The History of Lead-based Soldering
Lead has been used in soldering for centuries, with evidence of its use dating back to ancient civilizations. In the modern era, lead-based solders became the standard in the electronics industry due to their favorable properties, such as low melting point, good wettability, and excellent electrical conductivity.
The most common lead-based solder alloy is known as Sn63Pb37, which consists of 63% tin (Sn) and 37% lead (Pb) by weight. This eutectic alloy has a melting point of 183°C (361°F), making it suitable for a wide range of soldering applications.
Advantages of Lead-based Soldering
Lead-based solders offer several advantages over lead-free alternatives:
-
Lower melting point: Lead-based solders have a lower melting point compared to most lead-free solders, which means they require less energy to melt and can be used at lower temperatures. This reduces the risk of thermal damage to components and substrates.
-
Better wetting properties: Lead-based solders exhibit excellent wetting properties, meaning they can easily flow and adhere to the surfaces being joined. This results in stronger, more reliable solder joints.
-
Improved mechanical properties: Solder joints made with lead-based alloys have better mechanical properties, such as higher shear strength and better resistance to fatigue and creep.
-
Lower cost: Lead is relatively inexpensive compared to some of the metals used in lead-free solders, such as silver and copper. As a result, lead-based solders are generally more cost-effective.
Disadvantages of Lead-based Soldering
Despite its advantages, lead-based soldering has several drawbacks:
-
Environmental impact: Lead is a toxic heavy metal that can accumulate in the environment and cause harm to wildlife and ecosystems. When electronic devices containing lead are improperly disposed of, the lead can leach into soil and water, posing a long-term environmental risk.
-
Health risks: Exposure to lead can have serious health consequences, particularly for children and pregnant women. Lead can cause developmental delays, learning difficulties, and other neurological problems. In adults, lead exposure can lead to cardiovascular disease, kidney damage, and reproductive issues.
-
Regulatory restrictions: Many countries have implemented regulations, such as the RoHS directive, that restrict or prohibit the use of lead in electronic products. Manufacturers who continue to use lead-based solders may face legal and financial penalties, as well as barriers to entering certain markets.
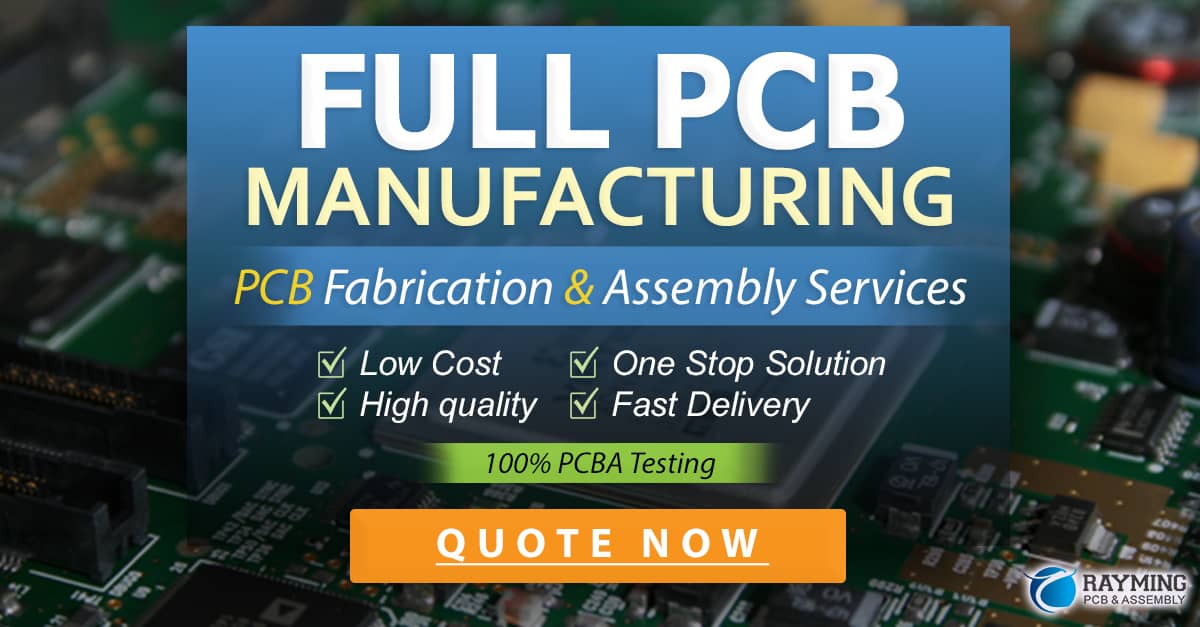
The RoHS Directive and Its Impact on Lead-based Soldering
The Restriction of Hazardous Substances (RoHS) directive is a set of regulations that limits the use of certain hazardous materials, including lead, in electronic and electrical equipment. The directive was first introduced by the European Union in 2003 and has since been adopted by many other countries worldwide.
Under RoHS, the maximum allowable concentration of lead in homogeneous materials is 0.1% by weight. This means that manufacturers must use lead-free solders or obtain exemptions for specific applications where lead-free alternatives are not feasible.
The implementation of RoHS has driven a significant shift towards lead-free soldering in the electronics industry. Many manufacturers have invested in research and development to create lead-free solder alloys that can meet the performance requirements of their products while complying with the directive.
