Understanding PCB Deformation and Its Impact on Electronics Manufacturing
Printed Circuit Boards (PCBs) are the backbone of modern electronics, providing a platform for interconnecting electronic components in a compact and efficient manner. However, during the manufacturing process and throughout their lifecycle, PCBs can experience various forms of deformation, such as bowing and twisting. These deformations can have significant implications for the functionality, reliability, and longevity of electronic devices. In this article, we will delve into the concepts of PCB bow and twist, explore their causes, and discuss strategies for minimizing their impact on PCB performance.
Table of Contents
- Introduction to PCB Deformation
- PCB Bow: Definition and Causes
- PCB Twist: Definition and Causes
- Impact of PCB Deformation on Electronics Performance
- Measuring and Quantifying PCB Bow and Twist
- Strategies for Minimizing PCB Deformation
- Material Selection
- Design Considerations
- Manufacturing Process Optimization
- Storage and Handling
- Industry Standards and Guidelines
- Case Studies and Real-World Examples
- Future Trends and Innovations
- Frequently Asked Questions (FAQ)
- Conclusion
Introduction to PCB Deformation
PCB deformation refers to any deviation from the intended flat and planar shape of a printed circuit board. Two common types of PCB deformation are bow and twist. These deformations can occur due to various factors, including material properties, manufacturing processes, and environmental conditions.
PCB deformation can lead to several issues, such as:
– Difficulties in component assembly and soldering
– Mechanical stress on components and solder joints
– Compromised electrical connections and signal integrity
– Reduced reliability and durability of the electronic device
Understanding the causes and effects of PCB bow and twist is crucial for ensuring the quality and performance of electronic products.
PCB Bow: Definition and Causes
PCB bow, also known as warpage, refers to the curvature or deviation from flatness along the length or width of a printed circuit board. A PCB is considered to have a bow when its center point is raised or lowered relative to its edges.
Several factors can contribute to PCB bow:
-
Coefficient of Thermal Expansion (CTE) Mismatch: Different materials used in PCB construction, such as the substrate, copper layers, and solder mask, have varying CTEs. During thermal cycling, these materials expand and contract at different rates, leading to stress and potential bowing.
-
Uneven Copper Distribution: An imbalance in the copper coverage between the top and bottom layers of a PCB can cause uneven thermal expansion, resulting in bowing.
-
Moisture Absorption: PCB substrates, particularly those made from hygroscopic materials like FR-4, can absorb moisture from the environment. This moisture absorption can lead to dimensional changes and bowing.
-
Mechanical Stress: Improper handling, mounting, or excessive mechanical forces during the assembly process can cause PCBs to bend or bow.
The extent of PCB bow can be influenced by factors such as the board thickness, material properties, and the presence of stiffeners or support structures.
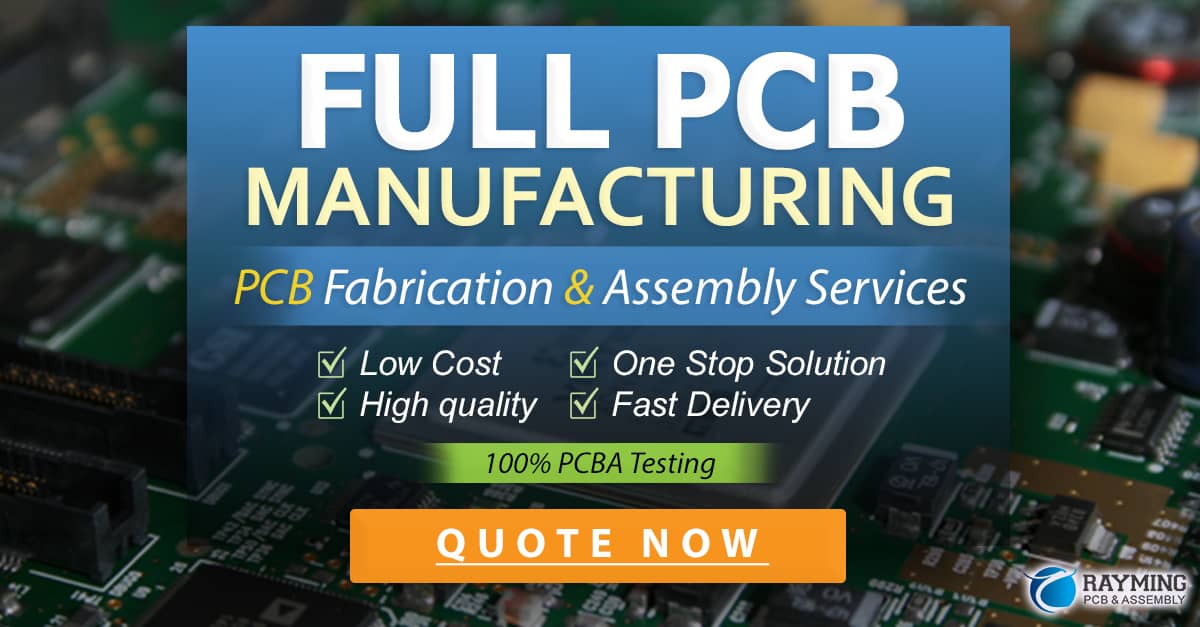
PCB Twist: Definition and Causes
PCB twist, also referred to as skew or warpage, is a type of deformation where the printed circuit board experiences a rotational distortion along its diagonal axis. In other words, one corner of the PCB is raised or lowered relative to the opposite corner.
