Understanding PCB Etch Factor and Its Significance in PCB Manufacturing
Introduction to PCB Etch Factor
PCB (Printed Circuit Board) etch factor is a crucial concept in the manufacturing process of printed circuit boards. It refers to the ratio between the etched depth and the amount of undercut that occurs during the etching process. The etch factor plays a significant role in determining the accuracy and precision of the final PCB product.
Importance of PCB Etch Factor
The etch factor is essential because it directly impacts the following aspects of PCB manufacturing:
-
Circuit Trace Width: The etch factor affects the width of the copper traces on the PCB. A higher etch factor results in narrower traces, while a lower etch factor leads to wider traces.
-
Impedance Control: Maintaining consistent impedance is crucial for high-speed PCB designs. The etch factor influences the impedance of the traces, and inconsistencies in the etch factor can lead to impedance mismatches and signal integrity issues.
-
Manufacturing Tolerances: The etch factor determines the manufacturing tolerances that can be achieved during PCB fabrication. A well-controlled etch factor allows for tighter tolerances and more precise PCB designs.
Factors Affecting PCB Etch Factor
Several factors can influence the PCB etch factor during the manufacturing process:
-
Etching Solution: The composition and concentration of the etching solution, such as ferric chloride or cupric chloride, can impact the etch factor. The solution’s temperature and agitation also play a role.
-
Copper Thickness: The thickness of the copper layer on the PCB affects the etch factor. Thicker copper layers require longer etching times and can result in a higher etch factor.
-
Etching Time: The duration of the etching process directly influences the etch factor. Longer etching times lead to deeper etching and a higher etch factor.
-
Artwork Design: The artwork design, including the spacing between traces and the overall PCB layout, can impact the etch factor. Proper design considerations help maintain a consistent etch factor across the board.
Calculating PCB Etch Factor
Etch Factor Formula
The PCB etch factor is calculated using the following formula:
Etch Factor = (Etch Depth) / (Undercut)
- Etch Depth: The etch depth refers to the vertical distance that the etching solution penetrates into the copper layer.
- Undercut: Undercut is the lateral distance that the etching solution erodes the copper beneath the photoresist mask.
Measuring Etch Depth and Undercut
To accurately calculate the etch factor, precise measurements of the etch depth and undercut are necessary. These measurements can be obtained using specialized equipment, such as:
-
Profilometer: A profilometer is an instrument that measures the surface profile of the PCB. It can provide precise measurements of the etch depth.
-
Microscope: An optical or scanning electron microscope (SEM) can be used to measure the undercut by examining the cross-section of the etched traces.
Example Calculation
Let’s consider an example to illustrate the calculation of the PCB etch factor. Suppose the following measurements were obtained:
- Etch Depth: 0.05 mm
- Undercut: 0.01 mm
Using the etch factor formula:
Etch Factor = (0.05 mm) / (0.01 mm) = 5
In this example, the PCB etch factor is 5.
Controlling PCB Etch Factor
Optimizing Etching Parameters
To achieve a desired etch factor and maintain consistency in PCB manufacturing, several etching parameters can be optimized:
-
Etching Solution: Selecting the appropriate etching solution and maintaining its concentration and temperature within specified ranges helps control the etch factor.
-
Etching Time: Adjusting the etching time based on the copper thickness and desired etch depth is crucial for achieving the target etch factor.
-
Agitation: Proper agitation of the etching solution ensures uniform etching and helps maintain a consistent etch factor across the PCB.
Design Considerations
PCB designers can also take certain measures to accommodate the etch factor and ensure manufacturability:
-
Trace Width and Spacing: Designing traces with appropriate widths and spacing based on the expected etch factor helps ensure accurate and reliable PCB performance.
-
Copper Thickness: Selecting the appropriate copper thickness for the PCB design, considering the etch factor, is important for achieving the desired circuit trace dimensions.
-
Artwork Compensation: Applying artwork compensation techniques, such as adding additional copper around critical features, can help counteract the effects of the etch factor and maintain the intended PCB geometry.
