Introduction to Rigid-Flex PCBs
Rigid-Flex PCBs are a unique type of printed circuit board that combines the benefits of both rigid and flexible PCBs. These boards consist of rigid sections connected by flexible sections, allowing for increased design flexibility, improved reliability, and reduced space requirements. Rigid-Flex PCBs are widely used in various industries, including aerospace, automotive, medical devices, and consumer electronics.
Key Features of Rigid-Flex PCBs
- Combination of rigid and flexible sections
- Improved reliability and durability
- Reduced space requirements
- Increased design flexibility
- Ability to withstand harsh environments
Advantages of Rigid-Flex PCBs
Space Savings
One of the primary advantages of Rigid-Flex PCBs is their ability to save space in electronic devices. By combining rigid and flexible sections, designers can create more compact and efficient layouts. This is particularly important in applications where space is limited, such as wearable devices, smartphones, and medical implants.
Improved Reliability
Rigid-Flex PCBs offer improved reliability compared to traditional rigid PCBs. The flexible sections allow for better stress relief and reduce the risk of connector failures due to vibration or mechanical stress. Additionally, the reduced number of connectors and solder joints in Rigid-Flex PCBs minimizes potential failure points, resulting in a more robust and reliable design.
Design Flexibility
The combination of rigid and flexible sections in Rigid-Flex PCBs provides designers with greater flexibility in creating complex and unique shapes. This enables the development of more ergonomic and user-friendly devices, as well as the integration of multiple functions into a single board. Rigid-Flex PCBs can be folded, bent, or twisted to fit into tight spaces or conform to specific product designs.
Reduced Assembly Time and Costs
By eliminating the need for multiple connectors and cables, Rigid-Flex PCBs can significantly reduce assembly time and costs. The simplified assembly process also minimizes the risk of human error, leading to higher quality and more consistent products. Additionally, the reduced component count and streamlined design can result in lower manufacturing and inventory costs.
Applications of Rigid-Flex PCBs
Aerospace and Defense
Rigid-Flex PCBs are extensively used in the aerospace and defense industries due to their ability to withstand harsh environments and extreme conditions. These boards can endure high temperatures, vibrations, and shock, making them ideal for applications such as avionics, satellite systems, and military equipment.
Automotive
In the automotive industry, Rigid-Flex PCBs are used in various applications, including infotainment systems, advanced driver assistance systems (ADAS), and engine control units (ECUs). The space-saving and reliability benefits of Rigid-Flex PCBs make them well-suited for the demanding requirements of modern vehicles.
Medical Devices
Rigid-Flex PCBs are increasingly used in medical devices, such as wearable monitors, implantable devices, and diagnostic equipment. The flexibility and compact size of these boards allow for the development of more comfortable and less invasive devices, while their reliability ensures consistent performance in critical medical applications.
Consumer Electronics
The consumer electronics industry has widely adopted Rigid-Flex PCBs in products such as smartphones, tablets, smartwatches, and virtual reality headsets. The space-saving and design flexibility offered by Rigid-Flex PCBs enable manufacturers to create more innovative and compact devices with improved functionality and user experience.
