Understanding Thermal Pads
What are Thermal Pads?
Thermal pads are thin, flexible materials that are placed between electronic components and heat sinks to enhance heat dissipation. They are typically made from materials with high thermal conductivity, such as silicone, polyurethane, or various filled elastomers. These pads are designed to conform to the surface of the components, filling any air gaps and ensuring optimal thermal contact.
Properties of Thermal Pads
The effectiveness of a thermal pad is determined by several key properties:
-
Thermal Conductivity: This refers to the material’s ability to transfer heat. Higher thermal conductivity values indicate better heat dissipation capabilities. Common thermal pad materials have thermal conductivity values ranging from 0.5 to 10 W/mK.
-
Thickness: Thermal pads come in various thicknesses to accommodate different component heights and gap sizes. Thinner pads generally provide better thermal performance, but thicker pads may be necessary for larger gaps or uneven surfaces.
-
Compressibility: The compressibility of a thermal pad determines how well it conforms to the surfaces of the component and heat sink. A more compressible pad will fill air gaps more effectively, improving thermal contact.
-
Electrical Insulation: Some thermal pads are designed to provide electrical insulation between the component and heat sink, preventing short circuits and ensuring the safety of the device.
Types of Thermal Pads
There are several types of thermal pads available, each with its own unique properties and applications.
Silicone Thermal Pads
Silicone thermal pads are widely used in the electronics industry due to their excellent thermal conductivity, flexibility, and durability. They are available in various thicknesses and can be easily cut to size. Silicone pads are also known for their high compressibility, making them suitable for applications with uneven surfaces.
Polyurethane Thermal Pads
Polyurethane thermal pads offer a balance between thermal conductivity and electrical insulation. They are often used in applications where both heat dissipation and electrical safety are critical. Polyurethane pads are also resistant to tearing and puncturing, making them a durable choice for demanding environments.
Phase Change Materials (PCMs)
Phase change materials are a special type of thermal pad that changes from a solid to a soft, pliable state at a specific temperature. This allows the material to conform to the surface of the component and heat sink, providing excellent thermal contact. PCMs are often used in high-performance applications where optimal heat dissipation is essential.
Applications of Thermal Pads in Circuit Board Manufacturing
Thermal pads are used in a wide range of electronic devices and applications, including:
-
Smartphones and Tablets: Thermal pads are used to dissipate heat generated by processors, batteries, and other components in mobile devices, ensuring optimal performance and preventing overheating.
-
Laptops and Computers: In laptops and desktop computers, thermal pads are used to transfer heat from CPUs, GPUs, and other high-performance components to heat sinks and cooling systems.
-
Power Electronics: Thermal pads are essential in power electronic applications, such as motor drives, inverters, and power supplies, where efficient heat dissipation is critical for reliable operation and longevity.
-
Automotive Electronics: In the automotive industry, thermal pads are used in various electronic systems, including engine control units, infotainment systems, and advanced driver assistance systems (ADAS), to ensure proper functioning in harsh environmental conditions.
-
LED Lighting: Thermal pads play a crucial role in LED lighting applications, helping to dissipate heat generated by the LEDs and maintain optimal brightness and color consistency.
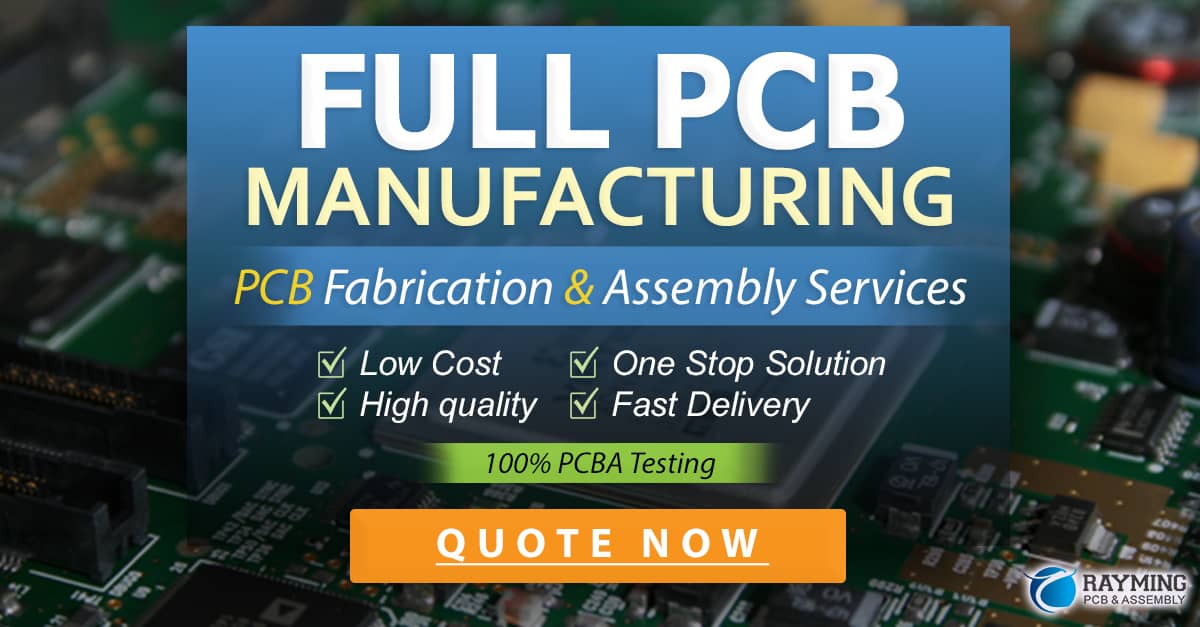
Selecting the Right Thermal Pad
Choosing the appropriate thermal pad for a specific application involves considering several factors:
-
Thermal Conductivity: Select a thermal pad with a thermal conductivity value that meets the heat dissipation requirements of the application.
