Table of Contents
- Introduction to Solder Bridging
- Causes of Solder Bridging
- Prevention Techniques
- Detecting Solder Bridges
- Repairing Solder Bridges
- Solder Bridging in Surface Mount Technology (SMT)
- Solder Bridging in Through-Hole Technology (THT)
- Tools and Equipment for Addressing Solder Bridging
- Best Practices for Soldering
- Frequently Asked Questions (FAQ)
- Conclusion
Introduction to Solder Bridging
Solder bridging is a defect that occurs during the soldering process, where excess molten solder inadvertently connects two or more points that should remain electrically isolated. This unintended connection can lead to various issues, ranging from minor glitches to complete device failure.
Understanding the basics of soldering is crucial to comprehend how solder bridging occurs. Soldering is the process of joining two or more metal surfaces by melting a filler metal (solder) between them. The solder, typically an alloy of tin and lead or lead-free alternatives, has a lower melting point than the metals being joined. When the solder cools and solidifies, it creates a strong electrical and mechanical bond.
However, when too much solder is applied or the soldering technique is improper, the molten solder can flow beyond the intended area and create a bridge between adjacent pins, pads, or traces. This unwanted connection can disrupt the designed electrical pathways, causing short circuits or altering the intended functionality of the electronic device.
Solder bridging is a concern in both through-hole technology (THT) and surface mount technology (SMT) assembly processes. In THT, the electronic components have long leads that are inserted through holes in the PCB and soldered on the opposite side. SMT, on the other hand, involves placing components directly onto pads on the PCB surface and soldering them in place. Due to the smaller size and tighter spacing of SMT components, solder bridging is more likely to occur in this assembly method.
Causes of Solder Bridging
Several factors can contribute to the occurrence of solder bridging during the electronic assembly process. Understanding these causes is essential for preventing and minimizing the risk of solder bridges. Some common causes include:
-
Excessive solder application: Applying too much solder is one of the primary reasons for solder bridging. When an excess amount of solder is used, it can easily flow and spread beyond the intended area, creating bridges between adjacent pins or pads.
-
Incorrect soldering temperature: Using a soldering iron with an inappropriate temperature can lead to solder bridging. If the temperature is too low, the solder may not melt completely, resulting in poor wetting and an increased risk of bridging. Conversely, if the temperature is too high, the solder can become excessively fluid and flow uncontrollably, causing bridges.
-
Improper soldering technique: Poor soldering techniques, such as holding the soldering iron on the joint for too long, applying insufficient heat, or using the wrong tip size, can contribute to solder bridging. Improper technique can cause the solder to flow erratically or result in an uneven distribution of solder.
-
Inadequate flux application: Flux is a chemical compound that helps remove oxides from metal surfaces and promotes solder wetting. Insufficient flux application or using low-quality flux can lead to poor solder flow and an increased risk of bridging.
-
Component placement issues: Misaligned or improperly placed components can create opportunities for solder bridging. If the component leads or pads are too close together or not properly aligned, the solder can easily bridge the gap between them.
-
PCB design factors: The PCB design itself can influence the likelihood of solder bridging. Factors such as pad size, spacing between pads, and the presence of solder mask can affect the soldering process. Smaller pad sizes and tighter spacing increase the risk of bridging, while a well-designed solder mask can help prevent accidental bridges.
-
Contamination: Contaminants on the PCB surface or component leads, such as dirt, grease, or oxidation, can hinder proper solder wetting and lead to bridging. Ensuring cleanliness of the surfaces before soldering is crucial for preventing contamination-related bridges.
By understanding these causes, electronics enthusiasts and professionals can take necessary precautions and adopt best practices to minimize the occurrence of solder bridging during the assembly process.
