Causes of Creep Corrosion
Several factors can contribute to the development of creep corrosion in PCBs:
Humidity and Temperature
High humidity levels and elevated temperatures can accelerate the process of creep corrosion. When moisture is present on the surface of a PCB, it can create an electrolytic solution that allows ions to move between conductive materials. This movement of ions is the primary mechanism behind creep corrosion.
Voltage Gradient
The presence of a voltage gradient between two conductive materials on a PCB can drive the migration of ions from one location to another. This gradient can be caused by differences in the electrical potential of various components or by the presence of stray currents on the board.
Contamination
Contaminants on the surface of a PCB, such as flux residues, dust, or salts, can contribute to the formation of an electrolytic solution and promote the migration of ions. These contaminants can come from various sources, including the manufacturing process, the environment, or improper handling and storage of the PCBs.
Material Properties
The properties of the conductive materials used in PCBs can also influence the likelihood of creep corrosion. Some materials, such as silver, are more susceptible to ion migration than others. Additionally, the spacing between conductive traces and the quality of the protective coatings applied to the PCB can affect its vulnerability to creep corrosion.
Effects of Creep Corrosion
Creep corrosion can have several detrimental effects on the performance and reliability of electronic devices:
Short Circuits
As conductive materials migrate and form unwanted connections between traces on a PCB, short circuits can occur. These short circuits can disrupt the normal functioning of the device, cause signal distortion, and even lead to complete failure.
Signal Degradation
Even if creep corrosion does not result in a complete short circuit, it can still cause signal degradation by altering the electrical characteristics of the PCB. This can manifest as increased noise, reduced signal strength, or changes in the frequency response of the device.
Intermittent Failures
Creep corrosion can cause intermittent failures in electronic devices, which can be particularly challenging to diagnose and repair. These failures may occur only under specific environmental conditions or after a certain period of use, making them difficult to reproduce and troubleshoot.
Reduced Reliability
Overall, creep corrosion can significantly reduce the reliability of electronic devices. As the unwanted connections formed by ion migration continue to grow and evolve over time, the risk of failure increases, potentially leading to premature device failure or unexpected downtime.
Prevention of Creep Corrosion
Several strategies can be employed to prevent or mitigate the effects of creep corrosion in PCBs:
Design Considerations
Proper PCB design can help reduce the risk of creep corrosion. This includes:
- Maximizing the spacing between conductive traces
- Avoiding sharp corners or points on traces, which can concentrate electric fields and promote ion migration
- Using protective coatings, such as conformal coatings or solder masks, to isolate conductive materials from the environment
Design Factor | Recommendation |
---|---|
Trace Spacing | Maximize spacing between conductive traces |
Trace Geometry | Avoid sharp corners or points on traces |
Protective Coatings | Use conformal coatings or solder masks |
Material Selection
Choosing materials that are less susceptible to ion migration can help prevent creep corrosion. For example, using gold or palladium instead of silver for conductive traces can reduce the risk of migration. Additionally, selecting high-quality base materials and laminates can improve the overall resistance of the PCB to environmental factors.
Manufacturing Process Control
Strict control of the PCB manufacturing process can help minimize the presence of contaminants that contribute to creep corrosion. This includes:
