The Need for IPC-2581 Standard
The electronics industry has long faced challenges in efficiently exchanging PCB design and manufacturing data due to the variety of proprietary formats used by different software tools and manufacturers. This lack of standardization often leads to errors, delays, and increased costs in the PCB manufacturing process. The IPC-2581 standard addresses these issues by providing a common language for data transfer, enabling seamless communication between all stakeholders involved in the PCB design and manufacturing process.
Benefits of Adopting IPC-2581
- Reduced errors and improved quality
- Faster time-to-market
- Lower manufacturing costs
- Enhanced collaboration between design and manufacturing teams
- Compatibility with a wide range of PCB design and manufacturing software tools
Key Features of IPC-2581
XML-based Format
IPC-2581 uses an XML-based format to represent PCB design and manufacturing data. XML (eXtensible Markup Language) is a widely adopted, human-readable, and machine-parsable format that allows for easy data exchange between different systems and software tools. The use of XML ensures that IPC-2581 data can be easily interpreted and processed by various PCB design and manufacturing software applications.
Comprehensive Data Representation
The IPC-2581 standard encompasses a wide range of PCB design and manufacturing data, including:
- Board layout and layer stackup information
- Component placement data
- Bill of Materials (BOM)
- Assembly instructions
- Test points and test coverage data
- Fabrication and assembly notes
By providing a comprehensive representation of PCB data, IPC-2581 eliminates the need for multiple file formats and ensures that all necessary information is communicated effectively between design and manufacturing teams.
Versioning and Change Management
IPC-2581 includes provisions for versioning and change management, allowing designers and manufacturers to track and manage revisions throughout the PCB design and manufacturing process. This feature is particularly important in ensuring that all stakeholders are working with the most up-to-date information and that changes are communicated effectively across the supply chain.
Integration with PCB Design and Manufacturing Software
Many leading PCB design and manufacturing software tools have incorporated support for the IPC-2581 standard, enabling users to easily import and export data in this format. Some of the software applications that support IPC-2581 include:
- Cadence Allegro
- Mentor Graphics PADS
- Altium Designer
- Zuken CR-8000
- Siemens NX PCB Exchange
The widespread adoption of IPC-2581 by software vendors has significantly contributed to the standard’s success and has made it easier for companies to implement IPC-2581 in their design and manufacturing workflows.
Implementing IPC-2581 in Your Organization
Assess Your Current Workflow
The first step in implementing IPC-2581 is to assess your current PCB design and manufacturing workflow. Identify the software tools and data formats used by your design and manufacturing teams, and evaluate the compatibility of these tools with the IPC-2581 standard. This assessment will help you determine the scope of the implementation and identify any potential challenges or gaps that need to be addressed.
Engage with Stakeholders
Engage with all stakeholders involved in the PCB design and manufacturing process, including designers, engineers, manufacturers, and suppliers. Communicate the benefits of adopting IPC-2581 and seek their input and support in the implementation process. Collaboration and buy-in from all stakeholders are essential for a successful IPC-2581 implementation.
Develop an Implementation Plan
Based on your workflow assessment and stakeholder input, develop a detailed implementation plan that outlines the steps required to adopt IPC-2581 in your organization. This plan should include:
- Training and education for design and manufacturing teams
- Software tool upgrades or migrations, if necessary
- Process changes to incorporate IPC-2581 data exchange
- Pilot projects to test and validate the implementation
- Metrics to measure the success of the implementation
Execute and Monitor
Execute your implementation plan, providing support and resources to your teams as they transition to using IPC-2581. Regularly monitor the progress of the implementation and track the metrics defined in your plan. Address any issues or challenges that arise promptly, and celebrate successes along the way.
Continuously Improve
Implementing IPC-2581 is not a one-time event, but rather an ongoing process of continuous improvement. Regularly review your IPC-2581 workflow, seek feedback from your teams, and identify opportunities for further optimization. Stay updated on the latest developments in the IPC-2581 standard and incorporate relevant updates and improvements into your workflow as they become available.
