What is Solder Wicking?
Solder wicking is a process that utilizes a specialized braided copper wire to absorb and remove excess or unwanted solder from a soldered joint or component. The braided wire, which is typically coated with a flux, is heated using a soldering iron. When the heated braid comes into contact with the molten solder, it wicks away the solder through capillary action, leaving a clean surface behind.
How Solder Wicking Works
The process of solder wicking relies on several key principles:
-
Capillary Action: The braided structure of the desoldering wick creates numerous small channels that facilitate the flow of molten solder. When the heated wick touches the solder, the solder is drawn into these channels through capillary action.
-
Heat Transfer: The copper braid is an excellent conductor of heat. When the soldering iron is applied to the wick, the heat is quickly transferred to the solder, causing it to melt and flow into the wick.
-
Flux: The solder wick is often pre-coated with a flux, which helps to break down oxidation and improve the wetting properties of the solder. This allows for more efficient solder removal and prevents the formation of unwanted residues.
Applications of Solder Wicking
Solder wicking finds numerous applications in the field of electronics, including:
-
Desoldering Components: When replacing or removing components from a PCB, solder wicking is an effective method for removing the solder that holds the component in place. By applying the heated wick to the soldered joints, the solder is absorbed, allowing the component to be easily lifted off the board.
-
Correcting Soldering Mistakes: Soldering errors, such as bridging between adjacent pads or applying too much solder, can be rectified using solder wicking. The excess solder is drawn away by the wick, leaving a clean and properly soldered joint.
-
Reworking and Repairing PCBs: In situations where a PCB needs to be repaired or modified, solder wicking is an indispensable tool. It allows for the precise removal of solder from specific areas, enabling the addition or removal of components, traces, or jumper wires.
-
Cleaning Solder Pads: Over time, solder pads on a PCB can become contaminated with oxidation, flux residue, or other impurities. Solder wicking can be used to clean these pads by removing the old solder and any associated contaminants, preparing the surface for fresh soldering.
Choosing the Right Solder Wick
When selecting a solder wick for your desoldering needs, consider the following factors:
-
Width: Solder wicks come in various widths to accommodate different sizes of solder joints. Choose a width that is appropriate for the scale of your work. Common widths include 0.8mm, 1.5mm, 2.0mm, and 2.5mm.
-
Flux Type: Solder wicks are available with different flux coatings, such as rosin (RMA), no-clean, or water-soluble. Select a flux type that is compatible with your soldering process and PCB materials.
-
Material: Most solder wicks are made from copper, but some specialty wicks may incorporate other materials like stainless steel or silver. Copper wicks are the most common and provide excellent heat transfer and absorption properties.
-
Quality: Opt for high-quality solder wicks from reputable manufacturers. Poor-quality wicks may have inconsistent braiding, ineffective flux coatings, or leave behind residues that can affect the integrity of your solder joints.
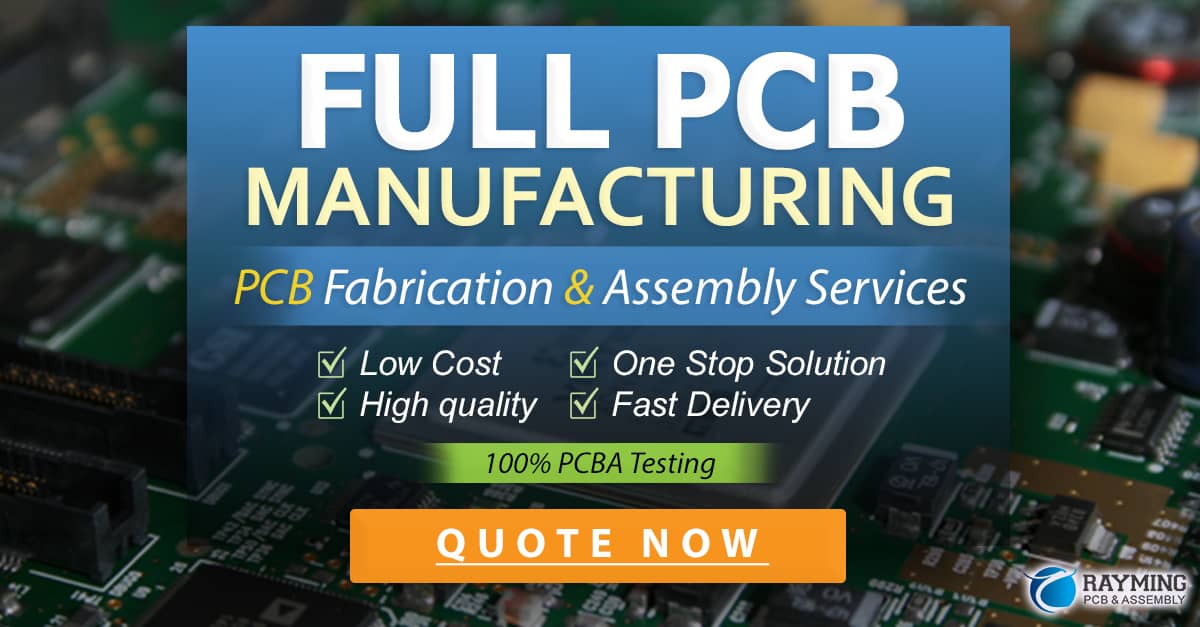
Best Practices for Using Solder Wick
To achieve the best results when using solder wick, follow these guidelines:
-
Use the Appropriate Temperature: Heat the soldering iron to the recommended temperature for the solder wick you are using. Excessive heat can damage the PCB or components, while insufficient heat may result in ineffective solder removal.
