Introduction to Solder mask dam
Solder mask dam, also known as SMD or solder mask defined pads, is a feature used in the design and manufacturing of printed circuit boards (PCBs). It involves creating a small barrier or “dam” of solder mask material around the copper pads where components will be soldered onto the PCB. This solder mask dam helps contain the molten solder during the assembly process, preventing solder bridges and improving the reliability of the solder joints.
In this comprehensive article, we will explore the concept of solder mask dam in detail, including its purpose, advantages, design considerations, and manufacturing processes. We will also address some frequently asked questions about solder mask dam to provide a thorough understanding of this important PCB feature.
The Purpose of Solder Mask Dam
Containing Molten Solder
The primary purpose of solder mask dam is to contain the molten solder during the reflow soldering process. When the PCB and its components are heated in a reflow oven, the solder paste melts and forms a liquid solder joint between the component leads and the copper pads. Without a solder mask dam, the molten solder could spread beyond the intended area, potentially causing short circuits or solder bridges between adjacent pads.
The solder mask dam acts as a physical barrier, preventing the molten solder from flowing outside the copper pad area. This containment ensures that the solder joint forms properly and remains confined to the desired location.
Preventing Solder Bridges
Solder bridges are unwanted connections that form between adjacent pads or traces due to the uncontrolled flow of molten solder. These bridges can cause short circuits, leading to malfunctions or even damage to the PCB and its components.
By using solder mask dam, the risk of solder bridges is significantly reduced. The dam provides a clear separation between the copper pads, making it less likely for the molten solder to bridge the gap and create an unintended connection.
Improving Solder Joint Reliability
Solder mask dam also contributes to the overall reliability of the solder joints. By containing the molten solder within a defined area, the dam helps ensure that the solder joint forms with the correct shape and volume. This promotes better mechanical strength and electrical conductivity of the joint.
Additionally, the solder mask dam can help prevent issues like solder balling or insufficiently wetted pads. Solder balling occurs when small spheres of solder form on the surface of the pad due to poor wetting or contamination. Insufficiently wetted pads happen when the molten solder fails to adhere properly to the copper surface. The presence of a solder mask dam can mitigate these issues by promoting better solder flow and adhesion.
Advantages of Solder Mask Dam
Enhanced Manufacturing Yield
One of the key advantages of using solder mask dam is the improvement in manufacturing yield. By reducing the occurrence of solder bridges and other soldering defects, solder mask dam helps minimize the number of PCBs that fail quality control inspections.
This enhanced manufacturing yield translates to cost savings for PCB manufacturers and their customers. Fewer defective boards mean less waste, rework, and production delays, ultimately leading to a more efficient and cost-effective manufacturing process.
Compatibility with Fine-Pitch Components
As electronic devices continue to shrink in size, the demand for PCBs with fine-pitch components has increased. Fine-pitch components have very small spacing between their leads, making it challenging to achieve reliable solder joints without the risk of solder bridges.
Solder mask dam is particularly beneficial for PCBs with fine-pitch components. The dam provides the necessary separation between the tightly spaced pads, ensuring that the molten solder remains confined to each individual pad. This compatibility with fine-pitch components enables the design and manufacturing of more compact and high-density PCBs.
Improved Aesthetics
In addition to its functional benefits, solder mask dam can also enhance the visual appearance of the PCB. The clean and well-defined edges of the copper pads created by the solder mask dam give the PCB a professional and aesthetically pleasing look.
This improved aesthetics can be especially important for PCBs used in consumer electronics or other applications where visual appeal is a consideration. A neat and visually appealing PCB can contribute to the overall perceived quality of the end product.