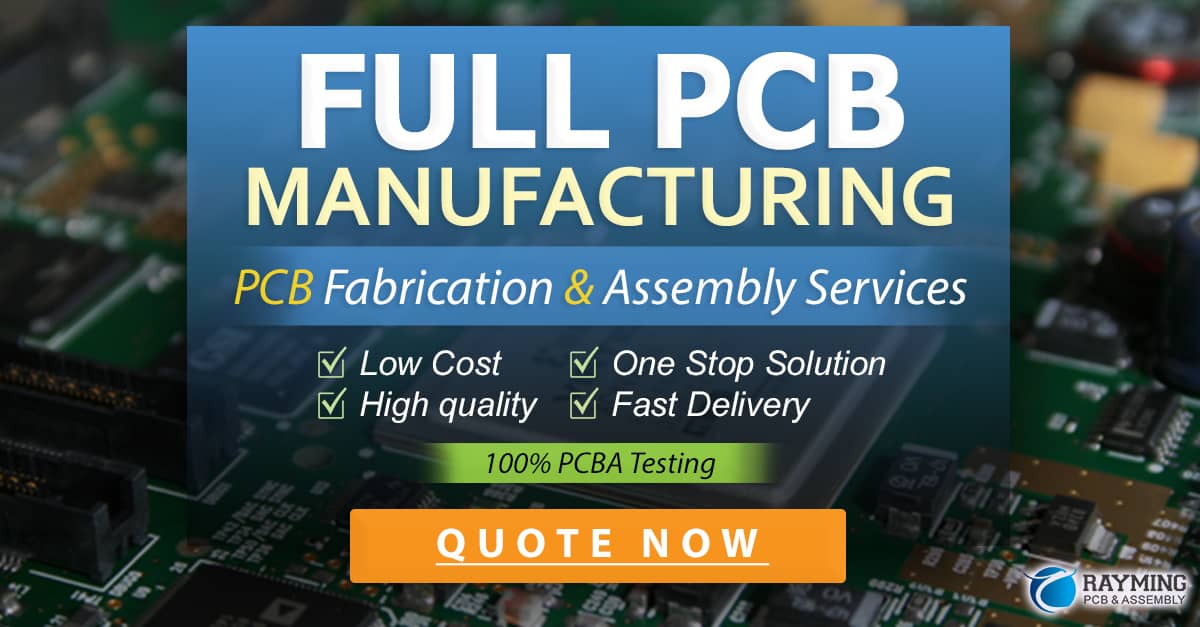
Manufacturing Process of Rigid-Flex PCBs
Material Selection
The manufacturing process of Rigid-Flex PCBs begins with the selection of appropriate materials for the rigid and flexible sections. The rigid sections typically use standard PCB materials, such as FR-4, while the flexible sections use thin, flexible substrates like polyimide or polyester. The choice of materials depends on the specific application requirements, such as temperature range, flexibility, and durability.
Layer Stack-up Design
The next step is to design the layer stack-up of the Rigid-Flex PCB. This involves determining the number and arrangement of conductive layers, insulating layers, and adhesive layers. The layer stack-up design must consider factors such as signal integrity, impedance control, and mechanical stability. Proper design of the layer stack-up is crucial for ensuring the optimal performance and reliability of the Rigid-Flex PCB.
Fabrication
The fabrication process of Rigid-Flex PCBs involves several steps:
- Cutting and laminating the flexible and rigid materials
- Drilling and plating through-holes
- Patterning and etching the conductive layers
- Applying solder mask and silkscreen
- Cutting and shaping the final board outline
The fabrication process requires specialized equipment and expertise to ensure the precise alignment and bonding of the rigid and flexible sections.
Assembly
Once the Rigid-Flex PCB is fabricated, the electronic components are assembled onto the board using standard SMT (surface-mount technology) or through-hole assembly processes. The flexible sections of the board may require special handling and support during the assembly process to prevent damage or deformation.
Testing and Inspection
After assembly, the Rigid-Flex PCB undergoes thorough testing and inspection to ensure its functionality, reliability, and compliance with design specifications. This may include electrical testing, visual inspection, and environmental stress testing, depending on the application requirements.
Design Considerations for Rigid-Flex PCBs
Bend Radius
When designing Rigid-Flex PCBs, it is essential to consider the bend radius of the flexible sections. The bend radius refers to the minimum radius at which the flexible section can be bent without causing damage or affecting its performance. The bend radius depends on factors such as the thickness and material of the flexible substrate, the number of conductive layers, and the presence of components near the bend area.
Stiffener Placement
Stiffeners are used in Rigid-Flex PCBs to provide support and stability to the flexible sections, especially in areas where components are mounted or where the board is subject to mechanical stress. Proper placement of stiffeners is crucial for ensuring the reliability and durability of the Rigid-Flex PCB. Stiffeners should be placed strategically to minimize stress on the flexible sections and to prevent delamination or cracking.
Signal Integrity
Maintaining signal integrity is critical in Rigid-Flex PCBs, particularly in high-speed or high-frequency applications. Designers must consider factors such as impedance control, crosstalk, and electromagnetic interference (EMI) when routing signals across the rigid and flexible sections. Proper grounding, shielding, and signal routing techniques should be employed to minimize signal degradation and ensure reliable performance.
Thermal Management
Thermal management is another important consideration in Rigid-Flex PCB design. The flexible sections of the board may have limited ability to dissipate heat, which can lead to higher operating temperatures and reduced reliability. Designers must carefully place heat-generating components and incorporate appropriate thermal management techniques, such as heat sinks, thermal vias, or active cooling solutions, to ensure proper heat dissipation and maintain the board’s performance and longevity.
