Introduction to Comparative Tracking Index (CTI)
Comparative Tracking Index (CTI) is a critical parameter in the selection of PCB base materials. It is a measure of a material’s ability to resist electrical tracking and erosion under high voltage stress and environmental conditions. CTI plays a crucial role in determining the reliability and performance of printed circuit boards (PCBs) in various applications, especially those involving high voltage and harsh environments.
Definition of CTI
CTI is defined as the voltage at which a conductive path forms on the surface of an insulating material due to degradation caused by electrical discharges. It is expressed in volts and is determined by a standardized test method, such as IEC 60112 or ASTM D3638.
Importance of CTI in PCB Design
The CTI of a PCB base material is essential for several reasons:
- Insulation performance: Materials with higher CTI values provide better insulation and are less prone to electrical tracking and breakdown.
- Reliability: PCBs with high CTI base materials are more reliable and have a longer lifespan, especially in demanding applications.
- Safety: In high voltage applications, using materials with adequate CTI ensures the safety of the equipment and personnel.
Factors Affecting CTI
Several factors influence the CTI of a PCB base material:
Material Composition
The chemical composition of the base material plays a significant role in determining its CTI. Materials with higher resistance to electrical discharges and erosion typically have higher CTI values.
Surface Contamination
Contamination on the surface of the PCB, such as dust, moisture, or chemical residues, can lower the CTI by providing a conductive path for electrical discharges.
Environmental Conditions
Factors such as temperature, humidity, and altitude can affect the CTI of a material. Higher temperatures and humidity levels generally reduce the CTI, while higher altitudes can increase the risk of electrical discharges due to reduced air pressure.
Common PCB Base Materials and their CTI Values
Various PCB base materials are used in the industry, each with its own CTI value. Some common materials include:
Material | CTI Range (V) |
---|---|
FR-4 | 175-400 |
Polyimide | 400-600 |
Teflon | 600+ |
Ceramic | 600+ |
FR-4
FR-4 is the most widely used PCB base material. It is a composite material made of woven fiberglass cloth with an epoxy resin binder. The CTI of FR-4 typically ranges from 175 to 400 volts, depending on the specific formulation and glass transition temperature (Tg).
Polyimide
Polyimide is a high-performance polymer known for its excellent thermal stability, chemical resistance, and mechanical properties. It has a higher CTI than FR-4, typically ranging from 400 to 600 volts, making it suitable for more demanding applications.
Teflon
Teflon, or polytetrafluoroethylene (PTFE), is a fluoropolymer with exceptional dielectric properties and a high CTI, often exceeding 600 volts. It is used in high-frequency and high-temperature applications.
Ceramic
Ceramic PCB base materials, such as alumina or aluminum nitride, have excellent insulation properties and a high CTI, typically above 600 volts. They are used in high-power and high-temperature applications.
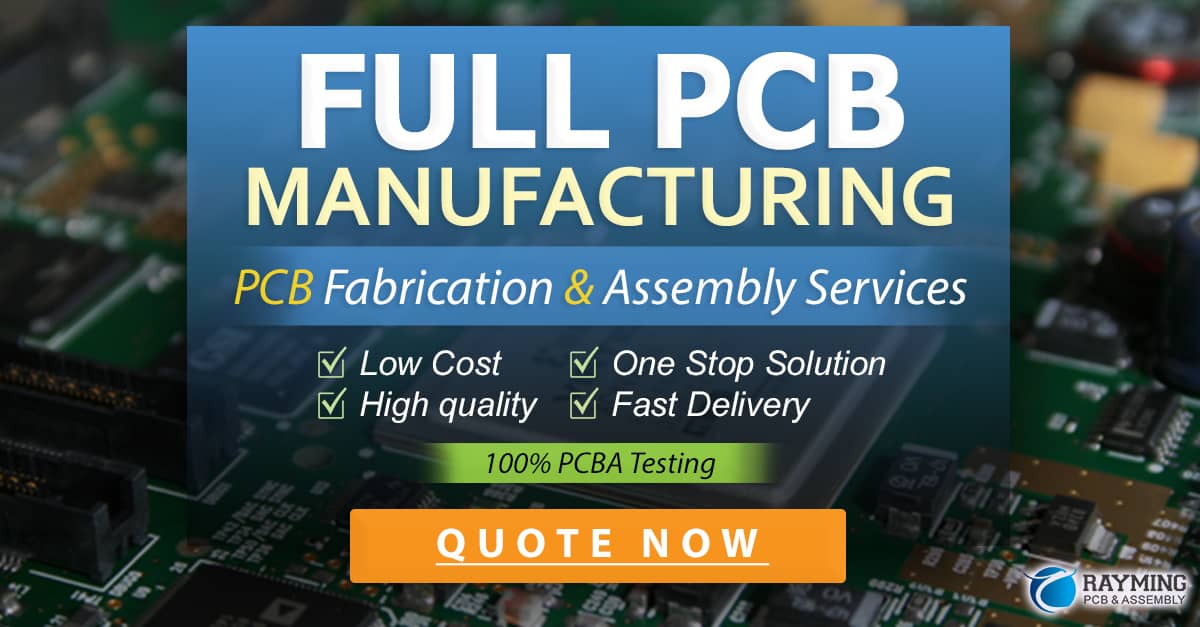
CTI Testing Methods
Several standardized test methods are used to determine the CTI of a material:
IEC 60112
The International Electrotechnical Commission (IEC) 60112 standard, also known as the “Proof Tracking Index” (PTI) test, is the most widely used method for determining CTI. In this test, a voltage is applied between two electrodes placed on the surface of the material, and the voltage is gradually increased until a conductive path forms. The highest voltage at which no tracking occurs is recorded as the PTI value.