-
Thickness: Consider the gap size between the component and heat sink, and choose a thermal pad thickness that will provide optimal thermal contact without excessive compression.
-
Compressibility: Evaluate the surface irregularities of the component and heat sink, and select a thermal pad with the appropriate compressibility to ensure good thermal contact.
-
Electrical Insulation: If electrical insulation is required, choose a thermal pad with the necessary dielectric properties to prevent short circuits and ensure device safety.
-
Operating Temperature: Consider the expected operating temperature range of the device and select a thermal pad that can withstand those temperatures without degrading or losing its properties.
Thermal Pad Application Process
Proper application of thermal pads is essential for achieving optimal thermal performance. The following steps outline the general process for applying thermal pads in circuit board manufacturing:
-
Surface Preparation: Clean the surfaces of the component and heat sink to remove any dirt, dust, or residue that may impede thermal contact.
-
Cutting the Thermal Pad: Cut the thermal pad to the appropriate size, ensuring that it covers the entire surface area of the component without overlapping or extending beyond the edges.
-
Applying the Thermal Pad: Remove the protective liner from one side of the thermal pad and place it on the surface of the component. Press the pad gently to ensure good adhesion.
-
Assembling the Heat Sink: Remove the protective liner from the other side of the thermal pad and place the heat sink on top of the pad. Apply even pressure to ensure good thermal contact between the pad, component, and heat sink.
-
Securing the Assembly: If necessary, use mechanical fasteners or clips to secure the heat sink in place, ensuring that the thermal pad remains compressed and in good contact with the surfaces.
Frequently Asked Questions (FAQ)
-
Q: Can thermal pads be reused?
A: No, thermal pads should not be reused. Once a thermal pad has been compressed and exposed to heat, its properties may degrade, reducing its effectiveness in subsequent applications. -
Q: How often should thermal pads be replaced?
A: Thermal pads should be replaced whenever the device is disassembled for maintenance or repairs. If the thermal pad shows signs of damage, such as tearing or excessive compression, it should be replaced immediately. -
Q: Can thermal pads be used in conjunction with thermal paste?
A: While thermal pads and thermal paste can be used together, it is generally not recommended. Thermal pads are designed to provide a complete thermal interface, and adding thermal paste may create uneven surfaces or air gaps, reducing the overall thermal performance. -
Q: Are there any environmental concerns associated with thermal pads?
A: Some thermal pads may contain materials that are not environmentally friendly, such as certain fillers or additives. When selecting a thermal pad, consider choosing products that are RoHS (Restriction of Hazardous Substances) compliant and free from harmful substances. -
Q: Can thermal pads be cut to custom shapes and sizes?
A: Yes, most thermal pads can be easily cut to custom shapes and sizes using scissors or a utility knife. This allows for precise fitting and coverage of components with unique geometries.
Conclusion
Thermal pads are a critical component in circuit board manufacturing, ensuring efficient heat dissipation and the proper functioning of electronic devices. By understanding the properties, types, and applications of thermal pads, engineers and manufacturers can make informed decisions when selecting the appropriate thermal interface material for their projects.
Proper application and maintenance of thermal pads are essential for achieving optimal thermal performance and prolonging the life of electronic components. As technology continues to advance and power densities increase, the importance of effective thermal management solutions, such as thermal pads, will only continue to grow.
Property | Silicone Thermal Pads | Polyurethane Thermal Pads | Phase Change Materials (PCMs) |
---|---|---|---|
Thermal Conductivity | High | Moderate | High |
Flexibility | High | Moderate | Low (solid state), High (soft state) |
Electrical Insulation | Low | High | Varies |
Durability | High | High | Moderate |
Compressibility | High | Moderate | High (soft state) |
Typical Applications | General electronics, Uneven surfaces | Power electronics, Insulation-critical applications | High-performance electronics, Optimal thermal contact |
By carefully considering the properties and characteristics of different thermal pad materials, manufacturers can select the most suitable option for their specific application, ensuring optimal heat dissipation, reliability, and performance in their circuit board designs.
0 Comments