Introduction to Single-Sided Printed Circuit Boards
A single-sided printed circuit board (PCB) is a basic type of PCB where conductive copper traces are printed on only one side of an insulating substrate material. Single-sided PCBs are the simplest and most cost-effective PCB option, often used for low-complexity electronic designs and projects.
Key Characteristics of Single-Sided PCBs
- Conductive copper traces on only one side of the substrate
- Insulating substrate material, typically FR-4 fiberglass
- Through-hole components mounted on the opposite side of the copper traces
- Simpler and more affordable compared to double-sided or multi-layer PCBs
Advantages and Disadvantages of Single-Sided PCBs
Advantages
- Cost-effective: Single-sided PCBs are the most economical option due to their simple manufacturing process and minimal material requirements.
- Easy to design: Designing single-sided PCBs is straightforward, making them ideal for beginners or simple electronic projects.
- Quick turnaround: The manufacturing process for single-sided PCBs is faster compared to more complex PCB types, resulting in shorter lead times.
- Suitable for low-frequency applications: Single-sided PCBs perform well in low-frequency electronic designs, as they have lower capacitance and inductance compared to multi-layer boards.
Disadvantages
- Limited routing options: With only one layer for conductive traces, single-sided PCBs have limited space for routing, which can make designing complex circuits challenging.
- Larger board size: To accommodate all the necessary components and traces, single-sided PCBs often require a larger board size compared to double-sided or multi-layer PCBs.
- Reduced electrical performance: Single-sided PCBs are not ideal for high-frequency or high-speed applications, as they are more susceptible to electromagnetic interference (EMI) and signal integrity issues.
- Limited heat dissipation: The single-sided nature of these PCBs can make it more difficult to effectively dissipate heat generated by components, which may impact the board’s overall performance and reliability.
Manufacturing Process of Single-Sided PCBs
The manufacturing process for single-sided PCBs typically involves the following steps:
-
Design and layout: The PCB design is created using electronic design automation (EDA) software, which generates the necessary Gerber files for manufacturing.
-
Substrate preparation: The insulating substrate material, usually FR-4 fiberglass, is cut to the required size and shape.
-
Copper cladding: A thin layer of copper foil is laminated onto one side of the substrate using heat and pressure.
-
Photoresist application: A light-sensitive photoresist material is applied to the copper-clad substrate.
-
Exposure and development: The photoresist is exposed to UV light through a photomask containing the PCB design pattern. The exposed areas of the photoresist are then removed during the development process.
-
Etching: The exposed copper areas are etched away using a chemical solution, leaving only the desired conductive traces on the substrate.
-
Photoresist removal: The remaining photoresist is stripped away, revealing the final copper trace pattern.
-
Drilling: Holes are drilled through the substrate to accommodate through-hole components and provide electrical connections between the component leads and the copper traces.
-
Surface finish: A surface finish, such as solder mask or silkscreen, may be applied to protect the copper traces and improve the PCB’s appearance.
-
Quality control: The finished single-sided PCB undergoes inspection and testing to ensure it meets the required specifications and quality standards.
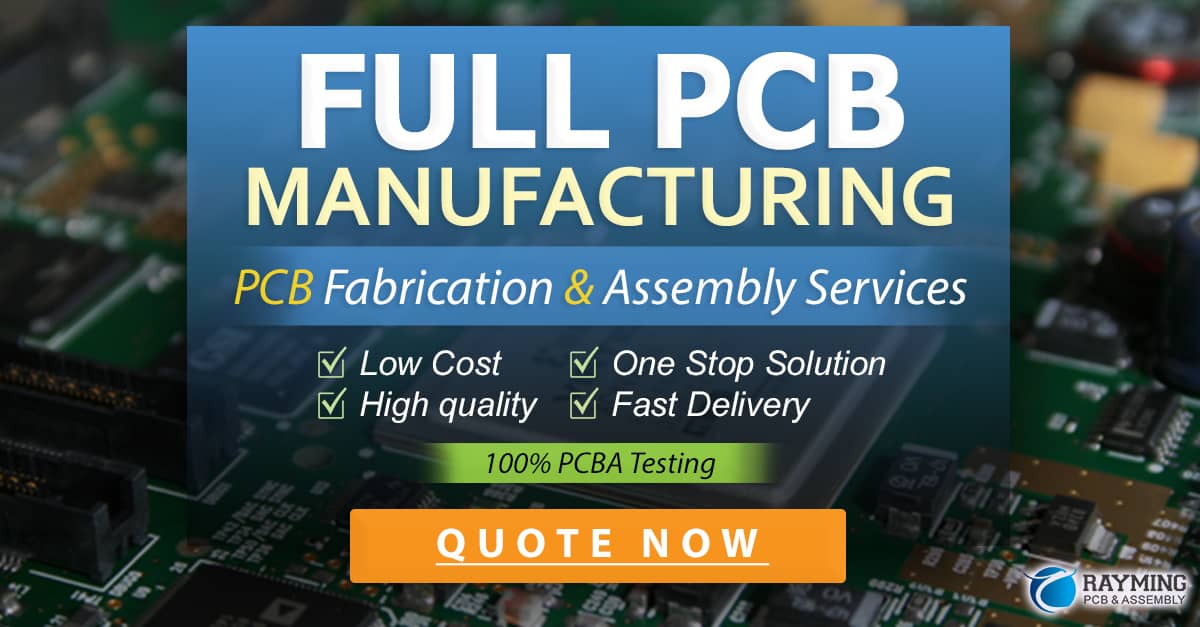
Design Considerations for Single-Sided PCBs
When designing single-sided PCBs, there are several key factors to consider:
Component Placement
- Arrange components to minimize the complexity of trace routing
- Group related components together to simplify connections
- Consider component sizes and footprints to ensure proper spacing
Trace Routing
- Use wider traces for power and ground connections to minimize resistance
- Avoid sharp angles or abrupt changes in trace direction to reduce signal reflections
- Maintain adequate spacing between traces to prevent short circuits and signal crosstalk
Thermal Management
- Position heat-generating components away from temperature-sensitive components
- Provide sufficient copper area for heat dissipation, such as using larger traces or copper pours
- Consider using thermal relief pads for components with high power dissipation
Electromagnetic Compatibility (EMC)
- Minimize trace lengths to reduce the potential for EMI
- Use ground planes or traces to shield sensitive signals from interference
- Follow best practices for grounding and power distribution to maintain signal integrity
Applications of Single-Sided PCBs
Single-sided PCBs are commonly used in a variety of electronic applications, such as:
- Low-complexity consumer electronics (e.g., toys, remote controls, calculators)
