Understanding Solder and Its Composition
Solder is an alloy, typically composed of tin (Sn) and lead (Pb), although lead-free alternatives are increasingly common due to environmental and health concerns. The specific composition of solder can vary depending on the intended application and desired properties.
Common Types of Solder
- Lead-based Solder:
- Tin-lead (Sn-Pb) solder is the most traditional type, with a typical composition of 60% tin and 40% lead (60/40).
-
Other common ratios include 63/37 and 50/50.
-
Lead-free Solder:
- Due to regulations such as the Restriction of Hazardous Substances (RoHS) directive, lead-free solders have gained popularity.
- Common lead-free solder alloys include:
- Tin-silver-copper (Sn-Ag-Cu or SAC): Typically contains 95.5% tin, 3.8% silver, and 0.7% copper (SAC305).
- Tin-copper (Sn-Cu): Usually contains 99.3% tin and 0.7% copper.
- Tin-silver (Sn-Ag): Commonly contains 96.5% tin and 3.5% silver.
Melting Point of Solder
The melting point of solder is a critical property that determines its suitability for various applications. It is the temperature at which the solder transitions from a solid to a liquid state.
Factors Affecting solder melting point
Several factors influence the melting point of solder:
- Composition:
- The ratio of tin to lead (or other elements in lead-free solders) significantly affects the melting point.
-
Higher lead content generally results in a lower melting point.
-
Impurities:
- The presence of impurities, such as oxidation or contamination, can alter the melting point of solder.
-
Oxidation can increase the melting point, while certain contaminants may lower it.
-
Heating Rate:
- The rate at which solder is heated can influence its melting behavior.
- Rapid heating may cause the solder to melt at a slightly higher temperature compared to slow, gradual heating.
Melting Points of Common Solder Alloys
The following table presents the melting points of some common solder alloys:
Solder Alloy | Composition | Melting Point (°C) | Melting Point (°F) |
---|---|---|---|
Sn60Pb40 | 60% Sn, 40% Pb | 183-188 | 361-370 |
Sn63Pb37 | 63% Sn, 37% Pb | 183 | 361 |
Sn50Pb50 | 50% Sn, 50% Pb | 183-216 | 361-421 |
SAC305 | 96.5% Sn, 3% Ag, 0.5% Cu | 217-220 | 423-428 |
Sn99.3Cu0.7 | 99.3% Sn, 0.7% Cu | 227 | 441 |
Sn96.5Ag3.5 | 96.5% Sn, 3.5% Ag | 221 | 430 |
It’s important to note that the melting points provided are approximate and can vary slightly based on factors such as heating rate and impurities.
Importance of Solder Melting Point
Understanding the melting point of solder is crucial for several reasons:
- Soldering Process:
- The melting point determines the temperature range required for successful soldering.
-
Insufficient heating may result in poor bonding, while excessive heating can damage components or cause unwanted melting of adjacent materials.
-
Component Compatibility:
- The melting point of solder must be lower than the maximum temperature that the components being soldered can withstand.
-
Exceeding the temperature limit of components can lead to damage or failure.
-
Rework and Repair:
- When reworking or repairing soldered joints, knowledge of the solder’s melting point is essential to avoid overheating and potential damage.
-
Selecting a solder with a suitable melting point can facilitate easier rework processes.
-
Manufacturing Processes:
- In automated soldering processes, such as wave soldering or reflow soldering, the melting point of the solder dictates the temperature profile and process parameters.
- Accurate control of the soldering temperature is necessary to ensure consistent and reliable results.
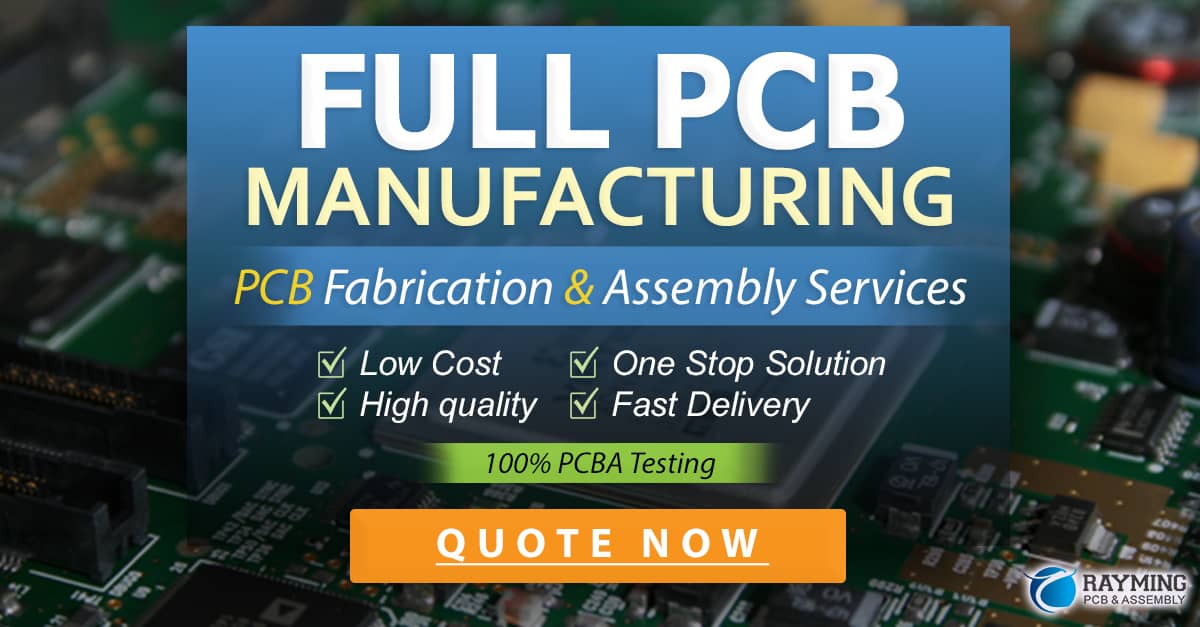
Choosing the Right Solder
When selecting solder for a specific application, consider the following factors:
- Melting Point:
- Choose a solder with a melting point that is appropriate for the components being soldered and the manufacturing process.
