What is EMI?
EMI refers to the unwanted effects of electromagnetic radiation on electronic devices. It can be generated by both natural sources, such as solar flares and lightning, and man-made sources, including power lines, motors, and other electronic devices. EMI can be categorized into two main types:
- Conducted EMI: Interference transmitted through physical connections, such as cables and wires.
- Radiated EMI: Interference transmitted through the air as electromagnetic waves.
Both types of EMI can cause problems in electronic devices, such as signal distortion, data corruption, and system malfunctions.
The Importance of EMI Shielding in Flexible PCBs
Flexible PCBs are designed to bend and twist, allowing for more compact and versatile electronic devices. However, this flexibility also makes them more susceptible to EMI. The close proximity of components and the lack of a rigid structure can lead to increased coupling of electromagnetic fields, resulting in higher levels of interference.
EMI shielding is essential in flexible PCBs to:
- Protect sensitive components from external EMI sources
- Prevent the PCB from generating EMI that could affect other devices
- Ensure compliance with EMC regulations, such as the FCC rules in the United States and the CE marking in the European Union
Without proper EMI shielding, flexible PCBs may experience performance issues, reduced reliability, and potential non-compliance with industry standards.
EMI Shielding Techniques for Flexible PCBs
Several techniques can be employed to provide EMI shielding in flexible PCBs. The choice of method depends on factors such as the level of shielding required, the operating frequency range, and the physical constraints of the design.
Conductive Coatings
One common approach to EMI shielding in flexible PCBs is the use of conductive coatings. These coatings are applied to the surface of the PCB and create a barrier that attenuates electromagnetic waves. Some popular conductive coatings include:
- Nickel-based coatings: These offer good shielding effectiveness and durability but may be more expensive than other options.
- Copper-based coatings: Copper provides excellent conductivity and shielding performance but may be prone to oxidation over time.
- Silver-based coatings: Silver has the highest conductivity among metals and offers excellent shielding effectiveness, but it is also the most expensive option.
Conductive coatings can be applied using various methods, such as electroless plating, electrolytic plating, and spraying. The choice of application method depends on the specific requirements of the design and the manufacturing process.
Conductive Adhesives
Another approach to EMI shielding in flexible PCBs is the use of conductive adhesives. These adhesives contain conductive particles, such as silver or nickel, that create a shielding layer when applied to the PCB. Conductive adhesives offer several advantages:
- They can be applied selectively to specific areas of the PCB, allowing for more targeted shielding.
- They can provide a strong bond between the shielding layer and the PCB, improving durability.
- They can be used to attach additional shielding components, such as conductive fabrics or foils.
However, conductive adhesives may have lower shielding effectiveness compared to conductive coatings and may be more susceptible to degradation over time.
Shielding Fabrics and Tapes
Conductive fabrics and tapes can be used to provide additional EMI shielding in flexible PCBs. These materials are typically made from woven or non-woven fibers that are coated with conductive materials, such as nickel, copper, or silver. They can be applied to the surface of the PCB or used to create shielding enclosures around specific components.
Shielding fabrics and tapes offer several benefits:
- They are highly flexible and can conform to the shape of the PCB, making them ideal for use in bendable and stretchable designs.
- They can be easily cut and shaped to fit specific areas of the PCB.
- They can be attached using conductive adhesives or mechanical fasteners, allowing for easy integration into the manufacturing process.
However, shielding fabrics and tapes may have lower shielding effectiveness compared to conductive coatings and may be more susceptible to wear and tear over time.
Grounding and Shielding Techniques
In addition to the use of conductive materials, proper grounding and shielding techniques are essential for effective EMI shielding in flexible PCBs. Some key considerations include:
- Proper grounding of the shielding layer: The shielding layer should be electrically connected to the ground plane of the PCB to provide a low-impedance path for electromagnetic currents.
- Use of shielding vias: Vias can be used to create a conductive path between the shielding layer and the ground plane, improving the overall shielding effectiveness.
- Minimizing gaps and openings: Gaps and openings in the shielding layer can allow electromagnetic waves to leak through, reducing the overall shielding effectiveness. Care should be taken to minimize these discontinuities in the design.