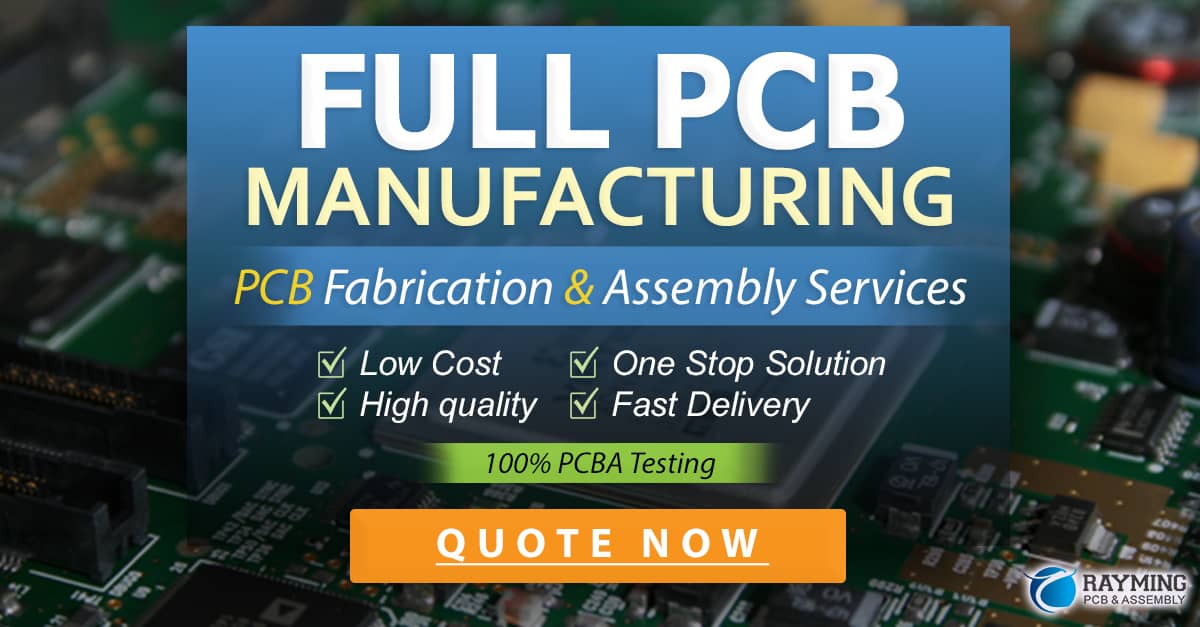
Prevention Techniques
Preventing solder bridging is crucial for ensuring the reliability and functionality of electronic assemblies. By implementing the following techniques, the risk of solder bridges can be significantly reduced:
-
Proper solder amount: One of the most effective ways to prevent solder bridging is to apply the correct amount of solder. Using just enough solder to create a strong and reliable joint is key. Excess solder should be avoided, as it increases the chances of bridging. A general rule of thumb is to apply solder that is approximately 1.5 to 2 times the diameter of the component lead or pad.
-
Temperature control: Maintaining the appropriate soldering temperature is essential for preventing solder bridging. The ideal temperature range depends on the type of solder being used. For leaded solder, a temperature between 315°C and 345°C (600°F to 650°F) is typically recommended, while lead-free solder may require slightly higher temperatures. Using a temperature-controlled soldering station allows for precise temperature adjustment and helps prevent overheating or underheating the solder.
-
Proper soldering technique: Employing the correct soldering technique is crucial for avoiding solder bridging. The soldering iron should be applied to both the component lead and the pad simultaneously, allowing the solder to melt and flow evenly. The iron should be held at a 45-degree angle to the joint, and the solder should be applied to the opposite side of the lead from the iron. Once a sufficient amount of solder has been applied, the iron should be removed quickly to prevent overheating and excessive solder flow.
-
Adequate flux usage: Flux plays a vital role in promoting proper solder flow and preventing bridging. Applying an appropriate amount of flux to the soldering area helps remove oxides, improves solder wetting, and reduces the surface tension of the molten solder. This allows the solder to flow more evenly and reduces the risk of bridging. However, it is important not to use excessive flux, as it can lead to residue buildup and potential contamination.
-
Accurate component placement: Properly placing and aligning components on the PCB is essential for preventing solder bridging. Ensure that the component leads or pads are correctly positioned and spaced according to the PCB design specifications. Use appropriate tools, such as tweezers or vacuum pickup tools, to handle and place components accurately. Double-check the alignment before soldering to minimize the risk of bridges caused by misplaced components.
