Understanding Thermal Resistance
Thermal resistance is a measure of a material’s ability to resist heat flow. In the context of PCBs, thermal resistance refers to the board’s capacity to dissipate heat generated by the mounted electronic components. It is expressed in units of degrees Celsius per watt (°C/W) and represents the temperature difference between two points on the PCB divided by the power dissipated.
The thermal resistance of a PCB is crucial because it directly impacts the operating temperature of the electronic components. Excessive heat can lead to component failure, reduced performance, and shortened lifespan. Therefore, designing PCBs with optimal thermal resistance is essential for ensuring the reliability and longevity of electronic devices.
Factors Influencing Thermal Resistance
Several factors contribute to the thermal resistance of a PCB:
-
PCB Material: The choice of PCB substrate material significantly influences thermal resistance. Common materials include FR-4, which is a glass-reinforced epoxy laminate, and metal core PCBs (MCPCBs), which feature a metal core for enhanced heat dissipation.
-
PCB Thickness: Thicker PCBs generally have lower thermal resistance due to their increased cross-sectional area, which allows for better heat conduction.
-
Copper Thickness: The thickness of the copper traces on the PCB affects thermal resistance. Thicker copper layers provide better heat conduction and help dissipate heat more efficiently.
-
Component Placement: The placement of components on the PCB can impact thermal resistance. Proper component spacing and arrangement can facilitate heat dissipation and prevent hotspots.
-
Thermal Vias: Thermal vias are small holes drilled through the PCB to transfer heat from one layer to another. They help conduct heat away from components and improve overall thermal performance.
-
Airflow: The presence of adequate airflow around the PCB can help dissipate heat through convection. Proper ventilation and cooling mechanisms, such as heatsinks and fans, can significantly reduce thermal resistance.
Measuring Thermal Resistance
Accurately measuring the thermal resistance of a PCB is crucial for validating thermal design and ensuring proper heat dissipation. There are several methods for measuring thermal resistance:
1. Thermal Imaging
Thermal imaging, also known as infrared thermography, is a non-contact method that uses an infrared camera to capture the temperature distribution across the PCB surface. By analyzing the thermal images, designers can identify hotspots, evaluate the effectiveness of cooling solutions, and calculate the thermal resistance between different points on the board.
2. Thermocouples
Thermocouples are temperature sensors that consist of two dissimilar metals joined together at one end. By attaching thermocouples to specific locations on the PCB and measuring the temperature difference between them, designers can calculate the thermal resistance using Ohm’s law for thermal circuits.
3. Thermal Test Chips
Thermal test chips are specialized integrated circuits designed to measure thermal resistance. These chips contain temperature-sensitive elements and can be mounted on the PCB at critical locations. By applying a known power to the test chip and measuring the resulting temperature change, designers can accurately determine the thermal resistance.
Optimizing Thermal Resistance
Minimizing the thermal resistance of a PCB is essential for ensuring optimal performance and reliability. Here are some strategies for optimizing thermal resistance:
-
Material Selection: Choose PCB materials with higher thermal conductivity, such as MCPCBs or high-performance laminates, to enhance heat dissipation.
-
Increase Copper Thickness: Increasing the thickness of the copper layers on the PCB improves heat conduction and reduces thermal resistance. This can be achieved through thicker copper foils or additional copper layers.
-
Optimize Component Placement: Carefully plan the placement of components on the PCB to minimize heat buildup and promote even heat distribution. Place high-power components away from heat-sensitive components and provide adequate spacing for heat dissipation.
-
Utilize Thermal Vias: Incorporate thermal vias in the PCB design to transfer heat from high-power components to other layers or to heatsinks. Thermal vias can be strategically placed near heat-generating components to improve heat conduction.
-
Implement Heatsinks: Attach heatsinks to high-power components to facilitate heat dissipation. Heatsinks increase the surface area for heat transfer and help convect heat away from the PCB.
-
Ensure Proper Ventilation: Design the enclosure or housing of the electronic device to allow for adequate airflow around the PCB. Proper ventilation helps remove heat through convection and prevents heat buildup.
-
Consider Thermal Interface Materials: Use thermal interface materials (TIMs), such as thermal pads or thermal adhesives, to improve heat transfer between components and heatsinks or between the PCB and the enclosure.
