Why is PCB-IST”>PCB-IST Important?
In today’s rapidly evolving electronics industry, PCBs are at the heart of countless devices and systems, ranging from consumer electronics to aerospace and military applications. As these applications become increasingly complex and demanding, the reliability of PCBs becomes a critical factor in determining the overall performance and longevity of the end product.
PCB-IST plays a crucial role in assessing the board’s ability to maintain its electrical and mechanical integrity under various environmental stresses, such as:
- Temperature fluctuations
- Humidity
- Vibration
- Mechanical shock
- Thermal cycling
By subjecting PCBs to these stresses in a controlled laboratory setting, manufacturers can identify potential failure modes and weaknesses in the interconnect structure. This information is invaluable in optimizing the PCB design, selecting appropriate materials, and refining the manufacturing process to improve the overall reliability of the final product.
Furthermore, PCB-IST helps manufacturers to:
- Reduce warranty claims and field failures
- Minimize product recalls and associated costs
- Enhance customer satisfaction and brand reputation
- Comply with industry standards and regulations
Types of PCB Interconnect Stress Tests
There are several types of stress tests that can be performed on PCBs to evaluate their interconnect reliability. Some of the most common tests include:
1. Thermal Cycling
Thermal cycling tests expose PCBs to alternating high and low-temperature extremes to simulate the effects of temperature fluctuations during the product’s lifecycle. The test typically involves subjecting the PCB to multiple cycles of rapid temperature changes, with dwell times at each extreme to allow for thermal stabilization.
The temperature range and the number of cycles are determined based on the product’s intended application and the expected environmental conditions. For example, a PCB designed for automotive applications may be subjected to a more severe thermal cycling test compared to a PCB intended for consumer electronics.
Thermal Cycling Test Parameters
Parameter | Description |
---|---|
Temperature Range | The minimum and maximum temperatures the PCB will be exposed to during the test, e.g., -40°C to +125°C |
Ramp Rate | The rate at which the temperature changes between the extremes, typically measured in °C/minute |
Dwell Time | The time the PCB is held at each temperature extreme to allow for thermal stabilization |
Number of Cycles | The total number of thermal cycles the PCB will undergo during the test |
2. Mechanical Shock and Vibration
Mechanical shock and vibration tests are designed to evaluate the PCB’s ability to withstand sudden impacts and continuous vibrations. These tests are particularly important for PCBs used in applications prone to mechanical stresses, such as automotive, aerospace, and military systems.
Shock tests typically involve subjecting the PCB to a high-acceleration, short-duration impulse, simulating the effects of sudden impacts or drops. Vibration tests, on the other hand, expose the PCB to continuous low-amplitude, high-frequency mechanical excitation, simulating the effects of prolonged exposure to vibration during operation.
Mechanical Shock Test Parameters
Parameter | Description |
---|---|
Peak Acceleration | The maximum acceleration the PCB will be subjected to during the shock test, typically measured in G’s (multiples of gravitational acceleration) |
Pulse Duration | The time duration of the shock impulse, typically measured in milliseconds |
Number of Shocks | The total number of shock impulses the PCB will undergo during the test |
Vibration Test Parameters
Parameter | Description |
---|---|
Frequency Range | The range of frequencies the PCB will be exposed to during the vibration test, typically measured in Hz |
Acceleration Amplitude | The maximum acceleration the PCB will experience during the vibration test, typically measured in G’s |
Duration | The total time the PCB will be subjected to vibration during the test |
3. Humidity Testing
Humidity testing evaluates the PCB’s ability to resist the effects of moisture and humidity. High humidity levels can lead to various issues, such as corrosion, electrical leakage, and delamination of the PCB’s layers.
Humidity tests typically involve exposing the PCB to a controlled environment with elevated humidity levels for an extended period. The temperature and humidity levels are carefully monitored and maintained throughout the test to ensure consistent and repeatable results.
Humidity Test Parameters
Parameter | Description |
---|---|
Temperature | The temperature at which the humidity test will be conducted, typically measured in °C |
Relative Humidity | The percentage of moisture in the air relative to the maximum amount of moisture the air can hold at the given temperature |
Duration | The total time the PCB will be exposed to the humid environment during the test |
4. Combined Environmental Stress Testing
Combined environmental stress testing involves subjecting the PCB to multiple environmental stresses simultaneously, such as temperature, humidity, and vibration. This type of testing is designed to simulate real-world conditions more accurately and identify potential interactions between different stress factors that may lead to PCB failure.
Combined stress tests are particularly valuable for PCBs used in harsh environments, where they may be exposed to a combination of stresses during their lifecycle. By conducting combined stress tests, manufacturers can gain a more comprehensive understanding of the PCB’s reliability and identify potential weaknesses that may not be apparent when testing for individual stress factors.
Interpreting PCB-IST Results
After conducting PCB interconnect stress tests, it is essential to interpret the results accurately to identify any potential issues and make informed decisions about the PCB’s design and manufacturing process.
Some key factors to consider when interpreting IST results include:
1. Failure Modes
Identify the specific failure modes observed during the stress tests, such as:
- Open circuits
- Short circuits
- Increased resistance
- Delamination
- Cracking or fracturing of interconnects
Understanding the failure modes can help pinpoint the root cause of the issue and guide the necessary corrective actions.
2. Time to Failure
Analyze the time it takes for the PCB to exhibit failures under the applied stresses. This information can help estimate the product’s expected lifespan and determine if it meets the required reliability standards.
3. Failure Rate
Calculate the failure rate of the PCBs tested, typically expressed as a percentage of the total number of samples. A high failure rate may indicate a systemic issue with the PCB design or manufacturing process that needs to be addressed.