-
Solder mask application: Solder mask is a coating applied to the PCB surface that helps prevent solder from flowing beyond the desired areas. It acts as a barrier, confining the solder to the exposed pads and preventing accidental bridging. When designing a PCB, consider incorporating a well-defined solder mask layer to protect against solder bridges. Ensure that the solder mask apertures are appropriately sized and positioned to allow for proper soldering while minimizing the risk of bridging.
-
Cleanliness and contamination control: Maintaining a clean soldering environment and ensuring the cleanliness of the PCB and components is crucial for preventing solder bridging. Contaminants such as dirt, grease, or oxidation can hinder proper solder flow and increase the risk of bridging. Before soldering, clean the PCB and component surfaces using appropriate solvents or cleaning agents. Avoid touching the surfaces with bare hands, as skin oils can introduce contamination. Use clean soldering tools and maintain a tidy workspace to minimize the chances of contamination-related bridging.
-
Inspection and quality control: Implementing a thorough inspection and quality control process can help identify and correct solder bridging issues before they cause further problems. After soldering, visually inspect the solder joints using magnification tools to check for any signs of bridging. Automated optical inspection (AOI) systems can also be used for more efficient and consistent detection of solder bridges in large-scale production environments. If bridges are found, they should be carefully removed and the affected areas should be resoldered correctly.
By implementing these prevention techniques, the occurrence of solder bridging can be significantly reduced, resulting in more reliable and robust electronic assemblies. It is important to develop good soldering practices, pay attention to detail, and continuously refine one’s skills to minimize the risk of solder bridging in both hobby and professional settings.
Detecting Solder Bridges
Detecting solder bridges is a critical step in ensuring the quality and reliability of electronic assemblies. Identifying and addressing solder bridges early in the manufacturing process can save time, effort, and resources by preventing potential issues from propagating to later stages or even reaching the end-user. Here are some common methods for detecting solder bridges:
-
Visual inspection: The most straightforward method for detecting solder bridges is through visual inspection. This involves carefully examining the soldered joints using the naked eye or magnification tools such as a magnifying glass, loupe, or microscope. Look for any visible connections or filaments of solder bridging adjacent pins, pads, or traces. Pay close attention to areas with tight spacing or where excess solder is more likely to accumulate. Visual inspection is a quick and cost-effective method, but it relies on the skill and attentiveness of the inspector.
-
Automated optical inspection (AOI): AOI is a more advanced and automated method for detecting solder bridges, particularly in high-volume manufacturing environments. AOI systems use high-resolution cameras and advanced image processing algorithms to capture and analyze images of the soldered PCB. These systems compare the captured images to a predefined set of rules or a “golden” reference image to identify any anomalies, including solder bridges. AOI can quickly and accurately detect bridges, even in complex and densely populated PCBs. However, AOI systems can be expensive and may require specialized programming and setup.
-
X-ray inspection: X-ray inspection is a non-destructive testing method that allows for the detection of solder bridges hidden beneath components or within multi-layer PCBs. X-ray systems use high-energy electromagnetic radiation to penetrate through the PCB and generate images of the internal structure. Solder bridges appear as bright spots or lines on the X-ray image, indicating the presence of excess solder. X-ray inspection is particularly useful for detecting bridges in ball grid array (BGA) packages or other components with hidden solder joints. However, X-ray equipment is costly and requires trained operators to interpret the images accurately.
-
Electrical testing: Electrical testing involves using various test methods to verify the electrical continuity and isolation of the soldered connections. Some common electrical testing techniques for detecting solder bridges include:
a. Continuity testing: Continuity testing checks for the presence of an electrical path between two points that should be isolated. By using a multimeter or a dedicated continuity tester, you can quickly identify any unintended connections caused by solder bridges. Place the test probes on the suspected bridged points and check for continuity. If the tester indicates continuity where it shouldn’t exist, a solder bridge is likely present.
b. Resistance measurement: Measuring the resistance between two points can help identify solder bridges. If a solder bridge is present, the resistance between the bridged points will be significantly lower than expected. Use a multimeter to measure the resistance and compare it to the expected value based on the circuit design. A lower resistance reading suggests the presence of a solder bridge.
c. In-circuit testing (ICT): ICT is an automated testing method that verifies the functionality and connectivity of individual components on a PCB. ICT systems use a bed-of-nails fixture to make electrical contact with specific test points on the PCB. The system then performs a series of electrical tests, including continuity and isolation tests, to detect any solder bridges or other manufacturing defects. ICT is highly accurate and efficient but requires specialized equipment and test fixture development.
