Understanding the Importance of Thermal Management
In modern electronic devices, the increasing power density and miniaturization of components have led to significant challenges in managing the heat generated during operation. Excessive heat can cause various issues, such as:
- Reduced performance and efficiency
- Decreased reliability and lifespan of components
- Potential damage to sensitive electronic elements
Effective thermal management is essential to address these challenges and ensure the proper functioning of electronic devices. Sink-pad copper substrates have emerged as a key solution for dissipating heat and maintaining optimal operating temperatures.
Composition and Structure of Sink-Pad Copper Substrates
Sink-pad copper substrates are typically composed of a copper base material that offers excellent thermal conductivity. Copper is chosen for its ability to efficiently transfer heat away from the electronic components. The substrate may also include additional layers or features to enhance its thermal management capabilities.
Copper Base Material
The copper base material used in Sink-Pad Substrates is selected for its high thermal conductivity, which allows for rapid heat dissipation. Copper has a thermal conductivity of approximately 400 W/mK, making it one of the most effective materials for thermal management in electronic packaging.
The thickness of the copper base can vary depending on the specific application and the amount of heat generated by the electronic components. Thicker copper bases provide better heat spreading and dissipation, but they also increase the overall thickness and weight of the substrate.
Insulation Layer
In some sink-pad copper substrates, an insulation layer is added to electrically isolate the copper base from the electronic components. This layer is typically made of a dielectric material, such as polyimide or epoxy, which provides electrical insulation while allowing heat to pass through.
The insulation layer helps prevent electrical short circuits and ensures the proper functioning of the electronic device. It is important to select an insulation material with good thermal conductivity to minimize the thermal resistance between the copper base and the electronic components.
Surface Finish
The surface finish of sink-pad copper substrates plays a crucial role in enhancing thermal transfer and ensuring reliable soldering of electronic components. Common surface finishes include:
- Organic Solderability Preservative (OSP): A thin, organic coating that prevents oxidation and improves solderability.
- Electroless Nickel Immersion Gold (ENIG): A layer of electroless nickel followed by a thin layer of immersion gold, providing excellent solderability and corrosion resistance.
- Immersion Tin (IT): A thin layer of tin applied through immersion, offering good solderability and cost-effectiveness.
The choice of surface finish depends on the specific requirements of the application, such as solderability, corrosion resistance, and compatibility with the assembly process.
Thermal Performance of Sink-Pad Copper Substrates
The thermal performance of sink-pad copper substrates is a critical factor in their effectiveness for heat dissipation. Several key parameters influence the thermal performance of these substrates:
Thermal Conductivity
Thermal conductivity is a measure of a material’s ability to conduct heat. As mentioned earlier, copper has a high thermal conductivity, making it an excellent choice for sink-pad substrates. The higher the thermal conductivity, the more efficiently heat can be transferred away from the electronic components.
Thermal Resistance
Thermal resistance is the measure of a material’s resistance to heat flow. In sink-pad copper substrates, the goal is to minimize thermal resistance to allow for efficient heat dissipation. Factors that affect thermal resistance include:
- Substrate thickness: Thicker substrates generally have lower thermal resistance, allowing for better heat spreading and dissipation.
- Surface roughness: A smooth surface finish helps reduce thermal resistance by improving contact between the substrate and the electronic components.
- Interface materials: The use of thermal interface materials, such as thermal greases or pads, can help reduce thermal resistance at the interface between the substrate and the components.
Heat Spreading
Heat spreading refers to the ability of the sink-pad copper substrate to distribute heat evenly across its surface. Effective heat spreading helps prevent hot spots and ensures uniform temperature distribution, which is crucial for maintaining the reliability and performance of electronic components.
The heat spreading capability of a sink-pad copper substrate depends on factors such as the thermal conductivity of the copper base, the substrate thickness, and the presence of any additional heat spreading layers or features.
