Introduction to PCB trace width
Printed Circuit Board (PCB) design is a complex process that involves various factors, including component placement, routing, and trace width. Among these factors, trace width plays a crucial role in ensuring the proper functioning and reliability of the PCB. In this article, we will explore the importance of PCB trace width, its impact on PCB performance, and the factors that influence trace width selection.
What is PCB Trace Width?
PCB trace width refers to the width of the copper tracks that connect various components on a PCB. These traces carry electrical signals and power between components, and their width directly affects the electrical characteristics of the circuit. Trace width is typically measured in mils (thousandths of an inch) or millimeters.
Factors Affecting PCB Trace Width Selection
Several factors influence the selection of appropriate trace widths in PCB design. Let’s discuss these factors in detail.
Current Carrying Capacity
One of the primary factors that determine trace width is the current carrying capacity. The amount of current flowing through a trace generates heat, which can lead to potential issues such as voltage drops, signal integrity problems, and even trace damage. To ensure that the traces can handle the required current without overheating, designers must select appropriate trace widths based on the maximum expected current.
The current carrying capacity of a trace is directly proportional to its cross-sectional area. Wider traces have a larger cross-sectional area and can carry more current compared to narrower traces. The relationship between trace width and current carrying capacity is governed by the following equation:
I = (ΔT × A) / (ρ × L)
Where:
– I is the maximum current in amperes (A)
– ΔT is the temperature rise above ambient in °C
– A is the cross-sectional area of the trace in square mils (sq. mils)
– ρ is the electrical resistivity of the trace material (copper) in ohm-inches (Ω-in)
– L is the length of the trace in inches (in)
To determine the appropriate trace width for a given current, designers can refer to standard trace width calculators or tables provided by PCB manufacturers. These resources take into account factors such as copper thickness, temperature rise, and trace length to provide recommended trace widths for various current levels.
Current (A) | Trace Width (mils) |
---|---|
0.5 | 10 |
1.0 | 20 |
2.0 | 40 |
3.0 | 60 |
4.0 | 80 |
Table 1: Recommended trace widths for different current levels (assuming 1 oz. copper and 10°C temperature rise)
Signal Integrity
Another critical factor that influences trace width selection is signal integrity. In high-speed digital circuits, the traces act as transmission lines, and their dimensions affect the propagation of signals. Improper trace widths can lead to issues such as reflections, crosstalk, and electromagnetic interference (EMI), which can degrade signal quality and cause system malfunctions.
To maintain signal integrity, designers must consider the characteristic impedance of the traces. The characteristic impedance depends on various factors, including trace width, trace thickness, dielectric constant of the PCB material, and the distance between the trace and the reference plane (ground or power plane). The goal is to match the characteristic impedance of the traces to the impedance of the source and load to minimize reflections and ensure proper signal propagation.
The characteristic impedance of a microstrip trace (trace on the outer layer of the PCB) can be calculated using the following equation:
Z₀ = 87 / √(ε_r + 1.41) × ln(5.98 × h / (0.8 × w + t))
Where:
– Z₀ is the characteristic impedance in ohms (Ω)
– ε_r is the dielectric constant of the PCB material
– h is the distance between the trace and the reference plane in mils
– w is the trace width in mils
– t is the trace thickness in mils
For stripline traces (traces embedded between two reference planes), the characteristic impedance equation is slightly different:
Z₀ = 60 / √ε_r × ln(4 × h / (0.67 × (0.8 × w + t)))
Designers often use impedance calculators or simulation tools to determine the appropriate trace widths and spacings for a given characteristic impedance and PCB stackup.
Manufacturing Constraints
PCB manufacturing capabilities and constraints also play a role in determining trace width. Different PCB fabrication processes have limitations on the minimum trace width and spacing they can reliably produce. These limitations are usually specified by the PCB manufacturer and are based on factors such as the type of equipment, etching process, and copper thickness.
For example, a standard PCB manufacturing process may have a minimum trace width and spacing of 5 mils (0.127 mm), while advanced processes can achieve trace widths and spacings down to 3 mils (0.076 mm) or even smaller. Designers must consider these manufacturing constraints when selecting trace widths to ensure that the PCB can be manufactured reliably and cost-effectively.
PCB Class | Minimum Trace Width (mils) | Minimum Spacing (mils) |
---|---|---|
Class 1 | 10 | 10 |
Class 2 | 8 | 8 |
Class 3 | 6 | 6 |
Class 4 | 4 | 4 |
Class 5 | 3 | 3 |
Table 2: PCB manufacturing classes and their corresponding minimum trace widths and spacings
PCB Space and Routing Considerations
PCB layout and routing considerations also influence trace width selection. In dense PCB designs with limited space, designers may need to use narrower traces to accommodate all the required connections and components. However, using narrower traces can increase the resistance and limit the current carrying capacity, which may require adjustments in other aspects of the design, such as copper thickness or layer count.
