Understanding BGA Packages
Before diving into the reballing process, it’s essential to understand what a BGA package is and why it’s used in electronic devices.
What is a BGA Package?
A BGA package is a type of surface-mount packaging used for integrated circuits (ICs) that utilizes a grid of solder balls to connect the IC to the printed circuit board (PCB). The solder balls are arranged in a grid pattern on the bottom side of the package, allowing for a high density of connections in a small area.
Advantages of BGA Packages
BGA packages offer several advantages over other types of IC packaging:
- High connection density: BGA packages can accommodate a large number of connections in a small footprint, making them ideal for complex, high-performance devices.
- Better thermal and electrical performance: The short connection paths between the IC and PCB in a BGA package result in improved thermal and electrical characteristics.
- Reduced package size: BGA packages enable smaller device sizes compared to other packaging types, such as quad flat packages (QFPs).
Common Applications of BGA Packages
BGA packages are widely used in various electronic devices, including:
- Smartphones and tablets
- Laptops and desktop computers
- Gaming consoles
- Network equipment
- Automotive electronics
Why BGA Reballing is Necessary
Over time, BGA connections can deteriorate or fail due to various reasons, leading to device malfunction or complete failure. Some common causes of BGA connection issues include:
- Thermal stress: Repeated heating and cooling cycles can cause the solder balls to crack or detach from the package or PCB.
- Mechanical stress: Physical stress, such as drops or impacts, can damage the solder balls or cause them to shear off.
- Manufacturing defects: Improperly applied solder balls or poor-quality materials can result in weak or faulty connections.
- Corrosion: Exposure to moisture or other corrosive elements can degrade the solder balls and cause connection failures.
When BGA connections fail, the device may exhibit symptoms such as:
- Intermittent operation
- Reduced performance
- Complete failure to power on or function
In these cases, BGA reballing can be used to repair the damaged connections and restore the device to proper functioning.
The BGA Reballing Process
The BGA reballing process involves several steps to remove the damaged solder balls and replace them with new ones. The following table outlines the general steps involved in BGA reballing:
Step | Description |
---|---|
1 | Identify the faulty BGA chip or package |
2 | Remove the chip from the PCB using a hot air rework station |
3 | Clean the PCB and chip pads to remove old solder and flux residue |
4 | Apply new solder paste or flux to the pads |
5 | Place new solder balls on the pads using a reballing stencil or manual placement |
6 | Reflow the solder balls using a hot air rework station or reflow oven |
7 | Clean the chip and PCB to remove excess flux |
8 | Reinstall the chip on the PCB and test for proper function |
Equipment and Materials Required for BGA Reballing
To perform BGA reballing, you’ll need the following equipment and materials:
- Hot air rework station with adjustable temperature and airflow controls
- Soldering iron
- Solder paste or flux
- Solder balls (sized to match the original BGA package)
- Reballing stencil (for applying solder balls)
- Cleaning supplies (isopropyl alcohol, Flux Remover, brushes)
- Magnifying tools (microscope or magnifying lamp)
- Tweezers and other small hand tools
Challenges and Considerations in BGA Reballing
BGA reballing is a complex and delicate process that requires skill, patience, and attention to detail. Some of the challenges and considerations in BGA reballing include:
- Proper alignment of the solder balls: Misaligned solder balls can result in poor connections or short circuits.
- Controlling temperature and airflow: Excessive heat or airflow can damage the chip or PCB, while insufficient heat can result in poor solder joint formation.
- Cleaning and surface preparation: Adequate cleaning and surface preparation are essential for ensuring good solder joint formation and preventing contamination.
- Selecting the correct solder ball size: Using solder balls that are too large or small can result in connection issues or mechanical stress on the package.
