What Causes PCB tombstoning?
Several factors can contribute to the occurrence of PCB tombstoning:
Uneven Heating
One of the primary causes of tombstoning is uneven heating during the reflow soldering process. When one end of a chip component heats up faster than the other, it can cause the component to lift off the pad on the cooler side. This uneven heating can be due to:
- Poor oven temperature profiling
- Inadequate preheating
- Improper placement of components on the PCB
- Variations in component thermal mass
Pad Design and Solderability
The design of the PCB pads and their solderability can also play a role in tombstoning:
- Unequal pad sizes: If the pads on either end of a component are not the same size, the molten solder may pull the component towards the larger pad, causing tombstoning.
- Poor pad solderability: Contamination, oxidation, or improper surface finish on the pads can lead to uneven solder wetting and tombstoning.
Component Selection and Placement
The choice of components and their placement on the PCB can influence the likelihood of tombstoning:
- Component size: Smaller chip components, such as 0201 and 01005 sizes, are more prone to tombstoning due to their low mass and high surface tension of molten solder.
- Component orientation: Components placed perpendicular to the direction of PCB travel in the reflow oven are more susceptible to tombstoning due to uneven heating.
Solder Paste Properties
The characteristics of the solder paste used in the assembly process can also affect tombstoning:
- Solder paste composition: The alloy composition and particle size of the solder paste can influence its melting behavior and surface tension, which may contribute to tombstoning.
- Solder paste volume: Insufficient or excessive solder paste can lead to uneven solder joint formation and tombstoning.
Preventing PCB Tombstoning
To minimize the occurrence of PCB tombstoning, several preventive measures can be implemented:
Optimizing Reflow Profile
Ensuring a well-designed and optimized reflow profile is essential for preventing tombstoning:
- Proper preheating: Adequate preheating helps to minimize temperature gradients across the PCB and components, reducing the risk of uneven heating and tombstoning.
- Temperature profiling: Regularly monitoring and adjusting the reflow oven temperature profile to maintain consistent heating across the PCB.
PCB Design Considerations
Incorporating tombstone-resistant features in the PCB design can help prevent the defect:
- Equal pad sizes: Designing pads with equal sizes on both ends of a component can promote even solder wetting and reduce the chance of tombstoning.
- Solder mask design: Proper solder mask design, such as using a solder mask defined (SMD) pad layout, can help control solder wetting and minimize tombstoning.
Component Selection and Placement
Careful component selection and placement strategies can reduce the risk of tombstoning:
- Larger component sizes: Using larger chip components, when possible, can help reduce the likelihood of tombstoning due to their higher mass and better stability during reflow.
- Component orientation: Orienting components parallel to the direction of PCB travel in the reflow oven can promote even heating and reduce tombstoning.
Solder Paste Optimization
Optimizing the solder paste properties and application can help prevent tombstoning:
- Solder paste selection: Choosing a solder paste with the appropriate alloy composition and particle size for the specific application can minimize tombstoning risk.
- Solder paste volume control: Ensuring the correct amount of solder paste is deposited on the pads through proper stencil design and printing process control.
Process Control and Monitoring
Implementing strict process control and monitoring measures can help identify and correct tombstoning issues:
- Inspection and testing: Regular visual inspection and electrical testing of assembled PCBs to detect tombstoning defects and track process performance.
- Statistical process control (SPC): Using SPC techniques to monitor process parameters, such as reflow temperatures and solder paste volumes, can help identify trends and prevent tombstoning.
Correcting PCB Tombstoning
If tombstoning defects are detected on an assembled PCB, several methods can be used to correct the issue:
Manual Rework
For small-scale production or prototypes, manual rework can be an option:
- Reheating the affected component using a focused heat source, such as a hot air pencil or soldering iron, to reflow the solder and allow the component to settle back onto the pads.
- Applying additional solder or flux to the lifted end of the component to promote better solder wetting and adhesion.
Automated Rework
In high-volume production, automated rework systems can be used to correct tombstoning defects:
- Rework stations equipped with vision systems and precise heating controls can accurately locate and reflow the affected components.
- Automated solder paste dispensing and component placement can ensure consistent and reliable rework results.
Selective Soldering
Selective soldering techniques can be employed to correct tombstoning defects:
- Using a selective soldering machine to apply focused heat and solder to the lifted end of the component, allowing it to settle back onto the pad.
- Selective soldering can be an efficient solution for reworking multiple tombstoned components on a single PCB.
