Introduction to PCB Aluminum Thermal Conductivity
Printed Circuit Boards (PCBs) are essential components in modern electronic devices. They provide a platform for mounting and interconnecting electronic components, allowing for the efficient transfer of electrical signals. However, as electronic devices become more compact and powerful, managing heat dissipation becomes a critical challenge. This is where PCB aluminum thermal conductivity comes into play.
PCB aluminum thermal conductivity refers to the ability of aluminum to conduct heat away from the electronic components mounted on the PCB. Aluminum is often used as a substrate material for PCBs due to its excellent thermal conductivity properties. By effectively dissipating heat, aluminum helps to maintain the optimal operating temperature of electronic components, ensuring their reliability and longevity.
In this article, we will explore the key factors that influence PCB aluminum thermal conductivity. Understanding these factors is crucial for designers and manufacturers to optimize the thermal management of PCBs and ensure the overall performance and reliability of electronic devices.
Factors Affecting PCB Aluminum Thermal Conductivity
1. Aluminum Alloy Composition
The composition of the aluminum alloy used in PCBs plays a significant role in determining its thermal conductivity. Different aluminum alloys have varying thermal conductivity values based on their chemical composition and manufacturing process.
Some commonly used aluminum alloys for PCBs include:
Alloy | Thermal Conductivity (W/mK) |
---|---|
1050 | 229 |
1100 | 222 |
3003 | 193 |
5052 | 138 |
6061 | 167 |
As seen from the table, the thermal conductivity values vary among different aluminum alloys. Alloys with higher purity, such as 1050 and 1100, generally exhibit higher thermal conductivity compared to alloys with more alloying elements, like 5052 and 6061.
When selecting an aluminum alloy for PCBs, designers must consider the specific thermal requirements of the application and choose an alloy that provides the desired balance between thermal conductivity and other mechanical properties.
2. Aluminum Thickness
The thickness of the aluminum substrate used in PCBs also influences its thermal conductivity. Thicker aluminum substrates provide a larger cross-sectional area for heat conduction, allowing for more efficient heat dissipation.
The relationship between aluminum thickness and thermal conductivity can be expressed using the following equation:
Q = k × A × (T1 - T2) / L
Where:
– Q is the rate of heat transfer (in watts)
– k is the thermal conductivity of aluminum (in W/mK)
– A is the cross-sectional area of the aluminum substrate (in m^2)
– T1 and T2 are the temperatures at the two ends of the aluminum substrate (in Kelvin)
– L is the thickness of the aluminum substrate (in meters)
From the equation, it is evident that increasing the thickness (L) of the aluminum substrate directly enhances the rate of heat transfer (Q), assuming all other factors remain constant.
However, it is important to note that increasing the aluminum thickness also adds weight and cost to the PCB. Designers must strike a balance between thermal performance and other design constraints when determining the optimal aluminum thickness for their specific application.
3. Surface Finishing
The surface finishing applied to the aluminum substrate can also impact its thermal conductivity. Various surface treatments, such as anodizing, plating, or coating, are commonly used to improve the corrosion resistance, electrical insulation, and aesthetic appearance of PCBs.
However, some surface treatments can create a thermal barrier, reducing the overall thermal conductivity of the aluminum substrate. For example, anodizing, which is a process of creating a protective oxide layer on the aluminum surface, can slightly decrease the thermal conductivity due to the insulating properties of the oxide layer.
On the other hand, certain surface treatments, like electroless nickel immersion gold (ENIG) plating, have minimal impact on thermal conductivity. ENIG provides a thin, uniform layer of nickel and gold on the aluminum surface, preserving its thermal conductivity while enhancing its corrosion resistance and solderability.
When selecting a surface finishing for PCBs, designers must consider the trade-offs between thermal performance, corrosion resistance, electrical insulation, and manufacturing cost.
4. PCB Layout and Design
The layout and design of the PCB itself can significantly influence the effectiveness of aluminum thermal conductivity. Proper placement of heat-generating components, such as high-power ICs or power transistors, is crucial for optimal heat dissipation.
Designers should consider the following factors when designing PCBs for effective thermal management:
-
Component Placement: Heat-generating components should be strategically placed on the PCB to minimize thermal hotspots and ensure even heat distribution. Placing components too close together can lead to localized heat buildup, while spacing them too far apart can increase the overall size of the PCB.