- Proper termination of shielded cables: When using shielded cables in conjunction with flexible PCBs, it is important to ensure that the cable shield is properly terminated to the PCB shielding layer to maintain shielding continuity.
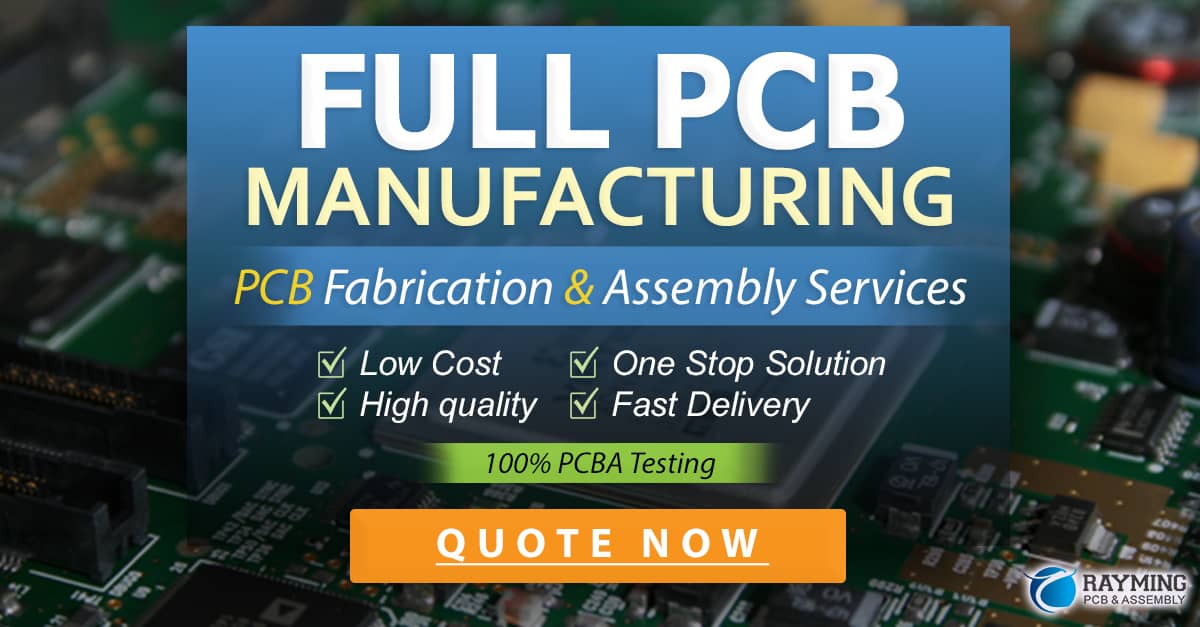
Evaluating EMI Shielding Performance
To ensure that a flexible PCB meets the required EMI shielding performance, it is necessary to conduct EMC testing. This typically involves measuring the electromagnetic emissions from the PCB and comparing them to the relevant EMC standards. Some common EMC testing methods include:
- Radiated emissions testing: This measures the electromagnetic fields emitted by the PCB using an antenna and spectrum analyzer.
- Conducted emissions testing: This measures the electromagnetic interference conducted through the power and signal lines of the PCB using a line impedance stabilization network (LISN) and spectrum analyzer.
- Immunity testing: This evaluates the ability of the PCB to function properly in the presence of external electromagnetic fields, using a signal generator and power amplifier to inject interference into the system.
The specific EMC testing requirements will depend on the intended application and the relevant industry standards. It is important to work with an experienced EMC testing lab to ensure that the testing is conducted properly and that the results are interpreted correctly.
EMI Shielding Materials and Their Properties
When selecting materials for EMI shielding in flexible PCBs, it is important to consider their electrical, mechanical, and thermal properties. Some key properties to consider include:
-
Conductivity: The shielding material should have high electrical conductivity to provide effective attenuation of electromagnetic waves. Materials with higher conductivity, such as silver and copper, generally offer better shielding performance.
-
Permeability: The magnetic permeability of the shielding material determines its ability to absorb and redirect magnetic fields. Materials with high permeability, such as nickel and mu-metal, are particularly effective at shielding low-frequency magnetic fields.
