Introduction to Halogen-free PCBs
Printed Circuit Boards (PCBs) are essential components in modern electronics, providing a platform for interconnecting various electronic components. As technology advances and environmental concerns grow, the demand for safer and more Eco-Friendly PCBs has increased. One such development is the introduction of halogen-free PCBs, which have gained popularity due to their reduced environmental impact and improved safety features.
What are Halogens?
Halogens are a group of chemical elements that include fluorine (F), chlorine (Cl), bromine (Br), iodine (I), and astatine (At). In the context of PCBs, the most commonly used halogens are chlorine and bromine, which are often found in the form of flame retardants.
The Need for Halogen-Free PCBs
Traditionally, PCBs have been manufactured using materials that contain halogens, particularly brominated flame retardants (BFRs). These substances are added to PCBs to improve their fire resistance and prevent the spread of flames in case of a fire. However, the use of halogens in PCBs has raised several concerns:
-
Environmental Impact: When halogen-containing PCBs are disposed of improperly or end up in landfills, the halogens can leach into the soil and groundwater, causing environmental contamination.
-
Health Risks: Exposure to halogens, especially through inhalation of fumes during PCB manufacturing or when PCBs are subjected to high temperatures, can pose health risks to workers and users.
-
Toxic Smoke: In the event of a fire, halogen-containing PCBs can release toxic smoke containing dioxins and furans, which are highly harmful to human health and the environment.
To address these concerns, the electronics industry has been moving towards the adoption of halogen-free PCBs.
Characteristics of Halogen-Free PCBs
Definition of Halogen-Free
A PCB is considered halogen-free when it meets the following criteria:
- The total halogen content in the PCB material is below 900 ppm (parts per million).
- The chlorine content is below 900 ppm.
- The bromine content is below 900 ppm.
These limits are based on the IEC 61249-2-21 standard, which defines the requirements for halogen-free PCBs.
Materials Used in Halogen-Free PCBs
Halogen-free PCBs are manufactured using alternative materials that do not contain halogens. Some commonly used halogen-free materials include:
-
Polyethylene Terephthalate (PET): PET is a thermoplastic polymer that offers good electrical properties, dimensional stability, and heat resistance.
-
Polyphenylene Oxide (PPO): PPO is a high-performance thermoplastic with excellent electrical insulation properties and good mechanical strength.
-
Polyethylene Naphthalate (PEN): PEN is a polyester material that provides superior thermal and mechanical properties compared to PET.
-
Polyimide (PI): PI is a high-temperature resistant polymer with excellent electrical insulation properties and dimensional stability.
These materials are used in combination with halogen-free flame retardants, such as metal hydroxides (aluminum hydroxide or magnesium hydroxide) or phosphorus-based compounds, to achieve the desired fire resistance properties.
Advantages of Halogen-Free PCBs
Halogen-free PCBs offer several advantages over their halogen-containing counterparts:
-
Reduced Environmental Impact: By eliminating halogens, halogen-free PCBs minimize the risk of environmental contamination during disposal or recycling.
-
Improved Safety: Halogen-free PCBs reduce the potential health risks associated with exposure to halogens during manufacturing and use.
-
Lower Toxicity in Case of Fire: In the event of a fire, halogen-free PCBs release less toxic smoke, minimizing the harm to human health and the environment.
-
Compliance with Regulations: Halogen-free PCBs help manufacturers comply with various environmental regulations and directives, such as RoHS (Restriction of Hazardous Substances) and WEEE (Waste Electrical and Electronic Equipment).
-
Improved Reliability: Some halogen-free materials, such as polyimide, offer better thermal and mechanical properties, enhancing the overall reliability of the PCB.
Applications of Halogen-Free PCBs
Halogen-free PCBs find applications in various industries and products where environmental friendliness, safety, and reliability are of utmost importance. Some common applications include:
-
Consumer Electronics: Smartphones, tablets, laptops, and other consumer devices often use halogen-free PCBs to meet environmental regulations and enhance product safety.
-
Automotive Electronics: With the increasing focus on vehicle safety and sustainability, halogen-free PCBs are being used in automotive electronics, such as engine control units, infotainment systems, and advanced driver assistance systems (ADAS).
-
Medical Devices: Halogen-free PCBs are preferred in medical devices to ensure patient safety and minimize the risk of toxic emissions during use or in case of a fire.
-
Industrial Equipment: Industrial control systems, power electronics, and other industrial applications benefit from the use of halogen-free PCBs, as they offer improved reliability and reduced environmental impact.
-
Aerospace and Defense: Halogen-free PCBs are used in aerospace and defense applications, where high reliability and safety are critical factors.
