What Causes PCB Delamination?
There are several potential causes of PCB delamination:
Moisture Absorption
One of the most common causes of delamination is moisture absorption by the PCB substrate material. FR-4, the most widely used PCB substrate, is somewhat hygroscopic and will absorb small amounts of moisture from the environment over time. If the moisture content becomes too high, it can vaporize during soldering operations. The rapid expansion of water vapor can cause localized delamination.
Thermal Stress
The coefficient of thermal expansion (CTE) measures how much a material expands when heated. Different materials in a PCB stackup have different CTEs. This CTE mismatch means the materials expand and contract at different rates as the PCB heats up and cools down during operation. Over many thermal cycles, this can lead to delamination, especially near the edges and corners of the board.
CTE mismatches are more problematic when using dissimilar materials like FR-4 and polyimide or when the copper percentage is very high. High layer count and thick PCBs are also at higher risk.
Mechanical Stress
PCBs can be subjected to various mechanical shocks and stresses during assembly, installation, and use. Flexing the board, rough handling, vibration, and impact can all impart mechanical stresses. If these stresses exceed the strength of the adhesion between layers, delamination can occur.
Causes of mechanical stress include:
- Depaneling methods like V-scoring that concentrate stress
- Excessive flexing during assembly or installation
- Structural design issues like insufficiently supported connectors
- Shock and vibration during transport or use
Chemical Contamination
Contamination of the PCB by incompatible chemicals is another potential cause of delamination. PCBs are exposed to a variety of chemicals during manufacturing and assembly, such as:
- Plating and etching solutions
- Fluxes and cleaning agents
- Conformal coatings and encapsulants
- Potting and filling compounds
If improperly selected or insufficiently cleaned, residues of these chemicals can degrade the adhesion between layers over time and lead to delamination. Ionic contamination is especially problematic.
Manufacturing Defects
Finally, defects introduced during the PCB manufacturing process can result in delamination. Some examples include:
- Insufficient or uneven pressure during lamination
- Prepreg material past its expiration date
- Contamination or damage to the inner layer surfaces
- Drilling burrs and resin smear in the holes
- Incompletely cured or dried layers
Careful process control and regular testing and inspection are needed to identify and correct these manufacturing issues.
Effects of PCB Delamination
Delamination can cause a variety of negative effects on PCB performance and reliability, including:
Intermittent Failures
In mild cases, delamination may only cause intermittent issues rather than hard failures. For example, an open circuit caused by delamination might still work most of the time if the separated pad is usually making contact. Intermittent failures can be especially difficult to troubleshoot.
Conductor Damage
Delaminated conductors are vulnerable to mechanical damage. Lacking the support of the surrounding substrate, they can be easily broken by handling or flexing. Delamination often starts at the outside edges of the board where conductors enter or exit, making them susceptible to damage.
Insulation Resistance Reduction
Delamination introduces a gap between layers that can be infiltrated by moisture and contaminants. Over time, these gaps can form conductive anodic filaments that degrade the insulation resistance between conductors on different layers. In severe cases, this may even allow short circuits to form.
Propagation of Cracks
Once delamination starts, it tends to spread rather than being self-limiting. Delamination gaps tend to propagate along the weakest interfaces first, like those between dissimilar materials. The spread of delamination can be accelerated by ongoing thermal or mechanical stresses.
Accelerated Failure Mechanisms
The presence of delamination can accelerate other PCB failure mechanisms as well. For example:
- The gaps and cracks provide a path for moisture and contaminant ingress
- Corrosion can proceed more rapidly on exposed conductors
- Unsupported barrel walls are more likely to crack
- Shock and vibration are transmitted more readily to components
Multiple interacting failure mechanisms tend to degrade the PCB faster than any one mechanism alone.
How to Prevent PCB Delamination
Prevention of delamination should be addressed in both the PCB design and manufacturing stages:
Material Selection
Choosing PCB substrate materials with lower moisture absorption and better thermal stability helps prevent delamination. Lower CTE FR-4 grades are available, as are non-DICY cured “high Tg” materials that absorb less moisture. For high reliability, consider polyimide or other non-organic materials.
Prepregs and laminate materials should be verified to have good quality and not be too old. Using prepregs that are too advanced or expired can result in poor adhesion.
Stack-Up Design
The PCB stack-up should be designed to minimize CTE mismatches between layers. Avoid thick cores, unbalanced construction, and excessive copper that can contribute to delamination.
If possible, use the same material for all layers of the stack-up. Using a different material for the outer layers might allow lower moisture absorption, but introduces a CTE mismatch that can lead to delamination.
Panelization
Choose a panelization method that minimizes mechanical stress on the PCB. Methods that concentrate stress at the board edges like V-scoring should be avoided in favor of more progressive methods like pizza-cutting or routing. Boards can also be partially routed and snapped apart after assembly to avoid stressing components.
Drilling and Plating
Careful process control is needed when drilling and plating through-holes. Drilling parameters like feed rate, spindle speed, and hit count should be optimized to avoid damage to the hole walls. Avoid excessive desmear etching that can attack the epoxy matrix.
Plating processes should be controlled to ensure good adhesion of the copper to the hole walls. Avoid excessive plating times and current densities that can lead to stressed deposits.
Thermal Profile
The reflow soldering thermal profile should be optimized to minimize the risk of delamination. Profiles with excessive peak temperatures or too little soak time can shock the PCB and cause delamination.
Vacuum drying of PCBs prior to assembly can help remove absorbed moisture and prevent popcorning during reflow. Baking times and temperatures must be carefully selected to avoid oxidizing the surface finish.