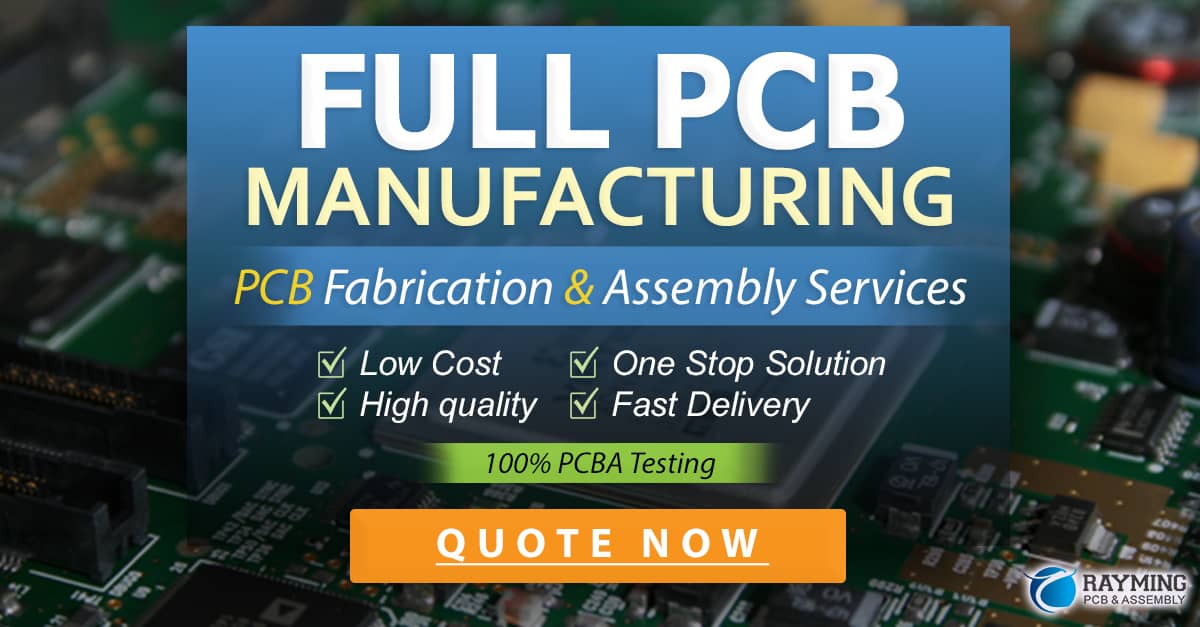
Design Considerations for Solder Mask Dam
Solder Mask Dam Width
When designing a PCB with solder mask dam, one of the key considerations is the width of the dam. The dam width refers to the distance between the edge of the copper pad and the edge of the solder mask opening.
The optimal dam width depends on various factors, including the size and pitch of the components, the soldering process used, and the PCB manufacturing capabilities. Generally, a wider dam provides better containment of the molten solder and reduces the risk of solder bridges. However, an excessively wide dam can make it difficult to properly align and place the components during assembly.
Typical dam widths range from 0.05mm to 0.15mm, depending on the specific requirements of the PCB design. It is important to consult with the PCB manufacturer and assembly provider to determine the appropriate dam width for a given project.
Copper Pad Size and Shape
The size and shape of the copper pads also play a role in the effectiveness of solder mask dam. The pads should be designed to accommodate the size and pitch of the component leads while providing sufficient area for a reliable solder joint.
When using solder mask dam, it is common to design the copper pads with a slightly larger size compared to non-dammed pads. This extra copper area compensates for the space taken up by the solder mask dam and ensures that there is enough exposed copper for proper soldering.
Additionally, the shape of the copper pads can impact the solder joint formation. Circular or oval pads are often preferred over rectangular pads because they promote better solder flow and reduce the risk of solder bridging at the corners.
Solder Mask Material Selection
The choice of solder mask material is another important consideration when using solder mask dam. The solder mask must be compatible with the PCB substrate material and the soldering process used.
Most commonly, liquid photoimageable (LPI) solder masks are used for solder mask dam applications. LPI solder masks are applied as a liquid coating and then exposed and developed using photolithography techniques to create the desired solder mask pattern.
LPI solder masks offer several advantages, including good resolution, durability, and resistance to chemical and environmental factors. They also provide a smooth and uniform surface finish, which is important for achieving consistent solder mask dam dimensions.
Other types of solder mask materials, such as dry film solder masks, can also be used for solder mask dam, depending on the specific requirements of the PCB design and manufacturing process.
Manufacturing Process for Solder Mask Dam
Solder Mask Application
The first step in creating solder mask dam is the application of the solder mask material onto the PCB. This is typically done using a screen printing or curtain coating process, depending on the type of solder mask used.
For LPI solder masks, the liquid solder mask is applied evenly across the surface of the PCB, covering both the copper traces and the areas where the solder mask dam will be formed. The thickness of the solder mask coating is carefully controlled to ensure consistent coverage and prevent any defects.