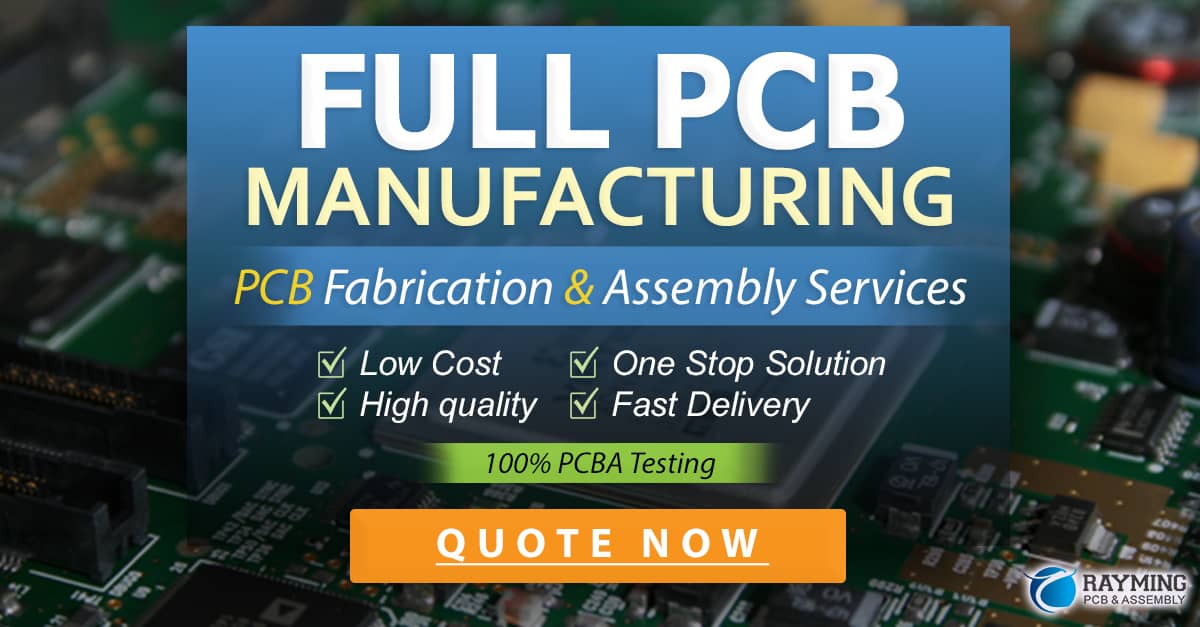
Manufacturing Process of Sink-Pad Copper Substrates
The manufacturing process of sink-pad copper substrates involves several key steps to ensure the desired thermal performance and reliability. The basic steps include:
-
Copper Lamination: The copper base material is laminated onto a dielectric substrate, such as a printed circuit board (PCB) or a ceramic substrate. The lamination process involves applying heat and pressure to bond the copper to the substrate.
-
Patterning and Etching: The desired circuit pattern is created on the copper layer through a photolithography process. The unwanted copper areas are etched away, leaving behind the required circuit traces and pads.
-
Insulation Layer Application: If an insulation layer is required, it is applied over the copper circuit pattern. The insulation layer can be applied through various methods, such as screen printing, spray coating, or lamination.
-
Surface Finish Application: The chosen surface finish, such as OSP, ENIG, or IT, is applied to the exposed copper areas. This step enhances solderability and provides protection against oxidation and corrosion.
-
Singulation: The substrate panel is cut into individual sink-pad copper substrates using methods such as dicing or routing.
Throughout the manufacturing process, strict quality control measures are implemented to ensure consistent thermal performance and reliability of the substrates.
Applications of Sink-Pad Copper Substrates
Sink-pad copper substrates find applications in various electronic packaging scenarios where efficient thermal management is crucial. Some common applications include:
Power Electronics
In power electronic devices, such as power amplifiers, voltage regulators, and motor drives, sink-pad copper substrates are used to dissipate the heat generated by high-power components. The substrates help maintain the temperature within acceptable limits, preventing overheating and ensuring reliable operation.
High-Performance Computing
High-performance computing systems, such as data centers and supercomputers, generate significant amounts of heat due to the high density of electronic components. Sink-pad copper substrates are used to effectively dissipate heat from processors, memory modules, and other heat-generating components, maintaining optimal performance and system stability.
Automotive Electronics
In the automotive industry, electronic components are subjected to harsh environmental conditions and high-temperature operation. Sink-pad copper substrates are used in various automotive electronic systems, such as engine control units, power electronics, and infotainment systems, to ensure reliable thermal management and long-term durability.
LED Lighting
High-power LED lighting applications require efficient heat dissipation to maintain the performance and lifespan of the LEDs. Sink-pad copper substrates are used as heat sinks in LED lighting modules, helping to transfer heat away from the LEDs and prevent premature degradation.
Telecommunications
In telecommunications equipment, such as base stations and routers, sink-pad copper substrates are used to manage the heat generated by high-frequency and high-power components. Effective thermal management helps ensure uninterrupted operation and reliable data transmission.
Advantages of Sink-Pad Copper Substrates
Sink-pad copper substrates offer several advantages over traditional thermal management solutions:
-
Excellent Thermal Conductivity: Copper’s high thermal conductivity enables efficient heat dissipation, helping to maintain optimal operating temperatures for electronic components.
-
Customizable Design: Sink-pad copper substrates can be customized to meet specific application requirements, such as different sizes, shapes, and thicknesses, allowing for optimal thermal performance and integration into various electronic packages.