On the other hand, using wider traces can simplify the routing process and provide more flexibility in component placement. Wider traces are less susceptible to manufacturing defects and can help improve the overall reliability of the PCB.
Designers must strike a balance between trace width, routing efficiency, and manufacturing feasibility to create a PCB layout that meets the design requirements while being cost-effective and reliable.
Impact of PCB Trace Width on Performance
The selection of appropriate trace widths has a significant impact on various aspects of PCB performance. Let’s explore some of these impacts in detail.
Resistance and Voltage Drop
The resistance of a trace is inversely proportional to its cross-sectional area. Narrower traces have higher resistance compared to wider traces of the same length and thickness. This increased resistance can lead to voltage drops along the trace, which can affect the performance of the connected components.
The voltage drop across a trace can be calculated using Ohm’s law:
V = I × R
Where:
– V is the voltage drop in volts (V)
– I is the current flowing through the trace in amperes (A)
– R is the resistance of the trace in ohms (Ω)
The resistance of a trace can be calculated using the following equation:
R = ρ × L / A
Where:
– R is the resistance in ohms (Ω)
– ρ is the electrical resistivity of the trace material (copper) in ohm-meters (Ω-m)
– L is the length of the trace in meters (m)
– A is the cross-sectional area of the trace in square meters (m²)
To minimize voltage drops and ensure proper performance, designers must select trace widths that provide sufficiently low resistance for the expected current levels. This is particularly important for power supply traces, where excessive voltage drops can cause components to malfunction or fail.
Power Loss and Heat Generation
As current flows through a trace, it encounters resistance, which leads to power dissipation in the form of heat. The power loss in a trace is proportional to the square of the current and the resistance of the trace. Narrower traces, with their higher resistance, will generate more heat compared to wider traces carrying the same current.
The power loss in a trace can be calculated using the following equation:
P = I² × R
Where:
– P is the power loss in watts (W)
– I is the current flowing through the trace in amperes (A)
– R is the resistance of the trace in ohms (Ω)
Excessive heat generation can lead to several problems, such as increased temperature of the PCB and components, reduced reliability, and potential failure. To mitigate these issues, designers must ensure that the trace widths are adequate to handle the expected power dissipation without causing thermal problems.
In some cases, designers may need to use additional techniques to manage heat, such as using thicker copper, adding thermal vias, or implementing heat sinks or cooling solutions.
Electromagnetic Compatibility (EMC)
Trace width also plays a role in the electromagnetic compatibility (EMC) of a PCB. EMC refers to the ability of a device to function properly in its electromagnetic environment without causing or being susceptible to electromagnetic interference (EMI).
In high-speed digital circuits, traces can act as antennas, radiating electromagnetic energy that can cause interference with other devices. Narrower traces tend to have higher impedance and are more prone to EMI radiation compared to wider traces. On the other hand, wider traces can help reduce EMI by providing a lower impedance path for high-frequency currents.
To minimize EMI and ensure EMC compliance, designers must carefully select trace widths and spacings, especially for critical signals such as clocks, high-speed interfaces, and power supply lines. Proper grounding, shielding, and the use of ground planes can also help reduce EMI and improve EMC performance.
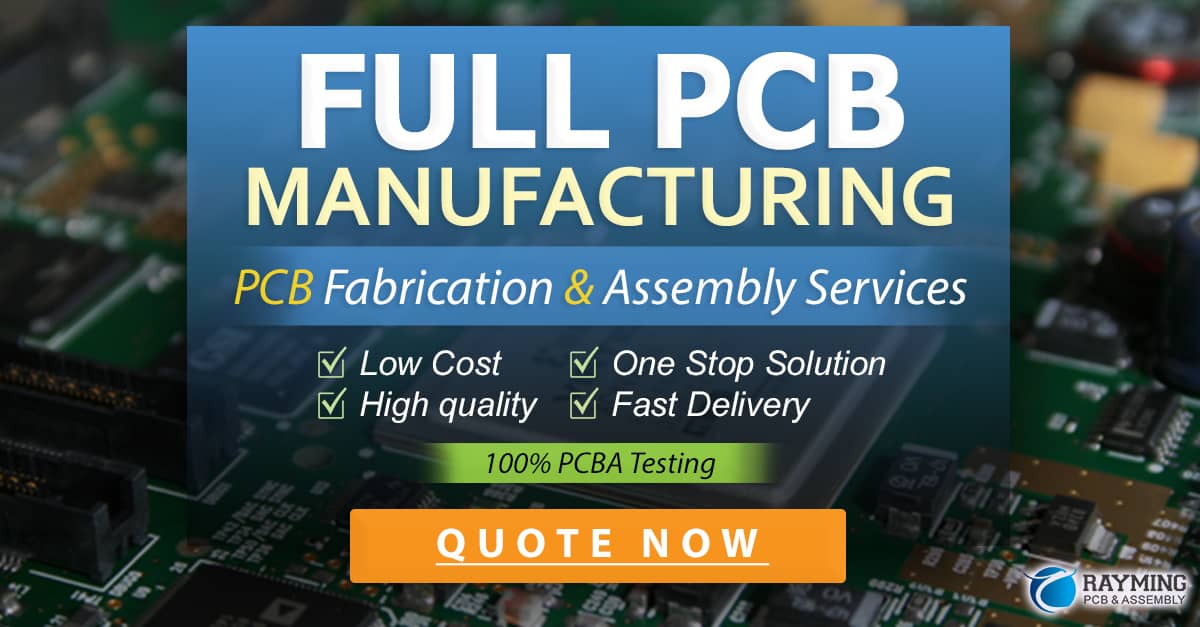
PCB Trace Width Design Guidelines
To ensure optimal performance and reliability of PCBs, designers should follow some general guidelines when selecting trace widths. These guidelines take into account the various factors discussed earlier, such as current carrying capacity, signal integrity, manufacturing constraints, and routing considerations.
