Understanding PCB Substrates
A PCB substrate is the insulating material that forms the base of a printed circuit board. It provides a stable and non-conductive surface for the copper traces and components to be placed on. The substrate also plays a vital role in determining the overall performance and reliability of the PCB.
Key Properties of PCB Substrates
When selecting a PCB substrate, several key properties need to be considered:
-
Dielectric Constant: The dielectric constant is a measure of a material’s ability to store electrical energy. A lower dielectric constant is desirable for high-frequency applications, as it reduces signal loss and improves signal integrity.
-
Thermal Conductivity: Thermal conductivity refers to a material’s ability to dissipate heat. A substrate with high thermal conductivity helps in efficiently removing heat from the components, preventing overheating and ensuring reliable operation.
-
Mechanical Strength: The substrate must possess sufficient mechanical strength to withstand the stresses encountered during manufacturing, assembly, and operation. It should resist warping, twisting, and cracking under various environmental conditions.
-
Moisture Resistance: The substrate should have low moisture absorption to prevent delamination and maintain its dimensional stability. Excessive moisture absorption can lead to the degradation of the PCB’s electrical and mechanical properties.
-
Flame Retardancy: In many applications, especially in the aerospace and automotive industries, the substrate must meet stringent flame retardancy requirements to ensure safety and compliance with industry standards.
Common Types of PCB Substrates
There are several types of PCB substrates available, each with its own unique properties and applications. Let’s explore some of the most common ones:
FR-4
FR-4 (Flame Retardant 4) is the most widely used PCB substrate material. It is a composite material made of woven fiberglass cloth impregnated with an epoxy resin. FR-4 offers a good balance of electrical, mechanical, and thermal properties, making it suitable for a wide range of applications.
Property | Value |
---|---|
Dielectric Constant | 4.2 – 4.5 |
Thermal Conductivity | 0.3 W/mK |
Tg (Glass Transition Temperature) | 130°C – 140°C |
Moisture Absorption | 0.1% – 0.2% |
Flame Retardancy | UL 94 V-0 |
High Tg FR-4
High Tg FR-4 is a variant of the standard FR-4 substrate, designed for applications that require higher thermal stability. It has a higher glass transition temperature (Tg) of 170°C – 180°C, which allows it to withstand higher operating temperatures without deformation or degradation.
Property | Value |
---|---|
Dielectric Constant | 4.2 – 4.5 |
Thermal Conductivity | 0.3 W/mK |
Tg (Glass Transition Temperature) | 170°C – 180°C |
Moisture Absorption | 0.1% – 0.2% |
Flame Retardancy | UL 94 V-0 |
Polyimide
Polyimide is a high-performance substrate material known for its excellent thermal stability, chemical resistance, and mechanical strength. It is often used in demanding applications such as aerospace, military, and high-temperature electronics.
Property | Value |
---|---|
Dielectric Constant | 3.4 – 3.5 |
Thermal Conductivity | 0.2 W/mK |
Tg (Glass Transition Temperature) | 250°C – 260°C |
Moisture Absorption | 0.4% – 0.8% |
Flame Retardancy | UL 94 V-0 |
Rogers Materials
Rogers materials are a family of high-frequency substrates designed for RF and microwave applications. They offer low dielectric loss, high thermal conductivity, and excellent dimensional stability. Some popular Rogers materials include:
- Rogers RO4000 Series
- Rogers RT/duroid
- Rogers TMM
Property | RO4003C | RT/duroid 5880 | TMM4 |
---|---|---|---|
Dielectric Constant | 3.38 | 2.20 | 4.5 |
Dissipation Factor | 0.0027 | 0.0009 | 0.002 |
Thermal Conductivity | 0.71 W/mK | 0.20 W/mK | 0.7 W/mK |
Tg (Glass Transition Temperature) | >280°C | >260°C | >250°C |
Aluminum
Aluminum substrates, also known as Metal Core PCBs (MCPCBs), are used in applications that require high thermal dissipation. The aluminum core provides an excellent heat spreading capability, allowing for efficient cooling of high-power components.
Property | Value |
---|---|
Thermal Conductivity | 150 W/mK – 200 W/mK |
Dielectric Constant | 4.5 – 4.7 |
Tg (Glass Transition Temperature) | N/A |
Moisture Absorption | N/A |
Flame Retardancy | UL 94 V-0 |
PCB Substrate Selection Considerations
When choosing a PCB substrate for a particular application, several factors need to be taken into account:
-
Electrical Requirements: Consider the dielectric constant, dissipation factor, and dielectric strength of the substrate based on the desired electrical performance of the PCB.
-
Thermal Management: Evaluate the thermal conductivity and glass transition temperature (Tg) of the substrate to ensure it can effectively dissipate heat generated by the components.
-
Mechanical Stress: Assess the mechanical strength and dimensional stability of the substrate to withstand the stresses encountered during manufacturing, assembly, and operation.
-
Environmental Conditions: Take into account the operating environment of the PCB, including temperature range, humidity, and chemical exposure, to select a substrate that can withstand these conditions.
-
Cost: Consider the cost implications of different substrate materials, balancing performance requirements with budget constraints.