Future Trends in Rigid-Flex PCBs
Increasing Adoption in IoT Devices
As the Internet of Things (IoT) continues to grow, the demand for compact, flexible, and reliable electronic devices is increasing. Rigid-Flex PCBs are well-suited for IoT applications, as they enable the development of small, lightweight, and highly integrated devices that can be easily deployed in various environments. The adoption of Rigid-Flex PCBs in IoT devices is expected to increase significantly in the coming years.
Advancements in Materials and Manufacturing Processes
Ongoing advancements in materials and manufacturing processes are driving the development of more sophisticated and high-performance Rigid-Flex PCBs. New materials with improved electrical, thermal, and mechanical properties are being developed to meet the evolving requirements of advanced applications. Additionally, improvements in manufacturing technologies, such as 3D printing and laser drilling, are enabling the production of more complex and precise Rigid-Flex PCB designs.
Integration of Embedded Components
The integration of embedded components, such as resistors, capacitors, and active devices, into Rigid-Flex PCBs is an emerging trend that offers several benefits. Embedded components can further reduce the size and weight of the board, improve signal integrity, and enhance overall system performance. As the technology matures, the adoption of embedded components in Rigid-Flex PCBs is expected to increase, enabling the development of more compact and highly integrated electronic devices.
Frequently Asked Questions (FAQ)
1. What is the difference between a Rigid-Flex PCB and a traditional rigid PCB?
A Rigid-Flex PCB combines both rigid and flexible sections in a single board, while a traditional rigid PCB consists entirely of rigid material. Rigid-Flex PCBs offer increased design flexibility, improved reliability, and reduced space requirements compared to traditional rigid PCBs.
2. What are the main benefits of using Rigid-Flex PCBs?
The main benefits of using Rigid-Flex PCBs include:
– Space savings due to more compact and efficient layouts
– Improved reliability and durability, with reduced risk of connector failures
– Increased design flexibility, allowing for complex shapes and multiple functions in a single board
– Reduced assembly time and costs, with fewer connectors and cables required
3. In which industries are Rigid-Flex PCBs commonly used?
Rigid-Flex PCBs are commonly used in various industries, including:
– Aerospace and defense, for applications such as avionics and military equipment
– Automotive, for infotainment systems, ADAS, and ECUs
– Medical devices, for wearable monitors, implantable devices, and diagnostic equipment
– Consumer electronics, for smartphones, tablets, smartwatches, and virtual reality headsets
4. What are the key design considerations for Rigid-Flex PCBs?
When designing Rigid-Flex PCBs, some key considerations include:
– Bend radius, to ensure the flexible sections can be bent without causing damage or affecting performance
– Stiffener placement, to provide support and stability to the flexible sections
– Signal integrity, to maintain reliable performance in high-speed or high-frequency applications
– Thermal management, to dissipate heat effectively and maintain the board’s performance and longevity
5. What are some future trends in Rigid-Flex PCBs?
Some future trends in Rigid-Flex PCBs include:
– Increasing adoption in IoT devices, driven by the demand for compact, flexible, and reliable electronic devices
– Advancements in materials and manufacturing processes, enabling the production of more sophisticated and high-performance boards
– Integration of embedded components, offering further size reduction and improved system performance
Conclusion
Rigid-Flex PCBs offer a unique combination of benefits, including space savings, improved reliability, increased design flexibility, and reduced assembly time and costs. These advantages have led to the widespread adoption of Rigid-Flex PCBs across various industries, such as aerospace, automotive, medical devices, and consumer electronics.
As technology continues to advance, the demand for more compact, flexible, and high-performance electronic devices will drive the ongoing development and adoption of Rigid-Flex PCBs. Designers and manufacturers must stay informed about the latest trends, materials, and manufacturing processes to create innovative and reliable Rigid-Flex PCB solutions that meet the evolving needs of their customers.
By understanding the key features, advantages, applications, and design considerations of Rigid-Flex PCBs, engineers and decision-makers can make informed choices when selecting the most appropriate PCB technology for their projects. As the electronics industry continues to push the boundaries of what is possible, Rigid-Flex PCBs will undoubtedly play a crucial role in shaping the future of electronic devices.
0 Comments