Solder Mask Exposure and Development
After the solder mask material is applied, it undergoes an exposure and development process to create the desired solder mask pattern, including the solder mask dam.
In the exposure step, the PCB is exposed to UV light through a photomask or phototool. The photomask contains the negative image of the solder mask pattern, allowing the UV light to selectively cure the solder mask material in the exposed areas.
Following exposure, the PCB is developed using a chemical solution that removes the uncured solder mask material. This development process reveals the copper pads and traces while leaving the cured solder mask in place, including the solder mask dam around the pads.
Solder Mask Curing
After the solder mask pattern is developed, the PCB undergoes a final curing process to fully harden and stabilize the solder mask material. This curing is typically done using heat, either in an oven or by passing the PCB through a hot air convection system.
The curing process ensures that the solder mask dam is fully formed and adhered to the PCB surface. It also improves the chemical and mechanical resistance of the solder mask, making it more durable and resistant to the stresses encountered during the soldering process.
Quality Control and Inspection
Throughout the manufacturing process, strict quality control measures are implemented to ensure that the solder mask dam meets the required specifications. This includes inspections at various stages, such as after solder mask application, exposure, development, and curing.
Common quality control methods for solder mask dam include:
- Visual inspection: Optically inspecting the PCB for any defects, such as incomplete solder mask coverage, bridging, or misalignment.
- Microscopic inspection: Using high-magnification microscopes to examine the solder mask dam dimensions and edges for consistency and accuracy.
- Automated optical inspection (AOI): Employing computer vision systems to automatically detect and classify solder mask defects based on predefined criteria.
- Electrical testing: Conducting electrical continuity and isolation tests to verify that the solder mask dam does not interfere with the intended electrical connections.
By implementing rigorous quality control processes, PCB manufacturers can ensure that the solder mask dam meets the required specifications and contributes to the overall reliability of the PCB assembly.
Frequently Asked Questions (FAQ)
1. What is the difference between solder mask dam and non-solder mask defined pads?
In a non-solder mask defined pad (NSMD) design, the copper pad extends slightly beyond the solder mask opening. The solder mask does not create a dam around the pad, and the molten solder can flow onto the exposed copper area.
In contrast, solder mask dam or solder mask defined (SMD) pads have the solder mask extending over the edge of the copper pad, creating a physical barrier that contains the molten solder within the pad area.
SMD pads offer better control over the solder joint formation and reduce the risk of solder bridging compared to NSMD pads.
2. Can solder mask dam be used with all types of components?
Solder mask dam is suitable for most surface mount components, including chip resistors, capacitors, inductors, and integrated circuits. It is particularly beneficial for components with fine pitch leads, such as QFPs, BGAs, and CSPs, where the risk of solder bridging is higher.
However, some components may have specific requirements or limitations regarding the use of solder mask dam. For example, certain high-power or high-frequency components may require larger copper pads or specific pad shapes that are not compatible with solder mask dam.
It is important to consult the component manufacturer’s guidelines and work closely with the PCB design and assembly teams to determine the suitability of solder mask dam for each component on the PCB.
3. How does solder mask dam affect the soldering process?
Solder mask dam can have a positive impact on the soldering process by promoting better solder joint formation and reducing the occurrence of soldering defects.
The dam helps contain the molten solder within the pad area, preventing solder spread and bridging. This containment ensures that the solder joint forms with the correct shape and volume, leading to improved mechanical strength and electrical conductivity.
Additionally, solder mask dam can help minimize issues like solder balling or insufficiently wetted pads by promoting better solder flow and adhesion to the copper surface.
However, it is important to note that the presence of solder mask dam may require adjustments to the soldering process parameters, such as solder paste stencil design, reflow profile, and component placement accuracy, to ensure optimal results.
4. Are there any challenges or limitations associated with using solder mask dam?
While solder mask dam offers many benefits, there are a few challenges and limitations to consider:
- Increased design complexity: Incorporating solder mask dam into the PCB design requires careful consideration of pad sizes, dam widths, and solder mask material selection. This added complexity may increase design time and effort.