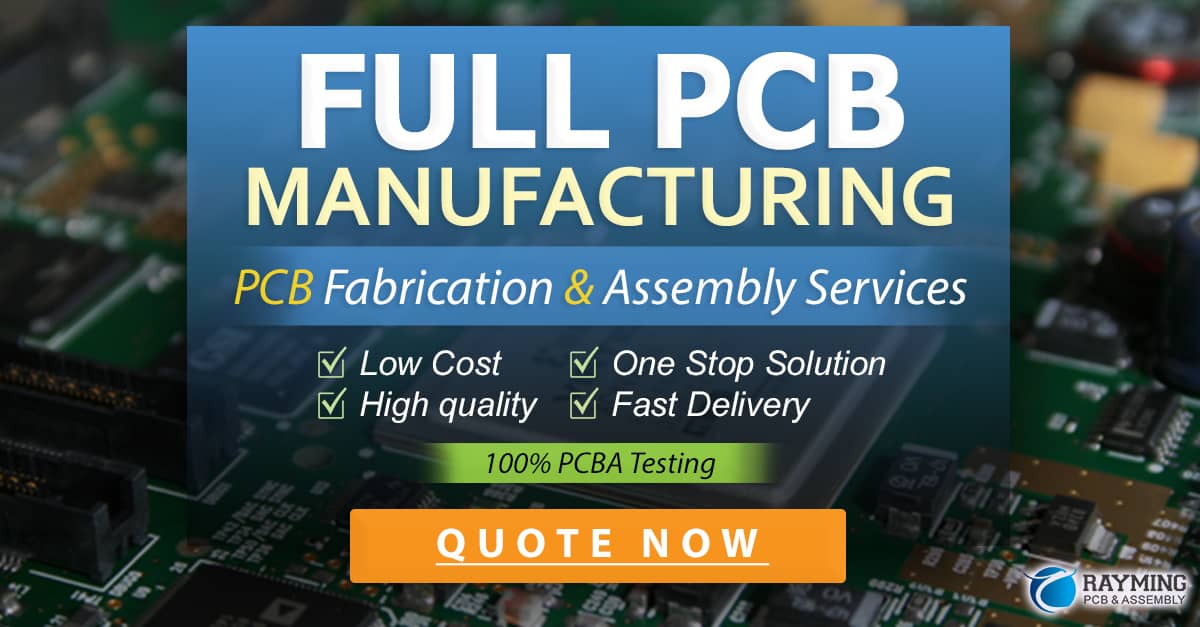
PCB Substrate Manufacturing Process
The manufacturing process of PCB substrates involves several steps:
-
Raw Material Preparation: The raw materials, such as fiberglass cloth and resin, are prepared and mixed according to the desired composition.
-
Impregnation: The fiberglass cloth is impregnated with the resin mixture to create a prepreg (pre-impregnated) material.
-
Lamination: Multiple layers of prepreg are stacked together and sandwiched between copper foils. The stack is then subjected to high pressure and temperature in a lamination press to fuse the layers together.
-
Curing: The laminated board undergoes a curing process to fully crosslink the resin and achieve the desired mechanical and electrical properties.
-
Copper Etching: The copper foils on the outer layers of the board are etched to create the desired circuit patterns.
-
Drilling: Holes are drilled through the board to accommodate component leads and vias.
-
Surface Finishing: The exposed copper surfaces are coated with a protective finish, such as solder mask or plating, to prevent oxidation and facilitate soldering.
Future Trends in PCB Substrates
As electronic devices continue to evolve, the demand for advanced PCB substrates is growing. Some of the emerging trends in PCB substrate technology include:
-
High-Frequency Materials: With the increasing adoption of 5G and millimeter-wave technologies, there is a growing demand for substrates that offer low dielectric loss and high signal integrity at high frequencies.
-
Embedded Components: Embedding passive components, such as resistors and capacitors, within the substrate itself helps in reducing the board size and improving signal integrity.
-
3D Printing: Additive manufacturing techniques, such as 3D printing, are being explored for the fabrication of PCB substrates with complex geometries and customized properties.
-
Eco-Friendly Materials: There is a growing focus on developing environmentally friendly substrate materials that are halogen-free, recyclable, and comply with RoHS (Restriction of Hazardous Substances) regulations.
Frequently Asked Questions (FAQ)
-
What is the most commonly used PCB substrate material?
FR-4 is the most widely used PCB substrate material due to its good balance of electrical, mechanical, and thermal properties, as well as its cost-effectiveness. -
What is the difference between FR-4 and High Tg FR-4?
High Tg FR-4 has a higher glass transition temperature (Tg) compared to standard FR-4, which allows it to withstand higher operating temperatures without deformation or degradation. -
What are the advantages of using an aluminum substrate?
Aluminum substrates, also known as Metal Core PCBs (MCPCBs), offer excellent thermal dissipation capabilities, making them suitable for applications with high-power components that generate significant heat. -
How do I choose the right PCB substrate for my application?
When selecting a PCB substrate, consider factors such as electrical requirements, thermal management, mechanical stress, environmental conditions, and cost. Evaluate the properties of different substrate materials and choose the one that best meets your specific application needs. -
What are the future trends in PCB substrate technology?
Some of the emerging trends in PCB substrate technology include the development of high-frequency materials for 5G and millimeter-wave applications, embedded components within the substrate, 3D printing of substrates, and the use of eco-friendly materials that comply with environmental regulations.
Conclusion
PCB substrates play a crucial role in the performance, reliability, and functionality of printed circuit boards. Understanding the types, properties, and applications of different substrate materials is essential for selecting the right substrate for a given project. From the widely used FR-4 to high-performance materials like polyimide and Rogers, each substrate offers unique advantages and considerations.
As technology advances and new applications emerge, the development of innovative PCB substrate solutions will continue to drive the electronics industry forward. By staying informed about the latest trends and advancements in PCB substrate technology, engineers and designers can make informed decisions and create high-quality, reliable electronic products.
0 Comments