-
Thermal Vias: Thermal vias are conductive pathways that provide a direct route for heat to transfer from the PCB surface to the aluminum substrate. By strategically placing thermal vias near heat-generating components, designers can enhance the thermal conductivity and improve overall heat dissipation.
-
Copper Thickness: The thickness of the copper traces on the PCB can also impact thermal conductivity. Thicker copper traces provide a larger cross-sectional area for heat conduction, allowing for more efficient heat transfer from the components to the aluminum substrate.
-
Thermal Interface Materials: Thermal interface materials (TIMs), such as thermal pads or thermal adhesives, are often used to improve the thermal contact between the PCB and the aluminum substrate. TIMs help to fill any air gaps and ensure efficient heat transfer, enhancing the overall thermal conductivity of the PCB assembly.
By optimizing the PCB layout and design, designers can maximize the benefits of aluminum thermal conductivity and ensure effective heat dissipation throughout the electronic device.
5. Environmental Factors
Environmental factors, such as ambient temperature and humidity, can also influence the thermal conductivity of aluminum in PCBs. As the ambient temperature increases, the thermal conductivity of aluminum decreases slightly due to increased lattice vibrations and phonon scattering.
The relationship between thermal conductivity and temperature can be approximated using the following equation:
k(T) = k₀ / (1 + α × (T - T₀))
Where:
– k(T) is the thermal conductivity at temperature T
– k₀ is the thermal conductivity at a reference temperature T₀
– α is the temperature coefficient of thermal conductivity (typically a small positive value)
From the equation, it is evident that as the temperature (T) increases, the thermal conductivity (k) decreases.
Humidity can also affect the thermal conductivity of aluminum, especially in environments with high moisture content. Moisture can lead to corrosion and oxidation of the aluminum surface, which can create a thermal barrier and reduce the overall thermal conductivity.
To mitigate the impact of environmental factors on PCB aluminum thermal conductivity, designers should consider the following:
-
Operating Temperature Range: Ensure that the selected aluminum alloy and PCB design can withstand the expected operating temperature range of the electronic device. This includes considering the maximum and minimum temperature limits, as well as any thermal cycling requirements.
-
Conformal Coating: Applying a conformal coating to the PCB can help protect the aluminum surface from moisture and corrosion. Conformal coatings act as a barrier, preventing moisture ingress and maintaining the thermal conductivity of the aluminum substrate over time.
-
Thermal Management Systems: In environments with high ambient temperatures or humidity, additional thermal management systems, such as heatsinks, fans, or liquid cooling, may be necessary to supplement the aluminum thermal conductivity and ensure effective heat dissipation.
By considering the environmental factors and implementing appropriate mitigation strategies, designers can ensure that the PCB aluminum thermal conductivity remains effective throughout the lifecycle of the electronic device.
Conclusion
PCB aluminum thermal conductivity is a critical factor in the thermal management of electronic devices. By understanding the key factors that influence aluminum thermal conductivity, designers and manufacturers can optimize the PCB design to ensure effective heat dissipation and maintain the reliability and performance of electronic components.
The main factors affecting PCB aluminum thermal conductivity include the aluminum alloy composition, aluminum thickness, surface finishing, PCB layout and design, and environmental factors. Each of these factors plays a significant role in determining the overall thermal performance of the PCB.
To maximize the benefits of PCB aluminum thermal conductivity, designers should carefully consider the specific requirements of their application and select the appropriate aluminum alloy, thickness, and surface finishing. They should also optimize the PCB layout and design, incorporating thermal vias, strategic component placement, and thermal interface materials to enhance heat dissipation.
Furthermore, designers must take into account the environmental factors, such as ambient temperature and humidity, and implement necessary mitigation strategies, like conformal coating or additional thermal management systems, to ensure the long-term effectiveness of the PCB aluminum thermal conductivity.
By understanding and addressing these factors, designers and manufacturers can create PCBs with optimal thermal performance, ensuring the reliability, longevity, and overall success of electronic devices in various applications.