The primary causes of PCB twist include:
-
Asymmetric Copper Distribution: When the copper traces and planes are not symmetrically distributed across the PCB layers, it can lead to uneven thermal expansion and contraction, causing the board to twist.
-
Unbalanced Mechanical Stress: Non-uniform mechanical stress during the manufacturing process, such as uneven pressure during lamination or improper handling, can result in PCB twist.
-
Material Inconsistencies: Variations in the properties of the PCB substrate, such as thickness or glass weave alignment, can contribute to twisting.
Like PCB bow, the severity of twist can be influenced by factors such as board thickness, material selection, and the presence of reinforcing structures.
Impact of PCB Deformation on Electronics Performance
PCB deformation, whether in the form of bow or twist, can have significant consequences for the performance and reliability of electronic devices. Some of the key impacts include:
-
Assembly Challenges: Deformed PCBs can pose difficulties during the component placement and soldering processes. Misaligned or poorly seated components can lead to weak solder joints and compromised electrical connections.
-
Mechanical Stress: Bowed or twisted PCBs can exert additional mechanical stress on components and solder joints, increasing the risk of failures such as cracks, fractures, or intermittent connections.
-
Signal Integrity Issues: Deformation can alter the intended impedance and signal propagation characteristics of PCB traces, leading to signal integrity problems such as reflections, crosstalk, and electromagnetic interference (EMI).
-
Reduced Reliability: PCBs subjected to excessive deformation may experience premature failures due to the cumulative effects of mechanical stress and compromised electrical connections.
-
Fitment and Enclosure Challenges: Deformed PCBs may not fit properly within their designated enclosures or mating connectors, leading to assembly issues and potential damage to the board or surrounding components.
To mitigate these impacts, it is essential to control and minimize PCB deformation throughout the design, manufacturing, and assembly processes.
Measuring and Quantifying PCB Bow and Twist
Accurate measurement and quantification of PCB bow and twist are crucial for ensuring compliance with industry standards and maintaining quality control. Several methods and tools are used to assess PCB deformation:
-
Visual Inspection: A simple visual examination can provide a qualitative assessment of PCB flatness and identify any obvious deformations.
-
Flatness Gauges: Specialized flatness gauges, such as dial indicators or feeler gauges, can be used to measure the deviation from flatness at specific points on the PCB surface.
-
3D Scanning: Advanced 3D scanning techniques, such as laser or optical scanning, can create detailed surface profiles of PCBs, allowing for precise measurement of bow and twist.
-
Shadow Moiré: This optical technique projects a grid pattern onto the PCB surface and analyzes the resulting moiré fringes to determine surface contours and deformation.
The measurement data obtained through these methods can be compared against industry standards and specifications to determine if the PCB deformation is within acceptable limits.
Strategies for Minimizing PCB Deformation
To minimize the occurrence and impact of PCB bow and twist, several strategies can be employed during the design, manufacturing, and handling stages.
Material Selection
Careful selection of PCB materials can help reduce the risk of deformation:
- Choose substrates with low CTE and good dimensional stability, such as high-quality FR-4 or specialized materials like polyimide or ceramic.
- Consider using materials with similar CTEs for the PCB substrate, copper layers, and solder mask to minimize thermal mismatch.
- Opt for materials with low moisture absorption properties to reduce the impact of humidity on PCB deformation.
Design Considerations
Incorporating certain design practices can help mitigate PCB bow and twist:
- Balance copper distribution across PCB layers to minimize uneven thermal expansion and contraction.
- Utilize symmetrical design techniques, such as mirroring or rotating component placement and routing, to promote even mechanical stress distribution.
- Incorporate stiffeners, support structures, or thicker PCB substrates to increase rigidity and resistance to deformation.
- Optimize the placement of heavy components or connectors to minimize localized stress concentrations.
Manufacturing Process Optimization
Refining the PCB manufacturing process can contribute to reduced deformation:
- Implement strict process controls and monitor key parameters, such as lamination pressure, temperature, and dwell time, to ensure consistency.
- Use specialized lamination techniques, such as vacuum lamination or pressure equalization, to minimize uneven stress distribution.
- Employ precise copper etching and plating processes to maintain consistent copper distribution and thickness across the PCB layers.
- Implement quality control measures, such as in-process inspection and post-manufacturing testing, to identify and address any deformation issues promptly.
Storage and Handling
Proper storage and handling practices can help preserve PCB flatness:
- Store PCBs in a controlled environment with stable temperature and humidity levels to minimize moisture absorption and thermal stress.
- Use appropriate packaging materials and techniques, such as vacuum sealing or moisture barrier bags, to protect PCBs during storage and transportation.