-
Determine the maximum expected current for each trace and select the appropriate trace width based on the current carrying capacity tables or calculators provided by the PCB manufacturer.
-
Consider the characteristic impedance requirements for high-speed signals and select trace widths and spacings that match the desired impedance, taking into account the PCB stackup and material properties.
-
Adhere to the minimum trace width and spacing guidelines specified by the PCB manufacturing process to ensure manufacturability and reliability.
-
Use wider traces for power supply and ground connections to minimize voltage drops and heat generation.
-
Keep trace lengths as short as possible to reduce resistance and minimize signal integrity issues.
-
Avoid abrupt changes in trace width, as they can cause impedance discontinuities and reflections. Use gradual transitions or impedance matching techniques when necessary.
-
Consider the use of copper pours or ground planes to provide low-impedance return paths and improve EMI performance.
-
Perform signal integrity simulations and analysis to verify the performance of critical traces and make necessary adjustments to the trace widths and spacings.
-
Collaborate with the PCB manufacturer to ensure that the selected trace widths and spacings are compatible with their manufacturing capabilities and design rules.
By following these guidelines and carefully considering the various factors that influence trace width selection, designers can create PCBs that meet the required performance, reliability, and manufacturability goals.
Frequently Asked Questions (FAQ)
- What is the most important factor to consider when selecting PCB trace widths?
-
The most important factor to consider when selecting PCB trace widths is the current carrying capacity. Traces must be wide enough to handle the expected current without causing excessive voltage drops, heat generation, or reliability issues.
-
How does trace width affect signal integrity in high-speed PCBs?
-
Trace width affects the characteristic impedance of the traces in high-speed PCBs. Improper trace widths can cause impedance mismatches, leading to signal reflections, crosstalk, and other signal integrity issues. Designers must select trace widths that match the desired characteristic impedance to ensure proper signal propagation.
-
Can I use the same trace width for all the traces on my PCB?
-
No, it is not recommended to use the same trace width for all the traces on a PCB. Different traces have different requirements based on their function, current carrying capacity, and signal integrity needs. Power supply traces, for example, typically require wider widths compared to signal traces.
-
What are the consequences of using traces that are too narrow?
-
Using traces that are too narrow can lead to several problems, such as increased resistance, voltage drops, excessive heat generation, and reduced reliability. Narrow traces may also be more susceptible to manufacturing defects and can limit the current carrying capacity of the circuit.
-
How do I determine the appropriate trace width for a given current?
- To determine the appropriate trace width for a given current, you can refer to current carrying capacity tables or calculators provided by PCB manufacturers. These resources take into account factors such as copper thickness, temperature rise, and trace length to provide recommended trace widths for various current levels. Alternatively, you can use the trace width equations discussed in this article to calculate the required width based on the desired current and other parameters.
Conclusion
PCB trace width is a critical factor in the design and performance of printed circuit boards. Proper selection of trace widths ensures that the PCB can handle the required current, maintain signal integrity, and meet the necessary manufacturing and reliability standards.
Designers must consider various factors when choosing trace widths, including current carrying capacity, characteristic impedance, manufacturing constraints, and routing considerations. By following established design guidelines and collaborating with PCB manufacturers, designers can create PCBs that meet the desired performance and reliability goals while being cost-effective and manufacturable.
As PCB technology continues to advance, with higher speeds, greater densities, and more complex designs, the importance of proper trace width selection will only increase. Designers must stay updated with the latest industry standards, design tools, and manufacturing capabilities to ensure that they can create PCBs that meet the ever-evolving demands of modern electronics.
0 Comments