Understanding Surface Finishes in PCB Manufacturing
Surface finishes are critical in PCB manufacturing as they protect the exposed copper pads from oxidation and contamination. They also enhance the solderability of the pads, allowing for proper bonding between the PCB and the electronic components during the assembly process. There are various types of surface finishes used in the industry, each with its own advantages and disadvantages. Some common surface finishes include:
- Hot Air Solder Leveling (HASL)
- Electroless Nickel Immersion Gold (ENIG)
- Immersion Silver
- Immersion Tin
- Organic Solderability Preservative (OSP)
Importance of Choosing the Right Surface Finish
Selecting the appropriate surface finish is crucial for the overall performance and reliability of the PCB. Factors to consider when choosing a surface finish include:
-
Solderability: The surface finish should provide excellent solderability, allowing for easy and reliable bonding of components to the PCB.
-
Shelf life: The surface finish should have a sufficient shelf life to maintain its solderability until the PCB is assembled.
-
Cost: The cost of the surface finish should be considered in relation to the overall project budget and the required performance.
-
Compatibility: The surface finish should be compatible with the PCB materials, components, and the intended application environment.
-
Environmental impact: Some surface finishes may have environmental concerns due to the use of certain chemicals or processes.
What is Organic Solderability Preservative (OSP)?
Organic Solderability Preservative (OSP) is a thin, transparent organic coating applied to the copper pads of a PCB. This coating acts as a barrier, protecting the copper from oxidation and contamination while maintaining its solderability. OSP is applied through a chemical process that involves cleaning the copper surface, applying the OSP coating, and then drying the PCB.
Composition of OSP
OSP coatings are typically composed of organic compounds such as benzimidazoles, benzotriazoles, or imidazoles. These compounds form a thin, uniform layer on the copper surface, typically measuring between 0.2 to 0.5 microns in thickness. The exact composition of OSP coatings may vary depending on the manufacturer and the specific requirements of the application.
How OSP Works
When applied to the copper pads, the OSP coating forms a chemical bond with the copper surface. This bond creates a protective layer that prevents oxygen and other contaminants from reacting with the copper, thus maintaining its solderability. During the soldering process, the OSP coating dissolves into the molten solder, allowing for a reliable and strong bond between the component and the PCB.
Advantages of OSP Surface Finish
OSP offers several advantages over other surface finishes, making it a popular choice in the PCB industry:
-
Cost-effective: OSP is one of the most cost-effective surface finishes available, as it requires fewer processing steps and materials compared to other finishes like ENIG or immersion silver.
-
Flat surface: OSP coatings provide a flat, planar surface, which is essential for fine-pitch components and high-density PCB designs.
-
Excellent solderability: OSP coatings offer excellent solderability, ensuring reliable and strong bonds between components and the PCB.
-
Environmentally friendly: Unlike some other surface finishes, OSP does not contain lead or other harmful substances, making it a more environmentally friendly option.
-
Compatibility with various soldering methods: OSP is compatible with a wide range of soldering methods, including wave soldering, reflow soldering, and hand soldering.
Comparison of OSP with Other Surface Finishes
Surface Finish | Cost | Shelf Life | Solderability | Environmental Impact |
---|---|---|---|---|
OSP | Low | 6-12 months | Excellent | Low |
ENIG | High | 12+ months | Excellent | Moderate |
Immersion Silver | Moderate | 6-12 months | Good | Low |
Immersion Tin | Moderate | 6-12 months | Good | Low |
HASL | Low | 6-12 months | Good | High (lead content) |
As shown in the table above, OSP offers a balance of cost-effectiveness, excellent solderability, and low environmental impact compared to other surface finishes.
