Introduction
The manufacturing of medical equipment is a complex and highly regulated process that requires adherence to strict standards and regulations to ensure the safety and effectiveness of the devices. One critical component of medical equipment is the printed circuit board (PCB) assembly, which plays a vital role in the functioning of the device. In this article, we will explore the key challenges of medical equipment manufacturing and how the standards and regulations apply to medical device PCB assemblies.
Key Challenges in Medical Equipment Manufacturing
1. Regulatory Compliance
One of the most significant challenges in medical equipment manufacturing is ensuring compliance with the various regulatory requirements. Medical devices are subject to strict regulations set by government agencies such as the Food and Drug Administration (FDA) in the United States and the European Medicines Agency (EMA) in Europe. These regulations cover all aspects of the device, from design and manufacturing to labeling and post-market surveillance.
2. Quality Control
Another major challenge in medical equipment manufacturing is maintaining high levels of quality control throughout the production process. Medical devices must meet stringent quality standards to ensure their safety and effectiveness. This requires rigorous testing and inspection at every stage of the manufacturing process, from raw materials to finished products.
3. Supply Chain Management
Medical equipment manufacturers often rely on a complex network of suppliers and subcontractors to produce the various components of their devices. Managing this supply chain can be a significant challenge, particularly when dealing with suppliers located in different countries with varying regulatory requirements and quality standards.
4. Rapid Technological Advancements
The medical device industry is constantly evolving, with new technologies and innovations emerging at a rapid pace. Keeping up with these advancements can be a challenge for manufacturers, who must continually invest in research and development to stay competitive.
5. Cost Pressures
Finally, medical equipment manufacturers face significant cost pressures, particularly in an increasingly competitive global market. Balancing the need to produce high-quality, safe, and effective devices with the need to keep costs down can be a difficult challenge.
PCB Regulations for Medical Devices
PCB assemblies are a critical component of many medical devices, and as such, they are subject to specific regulations and standards. Here are some of the key PCB regulations that apply to medical devices:
1. IPC Standards
The Association Connecting Electronics Industries (IPC) is a global trade association that develops standards for the electronics industry, including PCBs. The IPC has developed several standards specifically for medical device PCBs, including:
- IPC-6012 – Medical Devices Application Addendum to IPC-6012 Qualification and Performance Specification for Rigid Printed Boards
- IPC-6013 – Medical Devices Application Addendum to IPC-6013 Qualification and Performance Specification for Flexible Printed Boards
- IPC-6018 – Medical Device Application Addendum to IPC-6018 Microwave End Product Board Inspection and Test
These standards provide guidance on the design, fabrication, and testing of PCBs for medical devices to ensure their reliability and performance.
2. ISO 13485
ISO 13485 is an international standard that specifies requirements for a quality management system specific to the medical device industry. It is designed to ensure that medical device manufacturers consistently meet customer and regulatory requirements. PCB manufacturers that supply components for medical devices must comply with ISO 13485 requirements.
3. FDA Regulations
In the United States, medical devices are regulated by the FDA under the Federal Food, Drug, and Cosmetic Act. The FDA has established several regulations that apply to medical device PCBs, including:
- 21 CFR Part 820 – Quality System Regulation
- 21 CFR Part 11 – Electronic Records and Electronic Signatures
These regulations require medical device manufacturers to establish and maintain a quality management system that ensures the safety and effectiveness of their devices.
4. RoHS Directive
The Restriction of Hazardous Substances (RoHS) Directive is a European Union regulation that restricts the use of certain hazardous substances in electrical and electronic equipment, including PCBs. Medical devices are currently exempt from the RoHS Directive, but many manufacturers are voluntarily complying with the regulation to reduce the environmental impact of their products.
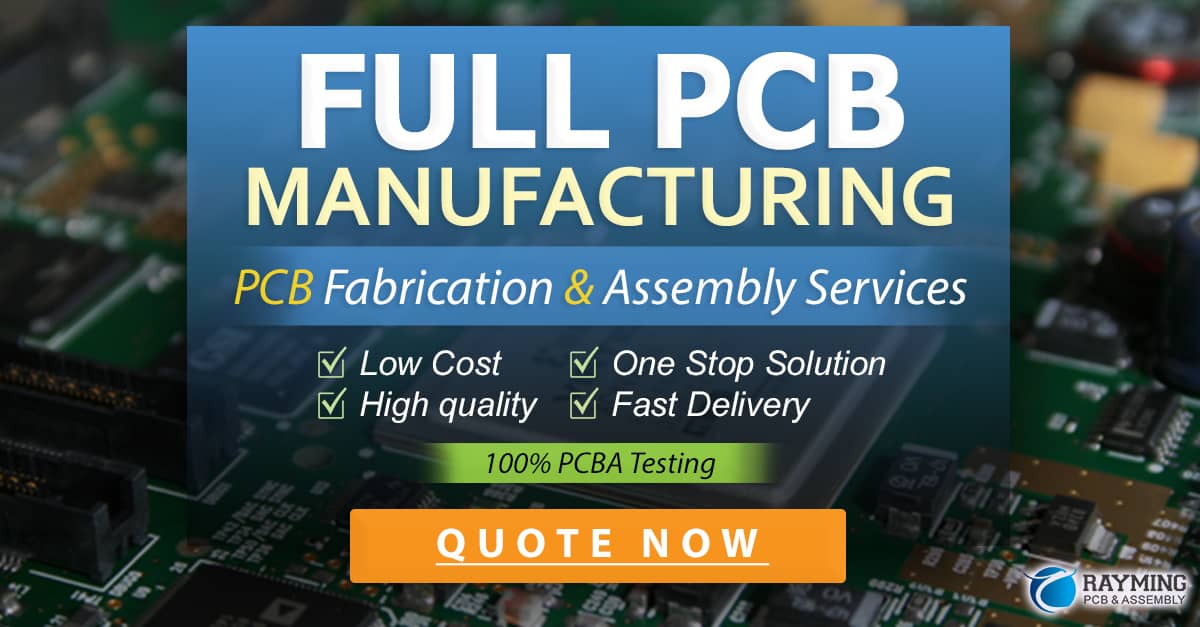
PCB Assembly Considerations for Medical Devices
When designing and manufacturing PCBs for medical devices, there are several key considerations that must be taken into account to ensure the safety and effectiveness of the device. Here are some of the most important PCB assembly considerations for medical devices:
1. Material Selection
The materials used in the construction of medical device PCBs must be carefully selected to ensure their biocompatibility and resistance to harsh environments. Common materials used in medical device PCBs include:
- FR-4: A flame-retardant epoxy laminate that is widely used in PCBs due to its excellent electrical and mechanical properties.