- Prototype and hobby projects
- Educational and learning kits
- Low-power and low-frequency devices (e.g., sensors, LED lighting, simple control systems)
- Cost-sensitive mass-produced products (e.g., promotional electronics, disposable devices)
Single-Sided PCB vs. Double-Sided and Multi-Layer PCBs
PCB Type | Layers | Complexity | Cost | Applications |
---|---|---|---|---|
Single-sided | 1 | Low | Low | Simple, low-frequency, cost-sensitive devices |
Double-sided | 2 | Medium | Medium | More complex designs, improved routing |
Multi-layer | 3+ | High | High | High-density, high-speed, advanced electronics |
Single-Sided PCBs
Single-sided PCBs have conductive traces on only one side of the substrate, making them the simplest and most affordable option. They are suitable for low-complexity designs and cost-sensitive applications.
Double-Sided PCBs
Double-sided PCBs have conductive traces on both sides of the substrate, allowing for more complex routing and higher component density. They offer improved performance and flexibility compared to single-sided PCBs but are more expensive to manufacture.
Multi-Layer PCBs
Multi-layer PCBs consist of three or more layers of conductive traces separated by insulating layers. They provide the highest level of design complexity, allowing for dense component placement and intricate routing. Multi-layer PCBs are used in advanced electronics that require high-speed performance, compact form factors, and superior signal integrity.
Future Trends in Single-Sided PCB Technology
As electronic devices continue to evolve, single-sided PCB technology is also advancing to meet new challenges and requirements:
-
Improved substrate materials: Researchers are developing new substrate materials with better thermal, mechanical, and electrical properties to enhance the performance and reliability of single-sided PCBs.
-
Advanced manufacturing techniques: Innovations in PCB manufacturing, such as 3D printing and laser processing, are enabling the creation of more intricate and precise single-sided PCB designs.
-
Flexible and stretchable PCBs: Single-sided flexible and stretchable PCBs are gaining popularity for wearable electronics and IoT applications, offering improved durability and conformability.
-
Eco-friendly materials and processes: There is a growing emphasis on using environmentally friendly materials and manufacturing processes for single-sided PCBs, such as halogen-free substrates and lead-free solders.
Frequently Asked Questions (FAQ)
- What is the difference between a single-sided PCB and a double-sided PCB?
-
A single-sided PCB has conductive traces on only one side of the substrate, while a double-sided PCB has traces on both sides. Double-sided PCBs offer more design flexibility and higher component density but are more expensive to manufacture.
-
Can single-sided PCBs be used for high-frequency applications?
-
Single-sided PCBs are not ideal for high-frequency applications due to their limited routing options and higher susceptibility to EMI and signal integrity issues. For high-frequency designs, double-sided or multi-layer PCBs are typically recommended.
-
How do I choose the right substrate material for my single-sided PCB?
-
The choice of substrate material depends on factors such as the operating temperature range, mechanical requirements, and dielectric properties needed for your application. FR-4 fiberglass is the most common substrate material for single-sided PCBs, offering good thermal and mechanical stability at a reasonable cost.
-
What is the typical turnaround time for manufacturing single-sided PCBs?
-
The turnaround time for single-sided PCBs is generally faster compared to more complex PCB types. Depending on the manufacturer and order volume, single-sided PCBs can often be produced within a few days to a week.
-
Are there any design limitations I should be aware of when creating single-sided PCBs?
- Single-sided PCBs have limited routing options due to having only one layer for conductive traces. This can make designing complex circuits challenging and may require a larger board size to accommodate all components and traces. It’s essential to consider component placement, trace routing, and thermal management carefully when designing single-sided PCBs.
Conclusion
Single-sided PCBs are a fundamental building block in the world of electronics, offering a cost-effective and simple solution for low-complexity designs. By understanding the characteristics, advantages, and limitations of single-sided PCBs, designers and engineers can make informed decisions when selecting the appropriate PCB type for their projects.
As technology advances, single-sided PCBs continue to evolve, with improvements in substrate materials, manufacturing techniques, and eco-friendly practices. While they may not be suitable for every application, single-sided PCBs remain an essential tool in the electronics industry, enabling the creation of a wide range of products and devices.
0 Comments