How does Automated Optical Inspection work?
AOI systems typically consist of the following components:
- Cameras: High-resolution cameras capture images of the inspected product from various angles.
- Lighting: Proper lighting is crucial to ensure consistent and accurate image capture. Different lighting techniques, such as direct, diffuse, or backlight illumination, may be used depending on the product and the types of defects being detected.
- Image processing software: Specialized software analyzes the captured images, comparing them to predefined templates or CAD data to identify any discrepancies or defects.
- Conveyor system: A conveyor system moves the products through the inspection area, ensuring consistent positioning and alignment for accurate image capture.
The AOI process involves the following steps:
- Image acquisition: The cameras capture images of the product as it passes through the inspection area.
- Image preprocessing: The captured images are processed to enhance their quality, remove noise, and prepare them for analysis.
- Image analysis: The image processing software compares the captured images to the reference data, looking for any deviations or defects.
- Defect classification: If defects are detected, the software classifies them based on predefined criteria, such as type, size, or location.
- Reporting: The AOI system generates a report detailing the inspection results, including the number and types of defects found, as well as their locations on the product.
Benefits of Automated Optical Inspection
Implementing AOI in the manufacturing process offers several advantages:
- Improved quality control: AOI systems can detect defects that may be missed by manual inspection, ensuring a higher level of product quality and reliability.
- Increased efficiency: Automated inspection is faster than manual inspection, allowing for higher throughput and reduced production time.
- Cost reduction: By detecting defects early in the manufacturing process, AOI helps reduce the cost of rework, scrap, and warranty claims.
- Consistency: AOI systems provide consistent and repeatable inspection results, eliminating the variability associated with manual inspection.
- Traceability: AOI systems generate detailed inspection reports, which can be used for traceability and root cause analysis of defects.
Applications of Automated Optical Inspection
AOI is widely used in various industries, including:
- Electronics manufacturing: AOI is commonly used to inspect PCBs, solder joints, and electronic components for defects such as missing components, incorrect placement, or solder bridging.
- Automotive industry: AOI systems are used to inspect automotive parts, such as connectors, sensors, and printed labels, ensuring they meet the required quality standards.
- Medical device manufacturing: AOI is employed to inspect medical devices, such as catheters, syringes, and implants, for defects that could compromise patient safety.
- Packaging industry: AOI systems are used to inspect product packaging for defects such as missing or misaligned labels, incorrect barcodes, or seal integrity issues.
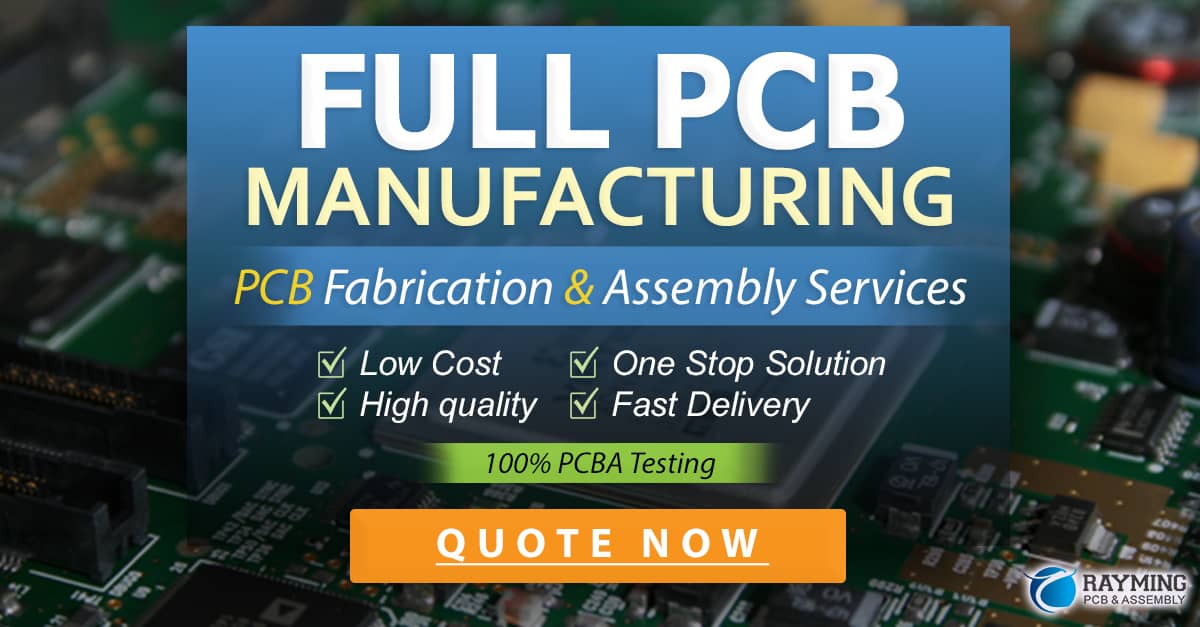
Types of defects detected by Automated Optical Inspection
AOI systems can detect a wide range of defects, depending on the specific application and the type of product being inspected. Some common defects detected by AOI in the electronics industry include:
Defect Type | Description |
---|---|
Missing components | Components that are absent from the PCB |
Misaligned components | Components that are not placed correctly on the PCB |
Solder bridging | Unintended connections between solder joints |
Insufficient solder | Solder joints that do not have enough solder material |
Excess solder | Solder joints with too much solder material |
Lifted leads | Component leads that are not properly soldered to the PCB |
Tombstoning | Components that stand up on one end due to uneven solder reflow |
Limitations of Automated Optical Inspection
While AOI offers many benefits, it also has some limitations:
- Initial investment: Implementing an AOI system can require a significant initial investment in equipment, software, and training.
