Introduction to Lead-Free Soldering
Lead-free soldering, also known as Restriction of Hazardous Substances (RoHS) compliant soldering, is a process used in the electronics industry to join components and printed circuit boards (PCBs) without the use of lead. This shift towards lead-free soldering was driven by the European Union’s RoHS directive, which aimed to reduce the environmental and health impacts of hazardous substances in electronic products.
The RoHS Directive and Its Impact
The RoHS directive, first introduced in 2003 and updated in 2011 (RoHS 2) and 2015 (RoHS 3), restricts the use of six hazardous materials in the manufacture of electronic and electrical equipment:
- Lead (Pb)
- Mercury (Hg)
- Cadmium (Cd)
- Hexavalent chromium (Cr6+)
- Polybrominated biphenyls (PBB)
- Polybrominated diphenyl ether (PBDE)
The directive applies to a wide range of electronic products, including household appliances, IT and telecommunications equipment, lighting equipment, electrical and electronic tools, toys, and leisure and sports equipment. By restricting the use of these hazardous substances, the RoHS directive aims to protect human health and the environment, as well as facilitate the recycling and safe disposal of electronic waste.
Lead-Free Solder Alloys
To comply with the RoHS directive, the electronics industry has developed several lead-free solder alloys as alternatives to the traditional tin-lead (Sn-Pb) solder. The most commonly used lead-free solder alloys include:
Tin-Silver-Copper (SAC) Alloys
SAC alloys are the most widely used lead-free solder alloys, with the most common composition being Sn96.5Ag3.0Cu0.5 (SAC305). These alloys offer good mechanical strength, thermal fatigue resistance, and wettability. However, they have a higher melting point compared to Sn-Pb solder, which can lead to increased thermal stress on components during the soldering process.
Tin-Copper (Sn-Cu) Alloys
Sn-Cu alloys, such as Sn99.3Cu0.7 (Sn99Cu1), are cost-effective alternatives to SAC alloys. They have a lower melting point than SAC alloys but may exhibit inferior mechanical properties and wettability.
Tin-Silver (Sn-Ag) Alloys
Sn-Ag alloys, such as Sn96.5Ag3.5, offer good mechanical strength and thermal fatigue resistance. However, they have a higher melting point than SAC alloys and may be more expensive due to their higher silver content.
Comparison of Lead-Free Solder Alloys
Alloy | Composition | Melting Point (°C) | Advantages | Disadvantages |
---|---|---|---|---|
SAC305 | Sn96.5Ag3.0Cu0.5 | 217-220 | Good mechanical strength and thermal fatigue resistance, good wettability | Higher melting point, increased thermal stress on components |
Sn99Cu1 | Sn99.3Cu0.7 | 227 | Cost-effective, lower melting point than SAC alloys | Inferior mechanical properties and wettability |
Sn96.5Ag3.5 | Sn96.5Ag3.5 | 221 | Good mechanical strength and thermal fatigue resistance | Higher melting point, more expensive due to higher silver content |
Challenges and Considerations in Lead-Free Soldering
The transition to lead-free soldering has presented several challenges and considerations for the electronics industry:
Higher Melting Point and Thermal Stress
Lead-free solder alloys generally have higher melting points compared to traditional Sn-Pb solder. This can lead to increased thermal stress on components during the soldering process, potentially affecting their reliability and performance. To mitigate this issue, manufacturers may need to adjust their soldering processes, such as using higher soldering temperatures, longer dwell times, or improved cooling methods.
Wetting and Spreading Characteristics
Lead-free solder alloys may exhibit different wetting and spreading characteristics compared to Sn-Pb solder. This can impact the quality of solder joints and the reliability of the soldered assembly. Manufacturers may need to optimize their soldering processes, such as adjusting the solder paste formulation, stencil design, or reflow profile, to ensure good solder joint formation.
Tin Whiskers and Reliability Concerns
The use of lead-free solder alloys, particularly those with high tin content, can increase the risk of tin whisker formation. Tin whiskers are thin, conductive filaments that can grow from tin-based surfaces and cause short circuits or other reliability issues. To mitigate this risk, manufacturers may employ various strategies, such as using conformal coatings, altering the surface finish of components, or using alloys with lower tin content.
Compatibility with Existing Equipment and Processes
The transition to lead-free soldering may require manufacturers to upgrade or modify their existing equipment and processes. This can include investing in new soldering machines, adjusting reflow profiles, and training personnel on lead-free soldering techniques. Manufacturers must carefully plan and manage this transition to ensure a smooth and cost-effective implementation of lead-free soldering.