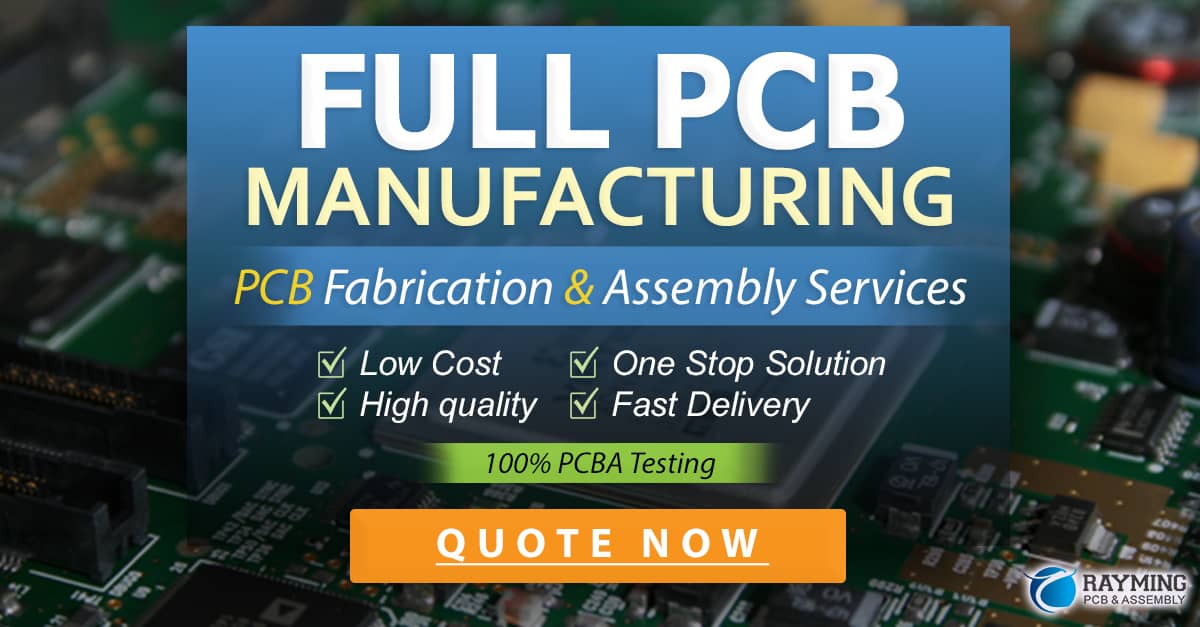
Frequently Asked Questions (FAQ)
-
What is PCB aluminum thermal conductivity?
PCB aluminum thermal conductivity refers to the ability of aluminum, used as a substrate material in PCBs, to conduct heat away from electronic components. It is a measure of how effectively aluminum can transfer heat, helping to maintain the optimal operating temperature of the components. -
Why is PCB aluminum thermal conductivity important?
PCB aluminum thermal conductivity is crucial for the thermal management of electronic devices. As electronic components generate heat during operation, effective heat dissipation is necessary to prevent overheating and ensure the reliability and longevity of the components. Aluminum’s excellent thermal conductivity properties make it a suitable substrate material for PCBs, helping to efficiently transfer heat away from the components. -
What are the main factors affecting PCB aluminum thermal conductivity?
The main factors affecting PCB aluminum thermal conductivity include: - Aluminum alloy composition
- Aluminum thickness
- Surface finishing
- PCB layout and design
- Environmental factors (ambient temperature and humidity)
Each of these factors plays a significant role in determining the overall thermal performance of the PCB and must be carefully considered during the design and manufacturing process.
- How can designers optimize PCB layout and design for better thermal conductivity?
Designers can optimize the PCB layout and design for better thermal conductivity by considering the following: - Strategic placement of heat-generating components to minimize thermal hotspots
- Incorporation of thermal vias to provide direct heat transfer pathways
- Selection of appropriate copper thickness for efficient heat conduction
- Use of thermal interface materials to enhance thermal contact between the PCB and aluminum substrate
By implementing these design strategies, designers can maximize the benefits of aluminum thermal conductivity and ensure effective heat dissipation throughout the electronic device.
- How can environmental factors impact PCB aluminum thermal conductivity?
Environmental factors, such as ambient temperature and humidity, can impact PCB aluminum thermal conductivity in the following ways: - Increased ambient temperature can slightly decrease the thermal conductivity of aluminum due to increased lattice vibrations and phonon scattering.
- High humidity can lead to corrosion and oxidation of the aluminum surface, creating a thermal barrier and reducing the overall thermal conductivity.
To mitigate the impact of environmental factors, designers can select aluminum alloys and PCB designs that can withstand the expected operating temperature range, apply conformal coatings to protect against moisture and corrosion, and implement additional thermal management systems, such as heatsinks or fans, to supplement the aluminum thermal conductivity.
0 Comments