-
Flexibility: The shielding material should be able to flex and bend without cracking or losing its shielding properties. This is especially important in flexible PCB applications where the board may be subjected to repeated bending and flexing.
-
Adhesion: The shielding material should have good adhesion to the PCB substrate to ensure reliable performance over the life of the product. Poor adhesion can lead to delamination and loss of shielding effectiveness.
-
Thermal stability: The shielding material should be able to withstand the thermal stresses encountered during the manufacturing process and in the end-use environment. This includes resistance to high temperatures during soldering and the ability to withstand thermal cycling without degradation.
Some common EMI shielding materials and their properties are summarized in the table below:
Material | Conductivity | Permeability | Flexibility | Adhesion | Thermal Stability |
---|---|---|---|---|---|
Silver | Excellent | Low | Good | Good | Good |
Copper | Excellent | Low | Good | Good | Good |
Nickel | Good | High | Good | Good | Good |
Aluminum | Good | Low | Good | Fair | Fair |
Mu-metal | Fair | Very High | Fair | Fair | Fair |
The choice of shielding material will depend on the specific requirements of the application, including the frequency range of concern, the level of shielding effectiveness required, and the mechanical and environmental constraints of the design.
Design Considerations for EMI Shielding in Flexible PCBs
When designing flexible PCBs with EMI shielding, several key factors should be considered to ensure optimal performance and manufacturability:
-
Shielding coverage: The shielding layer should provide adequate coverage of the sensitive components and traces on the PCB. This may require the use of multiple shielding layers or the incorporation of shielding vias to create a continuous shielding barrier.
-
Grounding strategy: The shielding layer should be properly grounded to the PCB ground plane to provide a low-impedance path for electromagnetic currents. This may involve the use of multiple ground connections or the incorporation of ground vias to ensure a robust ground network.
-
Flexibility requirements: The shielding design should take into account the flexibility requirements of the PCB. This may involve the use of flexible shielding materials, such as conductive fabrics or elastomeric composites, or the incorporation of strain relief features to minimize stress on the shielding layer during flexing.
-
Manufacturing process: The shielding design should be compatible with the intended manufacturing process, including the PCB fabrication, assembly, and testing steps. This may involve the selection of shielding materials and application methods that are suitable for the specific process flow and the consideration of any potential manufacturing challenges, such as adhesion or compatibility issues.
-
Cost and reliability: The shielding design should balance the cost and reliability requirements of the application. This may involve the selection of cost-effective shielding materials and processes that still provide adequate shielding performance and long-term reliability.
By carefully considering these design factors and working closely with the PCB fabricator and assembly partner, designers can create flexible PCBs with effective EMI shielding that meet the performance, reliability, and cost requirements of the application.
Frequently Asked Questions (FAQ)
-
What is the difference between EMI and EMC?
EMI (electromagnetic interference) refers to the unwanted effects of electromagnetic radiation on electronic devices, while EMC (electromagnetic compatibility) refers to the ability of a device to function properly in its intended electromagnetic environment without causing interference to other devices. -
Can EMI shielding be added to an existing flexible PCB design?
Yes, EMI shielding can be added to an existing flexible PCB design, but it may require some modifications to the layout and manufacturing process. It is generally easier and more cost-effective to incorporate EMI shielding from the beginning of the design process. -
How do I select the right EMI shielding material for my application?
The selection of the right EMI shielding material depends on several factors, including the frequency range of concern, the level of shielding effectiveness required, and the mechanical and environmental constraints of the design. It is important to work with an experienced EMI shielding supplier or consultant to evaluate the options and select the best material for the specific application. -
How much does EMI shielding add to the cost of a flexible PCB?
The cost of EMI shielding in a flexible PCB depends on several factors, including the shielding material, the application method, and the size and complexity of the PCB design. In general, adding EMI shielding will increase the overall cost of the PCB, but the exact amount will vary depending on the specific requirements of the application. -
Can EMI shielding be used in medical devices?
Yes, EMI shielding is commonly used in medical devices to ensure proper functioning and patient safety. However, medical devices have additional regulatory requirements and testing standards that must be met, so it is important to work with an experienced medical device EMI shielding supplier and to follow the relevant FDA and ISO guidelines.
0 Comments