-
Reliability: The use of sink-pad copper substrates enhances the reliability of electronic devices by preventing overheating and thermal-related failures. The substrates help ensure consistent performance and extend the lifespan of components.
-
Cost-Effectiveness: Compared to other advanced thermal management solutions, such as diamond or ceramic substrates, sink-pad copper substrates offer a cost-effective option for achieving efficient heat dissipation in electronic packaging.
-
Compatibility with Standard Manufacturing Processes: Sink-pad copper substrates can be manufactured using standard PCB fabrication processes, making them easily integrable into existing production lines and reducing implementation costs.
Future Trends and Developments
As electronic devices continue to advance, the demand for effective thermal management solutions, such as sink-pad copper substrates, is expected to grow. Some future trends and developments in this field include:
-
Advanced Materials: Research is ongoing to explore new materials and composite structures that can further enhance the thermal performance of sink-pad substrates. Materials with higher thermal conductivity and lower thermal resistance are being investigated to meet the increasing thermal management requirements of future electronic devices.
-
Integration with Advanced Packaging Technologies: Sink-pad copper substrates are being adapted to integrate with advanced packaging technologies, such as 3D packaging, through-silicon vias (TSVs), and embedded die packaging. These integrations allow for more efficient thermal management in high-density electronic packages.
-
Thermal Interface Material Optimization: Advancements in thermal interface materials, such as high-performance thermal greases, phase change materials, and low-melting-point alloys, are being explored to further reduce thermal resistance and improve the overall thermal performance of sink-pad copper substrates.
-
Simulation and Modeling: The use of advanced simulation and modeling techniques is becoming increasingly important in the design and optimization of sink-pad copper substrates. These tools help predict thermal behavior, identify potential hot spots, and optimize substrate design for specific applications, enabling more efficient and reliable thermal management solutions.
Frequently Asked Questions (FAQ)
- What is the primary function of sink-pad copper substrates in electronic packaging?
-
The primary function of sink-pad copper substrates is to dissipate heat generated by electronic components, helping to maintain optimal operating temperatures and ensure reliable performance.
-
Why is copper chosen as the base material for sink-pad substrates?
-
Copper is chosen as the base material for sink-pad substrates due to its high thermal conductivity (approximately 400 W/mK), which enables efficient heat transfer and dissipation from electronic components.
-
What is the purpose of the insulation layer in sink-pad copper substrates?
-
The insulation layer in sink-pad copper substrates electrically isolates the copper base from the electronic components, preventing short circuits while still allowing heat to pass through. It is typically made of a dielectric material with good thermal conductivity.
-
How does the surface finish of sink-pad copper substrates affect their performance?
-
The surface finish of sink-pad copper substrates, such as OSP, ENIG, or IT, enhances solderability, prevents oxidation, and ensures reliable bonding with electronic components. The choice of surface finish depends on the specific application requirements.
-
What are some common applications of sink-pad copper substrates?
- Sink-pad copper substrates are commonly used in various applications where efficient thermal management is crucial, such as power electronics, high-performance computing, automotive electronics, LED lighting, and telecommunications equipment.
Conclusion
Sink-pad copper substrates play a vital role in the thermal management of electronic devices, ensuring optimal performance, reliability, and longevity. By leveraging the high thermal conductivity of copper and specialized manufacturing processes, these substrates effectively dissipate heat generated by electronic components.
As electronic devices continue to advance, the demand for efficient thermal management solutions like sink-pad copper substrates will only increase. Ongoing research and development in materials, manufacturing processes, and integration with advanced packaging technologies will further enhance the capabilities of these substrates in meeting the thermal challenges of future electronic devices.
By understanding the composition, thermal performance, manufacturing process, and applications of sink-pad copper substrates, engineers and designers can make informed decisions when selecting thermal management solutions for their electronic packaging needs.
Parameter | Description |
---|---|
Thermal Conductivity | The ability of a material to conduct heat, measured in W/mK. Higher values indicate better heat transfer. |
Thermal Resistance | The measure of a material’s resistance to heat flow, measured in K/W. Lower values indicate better thermal performance. |
Surface Finish | The coating applied to the exposed copper areas, such as OSP, ENIG, or IT, to enhance solderability and protect against oxidation. |
Insulation Layer | A dielectric material layer that electrically isolates the copper base from electronic components while allowing heat to pass through. |
Heat Spreading | The ability of the substrate to distribute heat evenly across its surface, preventing hot spots and ensuring uniform temperature distribution. |
By considering these key parameters and understanding their impact on thermal management, designers can optimize the performance of sink-pad copper substrates in their electronic packaging applications.
0 Comments