How HASL Surface Finish is Applied
The HASL process consists of several steps to ensure a high-quality surface finish:
-
PCB Preparation: The PCB undergoes a cleaning process to remove any contaminants or oxides from the copper surface. This step is crucial for achieving a uniform and adherent solder coating.
-
Fluxing: A thin layer of flux is applied to the exposed copper pads to improve the wetting and spreading of the molten solder. The flux also helps to remove any remaining oxides and prevents oxidation during the soldering process.
-
Solder Dipping: The PCB is dipped into a molten solder bath, typically consisting of a tin-lead alloy (e.g., Sn63/Pb37). The solder bath temperature is maintained at around 240-260°C (464-500°F) to ensure proper wetting and coverage of the copper pads.
-
Hot Air Leveling: Immediately after the solder dipping, the PCB is subjected to a stream of hot air. The hot air helps to remove the excess solder from the pads, leaving a thin, uniform layer of solder. This process also levels the solder surface, ensuring a flat and smooth finish.
-
Cooling: The PCB is then cooled to room temperature, allowing the solder to solidify and form a strong bond with the copper pads.
Advantages of HASL Surface Finish
HASL offers several advantages that make it a popular choice for PCB surface finishes:
-
Cost-effectiveness: HASL is one of the most economical surface finish options available, making it suitable for high-volume production and cost-sensitive applications.
-
Excellent solderability: The solder coating provided by HASL ensures excellent solderability, enabling reliable and robust solder joints during the assembly process.
-
Compatibility: HASL is compatible with a wide range of soldering processes, including wave soldering, reflow soldering, and hand soldering.
-
Reworkability: PCBs with HASL surface finish can be easily reworked or repaired, as the solder can be melted and reshaped without compromising the integrity of the copper pads.
-
Shelf life: HASL-finished PCBs have a relatively long shelf life, as the solder coating protects the copper pads from oxidation and contamination.
Limitations of HASL Surface Finish
Despite its advantages, HASL also has some limitations that should be considered:
-
Flatness and coplanarity: The hot air leveling process may not achieve perfect flatness and coplanarity across all pads, especially for fine-pitch components. This can lead to challenges in component placement and soldering.
-
Thermal shock: The rapid temperature changes during the solder dipping and hot air leveling process can cause thermal shock to the PCB, potentially leading to warpage or delamination in some cases.
-
Solder thickness variation: The thickness of the solder coating may vary across different pads, depending on factors such as pad size, shape, and location. This can affect the consistency of the solder joints during assembly.
-
Environmental concerns: Traditional HASL processes use lead-based solder alloys, which pose environmental and health risks. Lead-free HASL alternatives, such as Sn99.3/Cu0.7 or Sn96.5/Ag3.0/Cu0.5, are available but may require process adjustments and higher operating temperatures.
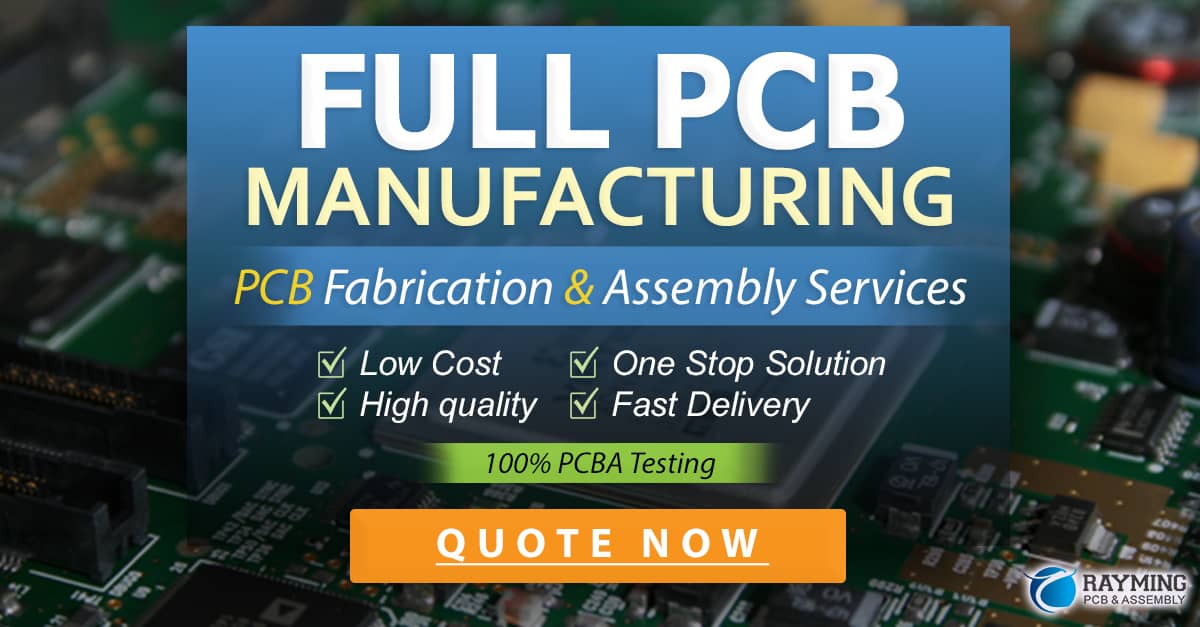
Comparison with Other Surface Finishes
HASL is one of several surface finish options available for PCBs. Here’s a comparison of HASL with some other common surface finishes:
Surface Finish | Advantages | Disadvantages |
---|---|---|
HASL | – Cost-effective – Excellent solderability – Compatible with various soldering processes |
– Potential flatness and coplanarity issues – Thermal shock concerns – Solder thickness variation |
ENIG (Electroless Nickel Immersion Gold) | – Excellent flatness and coplanarity – Good shelf life – Suitable for fine-pitch components |