- Polyimide: A high-temperature, flexible material that is often used in medical device PCBs due to its biocompatibility and resistance to harsh chemicals and sterilization processes.
- Ceramic: A high-performance material that is often used in medical device PCBs due to its excellent thermal and electrical properties.
2. Cleanliness and Contamination Control
Medical device PCBs must be manufactured in a clean and controlled environment to prevent contamination that could compromise the safety and effectiveness of the device. PCB manufacturers must follow strict cleanliness and contamination control procedures, including:
- Using clean room facilities with HEPA filtration and positive air pressure
- Implementing strict handling and storage procedures to prevent contamination
- Using specialized cleaning agents and processes to remove contaminants from the PCB surface
3. Sterilization Compatibility
Many medical devices must be sterilized before use to prevent infection and ensure patient safety. PCBs used in these devices must be designed and manufactured to withstand the sterilization process without degradation or damage. Common sterilization methods used for medical devices include:
- Ethylene oxide (EtO) gas sterilization
- Gamma radiation sterilization
- Steam sterilization (autoclaving)
PCB manufacturers must work closely with medical device designers to ensure that the PCB materials and components are compatible with the chosen sterilization method.
4. Reliability and Durability
Medical devices are often used in critical applications where failure could have serious consequences for patient health and safety. As such, medical device PCBs must be designed and manufactured to ensure high levels of reliability and durability. This includes:
- Using high-quality, reliable components and materials
- Implementing robust design practices to minimize the risk of failure
- Conducting extensive testing and validation to ensure the PCB meets performance and reliability requirements
5. Traceability and Documentation
Medical device manufacturers must maintain detailed documentation and traceability throughout the PCB assembly process to ensure compliance with regulatory requirements and facilitate problem-solving in the event of a device failure. This includes:
- Maintaining detailed records of all materials, components, and processes used in PCB assembly
- Implementing unique device identification (UDI) labeling to facilitate traceability
- Conducting failure mode and effects analysis (FMEA) to identify potential failure modes and implement corrective actions
FAQs
1. What is the difference between IPC and ISO standards for medical device PCBs?
IPC standards are specific to the electronics industry and provide detailed guidance on the design, fabrication, and testing of PCBs for medical devices. ISO 13485, on the other hand, is a quality management system standard that applies to the entire medical device manufacturing process, including PCB assembly.
2. Are medical devices exempt from the RoHS Directive?
Yes, medical devices are currently exempt from the RoHS Directive. However, many medical device manufacturers are voluntarily complying with the regulation to reduce the environmental impact of their products.
3. What is the purpose of clean room facilities in medical device PCB assembly?
Clean room facilities are used in medical device PCB assembly to prevent contamination that could compromise the safety and effectiveness of the device. These facilities have HEPA filtration and positive air pressure to minimize the risk of airborne contaminants.
4. What are some common sterilization methods used for medical devices?
Common sterilization methods used for medical devices include ethylene oxide (EtO) gas sterilization, gamma radiation sterilization, and steam sterilization (autoclaving). PCBs used in medical devices must be designed and manufactured to withstand the chosen sterilization method without degradation or damage.
5. Why is traceability important in medical device PCB assembly?
Traceability is important in medical device PCB assembly to ensure compliance with regulatory requirements and facilitate problem-solving in the event of a device failure. Manufacturers must maintain detailed records of all materials, components, and processes used in PCB assembly and implement unique device identification (UDI) labeling to facilitate traceability.
Conclusion
The manufacturing of medical equipment is a complex and highly regulated process that requires adherence to strict standards and regulations to ensure the safety and effectiveness of the devices. PCB assemblies are a critical component of many medical devices and are subject to specific regulations and standards, including IPC standards, ISO 13485, FDA regulations, and the RoHS Directive.
When designing and manufacturing PCBs for medical devices, there are several key considerations that must be taken into account, including material selection, cleanliness and contamination control, sterilization compatibility, reliability and durability, and traceability and documentation.
By understanding and adhering to these regulations and standards, medical device manufacturers can ensure that their products are safe, effective, and compliant with regulatory requirements. This ultimately helps to improve patient outcomes and advance the field of medical technology.
0 Comments