Introduction to Buried Vias
A buried via is a type of interconnect used in printed circuit board (PCB) design to connect different layers within the middle layers of the board, rather than connecting to the outer layers. Unlike through-hole vias which go through the entire board from top to bottom, buried vias are embedded within the inner layers and are not visible from the outer surfaces of the PCB.
Key Characteristics of Buried Vias
- Connect inner layers of a multi-layer PCB
- Do not extend to the top or bottom layers
- Require additional manufacturing steps compared to through-hole vias
- Enable higher density interconnects and more compact PCB designs
- Typically used in high-density interconnect (HDI) PCB designs
Advantages of Using Buried Vias
Space Savings and Increased Routing Density
One of the main advantages of using buried vias in PCB design is the ability to save space on the outer layers and increase the routing density. Since buried vias do not extend to the top or bottom layers, they free up valuable real estate that can be used for other components or additional routing traces. This is particularly beneficial in high-density designs where space is at a premium.
Improved Signal Integrity
Buried vias can also contribute to improved signal integrity in PCB designs. By providing shorter, more direct paths between layers, buried vias can reduce the overall length of interconnects, which in turn minimizes signal reflections, crosstalk, and other signal integrity issues. This is especially important in high-speed designs where maintaining signal integrity is critical.
Enhanced Mechanical Strength
Another advantage of buried vias is enhanced mechanical strength of the PCB. Since buried vias are embedded within the inner layers and do not extend to the outer surfaces, they are less susceptible to mechanical stress and damage compared to through-hole vias. This can lead to improved reliability and durability of the PCB, particularly in applications where the board may be subjected to physical stress or harsh environmental conditions.
Manufacturing Process for Buried Vias
Multi-Layer PCB Fabrication
The manufacturing process for buried vias is more complex compared to through-hole vias and involves additional steps in the multi-layer PCB fabrication process. The basic steps in creating a PCB with buried vias are as follows:
- Inner layer fabrication: The inner layers of the PCB are fabricated with the necessary circuitry and buried via holes.
- Lamination: The inner layers are laminated together with prepreg (pre-impregnated) material and copper foil.
- Drilling: Through-holes and blind vias (if any) are drilled through the laminated stackup.
- Plating: The drilled holes and buried vias are plated with copper to create electrical connections.
- Outer layer processing: The outer layers of the PCB are processed with the necessary circuitry and finishes.
Laser Drilling for Buried Vias
One of the key technologies used in the manufacturing of buried vias is laser drilling. Unlike mechanical drilling which is used for through-holes, laser drilling allows for the creation of smaller, more precise via holes in the inner layers of the PCB. Laser drilling uses a focused beam of light to vaporize the dielectric material and create the via holes, offering several advantages over mechanical drilling:
- Smaller via sizes: Laser drilling can create via holes as small as 50 microns in diameter, enabling higher density interconnects.
- Improved accuracy: Laser drilling offers higher precision and accuracy compared to mechanical drilling, reducing the risk of misaligned or incomplete vias.
- Faster processing: Laser drilling is a high-speed process that can create a large number of via holes in a short amount of time, improving manufacturing efficiency.
Drilling Method | Minimum Via Diameter | Accuracy | Speed |
---|---|---|---|
Mechanical Drilling | 200 microns | Moderate | Moderate |
Laser Drilling | 50 microns | High | High |
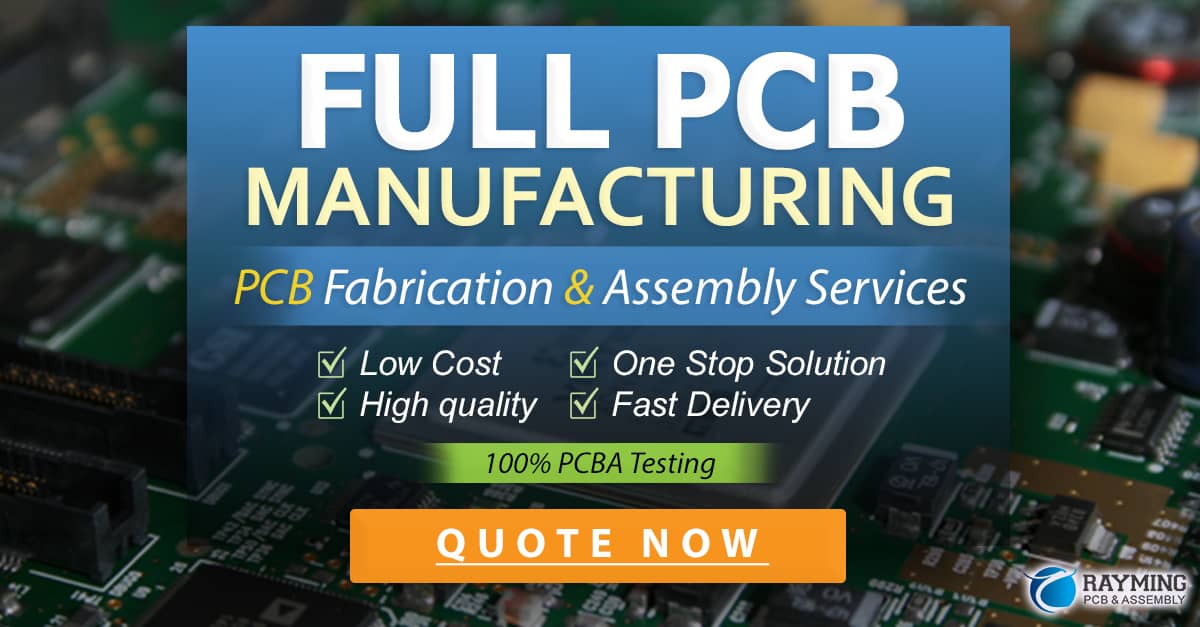
Design Considerations for Buried Vias
Via Sizes and Spacing
When designing a PCB with buried vias, it is important to consider the sizes and spacing of the vias to ensure manufacturability and reliability. The minimum via size and spacing will depend on the capabilities of the PCB manufacturer and the specific requirements of the design. Some general guidelines for buried via sizes and spacing include:
- Minimum via diameter: 0.1 mm to 0.2 mm (4 to 8 mils)
- Minimum via pad diameter: 0.25 mm to 0.3 mm (10 to 12 mils)
- Minimum via-to-via spacing: 0.25 mm to 0.3 mm (10 to 12 mils)
- Minimum via-to-trace spacing: 0.2 mm to 0.25 mm (8 to 10 mils)
It is always recommended to consult with the PCB manufacturer for their specific design rules and capabilities regarding buried vias.