– Higher cost compared to HASL – Potential for “black pad” defects – Harder to rework or repair |
OSP (Organic Solderability Preservative) | – Cost-effective – Flat surface finish – Environmentally friendly |
– Limited shelf life – Potential for poor solderability if not properly stored – Not suitable for multiple reflow cycles |
Immersion Silver | – Good solderability – Flat surface finish – Environmentally friendly |
– Higher cost compared to HASL – Potential for tarnishing over time – Not suitable for high-sulfur environments |
The choice of surface finish depends on various factors, such as the specific application requirements, component types, soldering processes, cost constraints, and environmental considerations.
Frequently Asked Questions (FAQ)
-
Q: Is HASL suitable for fine-pitch components?
A: While HASL can be used for fine-pitch components, it may not provide the same level of flatness and coplanarity as other surface finishes like ENIG or OSP. This can potentially lead to challenges in component placement and soldering. -
Q: Can HASL-finished PCBs be reworked or repaired?
A: Yes, HASL-finished PCBs can be easily reworked or repaired. The solder coating can be melted and reshaped without damaging the underlying copper pads, making it a suitable choice for applications that may require occasional repairs or modifications. -
Q: Are there lead-free alternatives to traditional HASL?
A: Yes, there are lead-free HASL alternatives available, such as Sn99.3/Cu0.7 or Sn96.5/Ag3.0/Cu0.5. These lead-free solder alloys provide similar benefits to traditional HASL but may require process adjustments and higher operating temperatures. -
Q: How does the shelf life of HASL compare to other surface finishes?
A: HASL-finished PCBs have a relatively long shelf life compared to some other surface finishes like OSP. The solder coating helps to protect the copper pads from oxidation and contamination, ensuring good solderability even after extended storage periods. -
Q: What are the environmental concerns associated with HASL?
A: Traditional HASL processes use lead-based solder alloys, which pose environmental and health risks. Lead is a toxic substance that can have harmful effects on human health and the environment. As a result, there has been a growing trend towards lead-free HASL alternatives and other environmentally friendly surface finishes.
Conclusion
Hot Air Solder Leveling (HASL) is a widely used and cost-effective surface finish technique for PCBs. It offers excellent solderability, compatibility with various soldering processes, and good shelf life. However, it also has some limitations, such as potential flatness and coplanarity issues, thermal shock concerns, and solder thickness variation.
When choosing a surface finish for a PCB, it is essential to consider the specific requirements of the application, including the component types, soldering processes, cost constraints, and environmental considerations. While HASL remains a popular choice for many applications, other surface finishes like ENIG, OSP, and Immersion Silver may be more suitable in certain cases.
As the electronics industry continues to evolve, there is a growing emphasis on lead-free and environmentally friendly surface finishes. Lead-free HASL alternatives and other green surface finishes are becoming increasingly popular, addressing the environmental concerns associated with traditional HASL processes.
Overall, HASL has proven to be a reliable and cost-effective surface finish option for PCBs, and it is likely to remain a common choice in the industry for the foreseeable future. However, as with any manufacturing process, it is important to weigh the advantages and limitations of HASL against the specific needs of the application to ensure the best possible results.
0 Comments