Introduction to PCB Plating Materials
Printed Circuit Boards (PCBs) are essential components in modern electronics, providing a platform for interconnecting electronic components. One crucial aspect of PCB manufacturing is the plating process, which involves applying a conductive layer onto the copper traces to enhance their electrical conductivity, solderability, and protection against corrosion. Various materials can be used for PCB plating, each with its own advantages and disadvantages. In this article, we will explore the cheapest material options for PCB plating and their properties.
Importance of Choosing the Right PCB Plating Material
Selecting the appropriate plating material for your PCB is critical for several reasons:
-
Conductivity: The plating material should provide excellent electrical conductivity to ensure efficient signal transmission and minimize resistance.
-
Solderability: The plated surface should allow for easy and reliable soldering of electronic components.
-
Corrosion Resistance: The plating material should protect the copper traces from oxidation and corrosion, ensuring the long-term reliability of the PCB.
-
Cost: Choosing a cost-effective plating material can help reduce overall production costs without compromising quality.
Common PCB Plating Materials
Before diving into the cheapest options, let’s briefly overview the most common PCB plating materials:
Gold (Au)
Gold is an excellent choice for PCB plating due to its outstanding conductivity, corrosion resistance, and solderability. However, it is also one of the most expensive options.
Silver (Ag)
Silver offers high conductivity and good solderability but is prone to oxidation and tarnishing over time. It is less expensive than gold but still relatively costly.
Nickel (Ni)
Nickel is often used as an undercoat for other plating materials, providing a barrier layer and improving adhesion. It offers good corrosion resistance but has lower conductivity compared to gold and silver.
Tin (Sn)
Tin is a popular choice for PCB plating due to its excellent solderability and relatively low cost. However, it has lower conductivity and corrosion resistance compared to gold and silver.
The Cheapest PCB Plating Materials
Now, let’s focus on the most cost-effective options for PCB plating:
1. Hot Air Solder Leveling (HASL)
HASL is a widely used and economical PCB plating method. In this process, the PCB is dipped into a molten solder bath, typically consisting of a tin-lead alloy. The excess solder is then blown off using hot air, resulting in a smooth, leveled surface. HASL offers several advantages:
- Low cost compared to other plating methods
- Good solderability
- Compatibility with a wide range of components
However, HASL also has some drawbacks:
- Uneven surface finish due to the nature of the process
- Potential for Solder Bridging and shorts
- Environmental concerns due to the use of lead (Pb) in the solder alloy
2. Immersion Tin (ISn)
Immersion tin plating is another cost-effective option for PCB plating. In this process, the copper traces are immersed in a tin solution, resulting in a thin, uniform layer of tin on the surface. Immersion tin offers several benefits:
- Relatively low cost compared to other plating methods
- Excellent solderability
- Flat and uniform surface finish
- RoHS compliance (lead-free)
However, immersion tin also has some limitations:
- Limited shelf life due to the formation of copper-tin intermetallic compounds
- Potential for Tin Whiskers, which can cause short circuits
- Lower conductivity compared to gold and silver
3. Organic Solderability Preservative (OSP)
OSP is a non-metallic coating applied to the copper traces to prevent oxidation and maintain solderability. It is one of the most cost-effective PCB plating options available. OSP has several advantages:
- Very low cost compared to other plating methods
- Excellent solderability
