Solder Definition
Solder is a low-melting-point metal alloy used to join together metal surfaces, primarily in the electronics industry. It is a crucial material in the assembly and repair of electronic devices, as it provides electrical, thermal, and mechanical connections between components. Solder is typically composed of tin and lead, although lead-free alternatives are increasingly common due to environmental and health concerns.
Composition of Solder
Traditionally, solder was made from a combination of tin and lead. The most common ratio was 60% tin and 40% lead (Sn60Pb40), known as “60/40 solder.” However, due to the toxicity of lead and its harmful effects on human health and the environment, lead-free solder alloys have been developed and are now widely used in the electronics industry.
Lead-free solder alloys typically consist of tin, silver, and copper (Sn-Ag-Cu or SAC). Common lead-free solder compositions include:
- SAC305 (96.5% tin, 3% silver, 0.5% copper)
- SAC387 (95.5% tin, 3.8% silver, 0.7% copper)
- SN100C (99.3% tin, 0.7% copper, with a small amount of nickel and germanium)
Properties of Solder
Solder possesses several properties that make it suitable for use in electronic applications:
- Low melting point: Solder melts at a relatively low temperature, allowing for easy application without damaging the components being joined.
- Electrical conductivity: Solder provides an electrically conductive path between components, ensuring proper circuit function.
- Thermal conductivity: Solder helps to dissipate heat generated by electronic components, preventing overheating and device failure.
- Mechanical strength: Solder forms a strong mechanical bond between components, providing structural integrity to the assembly.
The table below compares the properties of common lead-based and lead-free solder alloys:
Solder Alloy | Composition (%) | Melting Point (°C) | Electrical Conductivity (% IACS) | Thermal Conductivity (W/mK) |
---|---|---|---|---|
Sn60Pb40 | 60Sn-40Pb | 183-190 | 11.9 | 50 |
SAC305 | 96.5Sn-3Ag-0.5Cu | 217-220 | 13.0 | 55 |
SAC387 | 95.5Sn-3.8Ag-0.7Cu | 217-220 | 13.0 | 55 |
SN100C | 99.3Sn-0.7Cu-Ni-Ge | 227-229 | 13.5 | 60 |
*IACS: International Annealed Copper Standard
Solder Forms and Application Methods
Solder is available in various forms to accommodate different application methods and manufacturing processes. Some common forms include:
- Wire solder: A thin, flexible wire composed of solder alloy, often with a rosin core that serves as a flux to clean and prepare the metal surfaces for bonding. Wire solder is commonly used for hand soldering and rework.
- Solder paste: A mixture of tiny solder particles suspended in a flux paste. Solder paste is used in surface mount technology (SMT) and is applied to printed circuit boards (PCBs) using stencils or syringe dispensing before component placement.
- Solder preforms: Precisely shaped pieces of solder, such as rings, discs, or washers, used in specific applications where a controlled amount of solder is required.
- Solder balls: Tiny spheres of solder used in ball grid array (BGA) packages and flip-chip assembly.
Solder can be applied using various methods, depending on the form of solder and the manufacturing process:
- Hand soldering: A soldering iron is used to melt wire solder and apply it to the joint between components. This method is often used for small-scale assembly, rework, and repair.
- Wave soldering: A automated process where a PCB is passed over a molten solder wave, allowing the solder to coat and join the components to the board. Wave soldering is used for through-hole components.
- Reflow soldering: Used in SMT assembly, where solder paste is applied to the PCB, components are placed, and the entire assembly is heated in a reflow oven. The solder melts and forms joints between the components and the PCB pads.
- Selective soldering: A targeted soldering process that applies solder to specific areas of a PCB, often used for components that cannot withstand the high temperatures of reflow or wave soldering.
Soldering Process and Best Practices
To achieve reliable solder joints, it is essential to follow proper soldering techniques and best practices. The basic steps in the soldering process include:
- Surface preparation: Clean and prepare the surfaces to be joined, ensuring they are free from dirt, grease, and oxidation. This can be done using solvents, abrasives, or fluxes.
- Solder application: Apply the appropriate form of solder to the joint, using the chosen application method (e.g., hand soldering, reflow soldering).
- Heating: Apply heat to the joint using a soldering iron, hot air gun, or reflow oven, depending on the soldering method. The heat should be sufficient to melt the solder and allow it to flow between the surfaces.
- Cooling: Allow the solder joint to cool and solidify. Avoid disturbing the joint during cooling to prevent weakening or damage.
Best practices for soldering include:
- Use the appropriate solder alloy and form for the application
- Ensure proper surface preparation and cleanliness
- Apply the correct amount of solder
- Control the heating process to avoid overheating or underheating the joint
- Use appropriate tools and equipment, such as temperature-controlled soldering irons and ESD-safe workstations
- Inspect the solder joint for quality and reliability
Environmental and Health Considerations
The use of lead in solder has been a concern due to its toxicity and harmful effects on human health and the environment. Lead exposure can cause neurological, reproductive, and developmental problems, as well as damage to the kidneys and other organs.