Cleanliness
Strict cleanliness should be maintained throughout PCB fabrication and assembly. Avoid contamination by ionic species, organic residues, and particulates. Assemblies should be cleaned as soon as possible after soldering to remove flux residues.
Use only clean, fresh chemistry in fabrication processes. Regularly monitor chemical baths for contamination build-up and replace as needed. Use purified water for rinsing and washing steps.
Handling and Packing
Proper handling and packing of PCBs is essential to avoid delamination. Assemblies should be handled by the edges to avoid flexing. Avoid rough handling, excessive manual testing, or stacking heavy assemblies.
Packing should immobilize the PCB and prevent flexing or vibration in transport. Wrapping in ESD-safe bubble wrap or foam can provide both mechanical and electrostatic protection. Consider moisture-barrier bags for long-term storage or shipping to humid environments.
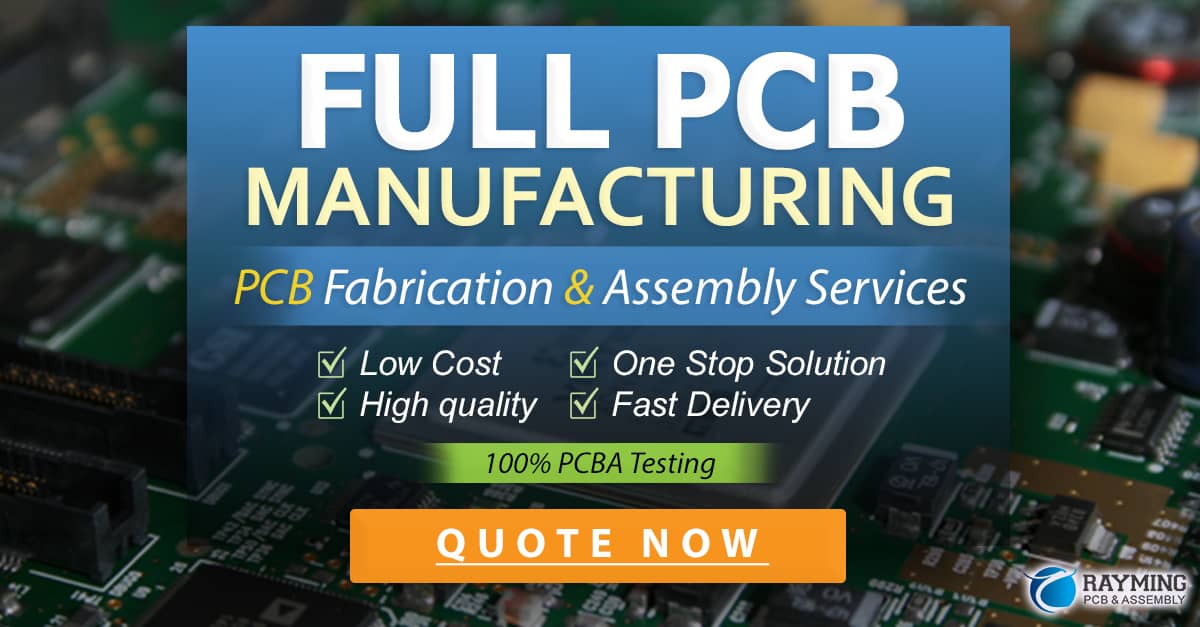
FAQ
What is the most common cause of PCB delamination?
Moisture absorption by the PCB substrate is one of the most common causes of delamination. When the absorbed moisture vaporizes rapidly during soldering, it can rupture the adhesion between layers.
Is PCB delamination more common in single-sided or double-sided PCBs?
PCB delamination is more common in multilayer PCBs than single or double-sided PCBs. Multilayer PCBs have more layer interfaces that can delaminate and are more likely to have CTE mismatches between layers.
Can PCB delamination be repaired?
In most cases, PCB delamination cannot be effectively repaired. While delaminated areas can sometimes be reinforced with epoxy or similar compounds, the repaired board is likely to have degraded performance and reliability. Rework of delaminated boards is generally not recommended.
How can you detect PCB delamination?
PCB delamination can often be detected visually by carefully inspecting the edges of the board for separation between layers. Delamination can also be detected by acoustic microscopy, X-ray inspection, or cross-sectioning of the board. Electrical testing may reveal open circuits or insulation resistance degradation caused by delamination.
What standards cover PCB delamination?
The most widely used standard for PCB delamination is IPC-TM-650, Method 2.4.8.1, “Peel Strength of Metallic Clad Laminates.” This method describes a destructive test for measuring the force required to separate the copper foil from the laminate. IPC-6012, “Qualification and Performance Specification for Rigid Printed Boards,” provides acceptability criteria for delamination in terms of allowable void area.
Here is an example table summarizing the causes and effects of PCB delamination:
Cause | Effects |
---|---|
Moisture absorption | Popcorning, insulation degradation, accelerated failure |
Thermal stress | Conductor cracking, barrel fractures, reduced life |
Mechanical stress | Broken conductors, pad lifting, shock failures |
Chemical contamination | Degraded adhesion, electrochemical migration |
Manufacturing defects | Interconnect failures, propagating cracks, field returns |
In summary, PCB delamination is a complex issue with multiple potential causes and far-reaching effects on reliability. Preventing delamination requires careful attention in both the design and manufacturing phases. By selecting materials properly, controlling the fabrication processes, and handling PCBs appropriately, the risk of delamination can be significantly reduced.
0 Comments