- Flat and uniform surface finish
- RoHS compliance (lead-free)
However, OSP also has some drawbacks:
- Limited shelf life, requiring proper storage and handling
- Potential for poor wetting during soldering if the OSP coating is damaged or contaminated
- Not suitable for high-temperature applications or multiple soldering cycles
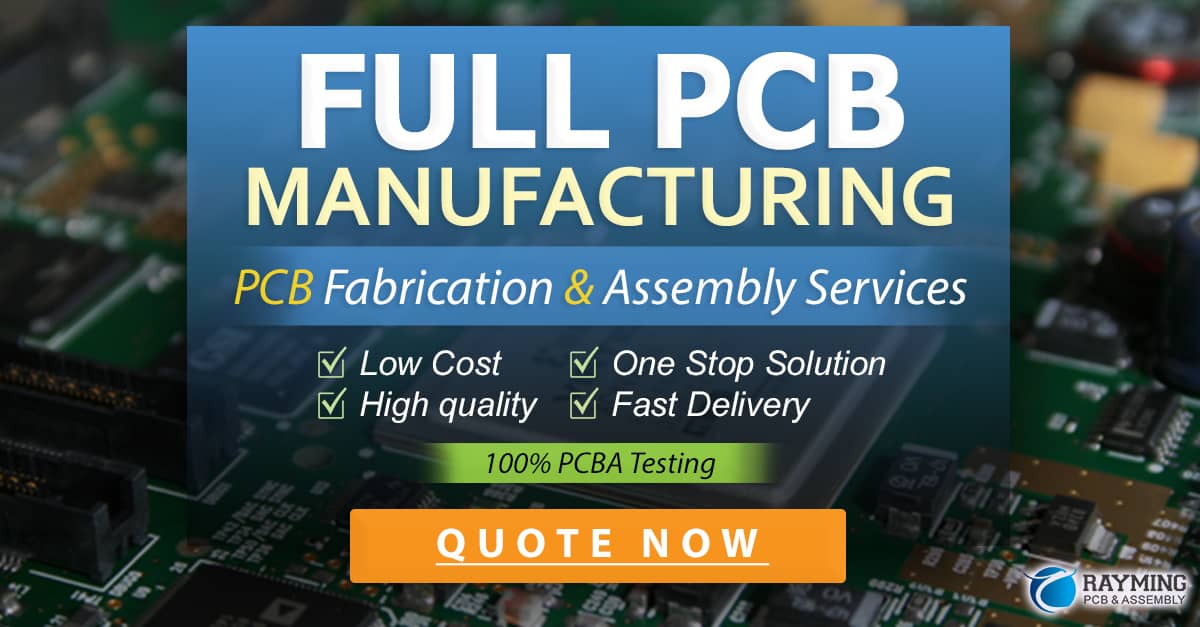
Cost Comparison of PCB Plating Materials
To better understand the cost differences between various PCB plating materials, let’s consider a hypothetical scenario of plating a 100 mm x 100 mm PCB with a copper thickness of 35 μm.
Plating Material | Approximate Cost per PCB |
---|---|
Gold (Au) | $5.00 – $10.00 |
Silver (Ag) | $3.00 – $6.00 |
Nickel (Ni) | $1.50 – $3.00 |
Tin (Sn) | $0.50 – $1.50 |
HASL | $0.20 – $0.50 |
Immersion Tin | $0.30 – $0.80 |
OSP | $0.10 – $0.30 |
Note: These costs are rough estimates and may vary depending on the specific manufacturer, location, and order quantity.
As evident from the table, OSP, HASL, and immersion tin are the most cost-effective options for PCB plating, with OSP being the cheapest among them.
Factors to Consider When Choosing a PCB Plating Material
While cost is an essential factor in selecting a PCB plating material, there are other important considerations to keep in mind:
-
Application Requirements: The choice of plating material should be based on the specific requirements of your application, such as conductivity, solderability, and environmental conditions.
-
Manufacturing Capabilities: Ensure that your chosen PCB Manufacturer has the necessary equipment and expertise to apply the selected plating material consistently and reliably.
-
Compliance with Standards: Consider any relevant industry standards or regulations, such as RoHS (Restriction of Hazardous Substances) or REACH (Registration, Evaluation, Authorization, and Restriction of Chemicals), when choosing a plating material.
-
Shelf Life and Storage: Some plating materials, such as OSP and immersion tin, have limited shelf life and require proper storage conditions to maintain their effectiveness.
-
Compatibility with Components: Ensure that the selected plating material is compatible with the components and soldering processes used in your PCB Assembly.
Conclusion
Choosing the cheapest material for PCB plating involves considering various factors, including cost, conductivity, solderability, corrosion resistance, and application requirements. OSP, HASL, and immersion tin emerge as the most cost-effective options, each with its own advantages and limitations. By carefully evaluating your specific needs and consulting with your PCB manufacturer, you can select the most suitable and economical plating material for your project.
Frequently Asked Questions (FAQ)
-
Q: What is the cheapest material for PCB plating?
A: Organic Solderability Preservative (OSP) is generally considered the cheapest material for PCB plating, followed by Hot Air Solder Leveling (HASL) and immersion tin. -
Q: Can I use OSP for high-temperature applications?
A: OSP is not recommended for high-temperature applications or multiple soldering cycles, as the coating may degrade under such conditions. -
Q: Is HASL a lead-free plating option?
A: Traditional HASL uses a tin-lead solder alloy, which contains lead (Pb). However, lead-free HASL options, such as tin-silver-copper (SAC) alloys, are available to meet RoHS compliance requirements. -
Q: What is the shelf life of immersion tin-plated PCBs?
A: The shelf life of immersion tin-plated PCBs is limited due to the formation of copper-tin intermetallic compounds. Typically, the shelf life is around 6-12 months, depending on storage conditions. -
Q: Can I use OSP for PCBs with fine-pitch components?
A: Yes, OSP is suitable for PCBs with fine-pitch components, as it provides a flat and uniform surface finish that facilitates accurate component placement and soldering.
0 Comments