What are Halogens and Why are They Used in Solder Paste?
Halogens are a group of chemical elements that include fluorine (F), chlorine (Cl), bromine (Br), iodine (I), and astatine (At). These elements are highly reactive and have similar chemical properties. In the context of solder paste, halogens, particularly chlorine and bromine, have been used as activators to improve the soldering process and enhance the reliability of solder joints.
Traditionally, solder paste formulations have included halogenated compounds for several reasons:
-
Improved wetting: Halogens help to remove oxides from the surface of the metal, allowing the solder to wet the surface more effectively and form a strong bond.
-
Enhanced flux activity: Halogenated compounds act as activators in the flux, promoting better solder flow and reducing the formation of voids or other defects in the solder joint.
-
Increased shelf life: Halogen-containing fluxes have a longer shelf life compared to halogen-free alternatives, as they are less susceptible to degradation over time.
However, despite these benefits, the use of halogens in solder paste has come under scrutiny due to potential environmental and health risks.
Concerns with Halogenated Solder Paste
The primary concerns with halogenated solder paste are related to the environmental and health impacts of halogen compounds.
Environmental Concerns
When electronic products containing halogenated materials are disposed of improperly, the halogens can be released into the environment. These compounds can persist in the ecosystem and accumulate in the food chain, potentially harming wildlife and contaminating water sources.
Moreover, when halogenated materials are incinerated, they can release toxic substances, such as dioxins and furans, which are known to have adverse effects on human health and the environment.
Health Concerns
Exposure to halogenated compounds has been linked to various health issues, including:
-
Respiratory problems: Inhaling fumes from halogenated solder paste during the soldering process can irritate the respiratory system and cause breathing difficulties.
-
Skin irritation: Direct contact with halogenated solder paste can cause skin irritation and allergic reactions in some individuals.
-
Long-term health effects: Prolonged exposure to halogenated compounds has been associated with an increased risk of certain cancers, developmental disorders, and hormonal disruptions.
Due to these concerns, there has been a growing demand for Halogen-Free Solder Paste alternatives that can provide similar performance without the associated environmental and health risks.
Advantages of Halogen-Free Solder Paste
Halogen-free solder paste offers several advantages over traditional halogenated formulations:
-
Reduced environmental impact: By eliminating halogens from the solder paste, the risk of releasing toxic substances into the environment during disposal or incineration is minimized.
-
Improved health and safety: Halogen-free solder paste reduces the potential for respiratory irritation and skin sensitization during the soldering process, creating a safer working environment for employees.
-
Compliance with regulations: Many countries and regions have implemented regulations restricting the use of halogenated materials in electronic products. Using halogen-free solder paste helps manufacturers comply with these regulations and avoid potential legal and financial consequences.
-
Enhanced product marketability: As consumers become more environmentally conscious, products that are manufactured using halogen-free materials may have a competitive advantage in the market.
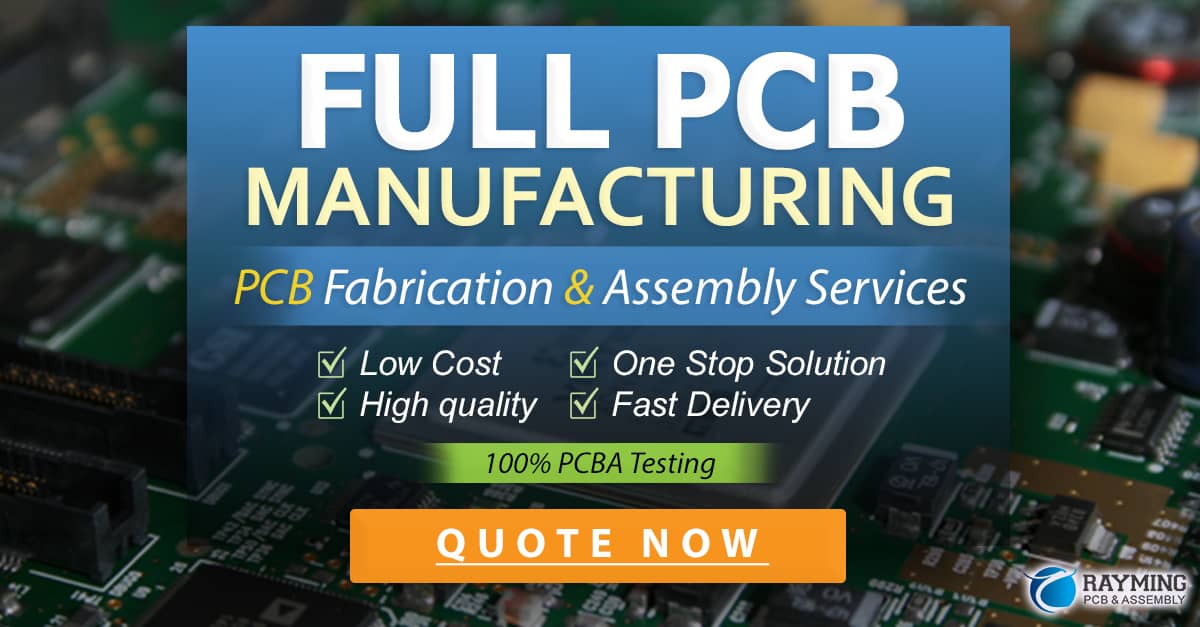
Challenges with Halogen-Free Solder Paste
While halogen-free solder paste offers several benefits, there are also some challenges associated with its use:
-
Performance limitations: Halogen-free fluxes may not provide the same level of wetting and flux activity as their halogenated counterparts, which can lead to issues such as poor solder joint formation or increased void formation.