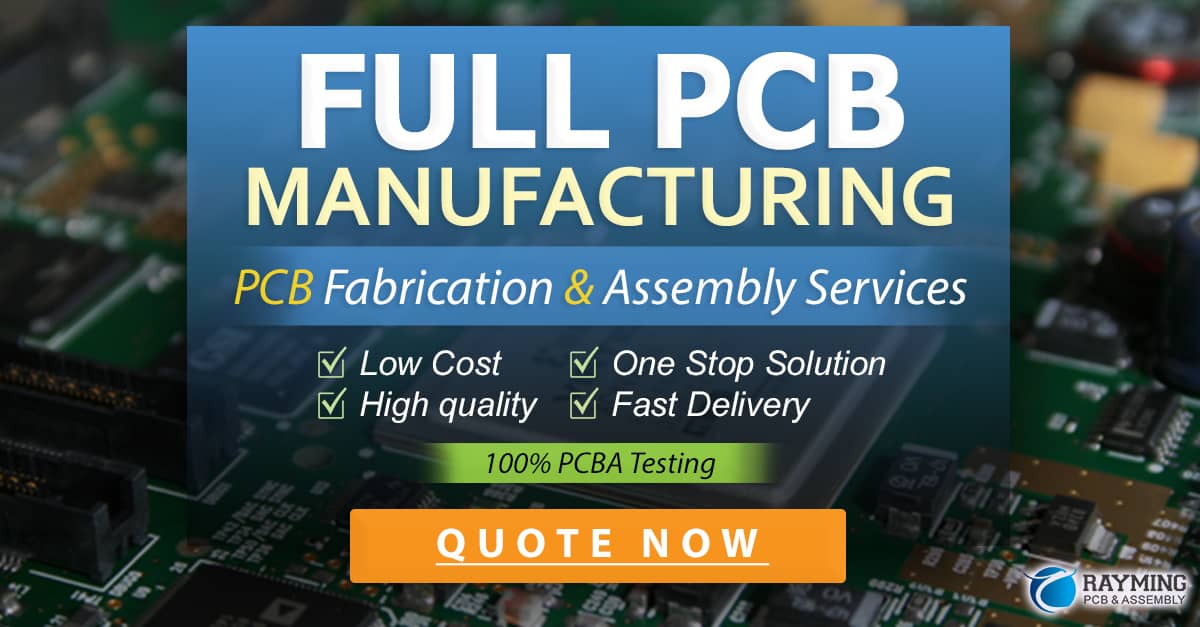
Best Practices for Implementing Lead-Free Soldering
To successfully implement lead-free soldering and ensure the reliability of lead-free soldered assemblies, manufacturers should consider the following best practices:
-
Careful alloy selection: Choose a lead-free solder alloy that meets the specific requirements of the application, considering factors such as melting point, mechanical strength, wettability, and cost.
-
Process optimization: Optimize the soldering process parameters, such as solder paste formulation, stencil design, reflow profile, and cooling methods, to ensure good solder joint formation and minimize thermal stress on components.
-
Equipment upgrades and maintenance: Invest in equipment that is compatible with lead-free soldering, and ensure proper maintenance and calibration to maintain process consistency and quality.
-
Training and education: Provide adequate training and education for personnel involved in lead-free soldering, including best practices, troubleshooting, and quality control.
-
Collaboration with suppliers: Work closely with component suppliers and contract manufacturers to ensure the compatibility and reliability of lead-free soldered assemblies.
-
Continuous improvement: Regularly monitor and assess the performance of lead-free soldered assemblies, and implement continuous improvement initiatives to address any issues and optimize the soldering process.
Frequently Asked Questions (FAQ)
1. What is the main difference between lead-free soldering and traditional soldering?
Lead-free soldering uses solder alloys that do not contain lead, while traditional soldering uses tin-lead (Sn-Pb) solder alloys. This change was driven by the RoHS directive, which aims to reduce the environmental and health impacts of hazardous substances in electronic products.
2. Are lead-free solder joints as reliable as traditional solder joints?
When implemented properly, lead-free solder joints can be as reliable as traditional solder joints. However, the transition to lead-free soldering has presented some challenges, such as higher melting points, different wetting and spreading characteristics, and the risk of tin whisker formation. Manufacturers must carefully optimize their soldering processes and materials to ensure the reliability of lead-free solder joints.
3. Can lead-free solder be used with existing soldering equipment?
In some cases, existing soldering equipment may need to be upgraded or modified to be compatible with lead-free soldering. This is because lead-free solder alloys have different properties, such as higher melting points, which may require adjustments to the soldering process. Manufacturers should assess their existing equipment and make necessary changes to ensure successful implementation of lead-free soldering.
4. How can manufacturers mitigate the risk of tin whisker formation in lead-free soldered assemblies?
Manufacturers can employ various strategies to mitigate the risk of tin whisker formation in lead-free soldered assemblies. These include using conformal coatings to protect the surface, altering the surface finish of components to reduce tin whisker growth, or using solder alloys with lower tin content. Additionally, proper process control and regular monitoring can help identify and address any tin whisker issues.
5. What are the long-term benefits of transitioning to lead-free soldering?
The transition to lead-free soldering offers several long-term benefits, both for the environment and human health. By reducing the use of hazardous substances like lead in electronic products, lead-free soldering helps minimize the environmental impact of electronic waste and facilitates safer recycling and disposal practices. Additionally, lead-free soldering reduces the potential for human exposure to lead, which can have detrimental health effects. As the electronics industry continues to grow and evolve, the adoption of lead-free soldering will contribute to a more sustainable and responsible future.
Conclusion
Lead-free soldering, driven by the RoHS directive, has become an essential part of the electronics industry’s efforts to reduce the environmental and health impacts of hazardous substances. By using lead-free solder alloys and optimizing soldering processes, manufacturers can produce reliable and compliant electronic products. However, the transition to lead-free soldering has presented several challenges, such as higher melting points, different wetting and spreading characteristics, and the risk of tin whisker formation.
To successfully implement lead-free soldering, manufacturers must carefully select solder alloys, optimize their soldering processes, upgrade equipment, and provide proper training for their personnel. Collaboration with suppliers and continuous improvement initiatives are also crucial for ensuring the reliability and performance of lead-free soldered assemblies.
As the electronics industry continues to evolve and prioritize sustainability, the adoption of lead-free soldering will play a vital role in creating a more environmentally friendly and responsible future. By embracing best practices and overcoming the challenges associated with lead-free soldering, manufacturers can contribute to the development of safer, more reliable, and more sustainable electronic products.
0 Comments