How Reflow Soldering Works
The reflow soldering process can be broken down into several key steps:
-
Solder Paste Application: Solder paste, a mixture of powdered solder and flux, is precisely applied to the PCB’s contact pads using a stencil or screen printing process. The stencil ensures the proper amount of solder is deposited in the correct locations.
-
Component Placement: Surface mount components are placed onto the solder paste deposits on the PCB. This is typically done by automated pick-and-place machines for speed and accuracy. Through-hole components requiring wave soldering may also be inserted.
-
Reflow Heating: The populated PCB is passed through a reflow oven on a conveyor belt. The oven precisely heats the board in stages:
- Preheat: Gradually raises PCB temperature to activate flux and remove solvents
- Thermal Soak: Holds at stable temperature to evenly heat PCB and components
- Reflow: Quickly spikes to peak temperature, melting solder to form connections
-
Cooling: Gradually cools PCB to solidify joints without thermal stress
-
Inspection: The reflowed assembly is visually inspected for defects like poor wetting, bridging, tombstoning. Electrical tests and x-ray inspection may also be used for hidden joints and voids.
Reflow Soldering Temperature Profile
Carefully controlling the reflow oven temperature profile is critical to forming reliable solder joints without damaging components. The exact profile depends on the solder paste formulation and component heat tolerances, but a typical lead-free profile hits these key points:
Stage | Temperature (°C) | Time (seconds) |
---|---|---|
Preheat | 150-180 | 60-120 |
Soak | 180-200 | 60-120 |
Reflow | 235-250 peak | 30-90 above liquids |
Cooling | < 6°C/sec | Until < 180 °C |
It’s important the peak temperature exceeds the solder’s melting point for long enough to fully wet all joint surfaces, but not so long it causes component or PCB damage. Modern reflow ovens tightly control conveyor speed and multi-zone heating to achieve the target profile across the entire PCB surface.
Solder Paste Selection
Solder paste selection is another key consideration in the reflow soldering process. The main aspects to consider are:
Alloy
The most common lead-free solder alloys for reflow are tin-silver-copper (SAC) formulations like SAC305 (96.5% tin, 3% silver, 0.5% copper). SAC alloys have higher melting points than traditional tin-lead solder, typically reflowing around 240°C. Some low-temperature lead-free alloys are available to reduce thermal stress.
Powder Size
Solder powder particle size affects paste printing and reflow behavior. Smaller powders deposit finer paste deposits for smaller pitches, but may have poorer wetting. Type 3 (25-45 μm) and Type 4 (20-38 μm) are common sizes.
Flux
The flux vehicle suspends the solder powder and cleans surfaces during reflow. Flux type (rosin, no-clean, water-soluble) is selected based on PCB materials, cleaning processes, and reliability requirements. Insufficient flux activity can cause poor wetting, while too much may leave corrosive residues.
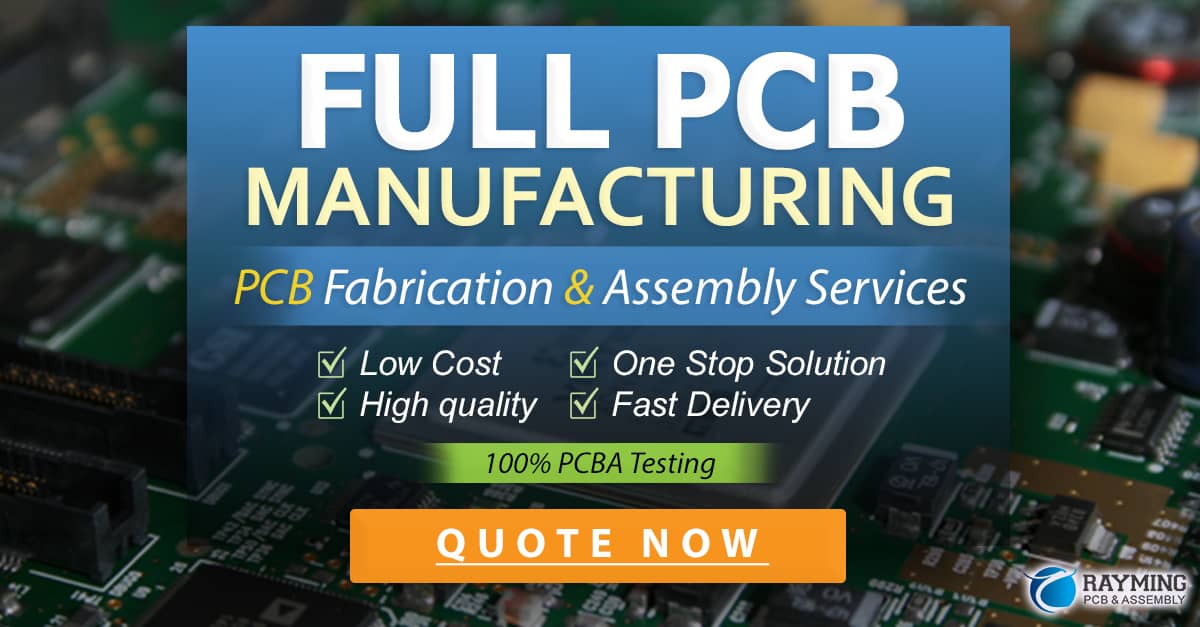
Advantages of Reflow Soldering