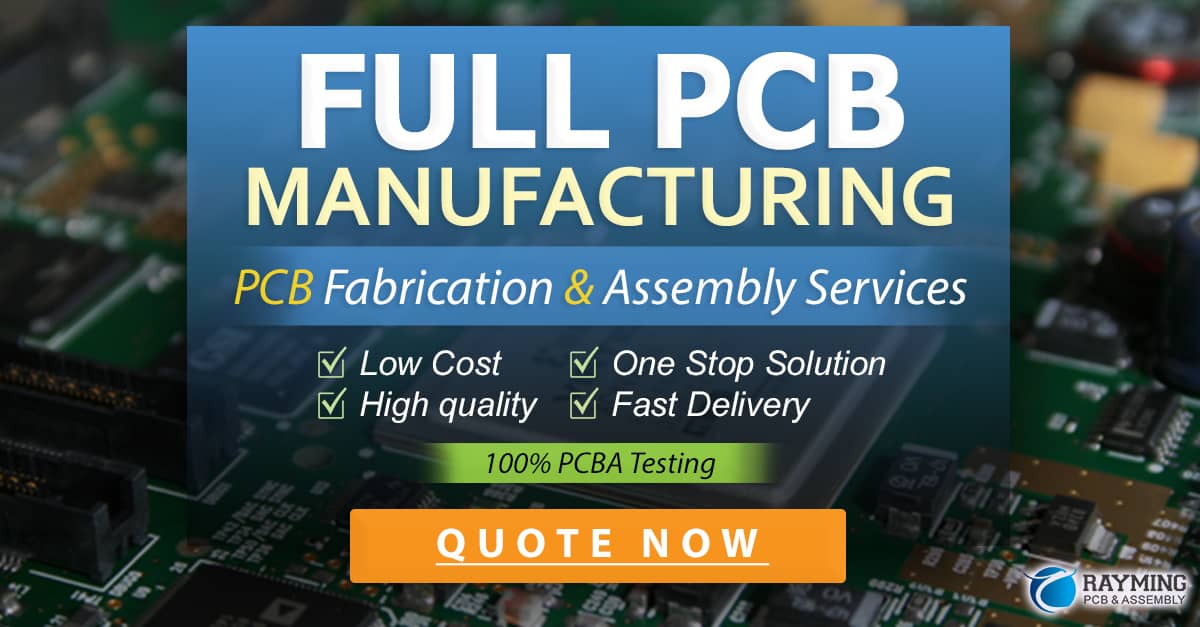
Alternatives to BGA Reballing
In some cases, BGA reballing may not be the most appropriate or cost-effective solution for repairing a device. Some alternatives to BGA reballing include:
BGA Rework
BGA rework involves removing the faulty BGA chip and replacing it with a new one, rather than replacing the solder balls. This process can be faster and less expensive than reballing, but it requires a compatible replacement chip.
PCB Replacement
If the PCB itself is damaged or the BGA chip is not the only component causing issues, replacing the entire PCB may be more cost-effective than attempting to repair individual components.
Device Replacement
In some cases, particularly with older or less expensive devices, it may be more economical to replace the entire device rather than investing in BGA reballing or other repair techniques.
Conclusion
BGA reballing is a valuable technique for repairing and refurbishing electronic devices with damaged or faulty BGA connections. By replacing the solder balls on a BGA package, technicians can restore proper function and extend the life of the device. However, BGA reballing is a complex process that requires specialized equipment, materials, and expertise.
When considering BGA reballing as a repair option, it’s essential to weigh the costs and benefits against alternatives such as BGA rework, PCB replacement, or device replacement. Ultimately, the most appropriate solution will depend on factors such as the type and extent of the damage, the availability of compatible replacement parts, and the overall value of the device.
Frequently Asked Questions (FAQ)
-
Q: How long does BGA reballing take?
A: The time required for BGA reballing varies depending on the complexity of the device and the experience of the technician. In general, reballing a single BGA chip can take anywhere from 30 minutes to several hours. -
Q: Can I perform BGA reballing myself?
A: While it is possible to perform BGA reballing yourself, it is not recommended unless you have significant experience with electronics repair and access to the necessary equipment and materials. Improper reballing can result in further damage to the device or injury to yourself. -
Q: How much does BGA reballing cost?
A: The cost of BGA reballing varies depending on the device, the extent of the damage, and the service provider. In general, professional BGA reballing services can range from $50 to $200 or more per chip. -
Q: Is BGA reballing a permanent fix?
A: When performed correctly, BGA reballing can be a long-lasting solution for damaged or faulty BGA connections. However, the longevity of the repair will depend on factors such as the quality of the workmanship, the materials used, and the operating conditions of the device. -
Q: Can BGA reballing fix other issues besides connection problems?
A: BGA reballing specifically addresses issues related to damaged or faulty solder ball connections. If the device has other underlying issues, such as a damaged PCB or faulty components, reballing alone may not resolve the problem.
0 Comments