-
Narrower process windows: Halogen-free solder paste formulations often have narrower process windows compared to halogenated alternatives, requiring more precise control over soldering parameters such as temperature and time.
-
Compatibility issues: Some halogen-free solder pastes may not be compatible with certain surface finishes or substrates, requiring manufacturers to carefully select and test materials to ensure reliable soldering results.
-
Higher cost: Halogen-free solder paste formulations may be more expensive than traditional halogenated alternatives due to the specialized chemistry and materials required to achieve similar performance levels.
Despite these challenges, ongoing research and development efforts have led to significant improvements in the performance and reliability of halogen-free solder paste formulations.
Choosing the Right Halogen-Free Solder Paste
When selecting a halogen-free solder paste for a specific application, several factors should be considered:
-
Alloy composition: Halogen-free solder pastes are available in various alloy compositions, such as SnAgCu (SAC) and SnCu. The choice of alloy will depend on the specific requirements of the application, including temperature cycling, mechanical stress, and environmental conditions.
-
Flux type: Halogen-free fluxes can be categorized as rosin-based, resin-based, or water-soluble. Each flux type has its own advantages and disadvantages in terms of wetting, residue cleaning, and compatibility with different surface finishes.
-
Particle size: Solder paste is available in different particle sizes, ranging from Type 1 (smallest) to Type 6 (largest). The choice of particle size will depend on the pitch and size of the components being soldered, as well as the desired print definition and solder joint profile.
-
Printing and reflow profiles: Halogen-free solder pastes may require different printing and reflow profiles compared to halogenated alternatives. It is important to work closely with the solder paste manufacturer to develop optimized process parameters that ensure reliable soldering results.
-
Compatibility with cleaning processes: If post-soldering cleaning is required, it is essential to ensure that the chosen halogen-free solder paste is compatible with the cleaning process and equipment being used.
The table below summarizes some of the key considerations when choosing a halogen-free solder paste:
Factor | Considerations |
---|---|
Alloy composition | – SnAgCu (SAC) – SnCu – Other lead-free alloys |
Flux type | – Rosin-based – Resin-based – Water-soluble |
Particle size | – Type 1 (smallest) – Type 2 – Type 3 – Type 4 – Type 5 – Type 6 (largest) |
Printing and reflow profiles | – Optimized parameters for halogen-free formulation – Consult with solder paste manufacturer |
Compatibility with cleaning processes | – Ensure compatibility with cleaning process and equipment |
By carefully considering these factors and working closely with solder paste manufacturers and equipment suppliers, manufacturers can successfully implement halogen-free solder paste in their production processes.
Frequently Asked Questions (FAQ)
-
Q: Are halogen-free solder pastes RoHS compliant?
A: Yes, halogen-free solder pastes are designed to be compliant with the Restriction of Hazardous Substances (RoHS) directive, which limits the use of certain hazardous substances, including halogens, in electronic products. -
Q: Can halogen-free solder pastes be used for both wave soldering and reflow soldering?
A: Yes, halogen-free solder pastes are available for both wave soldering and reflow soldering applications. However, the specific formulation and process parameters may differ between the two soldering methods. -
Q: Do halogen-free solder pastes require special storage conditions?
A: Halogen-free solder pastes generally have similar storage requirements to halogenated alternatives. They should be stored in a cool, dry place and used within the manufacturer’s recommended shelf life. However, some halogen-free formulations may be more sensitive to humidity and may require additional storage precautions. -
Q: Are halogen-free solder pastes more expensive than traditional halogenated formulations?
A: In general, halogen-free solder pastes may be more expensive than traditional halogenated alternatives due to the specialized chemistry and materials required to achieve similar performance levels. However, the cost difference can vary depending on the specific formulation and supplier. -
Q: Can halogen-free solder pastes be used for high-reliability applications, such as aerospace or medical devices?
A: Yes, halogen-free solder pastes can be used for high-reliability applications, provided that they meet the specific performance and reliability requirements of the industry. Many halogen-free formulations have been developed and tested to ensure they can withstand the demands of these critical applications.
In conclusion, halogen-free solder paste is an increasingly popular alternative to traditional halogenated formulations, offering reduced environmental impact, improved health and safety, and compliance with regulatory requirements. While there are still some challenges associated with the use of halogen-free solder paste, ongoing research and development efforts have led to significant improvements in performance and reliability. By carefully considering factors such as alloy composition, flux type, particle size, and compatibility with cleaning processes, manufacturers can successfully implement halogen-free solder paste in their production processes and meet the growing demand for environmentally friendly and safe electronic products.
0 Comments