Stackup and Layer Arrangement
The arrangement of layers and the overall stackup design are crucial considerations when using buried vias in a PCB. The placement of buried vias within the stackup will depend on the interconnect requirements of the design and the desired signal paths. Some common practices for buried via stackup design include:
- Placing buried vias symmetrically within the stackup to balance the mechanical stress and prevent warping.
- Avoiding buried vias in layers adjacent to the outer layers to minimize the risk of drilling or plating issues.
- Using a larger number of thinner layers to accommodate more buried vias and increase routing density.
- Considering the dielectric constant and thickness of the laminate materials to control impedance and signal integrity.
Layer | Material | Thickness (mm) | Dielectric Constant |
---|---|---|---|
Top Layer | FR-4 | 0.1 | 4.3 |
Inner Layer 1 | FR-4 | 0.2 | 4.3 |
Inner Layer 2 (with buried vias) | FR-4 | 0.2 | 4.3 |
Inner Layer 3 | FR-4 | 0.2 | 4.3 |
Bottom Layer | FR-4 | 0.1 | 4.3 |
Applications of Buried Vias
High-Density Interconnect (HDI) PCBs
Buried vias are commonly used in high-density interconnect (HDI) PCB designs, where the goal is to maximize the routing density and minimize the overall size of the board. HDI PCBs typically feature a large number of buried and blind vias to create complex interconnect structures within a limited space. Some examples of HDI PCB applications that rely on buried vias include:
- Smartphones and mobile devices
- Wearable electronics
- Miniature medical devices
- High-performance computing modules
High-Speed Digital Designs
Buried vias are also used in high-speed digital PCB designs to optimize signal paths and minimize signal integrity issues. By using buried vias to create shorter, more direct interconnects between layers, designers can reduce the overall signal path length and minimize the impact of impedance discontinuities, reflections, and crosstalk. This is particularly important in applications such as:
- High-speed networking equipment
- Radar and RF systems
- High-performance data acquisition systems
- Automotive electronics
Challenges and Limitations of Buried Vias
Manufacturing Complexity and Cost
One of the main challenges associated with using buried vias in PCB design is the increased manufacturing complexity and cost compared to through-hole vias. The additional steps involved in creating buried vias, such as laser drilling and multiple lamination cycles, can add significant time and expense to the PCB fabrication process. This can make buried vias less suitable for low-cost or high-volume production runs.
Reliability and Thermal Management
Another potential limitation of buried vias is the impact on reliability and thermal management of the PCB. Since buried vias are embedded within the inner layers and do not extend to the outer surfaces, they can be more susceptible to thermal stress and may have limited heat dissipation capabilities. This can be a concern in applications where the PCB is subjected to high temperatures or where effective thermal management is critical.
Design and Layout Challenges
Using buried vias in PCB design also presents some challenges in terms of design and layout. The placement and routing of buried vias must be carefully considered to ensure proper connectivity and signal integrity while avoiding potential manufacturing issues. Designers must also be aware of the specific design rules and constraints associated with buried vias, such as minimum sizes, spacing, and layer requirements, which can add complexity to the design process.
Frequently Asked Questions (FAQ)
What is the difference between a buried via and a blind via?
A buried via connects inner layers of a PCB without extending to the outer layers, while a blind via connects an outer layer to one or more inner layers without going through the entire board.
Can buried vias be used in single-layer PCBs?
No, buried vias are only applicable in multi-layer PCB designs since they connect inner layers within the board.
What is the typical size range for buried vias?
The typical size range for buried vias is 0.1 mm to 0.2 mm (4 to 8 mils) in diameter, although the specific size will depend on the capabilities of the PCB manufacturer and the requirements of the design.
Are buried vias more expensive than through-hole vias?
Yes, buried vias are generally more expensive than through-hole vias due to the additional manufacturing steps and complexity involved in their fabrication.
Can buried vias be repaired or reworked?
Repairing or reworking buried vias can be challenging since they are embedded within the inner layers of the PCB. In many cases, a buried via failure may require scrapping the entire board and starting over with a new fabrication run.
Conclusion
Buried vias are a powerful interconnect solution for multi-layer PCB designs, offering several advantages such as space savings, increased routing density, improved signal integrity, and enhanced mechanical strength. By embedding vias within the inner layers of the board, designers can create more compact and efficient interconnect structures that are well-suited for high-density and high-speed applications.
However, using buried vias also presents some challenges and limitations, including increased manufacturing complexity and cost, potential reliability and thermal management issues, and additional design and layout considerations. It is important for designers to carefully weigh the benefits and drawbacks of buried vias and to work closely with PCB manufacturers to ensure the successful implementation of these interconnects in their designs.
As PCB technology continues to evolve and the demand for more complex and compact electronic devices grows, buried vias will likely play an increasingly important role in enabling the next generation of high-performance and highly integrated PCB designs.
0 Comments