ASTM D3638
The American Society for Testing and Materials (ASTM) D3638 standard is similar to IEC 60112 but uses a different electrode configuration and voltage ramp rate. The test result is reported as the “Comparative Tracking Index” (CTI) value.
Designing PCBs with Appropriate CTI
When designing a PCB, it is essential to select a base material with an appropriate CTI value for the intended application. Here are some guidelines:
-
Determine the operating voltage: The CTI of the base material should be higher than the maximum expected voltage in the application, with an appropriate safety margin.
-
Consider environmental factors: If the PCB will be exposed to harsh environmental conditions, such as high humidity or temperature, choose a material with a higher CTI to compensate for the reduced insulation performance.
-
Evaluate cost and availability: High-CTI materials may be more expensive and less readily available than standard materials like FR-4. Consider the trade-offs between performance, cost, and lead time.
-
Follow industry standards: Adhere to relevant industry standards and guidelines, such as IPC-4101, when selecting PCB base materials and specifying CTI requirements.
Frequently Asked Questions (FAQ)
1. What is the difference between CTI and PTI?
CTI (Comparative Tracking Index) and PTI (Proof Tracking Index) are both measures of a material’s resistance to electrical tracking, but they are determined using slightly different test methods. CTI is based on the ASTM D3638 standard, while PTI is based on the IEC 60112 standard. The main difference lies in the electrode configuration and voltage ramp rate used in the tests.
2. Can the CTI of a PCB base material change over time?
Yes, the CTI of a material can degrade over time due to factors such as surface contamination, exposure to harsh environmental conditions, or material aging. It is essential to consider these factors when designing a PCB and to specify appropriate cleaning and protection measures to maintain the material’s CTI throughout its lifespan.
3. What is the minimum CTI required for high voltage applications?
The minimum CTI required for high voltage applications depends on the specific voltage level and safety standards applicable to the industry or application. As a general guideline, materials with a CTI of 400 volts or higher are typically used for high voltage applications. However, it is essential to consult relevant standards and regulations to determine the appropriate CTI for a given application.
4. Can the CTI be improved by surface treatments?
Yes, surface treatments such as conformal coating or solder mask can help improve the CTI of a PCB by providing an additional insulating layer and protecting the surface from contamination. However, it is essential to ensure that the surface treatment is compatible with the base material and does not adversely affect other properties such as adhesion or thermal performance.
5. How does the CTI of a material affect its dielectric constant?
The CTI of a material is not directly related to its dielectric constant. CTI measures a material’s resistance to electrical tracking, while the dielectric constant measures its ability to store electrical energy. However, materials with high CTI values often have good dielectric properties, as they are designed to provide excellent electrical insulation.
Conclusion
Comparative Tracking Index (CTI) is a critical parameter in the selection of PCB base materials, particularly for applications involving high voltage and harsh environments. It measures a material’s ability to resist electrical tracking and erosion, which directly affects the reliability and safety of the PCB. Factors such as material composition, surface contamination, and environmental conditions can influence the CTI of a material.
When designing a PCB, it is essential to choose a base material with an appropriate CTI value based on the intended application, operating voltage, and environmental factors. Common PCB base materials include FR-4, polyimide, Teflon, and ceramic, each with its own CTI range and properties. Standardized test methods, such as IEC 60112 and ASTM D3638, are used to determine the CTI of a material.
By understanding the importance of CTI and selecting PCB base materials with appropriate CTI values, designers can ensure the reliability, performance, and safety of their PCBs in various applications.
0 Comments