- Handle PCBs with care, avoiding excessive bending, twisting, or rough handling that can induce mechanical stress and deformation.
- Implement electrostatic discharge (ESD) protection measures to prevent damage to sensitive components and maintain PCB integrity.
By implementing these strategies throughout the PCB lifecycle, designers and manufacturers can effectively minimize the occurrence and impact of PCB bow and twist.
Industry Standards and Guidelines
Several industry standards and guidelines provide specifications and tolerances for PCB deformation, ensuring consistency and reliability in electronic products. Some key standards include:
- IPC-TM-650 2.4.22: Bow and Twist
- IPC-6012: Qualification and Performance Specification for Rigid Printed Boards
- IPC-A-610: Acceptability of Electronic Assemblies
- JEDEC JEP95: Design Guide 4.2 – Printed Board Flatness Guidelines
These standards outline measurement methods, acceptance criteria, and best practices for controlling PCB bow and twist. Adhering to these guidelines helps manufacturers produce high-quality PCBs that meet industry requirements and customer expectations.
Case Studies and Real-World Examples
To illustrate the impact of PCB deformation and the effectiveness of mitigation strategies, let’s consider a few real-world examples:
-
Smartphone Manufacturer: A smartphone manufacturer experienced high failure rates due to PCB bow causing intermittent connections and component failures. By implementing a balanced copper design and optimizing the lamination process, they significantly reduced the occurrence of bow and improved product reliability.
-
Automotive Electronics Supplier: An automotive electronics supplier encountered fitment issues and signal integrity problems due to PCB twist in their engine control modules. By incorporating stiffeners and enhancing their material selection process, they minimized twist and ensured proper fitment and performance of their modules.
-
Aerospace Electronics Company: An aerospace electronics company required extremely flat PCBs for their high-precision avionics systems. They utilized advanced 3D scanning techniques to measure and control PCB deformation, ensuring compliance with stringent flatness requirements.
These examples demonstrate the practical implications of PCB deformation and the importance of implementing effective strategies to mitigate its impact on electronic products.
Future Trends and Innovations
As electronic devices continue to evolve and become more complex, the challenges posed by PCB deformation will likely increase. However, ongoing research and innovations in materials, design, and manufacturing technologies offer promising solutions:
-
Advanced Materials: The development of novel PCB substrate materials with improved dimensional stability, lower CTE, and reduced moisture absorption will help minimize deformation risks.
-
3D Printing: Advancements in 3D printing technologies for electronics, such as conductive ink printing and multi-material printing, may enable the creation of PCBs with intricate geometries and built-in support structures to enhance flatness.
-
Simulation and Modeling: Sophisticated simulation and modeling tools will allow designers to predict and optimize PCB deformation behavior early in the design process, enabling proactive mitigation strategies.
-
Automated Inspection: The integration of advanced machine vision systems and artificial intelligence algorithms in PCB inspection processes will enable more accurate and efficient detection of deformation issues.
-
Flexible and Stretchable Electronics: The emergence of flexible and stretchable PCB technologies may require new approaches to managing deformation, as these substrates inherently exhibit different mechanical behaviors compared to rigid PCBs.
By staying at the forefront of these technological advancements, the electronics industry can continue to innovate and develop solutions to address the challenges posed by PCB bow and twist.
Frequently Asked Questions (FAQ)
- What is the difference between PCB bow and twist?
-
PCB bow refers to the curvature or deviation from flatness along the length or width of a PCB, while twist is a rotational distortion along the diagonal axis of the board.
-
How does PCB deformation affect the reliability of electronic devices?
-
PCB deformation can lead to component misalignment, weak solder joints, mechanical stress, and signal integrity issues, all of which can compromise the reliability and longevity of electronic devices.
-
What are some common causes of PCB bow and twist?
-
Common causes include CTE mismatch between PCB materials, uneven copper distribution, moisture absorption, asymmetric mechanical stress, and material inconsistencies.
-
How can PCB deformation be measured and quantified?
-
PCB deformation can be measured using visual inspection, flatness gauges, 3D scanning, and shadow moiré techniques. The obtained data can be compared against industry standards to determine compliance.
-
What are some strategies for minimizing PCB deformation?
- Strategies include careful material selection, balanced copper distribution, symmetrical design techniques, manufacturing process optimization, and proper storage and handling practices.
Conclusion
PCB bow and twist are critical aspects of PCB deformation that can significantly impact the performance, reliability, and longevity of electronic devices. Understanding the causes, effects, and mitigation strategies for PCB deformation is essential for designers, manufacturers, and quality control professionals in the electronics industry.
By implementing best practices in material selection, design, manufacturing, and handling, the occurrence and impact of PCB bow and twist can be effectively minimized. Adherence to industry standards and the adoption of innovative technologies and techniques will further contribute to the production of high-quality, reliable PCBs.
As the electronics industry continues to evolve, addressing the challenges posed by PCB deformation will remain a critical focus area. Through ongoing research, collaboration, and innovation, the industry can develop advanced solutions to ensure the flatness and integrity of PCBs, ultimately enhancing the performance and durability of electronic products.
0 Comments