- Limited depth perception: AOI systems may have difficulty detecting defects that are hidden or obscured, such as components under other components or defects within the product’s internal structure.
- False positives and false negatives: AOI systems may sometimes identify defects that are not actually present (false positives) or fail to detect actual defects (false negatives), requiring additional manual inspection to verify the results.
- Programming and setup: Developing inspection programs and setting up the AOI system for new products can be time-consuming and require specialized expertise.
Automated Optical Inspection vs. Manual Inspection
While AOI offers many advantages over manual inspection, there are some cases where manual inspection may still be necessary or preferred:
Inspection Method | Advantages | Disadvantages |
---|---|---|
Automated Optical Inspection | – High speed and throughput – Consistent and repeatable results – Ability to detect small or subtle defects – Detailed inspection reports |
– High initial investment – Limited depth perception – Potential for false positives and false negatives – Requires specialized programming and setup |
Manual Inspection | – Lower initial investment – Flexibility in handling a wide range of products – Ability to detect defects that may be missed by AOI – Human judgment and decision-making |
– Slower and less efficient than AOI – Inconsistent and subjective results – Limited ability to detect small or subtle defects – No detailed inspection reports |
In practice, many manufacturers use a combination of AOI and manual inspection to ensure the highest level of product quality. AOI is used for high-volume inspection of critical defects, while manual inspection is used for more complex or specialized tasks, or to verify the results of the AOI system.
Future trends in Automated Optical Inspection
As technology advances, AOI systems are becoming increasingly sophisticated and capable. Some of the future trends in AOI include:
- 3D AOI: The use of 3D imaging techniques, such as structured light or laser triangulation, allows AOI systems to capture and analyze three-dimensional images of products, providing better depth perception and the ability to detect defects that may be missed by traditional 2D AOI.
- Machine learning and artificial intelligence: The integration of machine learning and AI algorithms into AOI systems enables them to learn and adapt to new defect types and product variations, improving their accuracy and flexibility.
- Inline AOI: Integrating AOI systems directly into the production line allows for real-time inspection and feedback, enabling manufacturers to identify and correct defects more quickly and efficiently.
- Collaborative robots: The use of collaborative robots, or cobots, in conjunction with AOI systems allows for the automation of manual inspection tasks, such as handling and positioning products for inspection.
Frequently Asked Questions (FAQ)
- What is the difference between AOI and automated X-ray inspection (AXI)?
-
AOI uses visual imaging techniques to inspect the surface of products, while AXI uses X-rays to inspect the internal structure of products, such as solder joints or component placement within an assembled PCB.
-
Can AOI detect all types of defects?
-
While AOI is highly effective at detecting a wide range of defects, it may have limitations in detecting defects that are hidden or obscured, such as those within the internal structure of a product. In some cases, additional inspection methods, such as AXI or manual inspection, may be necessary to ensure comprehensive defect detection.
-
How does the speed of AOI compare to manual inspection?
-
AOI systems are generally much faster than manual inspection, with some systems capable of inspecting thousands of products per hour. The exact speed advantage depends on factors such as the complexity of the product, the number of inspection points, and the specific AOI system being used.
-
What training is required to operate an AOI system?
-
Operating an AOI system requires specialized training in programming, setup, and maintenance. Operators should have a good understanding of the products being inspected, the types of defects to look for, and how to interpret the inspection results. Some AOI system manufacturers offer training and certification programs to ensure operators have the necessary skills and knowledge.
-
How do I choose the right AOI system for my manufacturing process?
- Choosing the right AOI system depends on several factors, including the types of products being inspected, the defects being detected, the required inspection speed and accuracy, and the available budget. It’s important to work with an experienced AOI system provider who can assess your specific needs and recommend a system that meets your requirements. Additionally, it may be helpful to conduct a feasibility study or pilot project to validate the performance of the AOI system before making a full-scale implementation.
In conclusion, Automated Optical Inspection is a powerful technology that offers significant benefits for quality control and defect detection in manufacturing processes. By understanding the principles of AOI, its applications, and its limitations, manufacturers can make informed decisions about how to integrate this technology into their operations to improve product quality, increase efficiency, and reduce costs.
0 Comments