Understanding Solder Voids
Definition and Characteristics
A solder void is a small, enclosed cavity or gap within a solder joint that is devoid of solder material. These voids can occur between the component lead and the pad, or within the solder itself. Solder voids are typically spherical or irregular in shape and can vary in size from a few microns to several millimeters in diameter.
Types of Solder Voids
There are two main types of solder voids:
-
Macro voids: These are larger voids that are visible to the naked eye or through low-magnification optical inspection. Macro voids can significantly impact the strength and conductivity of the solder joint.
-
Micro voids: These are smaller voids that require high-magnification imaging techniques, such as X-ray or acoustic microscopy, to detect. Although micro voids may not immediately cause joint failure, they can lead to long-term reliability issues.
Causes of Solder Voids
Several factors can contribute to the formation of solder voids during the soldering process:
Outgassing
Outgassing is the primary cause of solder voids. It occurs when gases trapped within the solder paste, flux, or printed circuit board (PCB) laminate escape during the reflow process. As the solder melts and solidifies, these gases can create bubbles that remain trapped within the solder joint, forming voids.
Insufficient Wetting
Poor wetting of the solder to the component lead or pad surface can also lead to void formation. Insufficient wetting can be caused by factors such as:
- Contamination or oxidation of the surfaces to be soldered
- Incorrect solder paste composition or inadequate flux activity
- Inappropriate reflow temperature profile or cooling rate
Improper Solder Paste Printing
Issues with the solder paste printing process can contribute to void formation, such as:
- Incorrect stencil thickness or aperture size
- Poor paste transfer efficiency or inconsistent paste volume
- Inadequate stencil cleaning or damage to the stencil surface
PCB Design and Manufacturing Defects
Defects in the PCB design or manufacturing process can also lead to solder voids, including:
- Inadequate pad size or spacing
- Vias or plated through-holes with insufficient copper plating
- Contamination or moisture absorption in the PCB laminate
Effects of Solder Voids
Solder voids can have several negative effects on the reliability and performance of electronic assemblies:
Reduced Mechanical Strength
Voids in the solder joint can significantly reduce its mechanical strength and ability to withstand stress and strain. This weakening can lead to joint cracking or failure under thermal cycling, vibration, or mechanical shock.
Increased Electrical Resistance
The presence of voids in the solder joint can increase its electrical resistance, leading to higher power dissipation, localized heating, and potential signal integrity issues. In high-current applications, voids can cause excessive heating and premature joint failure.
Accelerated Fatigue and Creep
Solder voids can accelerate the fatigue and creep processes in the solder joint, particularly under thermal cycling conditions. As the solder expands and contracts, the stress concentration around the void can lead to crack initiation and propagation, ultimately causing joint failure.
Reliability Concerns
The cumulative effects of solder voids can lead to long-term reliability issues in electronic assemblies. Even if the voids do not cause immediate failure, they can degrade the joint’s performance over time, increasing the risk of intermittent failures or complete system breakdowns.