Reflow soldering offers several key advantages for electronics manufacturing:
-
Automation: The process is highly automated, using stencil printers, pick-and-place machines, and conveyor ovens for high-volume production with minimal manual labor.
-
Consistency: Precise control over solder paste deposition and heating profiles ensures consistent, repeatable joint quality across boards and production runs.
-
Flexibility: Reflow handles a wide range PCB designs and component types, from simple surface-mount boards to complex mixed assemblies with fine-pitch BGAs and chip-scale packages.
-
Reliability: With proper process control, reflow soldering forms strong, reliable joints with good wetting, minimal voids, and low thermal stress.
Challenges of Reflow Soldering
However, reflow soldering also presents some challenges:
-
Process Complexity: Reflow involves many interdependent variables (paste rheology, oven recipes, component placement tolerances) that must be carefully optimized and controlled for good results.
-
Thermal Limitations: The high temperatures needed for lead-free reflow can damage sensitive components or warp PCBs with high layer counts or large aspect ratios. Careful profile tuning and PCB design are needed.
-
Defect Potential: Issues like poor wetting, solder bridging, tombstoning, and head-in-pillow joints can occur with improper process settings, requiring rework. Identifying defects often requires skilled inspection.
-
Cost: Reflow ovens, printing and placement machines, and solder paste represent significant capital investments for high-volume production lines.
Frequently Asked Questions
What’s the difference between reflow and wave soldering?
Reflow soldering is used for surface-mount components, applying a controlled heat profile to paste deposits. Wave soldering is used for through-hole components, passing the board over a molten solder wave. Reflow offers more control and flexibility, while wave is simpler for high through-hole content.
Can reflow soldering be done without a stencil?
Solder paste can be dispensed or manually applied without a stencil, but stencil printing is preferred for consistency and fine pitch components. Stencils ensure even paste deposits of the proper volume at each pad location.
How hot does a reflow oven get?
Reflow ovens typically peak around 240-250°C for lead-free solder alloys, held for 30-90 seconds. The exact profile depends on the paste composition and component heat tolerance, ramping up and cooling gradually to minimize thermal shock.
What is the best solder paste for reflow?
The best solder paste depends on the application, considering alloy melting point, powder size for pitches, flux activity and cleaning. Tin-silver-copper (SAC) alloys are common for lead-free reflow. Type 3 or 4 powder works for most pitches. No-clean flux is popular for mild activation.
How do you inspect reflow solder joints?
Reflow joints are inspected visually for wetting, bridging, voids and component alignment. Automated optical inspection (AOI) compares to reference images to flag defects. X-ray inspection reveals hidden ball-grid array (BGA) and chip-scale package (CSP) joints. Electrical tests verify connectivity and signal integrity.
0 Comments