- Proper cleaning and drying of the PCB after each manufacturing step
- Using high-purity chemicals and materials
- Implementing dust control measures in the manufacturing environment
Environmental Control
Controlling the environment in which PCBs are used and stored can help reduce the risk of creep corrosion. This includes:
- Maintaining appropriate humidity levels (typically below 60% relative humidity)
- Avoiding exposure to high temperatures or temperature fluctuations
- Using protective packaging or enclosures to isolate PCBs from contaminants
Environmental Factor | Recommended Control |
---|---|
Humidity | Maintain below 60% relative humidity |
Temperature | Avoid high temperatures and fluctuations |
Contamination | Use protective packaging or enclosures |
Regular Inspection and Maintenance
Regularly inspecting PCBs for signs of creep corrosion and performing necessary maintenance can help detect and address issues before they lead to device failure. This may include:
- Visual inspection of the PCB surface for discoloration, dendrite growth, or other signs of corrosion
- Cleaning the PCB to remove contaminants
- Repairing or replacing damaged components or traces
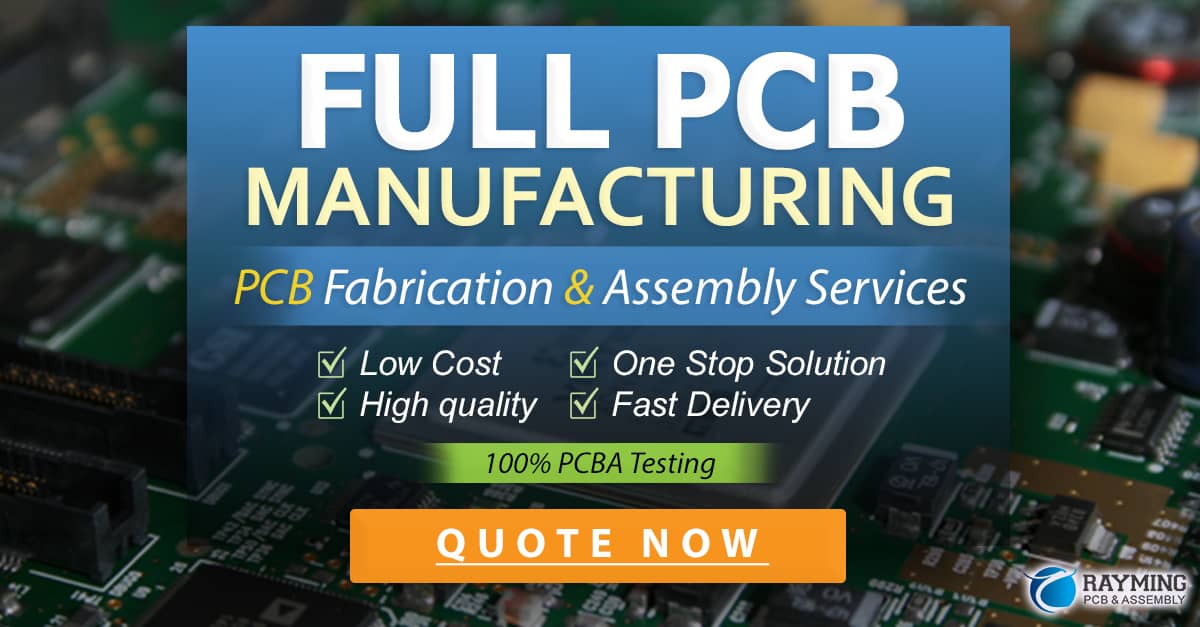
Frequently Asked Questions (FAQ)
-
What are the most common signs of creep corrosion on a PCB?
The most common signs of creep corrosion include discoloration of the PCB surface, the presence of dendrite-like growths between conductive traces, and a decrease in the overall performance or reliability of the electronic device. -
Can creep corrosion occur in all types of PCBs?
Creep corrosion can occur in any type of PCB that uses conductive materials such as copper or silver. However, the risk of creep corrosion may vary depending on the specific materials used, the design of the PCB, and the environmental conditions in which it operates. -
How can I test for creep corrosion in my PCBs?
Visual inspection is the most common method for detecting creep corrosion. This can be done using a microscope or high-resolution camera to look for signs of dendrite growth or discoloration on the PCB surface. Electrical testing, such as resistance or continuity measurements, can also be used to identify unwanted connections caused by creep corrosion. -
Is creep corrosion reversible?
In some cases, early stages of creep corrosion can be reversed by cleaning the PCB and removing the contaminants or dendrite growths. However, if the corrosion has progressed to the point of causing permanent damage to the conductive traces or components, the affected areas may need to be repaired or replaced. -
How often should I inspect my PCBs for creep corrosion?
The frequency of PCB inspections for creep corrosion depends on the specific application and environment in which the device operates. In general, it is recommended to inspect PCBs at least once per year, or more frequently if the device is exposed to harsh environmental conditions or if signs of corrosion are detected during previous inspections.
Conclusion
Creep corrosion is a significant concern for the reliability and performance of electronic devices that utilize PCBs. By understanding the causes, effects, and prevention methods of creep corrosion, designers and manufacturers can take steps to minimize the risk of this type of corrosion and ensure the long-term functionality of their products.
Implementing proper design considerations, selecting appropriate materials, controlling the manufacturing process and environment, and performing regular inspections and maintenance are all essential strategies for preventing and mitigating the effects of creep corrosion in PCBs.
By adopting these best practices and staying informed about the latest developments in PCB technology and corrosion prevention, the electronics industry can continue to produce reliable, high-performance devices that meet the ever-growing demands of modern applications.
0 Comments