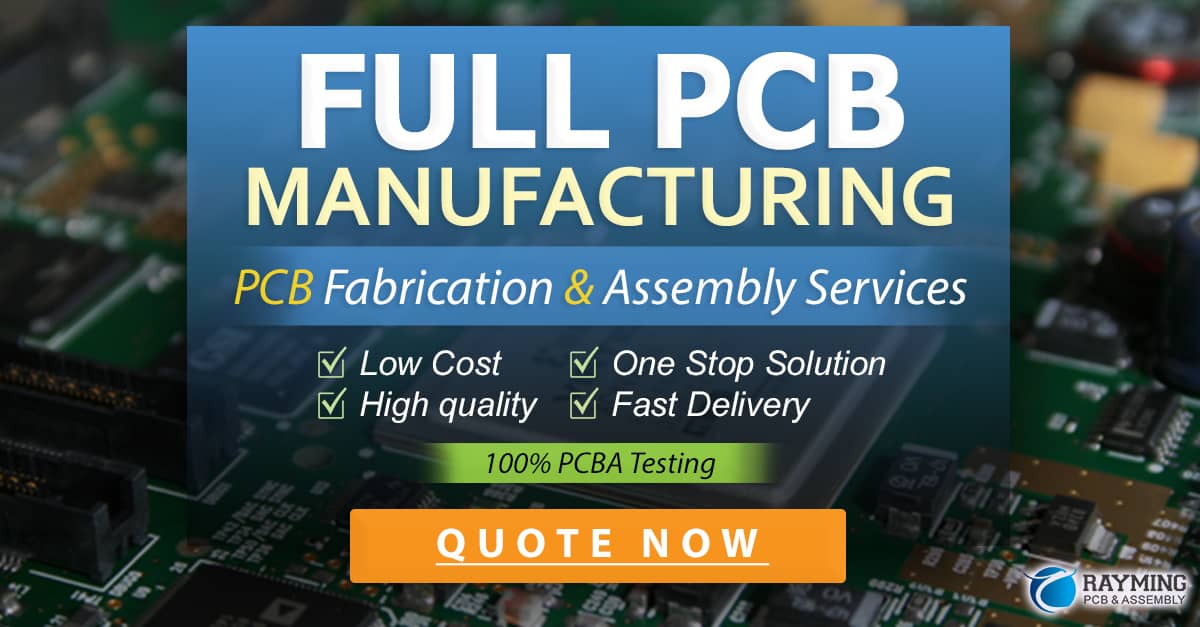
Detecting Solder Voids
Several techniques can be used to detect and characterize solder voids in electronic assemblies:
Visual Inspection
Macro voids can often be detected through visual inspection using low-magnification optical microscopes or high-resolution cameras. However, visual inspection is limited to surface-level examination and cannot detect voids within the solder joint or under components.
X-Ray Inspection
X-ray inspection is a non-destructive technique that can detect both macro and micro voids within the solder joint. Two-dimensional (2D) X-ray imaging provides a top-down view of the joint, while three-dimensional (3D) X-ray computed tomography (CT) offers a more detailed, cross-sectional analysis of void size, shape, and location.
Acoustic Microscopy
Scanning acoustic microscopy (SAM) is another non-destructive method for detecting solder voids. SAM uses high-frequency ultrasound waves to create images of the internal structure of the solder joint. Voids appear as distinct echoes or reflections in the acoustic image.
Cross-Sectional Analysis
For a more detailed examination of solder voids, cross-sectional analysis can be performed. This destructive technique involves cutting the solder joint and examining the exposed cross-section using optical or electron microscopy. While this method provides valuable information on void morphology and distribution, it is limited to a small sample size and cannot be used for in-line inspection.
Preventing Solder Voids
To minimize the occurrence of solder voids, several preventive measures can be implemented in the soldering process:
Solder Paste Selection
Choosing a high-quality solder paste with the appropriate composition and flux activity can help reduce void formation. Lead-free solder pastes with higher silver content and more active flux systems have been shown to produce fewer voids compared to their lead-based counterparts.