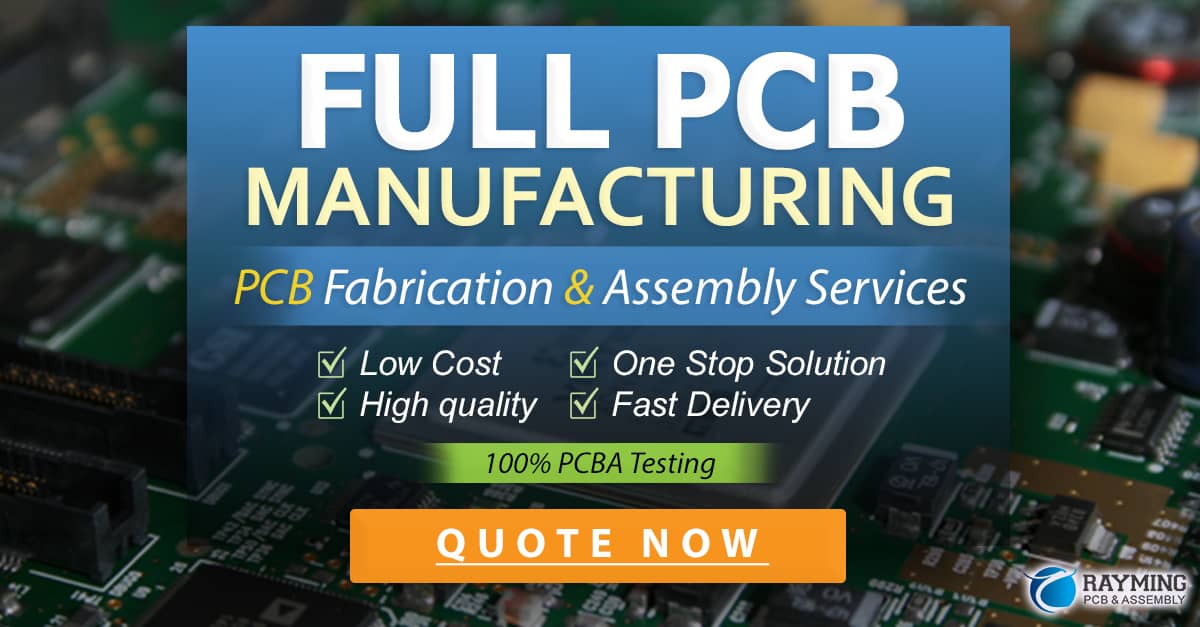
Thermal Resistance Calculation
To calculate the thermal resistance of a PCB, you need to know the temperature difference between two points on the board and the power dissipated. The thermal resistance (Rth) can be calculated using the following formula:
Rth = ΔT / P
Where:
– Rth is the thermal resistance in °C/W
– ΔT is the temperature difference between two points on the PCB in °C
– P is the power dissipated in watts (W)
For example, if the temperature difference between two points on a PCB is 20°C and the power dissipated is 5W, the thermal resistance can be calculated as follows:
Rth = 20°C / 5W = 4°C/W
Thermal Resistance of Common PCB Materials
The thermal resistance of a PCB depends on the material used for the substrate. Here is a table comparing the thermal resistance of common PCB materials:
Material | Thermal Conductivity (W/mK) | Thermal Resistance (°C/W) |
---|---|---|
FR-4 | 0.3 – 0.4 | 8 – 10 |
Polyimide | 0.2 – 0.3 | 10 – 15 |
Alumina | 20 – 30 | 0.3 – 0.5 |
Aluminum | 150 – 220 | 0.05 – 0.07 |
Copper | 385 – 400 | 0.025 – 0.026 |
As seen from the table, materials with higher thermal conductivity, such as aluminum and copper, have lower thermal resistance compared to materials like FR-4 and polyimide.
FAQ
-
What is thermal resistance in PCBs?
Thermal resistance in PCBs refers to the board’s ability to resist heat flow and dissipate heat generated by the mounted electronic components. It is measured in units of degrees Celsius per watt (°C/W). -
Why is thermal resistance important in PCB design?
Thermal resistance is crucial in PCB design because it directly affects the operating temperature of electronic components. High thermal resistance can lead to excessive heat buildup, which can cause component failure, reduced performance, and shortened lifespan. -
What factors influence the thermal resistance of a PCB?
Several factors influence the thermal resistance of a PCB, including the choice of PCB material, PCB thickness, copper thickness, component placement, the presence of thermal vias, and airflow around the board. -
How can thermal resistance be measured in PCBs?
Thermal resistance can be measured using techniques such as thermal imaging, thermocouples, and thermal test chips. These methods involve measuring the temperature difference between two points on the PCB and calculating the thermal resistance based on the power dissipated. -
What are some strategies for optimizing thermal resistance in PCBs?
Strategies for optimizing thermal resistance in PCBs include selecting materials with higher thermal conductivity, increasing copper thickness, optimizing component placement, utilizing thermal vias, implementing heatsinks, ensuring proper ventilation, and using thermal interface materials.
Conclusion
Thermal resistance is a critical parameter in PCB design that directly impacts the performance and reliability of electronic devices. By understanding the factors that influence thermal resistance and implementing appropriate design strategies, engineers can optimize the thermal performance of PCBs.
Measuring thermal resistance using techniques like thermal imaging, thermocouples, and thermal test chips allows designers to validate their thermal designs and make necessary adjustments. By selecting suitable materials, optimizing component placement, utilizing thermal vias, and implementing effective cooling solutions, designers can minimize thermal resistance and ensure the long-term reliability of electronic components.
As electronic devices continue to become more compact and powerful, managing thermal resistance in PCBs will remain a crucial aspect of electronic design. By staying updated with the latest materials, technologies, and design practices, engineers can overcome thermal challenges and create PCBs that meet the demanding requirements of modern electronics.
0 Comments