- Functional testing: Functional testing involves powering up the assembled PCB and testing its overall functionality. While functional testing may not directly target solder bridges, it can help identify any anomalous behavior or malfunctions caused by bridges. If the device fails to operate as expected or exhibits unusual behavior, it may indicate the presence of a solder bridge affecting the circuit’s functionality. Functional testing is typically performed after other detection methods to ensure the overall quality and performance of the assembled PCB.
Detecting solder bridges requires a combination of visual inspection, automated inspection systems, electrical testing, and functional testing techniques. The choice of detection method depends on factors such as the complexity of the PCB, the production volume, available resources, and the required level of accuracy. Implementing multiple detection methods helps catch solder bridges at different stages of the manufacturing process, reducing the risk of defective products reaching the end-user.
Repairing Solder Bridges
Once a solder bridge has been detected, it is crucial to repair it promptly to ensure the proper functioning of the electronic assembly. Repairing solder bridges requires a careful and methodical approach to avoid causing further damage to the PCB or components. Here are some techniques and considerations for repairing solder bridges:
- Desoldering: Desoldering is the process of removing the excess solder that is causing the bridge. There are several methods for desoldering, depending on the tools available and the specific situation:
a. Solder wick: Solder wick, also known as desoldering braid, is a copper braid coated with flux. To use solder wick, place it over the solder bridge and apply heat using a soldering iron. The molten solder will be drawn into the wick through capillary action, removing the excess solder and breaking the bridge. Repeat the process until the bridge is completely removed. Solder wick is effective for removing small to medium-sized bridges.
b. Desoldering pump: A desoldering pump, also called a solder sucker, is a manual tool that uses suction to remove molten solder. To use a desoldering pump, first heat the solder bridge with a soldering iron to melt the solder. Then, quickly place the tip of the desoldering pump near the molten solder and activate the suction. The pump will draw the molten solder into its chamber, removing the bridge. Desoldering pumps are useful for removing larger amounts of solder.
c. Desoldering station: A desoldering station is an advanced tool that combines a soldering iron with a vacuum pump. It allows for precise and controlled removal of solder bridges. The desoldering station heats the solder bridge while simultaneously applying suction to remove the molten solder. Desoldering stations are preferred for professional use and are highly effective for removing bridges on small and delicate components.
-
Cleaning: After desoldering, it is important to clean the affected area to remove any residual solder or flux. Use a solvent-soaked swab or a cleaning brush to gently remove any remaining debris. Isopropyl alcohol is commonly used as a cleaning solvent. Ensure that the area is completely clean and free from any contaminants before proceeding with further repairs or resoldering.
-
Resoldering: Once the solder bridge has been removed and the area cleaned, the affected components may need to be resoldered. Apply a small amount of fresh solder to the pads or leads, ensuring a proper and strong connection. Use the appropriate soldering technique, as described in the prevention techniques section, to avoid creating new bridges during the repair process. If necessary, replace any damaged components before resoldering.
-
Inspection: After repairing the solder bridge, it is crucial to inspect the repaired area to ensure that the bridge has been completely removed and that the solder joints are properly formed. Use visual inspection techniques, such as magnification or microscopy, to closely examine the repaired area. Check for any remaining solder filaments, shorts, or insufficient solder coverage. If any issues are found, repeat the repair process until the solder joint meets the required quality standards.
-
Functional testing: Once the visual inspection is satisfactory, perform functional testing to verify that the repaired assembly operates as intended. Power up the device and test its functionality, paying close attention to any areas related to the repaired solder bridge. Ensure that the device performs as expected and that there are no lingering
0 Comments