Stencil Design and Printing Optimization
Proper stencil design and printing parameters can ensure consistent solder paste deposition and minimize the risk of void formation. Key factors to consider include:
- Optimal stencil thickness and aperture size for the component pitch and pad geometry
- Adequate stencil cleaning and maintenance to prevent paste buildup or contamination
- Proper printer setup, including squeegee pressure, speed, and angle
Reflow Profile Optimization
Optimizing the reflow temperature profile can help minimize outgassing and ensure proper solder wetting. Key considerations include:
- Gradual ramp-up to the peak temperature to allow for controlled outgassing
- Sufficient time above the solder liquidus temperature to promote complete wetting
- Controlled cooling rate to prevent rapid solidification and void entrapment
PCB Design and Surface Finish
Proper PCB design and surface finish can also help reduce void formation. Guidelines include:
- Adequate pad size and spacing for the component pitch and solder volume
- Proper via design and copper plating to ensure reliable connections
- Use of low-void-potential surface finishes, such as immersion silver or electroless nickel/immersion gold (ENIG)
Process Control and Monitoring
Implementing statistical process control (SPC) and regular monitoring of the soldering process can help identify and address potential void-forming conditions. Key metrics to monitor include:
- Solder paste print quality and volume consistency
- Reflow oven temperature profiles and conveyor speed
- Solder joint visual and X-ray inspection results
Addressing Solder Voids
When solder voids are detected in electronic assemblies, several approaches can be taken to address them:
Rework and Repair
For individual solder joints with voids that exceed acceptable levels, manual rework, and repair can be performed. This process typically involves removing the affected component, cleaning the pads, and resoldering with fresh paste or wire. However, rework can be time-consuming and may introduce additional stress to the PCB.
Process Adjustment
If solder voids are consistently detected across multiple assemblies, adjusting the soldering process parameters may be necessary. This can involve modifying the solder paste composition, stencil design, reflow profile, or other factors based on the root cause analysis of the void formation.
Design Modification
In some cases, solder voids may be attributed to inherent limitations in the PCB or component design. Modifying the design, such as increasing pad size, optimizing via placement, or changing the component package, can help reduce void formation in future production runs.
Acceptance Criteria and Risk Assessment
Establishing acceptable levels of solder void size, quantity, and distribution based on industry standards and application requirements can help guide inspection and rework decisions. Conducting a risk assessment of the potential impact of voids on the assembly’s reliability and performance can also inform the appropriate course of action.
Frequently Asked Questions (FAQ)
-
What is the difference between a macro void and a micro void?
Macro voids are larger voids that are visible to the naked eye or through low-magnification optical inspection, while micro voids are smaller voids that require high-magnification imaging techniques, such as X-ray or acoustic microscopy, to detect. -
Can solder voids cause complete joint failure?
While solder voids may not always cause immediate joint failure, they can significantly weaken the mechanical strength and increase the electrical resistance of the joint. Over time, the presence of voids can accelerate fatigue and creep processes, leading to crack initiation, propagation, and potential joint failure. -
How can X-ray inspection detect solder voids?
X-ray inspection is a non-destructive technique that can detect both macro and micro voids within the solder joint. Two-dimensional (2D) X-ray imaging provides a top-down view of the joint, while three-dimensional (3D) X-ray computed tomography (CT) offers a more detailed, cross-sectional analysis of void size, shape, and location. -
What are some key factors in preventing solder void formation?
To prevent solder void formation, key factors include selecting high-quality solder paste, optimizing stencil design and printing parameters, tuning the reflow temperature profile, ensuring proper PCB design and surface finish, and implementing process control and monitoring measures. -
How can solder voids be addressed in electronic assemblies?
When solder voids are detected, they can be addressed through manual rework and repair of individual joints, adjusting the soldering process parameters based on root cause analysis, modifying the PCB or component design, or establishing acceptance criteria and conducting risk assessments to guide inspection and rework decisions.
Conclusion
Solder voids are a critical defect in the soldering process that can have significant implications for the reliability and performance of electronic assemblies. Understanding the causes, effects, and prevention methods of solder voids is essential for ensuring the production of high-quality, reliable solder joints.
By implementing a combination of material selection, process optimization, design considerations, and inspection techniques, manufacturers can effectively minimize the occurrence of solder voids and address them when they do occur. Regularly monitoring and controlling the soldering process, as well as staying up-to-date with industry best practices and standards, can help maintain the integrity of solder joints and the overall reliability of electronic products.
As electronic devices continue to become more complex and miniaturized, the importance of understanding and managing solder voids will only continue to grow. By actively working to prevent and address this critical defect, manufacturers can improve the quality, reliability, and longevity of their products, ultimately benefiting both their customers and their bottom line.
0 Comments