4. Statistical Analysis
Conduct statistical analysis on the test results to determine the reliability metrics, such as the mean time to failure (MTTF) or the mean time between failures (MTBF). These metrics can help compare the reliability of different PCB designs or manufacturing processes and make data-driven decisions.
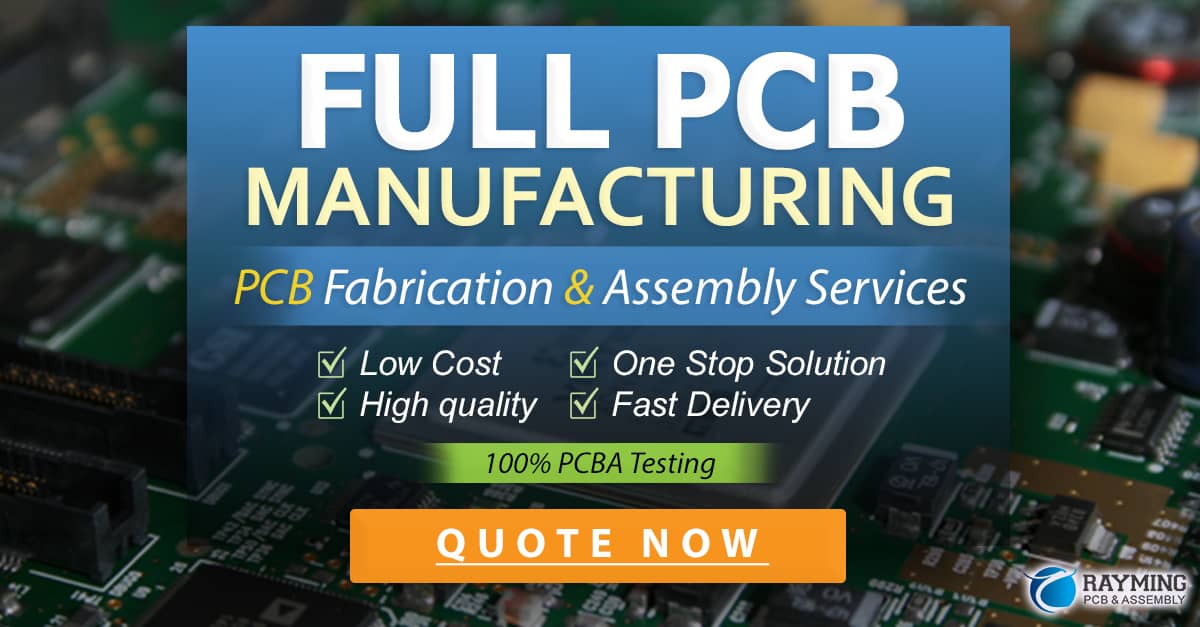
Best Practices for PCB-IST
To ensure the effectiveness and reliability of PCB interconnect stress testing, consider the following best practices:
-
Define clear test objectives and requirements based on the product’s intended application and environmental conditions.
-
Select appropriate test methods and parameters that accurately simulate the expected stresses the PCB will encounter during its lifecycle.
-
Use statistically significant sample sizes to ensure the test results are representative of the entire production run.
-
Maintain proper documentation of the test setup, parameters, and results for future reference and analysis.
-
Regularly calibrate and maintain the test equipment to ensure accurate and consistent results.
-
Collaborate with experienced PCB design and manufacturing partners who can provide guidance and support throughout the testing process.
By following these best practices and leveraging the insights gained from PCB-IST, manufacturers can optimize their PCB designs, improve reliability, and reduce the risk of field failures, ultimately leading to higher customer satisfaction and a stronger market position.
Frequently Asked Questions (FAQ)
1. What is the difference between PCB-IST and other reliability tests?
PCB Interconnect Stress Testing (PCB-IST) specifically focuses on evaluating the reliability and durability of the PCB’s interconnects, such as traces, vias, and solder joints, under various environmental stresses. Other reliability tests may focus on different aspects of the PCB, such as the substrate material, component performance, or overall system functionality.
2. How long does a typical PCB-IST take to complete?
The duration of a PCB-IST can vary significantly depending on the specific test methods, parameters, and sample size. Some tests, such as thermal cycling or humidity exposure, may take several days or even weeks to complete, while others, like mechanical shock tests, can be performed in a matter of hours. The test duration should be carefully planned and aligned with the product development timeline and reliability requirements.
3. Can PCB-IST be performed on prototype or pre-production samples?
Yes, PCB-IST can be performed on prototype or pre-production samples to identify potential issues early in the product development cycle. Testing early samples can help validate the PCB design and manufacturing process, allowing for necessary adjustments and optimizations before mass production begins. However, it is important to ensure that the prototype samples are representative of the final production version to obtain meaningful test results.
4. How do I determine the appropriate sample size for PCB-IST?
The appropriate sample size for PCB-IST depends on several factors, such as the desired confidence level, the expected failure rate, and the acceptable margin of error. Statistical tools and calculations, such as power analysis or the binomial distribution, can be used to determine the minimum sample size required to achieve statistically significant results. In general, larger sample sizes provide more reliable and representative test results but may also increase the cost and duration of the testing process.
5. What should I do if my PCB fails the interconnect stress tests?
If your PCB fails the interconnect stress tests, the first step is to analyze the failure modes and identify the root cause of the issue. This may involve further testing, microscopic inspection, or cross-sectioning of the failed samples. Once the root cause is identified, work with your PCB design and manufacturing teams to implement the necessary corrective actions, such as design modifications, material selection, or process improvements. Repeat the stress tests on the updated samples to verify the effectiveness of the corrective actions and ensure the PCB meets the required reliability standards.
0 Comments