-
Apply Flux: If the solder wick is not pre-fluxed, apply a small amount of flux to the area you wish to desolder. This will help the solder to flow more easily and improve the wicking action.
-
Position the Wick Correctly: Place the solder wick flat against the soldered joint, ensuring good contact between the wick and the solder. Apply gentle pressure to maintain contact throughout the desoldering process.
-
Use a Clean Tip: Keep the soldering iron tip clean and well-tinned to ensure efficient heat transfer. A dirty or oxidized tip will hinder the desoldering process and may result in poor wicking performance.
-
Avoid Excessive Dwell Time: Do not leave the heated wick in contact with the PCB or component for an extended period. Prolonged exposure to heat can cause damage. Once the solder has been absorbed, remove the wick promptly.
-
Trim Used Wick: As you use the solder wick, the portion that has absorbed solder will become saturated and less effective. Trim off the used section of the wick using scissors or wire cutters to expose fresh, unsaturated braid.
-
Clean the PCB: After desoldering, use a brush or swab to remove any remaining flux residue from the PCB. This will help prevent corrosion and ensure a clean surface for subsequent soldering operations.
Common Mistakes to Avoid
When using solder wick, be aware of these common mistakes to ensure optimal results:
-
Applying Excessive Pressure: Pressing too hard on the solder wick can cause it to fray or break, reducing its effectiveness. Apply just enough pressure to maintain good contact with the solder.
-
Using a Wick That is Too Small: Choosing a solder wick that is too narrow for the job can result in incomplete solder removal or require multiple passes. Select a wick width that is appropriate for the size of the solder joint.
-
Overheating the PCB: Applying too much heat or leaving the soldering iron in contact with the PCB for too long can damage the board, lift pads, or cause delamination. Use the lowest effective temperature and minimize dwell time to prevent overheating.
-
Reusing Saturated Wick: Once a section of the solder wick becomes fully saturated with solder, it loses its ability to absorb more. Continuing to use a saturated wick will be ineffective and may even deposit solder back onto the joint. Always trim off used sections of the wick.
Alternatives to Solder Wicking
While solder wicking is a widely used method for desoldering, there are alternative tools and techniques available:
-
Desoldering Pump (Solder Sucker): A desoldering pump is a manual tool that uses suction to remove molten solder from a joint. It consists of a spring-loaded plunger that creates a vacuum when released, drawing the solder into the tool.
-
Desoldering Station: A desoldering station is an electric tool that combines a soldering iron with a vacuum pump. It heats the solder and simultaneously sucks it away from the joint, providing a more automated and controlled desoldering process.
-
Desoldering Tweezers: Desoldering tweezers are specialized pliers that have heated tips on both jaws. They are used to melt and remove solder from surface-mounted components by gripping the component leads and simultaneously applying heat.
Frequently Asked Questions (FAQ)
-
Can solder wick be reused?
A: While solder wick can be used multiple times, it is important to trim off the saturated sections and expose fresh braid for effective solder removal. Reusing heavily saturated wick will result in poor performance and may even redeposit solder onto the joint. -
How do I choose the right width of solder wick?
A: The width of the solder wick should be selected based on the size of the solder joint you are working with. For smaller joints, such as those found on surface-mounted components, a narrower wick (0.8mm to 1.5mm) is appropriate. For larger joints or through-hole components, wider wicks (2.0mm to 2.5mm) are more suitable. -
Can solder wick remove lead-free solder?
A: Yes, solder wick can be used to remove both leaded and lead-free solder. However, lead-free solder typically requires higher temperatures for melting, so ensure that your soldering iron is set to the appropriate temperature and that you are using a wick designed for lead-free applications. -
How do I prevent the solder wick from sticking to the soldering iron tip?
A: To prevent the solder wick from sticking to the soldering iron tip, ensure that the tip is clean and well-tinned. Apply a small amount of fresh solder to the tip before using the wick to improve heat transfer and prevent sticking. Additionally, avoid applying excessive pressure or leaving the wick in contact with the tip for too long. -
Can solder wick be used on sensitive components?
A: Solder wick can be used on most components, but extra care should be taken with sensitive components such as ICs, LEDs, and transistors. Use the lowest effective temperature and minimize the dwell time to prevent damage from overheating. In some cases, alternative desoldering methods, such as a desoldering station with adjustable temperature control, may be more suitable for sensitive components.
Conclusion
Solder wicking is an indispensable technique for anyone involved in electronics repair, rework, or prototyping. By understanding the principles behind solder wicking, selecting the appropriate wick, and following best practices, you can effectively remove unwanted solder and achieve clean, reliable solder joints. Whether you are a hobbyist or a professional, mastering the art of solder wicking will greatly enhance your ability to troubleshoot, modify, and repair electronic circuits.
Remember to always prioritize safety when working with soldering tools and materials. Use appropriate personal protective equipment, work in a well-ventilated area, and dispose of used solder wick responsibly. With practice and patience, you will develop the skills and confidence to tackle a wide range of desoldering tasks using solder wicking techniques.
0 Comments