used, manufacturers can optimize their powder coating operations to achieve the best possible results.
With its environmental friendliness, durability, and design flexibility, powder coating is an increasingly popular choice for industries ranging from automotive and aerospace to furniture and appliances. As technology continues to advance, it is likely that the powder spray process will continue to evolve and improve, offering even greater benefits and opportunities for manufacturers and consumers alike.
0 Comments