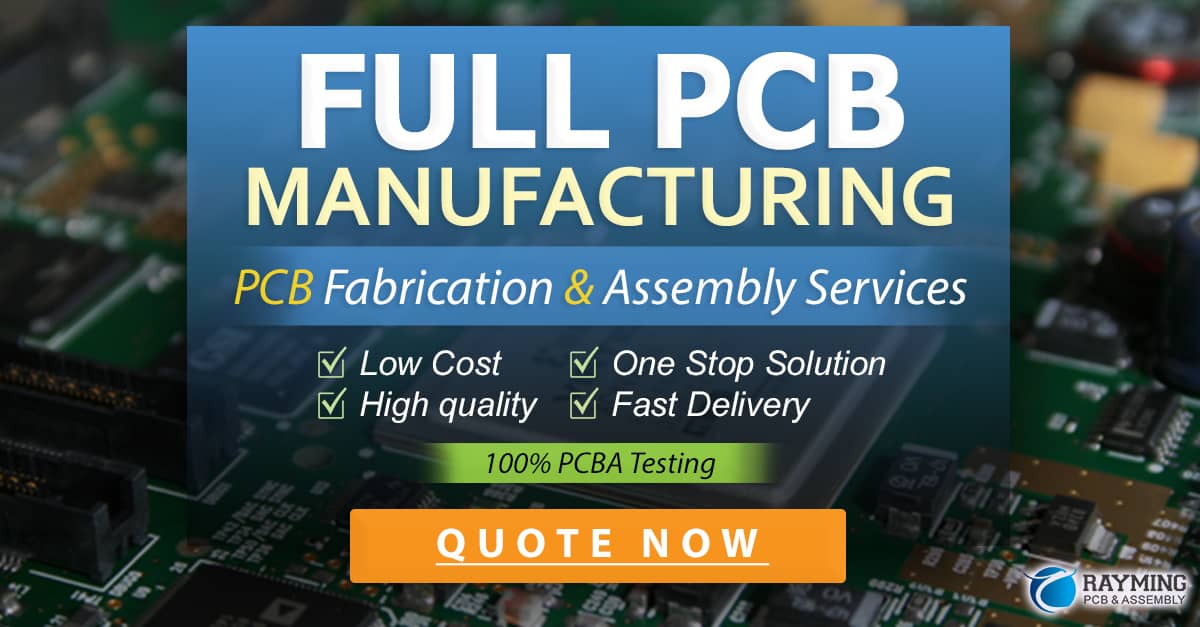
Impact of PCB Etch Factor on PCB Performance
Signal Integrity
The PCB etch factor has a direct impact on signal integrity in high-speed PCB designs. Inconsistencies in the etch factor can lead to variations in trace width and impedance, resulting in signal reflections, crosstalk, and other signal integrity issues. Maintaining a consistent etch factor is crucial for ensuring reliable signal transmission and minimizing signal distortion.
Power Integrity
The etch factor also affects power integrity in PCB designs. Variations in the etch factor can cause inconsistencies in the width of power and ground traces, leading to voltage drops and power distribution problems. Proper control of the etch factor helps maintain consistent power delivery and minimizes issues such as voltage ripple and ground bounce.
Thermal Management
The PCB etch factor can impact thermal management in PCB designs. Variations in the etch factor can result in inconsistent trace widths, affecting the current-carrying capacity and thermal dissipation of the traces. A well-controlled etch factor ensures that traces have the intended width and can handle the required current without excessive heating or thermal stress.
Frequently Asked Questions (FAQ)
-
What is the ideal PCB etch factor?
The ideal PCB etch factor depends on the specific requirements of the PCB design. Generally, an etch factor between 1.2 and 1.5 is considered desirable for most PCB applications. However, the exact target etch factor may vary based on factors such as the PCB layer count, copper thickness, and manufacturing capabilities. -
How does the PCB etch factor affect impedance?
The PCB etch factor directly influences the impedance of the traces on the PCB. A higher etch factor results in narrower traces, which increases the impedance. Conversely, a lower etch factor leads to wider traces and lower impedance. Inconsistencies in the etch factor can cause impedance mismatches, leading to signal integrity issues in high-speed PCB designs. -
Can the PCB etch factor be controlled during the manufacturing process?
Yes, the PCB etch factor can be controlled during the manufacturing process by optimizing various etching parameters. These include the composition and concentration of the etching solution, etching time, temperature, and agitation. PCB manufacturers employ strict process controls and monitoring techniques to maintain a consistent etch factor throughout the production process. -
How does the PCB etch factor affect manufacturing costs?
The PCB etch factor can impact manufacturing costs in several ways. A higher etch factor requires more precise control during the etching process, which can increase manufacturing time and costs. Additionally, designs with tighter tolerances and smaller feature sizes, which are affected by the etch factor, may require more advanced manufacturing techniques and materials, further increasing costs. -
What can PCB designers do to accommodate the etch factor in their designs?
PCB designers can take several measures to accommodate the etch factor in their designs. These include designing traces with appropriate widths and spacing based on the expected etch factor, selecting suitable copper thicknesses, and applying artwork compensation techniques. Collaborating closely with the PCB manufacturer and communicating design requirements can help ensure that the PCB design is optimized for the specific etch factor and manufacturing process.
Conclusion
PCB etch factor is a critical parameter in the manufacturing process of printed circuit boards. It represents the ratio between the etch depth and undercut during the etching process and has a significant impact on the accuracy, precision, and performance of the final PCB product. Understanding the factors that influence the etch factor, such as etching solution, copper thickness, etching time, and artwork design, is essential for achieving consistent and reliable PCB manufacturing.
Calculating the PCB etch factor involves measuring the etch depth and undercut using specialized equipment and applying the etch factor formula. Controlling the etch factor requires optimizing etching parameters and considering design factors such as trace width, spacing, and copper thickness. PCB designers can also employ artwork compensation techniques to accommodate the etch factor and ensure manufacturability.
The PCB etch factor has far-reaching implications for signal integrity, power integrity, and thermal management in PCB designs. Inconsistencies in the etch factor can lead to signal distortion, power distribution issues, and thermal problems. Therefore, maintaining a well-controlled etch factor is crucial for achieving reliable and high-performance PCB designs.
By understanding the significance of PCB etch factor, optimizing manufacturing processes, and collaborating closely with PCB manufacturers, designers can ensure that their PCB designs are optimized for the specific etch factor and meet the desired performance and reliability requirements.
0 Comments