The Importance of PCB Standards
PCB standards play a crucial role in the electronics industry by:
-
Ensuring consistency and reliability: Standards help maintain a consistent level of quality across different PCB manufacturers, ensuring that boards from various sources are compatible and reliable.
-
Facilitating communication: By adhering to common standards, designers, manufacturers, and customers can communicate effectively, reducing the likelihood of errors and misunderstandings.
-
Promoting safety: PCB standards include guidelines for safety, such as proper isolation, creepage, and clearance distances, which help prevent electrical hazards and ensure the safe operation of electronic devices.
-
Enabling interoperability: Standards ensure that PCBs from different manufacturers can work together seamlessly, making it easier to integrate components and systems from various sources.
-
Reducing costs: By following established standards, manufacturers can minimize errors, reduce rework, and improve efficiency, ultimately leading to cost savings.
Major PCB Standards Organizations
Several organizations develop and maintain PCB standards. The most prominent ones include:
IPC (Association Connecting Electronics Industries)
IPC is a global trade association that focuses on the electronics manufacturing industry. It develops and maintains a wide range of standards for PCB design, fabrication, assembly, and testing. Some of the most important IPC standards include:
- IPC-2221: Generic Standard on Printed Board Design
- IPC-6012: Qualification and Performance Specification for Rigid Printed Boards
- IPC-A-600: Acceptability of Printed Boards
- IPC-A-610: Acceptability of Electronic Assemblies
UL (Underwriters Laboratories)
UL is a global safety certification company that develops standards and testing protocols for various products, including PCBs. UL standards focus on safety aspects, such as flammability, thermal management, and electrical insulation. Some relevant UL standards for PCBs include:
- UL 94: Standard for Safety of Flammability of Plastic Materials for Parts in Devices and Appliances
- UL 746E: Standard for Polymeric Materials – Industrial Laminates, Filament Wound Tubing, Vulcanized Fibre, and Materials Used in Printed Wiring Boards
- UL 796: Standard for Printed Wiring Boards
JEDEC (Joint Electron Device Engineering Council)
JEDEC is an independent semiconductor engineering trade organization and standardization body. While JEDEC primarily focuses on semiconductor standards, some of its standards also apply to PCBs, particularly in the context of component packaging and mounting. Examples include:
- JESD22: Reliability Test Methods for Packaged Devices
- JESD625: Requirements for Handling Electrostatic-Discharge-Sensitive (ESDS) Devices
Key PCB Standards
Now let’s take a closer look at some of the most important PCB standards and their implications for designers and manufacturers.
IPC-2221: Generic Standard on Printed Board Design
IPC-2221 is a comprehensive standard that provides guidelines for the design of PCBs. It covers various aspects of PCB design, including:
- Board layout and routing
- Electrical clearances and creepage distances
- Hole sizes and pad dimensions
- Solder mask and silkscreen requirements
- Tolerances and dimensioning
This standard helps designers create PCBs that are manufacturable, reliable, and compliant with industry requirements. By following IPC-2221 guidelines, designers can minimize design-related issues and ensure that their boards can be efficiently manufactured and assembled.
IPC-6012: Qualification and Performance Specification for Rigid Printed Boards
IPC-6012 is a performance specification standard that defines the requirements for the manufacture of rigid PCBs. It covers various aspects of PCB fabrication, including:
- Material selection and quality
- Conductor and dielectric thickness
- Hole and via requirements
- Surface finish and plating
- Dimensional tolerances
- Electrical and mechanical testing
This standard helps ensure that PCBs meet the necessary quality and performance requirements for their intended applications. Manufacturers can use IPC-6012 to establish process controls and testing procedures that guarantee the consistency and reliability of their products.
IPC-A-600: Acceptability of Printed Boards
IPC-A-600 is a visual inspection standard that provides criteria for determining the acceptability of PCBs. It defines various defect categories and their acceptable limits, such as:
- Conductor and dielectric thickness
- Hole and via quality
- Solder mask and silkscreen registration
- Surface finish and plating defects
- Laminate and substrate defects
This standard helps manufacturers and customers establish a common understanding of PCB quality and acceptability. By referring to IPC-A-600, inspectors can objectively evaluate PCBs and determine whether they meet the required quality standards.
IPC-A-610: Acceptability of Electronic Assemblies
IPC-A-610 is a visual inspection standard that focuses on the acceptability of electronic assemblies, including PCBs populated with components. It provides criteria for evaluating the quality of solder joints, component placement, and mechanical assembly. Some key aspects covered by IPC-A-610 include:
- Solder joint appearance and quality
- Component alignment and orientation
- Lead and termination requirements
- Mechanical assembly and fastening
- Cleanliness and contamination
This standard ensures that electronic assemblies meet the necessary quality and reliability requirements for their intended applications. Manufacturers and inspectors can use IPC-A-610 to assess the quality of assembled PCBs and identify any issues that may impact their performance or reliability.