Lead-free Solder Alternatives
To comply with RoHS and other lead-restriction regulations, manufacturers have developed a range of lead-free solder alloys. These alloys typically contain a combination of tin, silver, copper, and other metals. Some common lead-free solder alloys include:
-
SAC305 (Sn96.5Ag3.0Cu0.5): This alloy contains 96.5% tin, 3% silver, and 0.5% copper. It has a melting point of 217-220°C and is widely used in the electronics industry due to its good mechanical properties and reliability.
-
SN100C (Sn99.3Cu0.7 + Ni): This alloy contains 99.3% tin and 0.7% copper, with a small amount of nickel added to improve wetting properties. It has a melting point of 227°C and is known for its excellent solderability and resistance to tin whisker growth.
-
SnCuNi (Sn99.2Cu0.7Ni0.1): This alloy contains 99.2% tin, 0.7% copper, and 0.1% nickel. It has a melting point of 227°C and offers good mechanical properties and resistance to thermal cycling.
While lead-free solders have been successfully adopted in many applications, they present some challenges compared to lead-based solders. Lead-free solders typically have higher melting points, which can increase the risk of thermal damage to components and substrates. They may also have different wetting properties and require adjustments to soldering processes and equipment.
Applications Where Lead-based Soldering is Still Used
Despite the widespread adoption of lead-free soldering, there are still some applications where lead-based solders are used. These are typically cases where the performance requirements or operating conditions make lead-free alternatives unsuitable. Examples include:
-
High-reliability aerospace and defense electronics: These applications often involve extreme temperatures, vibration, and other harsh conditions that can compromise the reliability of lead-free solder joints.
-
Medical devices: Some medical devices, such as implantable pacemakers and defibrillators, may use lead-based solders due to their proven reliability and long-term stability.
-
Certain automotive electronics: While most automotive electronics have transitioned to lead-free soldering, some high-temperature or safety-critical applications may still use lead-based solders.
In these cases, manufacturers may need to obtain RoHS exemptions or use lead-based solders in compliance with other regulations, such as the End-of-Life Vehicles (ELV) directive.
Best Practices for Lead-based Soldering
When using lead-based solders, it is essential to follow best practices to minimize the environmental and health risks associated with lead exposure:
-
Use proper ventilation and fume extraction: Lead fumes can be harmful if inhaled, so it is crucial to use adequate ventilation and fume extraction systems when soldering with lead-based alloys.
-
Wear personal protective equipment (PPE): Workers should wear appropriate PPE, such as gloves, safety glasses, and respirators, to reduce the risk of lead exposure.
-
Properly dispose of lead-containing waste: Lead-containing solder waste, dross, and contaminated materials should be collected and disposed of in accordance with local regulations to prevent environmental contamination.
-
Train workers on lead safety: Employees who work with lead-based solders should receive training on the hazards of lead exposure and the proper handling and disposal of lead-containing materials.
-
Monitor lead exposure levels: Regular monitoring of lead exposure levels through air sampling and biological monitoring can help ensure that workers are not being exposed to excessive levels of lead.
Conclusion
Lead-based soldering has been a staple of the electronics industry for decades, offering reliable, low-cost, and easy-to-use solutions for joining metal components. However, growing concerns about the environmental and health impacts of lead have led to the development of lead-free alternatives and the implementation of regulations like the RoHS directive.
While lead-free solders have been successfully adopted in many applications, lead-based soldering remains important in certain high-reliability and specialized applications. When using lead-based solders, it is crucial to follow best practices to minimize the risks associated with lead exposure and ensure compliance with relevant regulations.
As the electronics industry continues to evolve, manufacturers will need to balance the performance requirements of their products with the need to reduce the environmental and health impacts of their processes and materials.
FAQ
-
Q: What is the most common lead-based solder alloy?
A: The most common lead-based solder alloy is Sn63Pb37, which consists of 63% tin (Sn) and 37% lead (Pb) by weight. This eutectic alloy has a melting point of 183°C (361°F). -
Q: What are the main advantages of lead-based solders compared to lead-free alternatives?
A: Lead-based solders have a lower melting point, better wetting properties, improved mechanical properties, and lower cost compared to most lead-free solders. -
Q: What is the RoHS directive, and how does it impact the use of lead-based solders?
A: The Restriction of Hazardous Substances (RoHS) directive is a set of regulations that limits the use of certain hazardous materials, including lead, in electronic and electrical equipment. Under RoHS, the maximum allowable concentration of lead in homogeneous materials is 0.1% by weight. -
Q: Are there still applications where lead-based soldering is used despite the RoHS directive?
A: Yes, there are some applications, such as high-reliability aerospace and defense electronics, medical devices, and certain automotive electronics, where lead-based solders may still be used due to performance requirements or harsh operating conditions. -
Q: What are some best practices for minimizing the risks associated with lead exposure when using lead-based solders?
A: Best practices include using proper ventilation and fume extraction, wearing personal protective equipment (PPE), properly disposing of lead-containing waste, training workers on lead safety, and monitoring lead exposure levels.
Property | Lead-based Solder (Sn63Pb37) | Lead-free Solder (SAC305) |
---|---|---|
Composition | 63% Sn, 37% Pb | 96.5% Sn, 3% Ag, 0.5% Cu |
Melting Point | 183°C (361°F) | 217-220°C (423-428°F) |
Wetting Properties | Excellent | Good |
Mechanical Properties | Very Good | Good |
Cost | Low | Higher |
Environmental Impact | High | Low |
Health Risks | High | Low |
RoHS Compliance | No | Yes |
0 Comments