- Manufacturing constraints: Not all PCB manufacturers have the capability to produce solder mask dam with the required accuracy and consistency. It is important to choose a manufacturer with experience and expertise in solder mask dam fabrication.
- Cost implications: Implementing solder mask dam may incur additional costs compared to non-dammed designs, due to the extra processing steps and quality control measures required.
- Component compatibility: Some components may not be suitable for use with solder mask dam due to their specific pad requirements or packaging constraints.
Despite these challenges, the benefits of solder mask dam often outweigh the limitations, particularly for PCBs with high-density and fine-pitch components.
5. How can I ensure the success of a PCB design with solder mask dam?
To ensure the success of a PCB design with solder mask dam, consider the following tips:
- Clearly communicate your requirements and expectations to the PCB design and manufacturing teams, including any specific standards or guidelines that need to be followed.
- Work closely with the component suppliers to obtain accurate dimensions and pad layout recommendations for each component used in the design.
- Use reputable PCB design software that supports solder mask dam features and can generate the necessary manufacturing files.
- Collaborate with the PCB manufacturer to determine the optimal solder mask dam parameters, such as dam width, pad size, and solder mask material, based on their capabilities and experience.
- Incorporate appropriate testing and inspection methods into the manufacturing process to verify the quality and consistency of the solder mask dam.
- Conduct thorough design reviews and prototyping to validate the PCB design and identify any potential issues early in the development cycle.
By following these guidelines and working closely with the PCB design and manufacturing teams, you can maximize the chances of success for your PCB design with solder mask dam.
Conclusion
Solder mask dam is a valuable feature in PCB design and manufacturing that offers numerous benefits, including better control over solder joint formation, reduced risk of solder bridging, improved manufacturing yields, and enhanced PCB aesthetics. By creating a physical barrier around the copper pads, solder mask dam helps contain molten solder and promotes more reliable and consistent solder joints.
When incorporating solder mask dam into a PCB design, it is important to consider factors such as dam width, copper pad size and shape, and solder mask material selection. Close collaboration between the PCB design, manufacturing, and assembly teams is essential to ensure the successful implementation of solder mask dam.
While there are some challenges and limitations associated with solder mask dam, the advantages it provides often justify its use, particularly for PCBs with high-density and fine-pitch components.
As technology continues to advance and electronic devices become increasingly compact and complex, the use of solder mask dam is likely to become even more prevalent in the PCB industry. By understanding the principles, benefits, and best practices associated with solder mask dam, PCB designers and manufacturers can leverage this feature to create more reliable, efficient, and visually appealing PCBs.
Comparison Table: Solder Mask Dam vs. Non-Solder Mask Defined Pads
Feature | Solder Mask Dam (SMD) | Non-Solder Mask Defined (NSMD) |
---|---|---|
Solder Mask Coverage | Solder mask extends over the edge of the copper pad | Copper pad extends beyond the solder mask opening |
Solder Containment | Better containment of molten solder within the pad area | Molten solder can flow onto the exposed copper area |
Solder Bridging Risk | Reduced risk of solder bridging between adjacent pads | Higher risk of solder bridging due to solder spread |
Manufacturing Yield | Improved manufacturing yield due to fewer soldering defects | Potentially lower manufacturing yield due to solder bridging |
Component Compatibility | Suitable for most surface mount components, especially fine-pitch | May be preferred for certain high-power or high-frequency components |
Design Complexity | Requires careful consideration of pad sizes, dam widths, and solder mask material | Simpler design, but may require larger pad spacing to avoid bridging |
Cost Implications | May incur additional costs due to extra processing steps and quality control | Generally less expensive than solder mask dam designs |
This table provides a side-by-side comparison of the key features and considerations for solder mask dam (SMD) and non-solder mask defined (NSMD) pad designs. It highlights the differences in solder mask coverage, solder containment, bridging risk, manufacturing yield, component compatibility, design complexity, and cost implications.
While solder mask dam offers several advantages, such as better solder containment and reduced bridging risk, NSMD pads may be preferred in certain situations, such as for high-power or high-frequency components that require specific pad configurations.
Ultimately, the choice between solder mask dam and NSMD pads depends on the specific requirements of the PCB design, the components used, and the manufacturing capabilities available. This comparison table aims to provide a clear overview of the key factors to consider when making this decision.
0 Comments