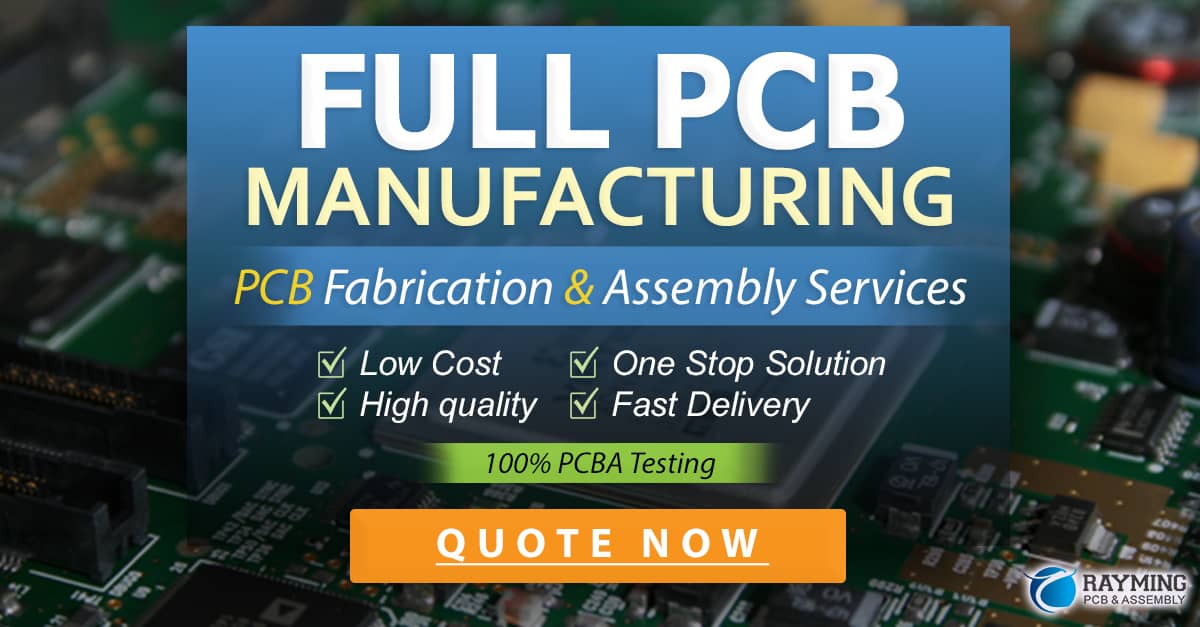
Case Studies
Company A: Streamlining Design-to-Manufacturing Handoff
Company A, a leading electronics manufacturer, faced significant challenges in the handoff of PCB design data to their manufacturing team. The use of multiple proprietary formats led to errors, delays, and increased costs. By implementing IPC-2581, Company A was able to streamline their design-to-manufacturing handoff process, reducing errors by 80% and cutting time-to-market by 25%.
Company B: Enhancing Collaboration with Suppliers
Company B, an automotive electronics supplier, struggled with effective collaboration with their PCB fabrication and assembly partners due to the lack of a standardized data exchange format. By adopting IPC-2581, Company B was able to enhance collaboration with their suppliers, resulting in fewer miscommunications, improved quality, and a 15% reduction in manufacturing costs.
Frequently Asked Questions (FAQ)
-
Q: Is IPC-2581 compatible with my existing PCB design software?
A: Many leading PCB design software tools, such as Cadence Allegro, Mentor Graphics PADS, and Altium Designer, support the IPC-2581 standard. Check with your software vendor to confirm compatibility and determine if any upgrades or add-ons are required. -
Q: How does IPC-2581 compare to other PCB data exchange formats like ODB++?
A: IPC-2581 and ODB++ are both industry-standard formats for PCB data exchange. While ODB++ is widely adopted, IPC-2581 offers a more comprehensive and up-to-date representation of PCB data, including support for newer technologies and design features. Additionally, IPC-2581 is an open standard, which promotes wider adoption and interoperability. -
Q: Can IPC-2581 be used for both rigid and flexible PCBs?
A: Yes, IPC-2581 supports both rigid and flexible PCB designs, as well as rigid-flex combinations. The standard includes provisions for representing the unique characteristics and requirements of flexible PCBs, such as bend regions and material properties. -
Q: How long does it typically take to implement IPC-2581 in an organization?
A: The implementation timeline for IPC-2581 varies depending on the size and complexity of your organization, as well as the current state of your PCB design and manufacturing workflow. A typical implementation can take anywhere from a few weeks to several months, depending on factors such as the number of stakeholders involved, the extent of software tool updates required, and the need for process changes. -
Q: What resources are available to help with IPC-2581 implementation?
A: IPC provides a range of resources to support the adoption and implementation of IPC-2581, including: - IPC-2581 specification documents and guidelines
- Training and certification programs
- User forums and discussion groups
- Case studies and best practices from successful implementations
Additionally, many PCB design and manufacturing software vendors offer support, training, and consulting services to help organizations implement IPC-2581 effectively.
Conclusion
IPC-2581 is a powerful and comprehensive standard for the exchange of PCB design and manufacturing data. By providing a unified, XML-based format for data representation, IPC-2581 enables seamless communication between PCB designers, manufacturers, and assemblers, leading to reduced errors, improved quality, and faster time-to-market.
Implementing IPC-2581 in your organization requires careful planning, stakeholder engagement, and a commitment to continuous improvement. However, the benefits of adoption are clear, as demonstrated by the success stories of companies that have embraced this standard.
As the electronics industry continues to evolve and new technologies emerge, the importance of effective data exchange and collaboration will only continue to grow. By adopting IPC-2581, your organization can position itself for success in this dynamic and competitive landscape, ensuring that your PCB design and manufacturing processes are efficient, accurate, and adaptable to future challenges.
0 Comments