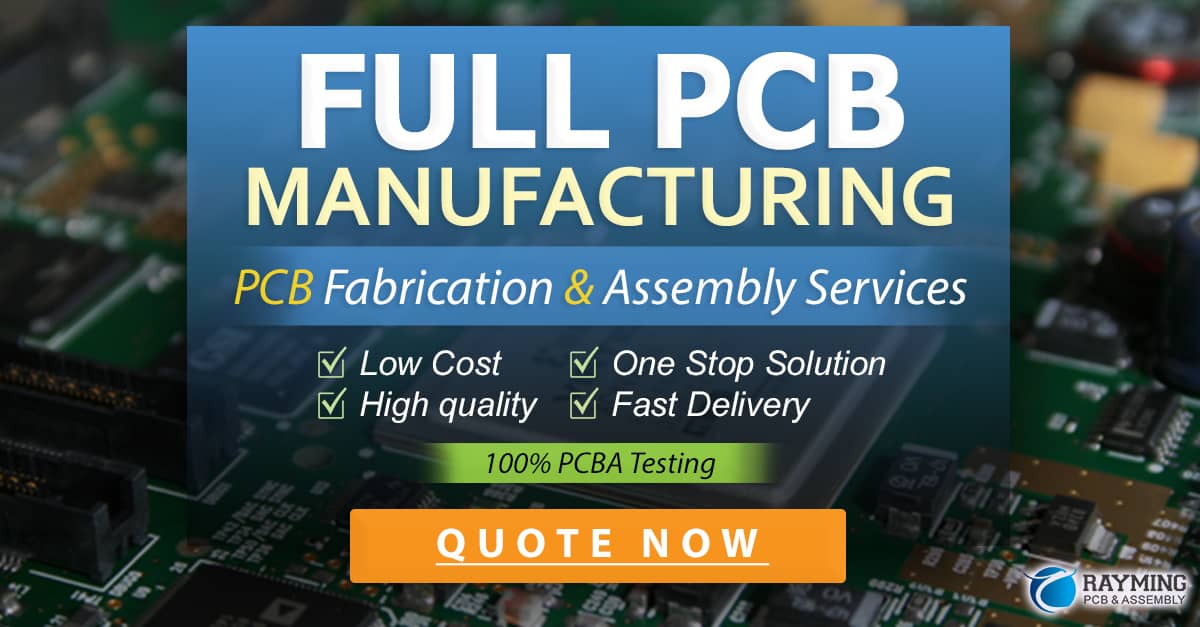
Choosing the Right PCB Class
IPC standards also define different classes of PCBs based on their intended applications and quality requirements. These classes help designers and manufacturers select the appropriate level of quality and performance for their specific needs. The three main PCB classes are:
- Class 1: General Electronic Products
- Suitable for non-critical applications where cosmetic defects are acceptable, and the risk of failure is low.
-
Examples: consumer electronics, toys, and low-end appliances.
-
Class 2: Dedicated Service Electronic Products
- Suitable for products where extended life and reliability are required, and some cosmetic defects are acceptable.
-
Examples: industrial controls, automotive electronics, and medical devices.
-
Class 3: High Reliability Electronic Products
- Suitable for critical applications where failure could result in significant consequences, such as loss of life or substantial economic impact.
- Examples: aerospace, military, and life-support systems.
Designers and manufacturers should carefully consider the intended application and quality requirements when selecting the appropriate PCB class. This ensures that the PCBs meet the necessary performance and reliability standards while minimizing unnecessary costs.
PCB Standards and Environmental Regulations
In addition to quality and performance standards, PCBs must also comply with various environmental regulations. These regulations aim to minimize the environmental impact of electronics manufacturing and ensure the safe disposal of electronic waste. Some key environmental regulations that impact PCBs include:
- RoHS (Restriction of Hazardous Substances): Restricts the use of certain hazardous substances, such as lead, mercury, and cadmium, in electronic products.
- WEEE (Waste Electrical and Electronic Equipment): Requires the proper collection, treatment, and recycling of electronic waste.
- REACH (Registration, Evaluation, Authorization, and Restriction of Chemicals): Regulates the use of chemicals in products, including PCBs, to ensure the protection of human health and the environment.
Designers and manufacturers must ensure that their PCBs comply with these environmental regulations to avoid legal and financial consequences, as well as to minimize their environmental footprint.
Frequently Asked Questions (FAQ)
-
Q: What is the difference between IPC and UL standards for PCBs?
A: IPC standards focus on the design, fabrication, assembly, and testing of PCBs, ensuring their quality, reliability, and consistency. UL standards, on the other hand, primarily focus on safety aspects, such as flammability, thermal management, and electrical insulation. -
Q: Can a PCB be compliant with multiple standards simultaneously?
A: Yes, a PCB can be designed and manufactured to comply with multiple standards simultaneously. For example, a board may adhere to IPC-2221 for design, IPC-6012 for fabrication, and UL 94 for flammability requirements. -
Q: How do I know which PCB class to choose for my application?
A: The choice of PCB class depends on the intended application, the required level of reliability, and the consequences of failure. Class 1 is suitable for non-critical applications, Class 2 for products requiring extended life and reliability, and Class 3 for critical applications where failure could result in significant consequences. -
Q: Are PCB standards mandatory?
A: While not all PCB standards are legally mandatory, complying with relevant standards is often a requirement for products to be accepted in the market. Many customers and industries expect PCBs to meet specific standards to ensure quality, reliability, and safety. -
Q: How can I ensure that my PCB design complies with relevant standards?
A: To ensure compliance with PCB standards, designers should familiarize themselves with the relevant standards and guidelines, such as IPC-2221. They can also use PCB design software that includes built-in design rule checks (DRCs) based on these standards. Consulting with experienced PCB designers and manufacturers can also help ensure compliance.
Conclusion
PCB standards play a crucial role in ensuring the quality, reliability, and consistency of printed circuit boards. By adhering to established standards from organizations like IPC, UL, and JEDEC, designers and manufacturers can create PCBs that meet industry requirements and customer expectations. These standards cover various aspects of PCB design, fabrication, assembly, and testing, as well as safety and environmental considerations.
Understanding and complying with relevant PCB standards is essential for designers, manufacturers, and customers alike. It helps facilitate communication, promote interoperability, and ultimately leads to better-quality products that are safer and more reliable. As the electronics industry continues to evolve, staying up-to-date with the latest PCB standards and best practices will remain crucial for success in this dynamic field.
0 Comments