Understanding the Basics of PCB Bare Boards
What is a PCB?
A Printed Circuit Board, or PCB, is a board made of non-conductive material, such as fiberglass, with copper traces printed on it to connect the various components in an electronic device. These boards are used in almost all electronic devices, from simple calculators to complex computers and smartphones.
The Role of PCB Bare Boards in Electronics Manufacturing
PCB bare boards are the starting point for the assembly of electronic devices. They provide the foundation upon which components such as resistors, capacitors, and integrated circuits are soldered. The copper traces on the board act as the wiring that connects these components together to create a functional electronic circuit.
Types of PCB Bare Boards
There are several types of PCB bare boards, each with its own unique characteristics and applications:
Type | Description | Applications |
---|---|---|
Single-sided | Copper traces on one side of the board | Simple, low-cost devices |
Double-sided | Copper traces on both sides of the board | More complex devices requiring higher component density |
Multi-layer | Multiple layers of copper traces separated by insulating layers | High-density, complex devices such as smartphones and computers |
Flexible | Made of flexible materials such as polyimide | Devices requiring flexibility, such as wearable electronics |
Rigid-Flex | Combination of rigid and flexible sections | Devices requiring both stability and flexibility |
The Manufacturing Process of PCB Bare Boards
Designing the PCB
The first step in manufacturing a PCB bare board is designing the circuit. This is typically done using specialized software called Electronic Design Automation (EDA) tools. The designer creates a schematic diagram of the circuit, which shows how the various components are connected. They then use this schematic to create a layout of the PCB, which shows the physical placement of the components and the routing of the copper traces.
Printing the Circuit Pattern
Once the design is complete, the next step is to print the circuit pattern onto the PCB substrate. This is typically done using a photolithographic process:
- The PCB substrate is coated with a light-sensitive material called photoresist.
- The circuit pattern is printed onto a transparency film.
- The transparency is placed on top of the photoresist-coated PCB, and the board is exposed to UV light.
- The areas of the photoresist that were exposed to light become soluble and are washed away, leaving the circuit pattern exposed.
Etching the Copper
After the circuit pattern has been printed, the next step is to etch away the unwanted copper, leaving only the copper traces that form the circuit:
- The PCB is immersed in an etchant solution, typically ferric chloride or ammonium persulfate.
- The etchant dissolves the copper that is not protected by the photoresist.
- The remaining photoresist is then stripped away, leaving the copper traces.
Drilling and Plating
The final steps in manufacturing a PCB bare board involve drilling holes for through-hole components and applying a protective finish to the copper traces:
- Holes are drilled in the board where through-hole components will be inserted.
- A thin layer of copper is electroplated onto the walls of the holes to create electrical connections between the layers of the board.
- A protective finish, such as solder mask or silkscreen, is applied to the board to protect the copper traces and prevent short circuits.
Quality Control and Testing of PCB Bare Boards
Visual Inspection
The first step in quality control is a visual inspection of the PCB bare board. This involves checking for defects such as:
- Incomplete or overetched traces
- Short circuits between traces
- Drill holes that are too small, too large, or misaligned
- Contamination or debris on the board surface
Electrical Testing
After visual inspection, the PCB bare board undergoes electrical testing to ensure that all the connections are functioning correctly. This typically involves using a test fixture or flying probe tester to check the continuity and resistance of each trace and connection.
Microsectioning
For critical applications, such as aerospace or medical devices, PCB bare boards may undergo microsectioning. This involves cutting a cross-section of the board and examining it under a microscope to check for internal defects such as:
- Delamination between layers
- Voids or cracks in the copper plating
- Insufficient or excessive copper thickness
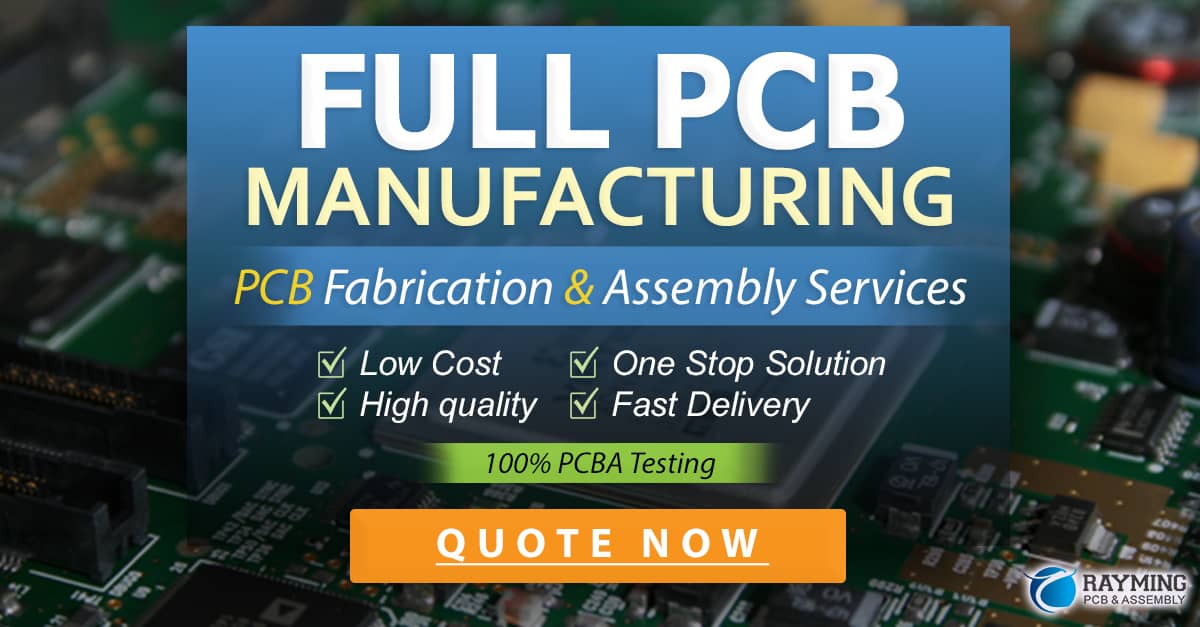
Applications of PCB Bare Boards
Consumer Electronics
PCB bare boards are used in virtually all consumer electronic devices, from smartphones and laptops to televisions and gaming consoles. These boards are typically multi-layer and high-density to accommodate the large number of components and complex circuitry required.