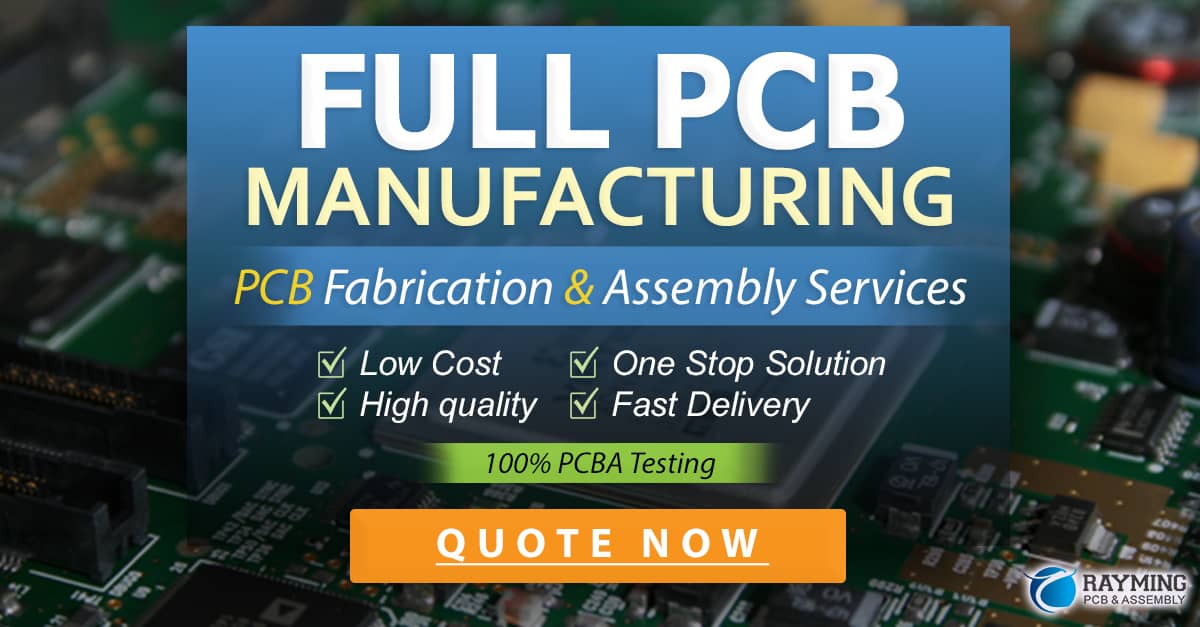
FAQs
-
Q: What is the difference between tombstoning and drawbridging?
A: Tombstoning occurs when one end of a chip component lifts off the PCB pad, while drawbridging happens when both ends of the component lift off the pads, forming a “bridge” shape. -
Q: Can tombstoning be detected by automated optical inspection (AOI)?
A: Yes, most modern AOI systems are capable of detecting tombstoning defects using advanced algorithms and 3D imaging techniques. -
Q: How does the use of nitrogen in the reflow oven affect tombstoning?
A: Using nitrogen in the reflow oven can help reduce tombstoning by minimizing oxidation on the PCB pads and component terminations, promoting better solder wetting and adhesion. -
Q: Can tombstoning occur with through-hole components?
A: Tombstoning is primarily associated with surface mount components, as through-hole components are inserted into drilled holes in the PCB and are less susceptible to lifting off the pads during soldering. -
Q: What is the impact of tombstoning on the reliability of the assembled PCB?
A: Tombstoning can lead to electrical open circuits, reduced mechanical strength, and increased stress on the affected solder joints, potentially compromising the long-term reliability of the assembled PCB.
In conclusion, PCB tombstoning is a common SMT defect that can be caused by various factors, including uneven heating, pad design, component selection, and solder paste properties. By implementing preventive measures, such as optimizing the reflow profile, considering PCB design factors, selecting appropriate components, and controlling the solder paste application, the risk of tombstoning can be significantly reduced. If tombstoning defects are detected, manual rework, automated rework systems, or selective soldering techniques can be employed to correct the issue and ensure the quality and reliability of the final assembled PCB.
Cause | Prevention |
---|---|
Uneven heating | – Proper preheating – Temperature profiling |
Pad design and solderability | – Equal pad sizes – Solder mask design |
Component selection and placement | – Larger component sizes – Component orientation |
Solder paste properties | – Solder paste selection – Solder paste volume control |
Correction Method | Applicability |
---|---|
Manual rework | Small-scale production or prototypes |
Automated rework | High-volume production |
Selective soldering | Efficient solution for reworking multiple tombstoned components |
By understanding the causes, prevention techniques, and correction methods for PCB tombstoning, manufacturers can ensure the production of high-quality and reliable electronic assemblies, ultimately leading to improved product performance and customer satisfaction.
0 Comments