-
Consider the maximum temperature tolerance of the components and ensure the solder’s melting point is sufficiently lower.
-
Composition:
- Determine whether lead-based or lead-free solder is required based on regulations, environmental considerations, and the specific application.
-
Lead-free solders typically have higher melting points compared to lead-based solders.
-
Wetting and Flow Characteristics:
- Assess the wetting and flow properties of the solder, which affect its ability to form reliable and consistent solder joints.
-
Good wetting ensures proper adhesion and coverage, while good flow allows the solder to fill gaps and create strong bonds.
-
Mechanical Strength:
- Consider the mechanical strength requirements of the soldered joints.
-
Some solder alloys, such as those containing silver, offer improved mechanical strength compared to standard tin-lead solders.
-
Compatibility with Surface Finishes:
- Ensure that the chosen solder is compatible with the surface finishes of the components and printed circuit boards (PCBs) being soldered.
- Certain surface finishes, such as nickel or gold, may require specific solder alloys for optimal bonding.
Soldering Techniques and Temperature Control
Proper soldering techniques and temperature control are essential to achieve reliable and high-quality solder joints. Here are some key considerations:
- Soldering Iron Temperature:
- Set the soldering iron temperature based on the melting point of the solder being used.
- A general guideline is to set the temperature approximately 30-50°C (54-90°F) above the solder’s melting point.
-
Excessive temperatures can cause oxidation, damage components, or lead to unwanted melting of adjacent materials.
-
Preheating:
- Preheating the components and PCB can help reduce thermal shock and improve solder flow.
-
Gradual preheating is particularly important for larger components or assemblies to minimize the risk of damage due to rapid temperature changes.
-
Soldering Time:
- Minimize the time the soldering iron is in contact with the components and PCB to avoid overheating.
-
Prolonged heat exposure can degrade the solder joint quality and potentially damage sensitive components.
-
Tip Size and Shape:
- Select an appropriate soldering iron tip size and shape based on the size and accessibility of the solder joints.
-
A tip that is too large may apply excessive heat, while a tip that is too small may not provide sufficient heat transfer.
-
Cleanliness:
- Ensure that the surfaces to be soldered are clean and free from contaminants, such as oils, dirt, or oxidation.
- Clean surfaces promote better solder wetting and help form reliable solder joints.
Frequently Asked Questions (FAQ)
-
Q: What is the most common type of solder used in electronics?
A: The most common type of solder used in electronics is lead-free solder, particularly SAC305, which contains 96.5% tin, 3% silver, and 0.5% copper. This is due to regulations that restrict the use of lead in electronic products. -
Q: Can lead-free solder be used with components that are rated for lead-based solder?
A: In most cases, lead-free solder can be used with components rated for lead-based solder. However, it’s essential to consider the higher melting point of lead-free solders and ensure that the components can withstand the required soldering temperature. -
Q: How does the melting point of solder affect the soldering process?
A: The melting point of solder determines the temperature range required for successful soldering. It influences the selection of soldering iron temperature, preheating requirements, and the overall soldering process parameters. -
Q: Can solder with a higher melting point be used for applications that require higher temperature resistance?
A: Yes, solders with higher melting points, such as high-temperature lead-free solders or specialty alloys, can be used for applications that demand higher temperature resistance. These solders provide improved thermal stability and reduce the risk of joint failure due to elevated temperatures. -
Q: How can I determine the melting point of a specific solder alloy?
A: The melting point of a specific solder alloy can be determined by referring to the manufacturer’s specifications or technical data sheets. Additionally, there are online resources and reference tables that provide melting point information for common solder alloys.
Conclusion
Understanding the melting point of solder is crucial for achieving reliable and high-quality solder joints in various applications. The melting point is influenced by factors such as composition, impurities, and heating rate. Choosing the right solder based on its melting point, composition, and other properties is essential for ensuring compatibility with components and manufacturing processes.
Proper soldering techniques, including temperature control, preheating, and cleanliness, play a vital role in obtaining optimal results. By considering the melting point of solder and following best practices, manufacturers and technicians can produce robust and dependable soldered assemblies.
As technology advances and regulations evolve, the development of new solder alloys with tailored melting points and enhanced properties will continue to shape the electronics and metalworking industries. Staying informed about the latest advancements and guidelines related to solder melting points is essential for professionals working in these fields.
0 Comments