To address these concerns, the electronics industry has shifted towards lead-free solder alloys, driven by regulations such as the Restriction of Hazardous Substances (RoHS) directive in the European Union. RoHS restricts the use of lead and other hazardous substances in electronic and electrical equipment.
However, lead-free solder alloys present their own challenges, such as higher melting points, different wetting properties, and potential reliability issues. Ongoing research and development efforts aim to improve lead-free solder alloys and address these challenges.
When working with solder, it is essential to take appropriate safety precautions, such as:
- Using ventilation or fume extraction systems to minimize exposure to solder fumes
- Wearing personal protective equipment (PPE) such as gloves and safety glasses
- Properly disposing of solder waste and following local regulations for hazardous materials
Frequently Asked Questions (FAQ)
-
What is solder made of?
Solder is typically made from a combination of metals, such as tin, lead, silver, and copper. Lead-based solders commonly use a 60/40 tin-lead ratio, while lead-free solders often consist of tin, silver, and copper (SAC alloys). -
What is the purpose of solder in electronics?
Solder serves three main purposes in electronics: it provides electrical conductivity between components, allows for heat dissipation, and forms a mechanical bond to hold components in place. -
What is the difference between lead-based and lead-free solder?
Lead-based solder contains a significant amount of lead, typically around 40%, while lead-free solder uses alternative alloys without lead, such as tin-silver-copper (SAC). Lead-free solders have been developed to address the health and environmental concerns associated with lead. -
What is the melting point of solder?
The melting point of solder varies depending on the alloy composition. Lead-based solders typically melt between 183°C and 190°C, while lead-free solders have slightly higher melting points, usually between 217°C and 227°C. -
How can I choose the right solder for my application?
When choosing solder, consider factors such as the required melting point, electrical and thermal conductivity, mechanical strength, and compatibility with the components and PCB materials. Consult solder manufacturers’ specifications and industry standards to select the most appropriate solder alloy for your specific application.
Conclusion
Solder is an essential material in the electronics industry, providing electrical, thermal, and mechanical connections between components. Its low melting point, conductivity, and mechanical strength make it suitable for various assembly and repair applications. The transition from lead-based to lead-free solder alloys has been driven by environmental and health concerns, presenting new challenges and opportunities for the industry.
Understanding the properties, forms, and application methods of solder is crucial for anyone working in electronics manufacturing or repair. By following best practices and taking appropriate safety precautions, reliable and high-quality solder joints can be achieved, ensuring the proper function and longevity of electronic devices.
As the electronics industry continues to evolve, ongoing research and development efforts will focus on improving solder alloys, addressing the challenges of lead-free soldering, and finding innovative solutions for the assembly and interconnection of advanced electronic components.
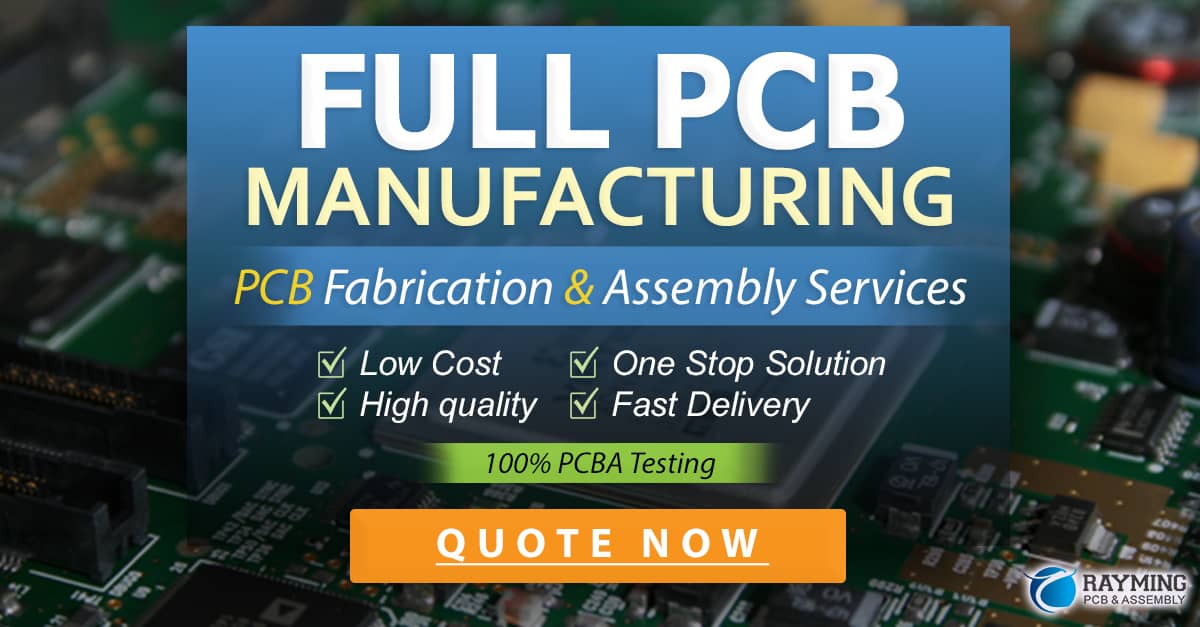
0 Comments