Industrial Electronics
PCB bare boards are also used extensively in industrial electronics, such as control systems, automation equipment, and test and measurement devices. These boards often require special features such as high-current traces, heavy copper plating, or impedance control to meet the demanding requirements of industrial applications.
Medical Devices
PCB bare boards are critical components in many medical devices, from diagnostic equipment to implantable devices such as pacemakers and insulin pumps. These boards must meet stringent quality and reliability standards to ensure patient safety and device performance.
Automotive Electronics
Modern vehicles contain a large number of electronic systems, from engine control modules to infotainment systems. PCB bare boards used in automotive applications must be able to withstand harsh environmental conditions such as extreme temperatures, vibration, and moisture.
Aerospace and Defense
PCB bare boards used in aerospace and defense applications must meet the highest standards of reliability and performance. These boards are often subject to rigorous testing and certification processes to ensure they can withstand the extreme conditions encountered in space and military environments.
Future Trends in PCB Bare Board Technology
Miniaturization
As electronic devices continue to shrink in size, PCB bare boards must also become smaller and more densely packed. This trend towards miniaturization is driving the development of new technologies such as embedded components, where passive components are built directly into the PCB substrate.
High-Speed and High-Frequency
The demand for faster data transfer rates and higher bandwidth is driving the development of PCB bare boards that can support high-speed and high-frequency signals. This requires the use of advanced materials such as low-loss dielectrics and special design techniques such as controlled impedance and differential signaling.
Sustainability and Environmental Responsibility
As awareness of the environmental impact of electronics manufacturing grows, there is an increasing focus on developing PCB bare boards that are more sustainable and environmentally friendly. This includes the use of lead-free materials, halogen-free flame retardants, and recyclable substrates.
Additive Manufacturing
Additive manufacturing, also known as 3D printing, is a promising new technology for the production of PCB bare boards. This approach allows for the creation of complex, three-dimensional structures that would be difficult or impossible to achieve with traditional subtractive manufacturing methods.
Frequently Asked Questions (FAQ)
-
What is the difference between a PCB and a PCB bare board?
A PCB bare board is the foundation of a printed circuit board before any components are attached. It consists of the non-conductive substrate with the copper traces that form the electrical connections. A complete PCB includes the bare board with all the components soldered onto it. -
What materials are PCB bare boards made of?
PCB bare boards are typically made of a non-conductive substrate such as fiberglass, composite epoxy, or other laminate materials. The substrate is then coated with a thin layer of copper foil, which is etched to form the electrical traces. -
How are PCB bare boards manufactured?
PCB bare boards are manufactured using a photolithographic process. The circuit pattern is first printed onto a transparency film, which is then used to expose a photoresist-coated copper-clad board. The exposed areas of photoresist are washed away, and the unwanted copper is etched, leaving the desired circuit traces. -
What are the different types of PCB bare boards?
There are several types of PCB bare boards, including single-sided, double-sided, multi-layer, flexible, and rigid-flex. Each type has its own unique characteristics and applications. -
What are the challenges in PCB bare board manufacturing?
Some of the challenges in PCB bare board manufacturing include achieving high precision and accuracy in the printing and etching processes, maintaining consistent quality across large production runs, and keeping up with the ever-increasing demand for smaller, faster, and more complex boards.
Conclusion
PCB bare boards are the unsung heroes of the electronics industry. They provide the foundation upon which all electronic devices are built, from simple calculators to complex supercomputers. The manufacturing process for PCB bare boards is a complex and precise one, involving multiple steps and rigorous quality control measures.
As electronic devices continue to evolve and become more sophisticated, so too must the PCB bare boards that power them. Trends such as miniaturization, high-speed and high-frequency operation, sustainability, and additive manufacturing are shaping the future of PCB bare board technology.
Despite the challenges, the PCB bare board industry continues to innovate and adapt to meet the ever-changing needs of the electronics market. As long as there is demand for newer, faster, and more powerful electronic devices, there will be a need for the PCB bare boards that make them possible.
0 Comments