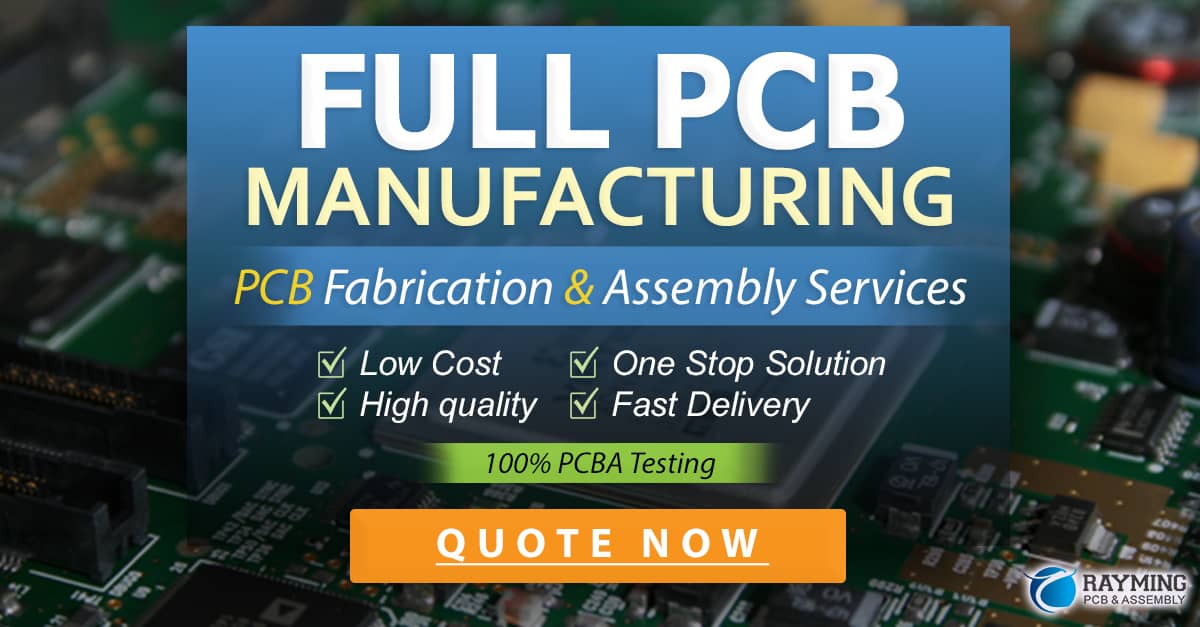
Applications of OSP Surface Finish
OSP surface finish is widely used in various industries and applications, including:
-
Consumer electronics: OSP is commonly used in the manufacturing of PCBs for consumer electronic devices such as smartphones, tablets, and laptops.
-
Automotive electronics: The automotive industry relies on OSP for the production of PCBs used in various vehicle systems, such as infotainment, sensors, and control modules.
-
Medical devices: OSP is used in the manufacturing of PCBs for medical devices, where reliability and performance are critical.
-
Industrial equipment: PCBs with OSP surface finish are used in a wide range of industrial equipment, including control systems, automation devices, and monitoring equipment.
Case Studies
-
Smartphone manufacturer: A leading smartphone manufacturer chose OSP surface finish for their PCBs due to its cost-effectiveness and excellent solderability. By using OSP, the company was able to achieve high-quality, reliable bonding of components while keeping production costs low.
-
Automotive electronics supplier: An automotive electronics supplier selected OSP for their PCBs used in vehicle control modules. The OSP surface finish provided the necessary protection against oxidation and ensured reliable soldering, resulting in improved overall product quality and performance.
Best Practices for Working with OSP Surface Finish
When working with PCBs that have an OSP surface finish, there are several best practices to follow to ensure optimal results:
-
Storage: Store OSP-coated PCBs in a cool, dry environment to prevent moisture absorption and maintain the integrity of the coating.
-
Handling: Handle OSP-coated PCBs with clean, lint-free gloves to avoid contamination of the surface.
-
Soldering: Follow the recommended soldering parameters, including temperature and time, to achieve the best results and avoid damaging the OSP coating.
-
Cleaning: If cleaning is necessary, use approved cleaning agents and methods that are compatible with the OSP coating to prevent degradation of the surface finish.
-
Inspection: Regularly inspect the OSP-coated PCBs for any signs of oxidation, contamination, or damage, and take corrective action as needed.
Frequently Asked Questions (FAQ)
- What is the shelf life of OSP surface finish?
-
The shelf life of OSP surface finish is typically 6-12 months when stored in proper conditions. It is essential to keep OSP-coated PCBs in a cool, dry environment to maintain their solderability.
-
Can OSP be used for high-temperature applications?
-
OSP is suitable for most standard soldering processes, including wave soldering and reflow soldering. However, for high-temperature applications, it is recommended to consult with the PCB manufacturer to ensure the OSP coating can withstand the required temperatures.
-
Is OSP compatible with lead-free soldering?
-
Yes, OSP surface finish is compatible with lead-free soldering processes. The organic compounds used in OSP coatings are designed to dissolve into both lead-based and lead-free solders, ensuring reliable bonding.
-
How does OSP compare to ENIG in terms of cost?
-
OSP is generally more cost-effective than ENIG, as it requires fewer processing steps and materials. While ENIG offers a longer shelf life, OSP provides a balance of cost savings and excellent solderability for most applications.
-
Can OSP be used for fine-pitch components?
- Yes, OSP surface finish is well-suited for fine-pitch components due to its flat, planar surface. The thin, uniform coating allows for precise placement and soldering of small components, making it an ideal choice for high-density PCB designs.
Conclusion
Organic Solderability Preservative (OSP) or Anti-Tarnish Surface Finish is a critical aspect of PCB manufacturing, providing a cost-effective and reliable solution for protecting copper pads and ensuring excellent solderability. By understanding the properties, advantages, and best practices associated with OSP, PCB designers and manufacturers can make informed decisions when selecting surface finishes for their projects. As the electronics industry continues to evolve, OSP remains a popular choice for a wide range of applications, offering a balance of performance, cost-effectiveness, and environmental friendliness.
0 Comments