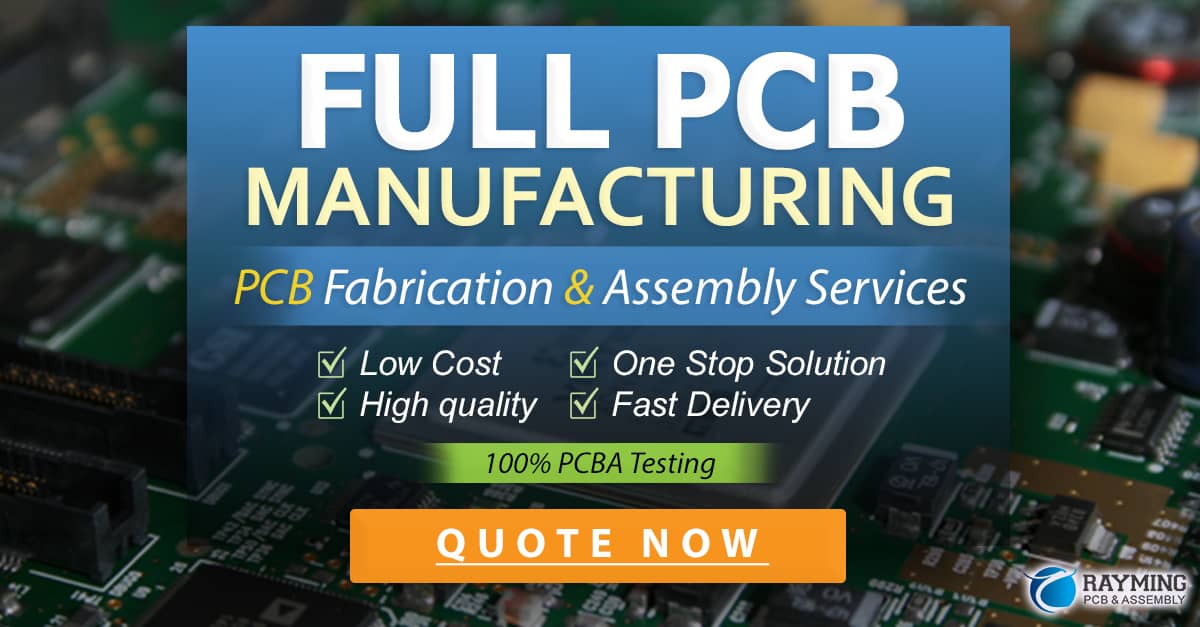
Challenges and Considerations
While halogen-free PCBs offer numerous benefits, there are some challenges and considerations to keep in mind:
-
Cost: Halogen-free materials and manufacturing processes may be more expensive compared to traditional halogen-containing PCBs. However, the long-term benefits of using halogen-free PCBs often outweigh the initial cost difference.
-
Material Availability: The availability of halogen-free materials may be limited compared to traditional PCB Materials. This can impact lead times and production schedules.
-
Manufacturing Process Adjustments: Transitioning to halogen-free PCBs may require adjustments to the manufacturing process, such as changes in lamination parameters or soldering temperatures, to accommodate the different material properties.
-
Compatibility with Existing Designs: When switching to halogen-free PCBs, it is important to evaluate the compatibility of the new materials with existing PCB Designs and components. In some cases, minor design modifications may be necessary to ensure optimal performance.
Frequently Asked Questions (FAQ)
-
Q: Are halogen-free PCBs more expensive than traditional PCBs?
A: Yes, halogen-free PCBs may have a higher initial cost due to the specialized materials and manufacturing processes involved. However, the long-term benefits, such as reduced environmental impact and improved safety, often justify the additional cost. -
Q: Can halogen-free PCBs be used in high-temperature applications?
A: Yes, some halogen-free materials, such as polyimide (PI), offer excellent high-temperature resistance and can be used in applications that require operation at elevated temperatures. -
Q: Are halogen-free PCBs compliant with RoHS and WEEE directives?
A: Yes, halogen-free PCBs are designed to meet the requirements of RoHS (Restriction of Hazardous Substances) and WEEE (Waste Electrical and Electronic Equipment) directives, which aim to reduce the use of hazardous substances in electronic products. -
Q: Can halogen-free PCBs be recycled?
A: Yes, halogen-free PCBs are more environmentally friendly and can be recycled more easily compared to halogen-containing PCBs. The absence of halogens reduces the risk of contamination during the recycling process. -
Q: Are there any performance differences between halogen-free and traditional PCBs?
A: In general, halogen-free PCBs can offer similar or even better performance compared to traditional PCBs. Some halogen-free materials, such as polyimide, provide enhanced thermal and mechanical properties, which can improve the overall reliability of the PCB.
Conclusion
Halogen-free PCBs represent a significant step towards more environmentally friendly and safer Electronics Manufacturing. By eliminating the use of halogens, these PCBs reduce the risk of environmental contamination, improve safety for workers and users, and minimize the release of toxic substances in case of a fire. While there may be some challenges and considerations associated with transitioning to halogen-free PCBs, the long-term benefits make them an attractive choice for a wide range of applications.
As environmental regulations become more stringent and consumers increasingly demand eco-friendly products, the adoption of halogen-free PCBs is expected to grow further. By embracing this technology, manufacturers can contribute to a more sustainable future while ensuring the production of reliable and safe electronic devices.
0 Comments