Introduction to Multi-layer Boards
Multi-layer boards, also known as multilayer printed circuit boards (PCBs), are essential components in modern electronics. These complex structures consist of multiple layers of conductive copper sheets separated by insulating materials, allowing for dense and efficient routing of electrical signals within a compact space. The use of multi-layer boards has revolutionized the electronics industry, enabling the development of smaller, faster, and more powerful devices.
Key Features of Multi-layer Boards
- Multiple copper layers for complex circuitry
- Insulating layers to prevent short circuits
- Through-hole vias and blind vias for inter-layer connections
- High signal integrity and reduced electromagnetic interference (EMI)
- Compact size and increased functionality
Advantages of Using Multi-layer Boards
Space Savings and Miniaturization
One of the primary advantages of using multi-layer boards is the ability to save space and achieve miniaturization. By stacking multiple layers of circuitry, designers can create complex circuits within a smaller footprint compared to single-layer or double-layer boards. This is particularly important in today’s electronic devices, where consumers demand smaller, more portable products without compromising functionality.
Improved Signal Integrity
Multi-layer boards offer improved signal integrity compared to their single-layer counterparts. The use of dedicated ground and power planes helps to reduce electromagnetic interference (EMI) and crosstalk between signals. By carefully designing the layer stack-up and routing signals strategically, engineers can minimize signal distortion and ensure reliable performance, even at high frequencies.
Increased Reliability
The construction of multi-layer boards contributes to their increased reliability. The insulating layers between the conductive copper layers prevent short circuits and provide mechanical stability to the board. Additionally, the use of through-hole vias and blind vias for inter-layer connections ensures robust electrical connections, reducing the risk of failures due to poor connectivity.
Enhanced Thermal Management
Multi-layer boards can be designed with thermal management in mind. By incorporating dedicated layers for heat dissipation, such as ground planes or thermal vias, designers can effectively distribute and dissipate heat generated by components. This helps to prevent overheating and ensures the long-term reliability of the electronic device.
Manufacturing Process of Multi-layer Boards
Layer Stack-up Design
The first step in manufacturing a multi-layer board is designing the layer stack-up. This involves determining the number of layers required, the thickness of each layer, and the arrangement of conductive and insulating materials. The stack-up design must consider factors such as signal integrity, impedance control, and manufacturability.
Lamination and Drilling
Once the layer stack-up is finalized, the individual layers are laminated together using heat and pressure. The resulting multi-layer structure is then drilled to create through-holes for component placement and inter-layer connections. Precise drilling is crucial to ensure accurate alignment of the layers and proper connectivity.
Plating and Etching
After drilling, the through-holes are plated with conductive material, typically copper, to establish electrical connections between layers. The outer layers of the board are then etched to create the desired circuit patterns. This process involves applying a photoresist coating, exposing it to UV light through a patterned mask, and then chemically removing the unwanted copper.
Solder Mask and Silkscreen Application
A solder mask, usually green in color, is applied to the outer layers of the multi-layer board to protect the circuitry from damage and prevent accidental short circuits during soldering. The solder mask also helps to improve the board’s aesthetic appearance. Finally, a silkscreen layer is added to provide text and symbols for component placement and identification.
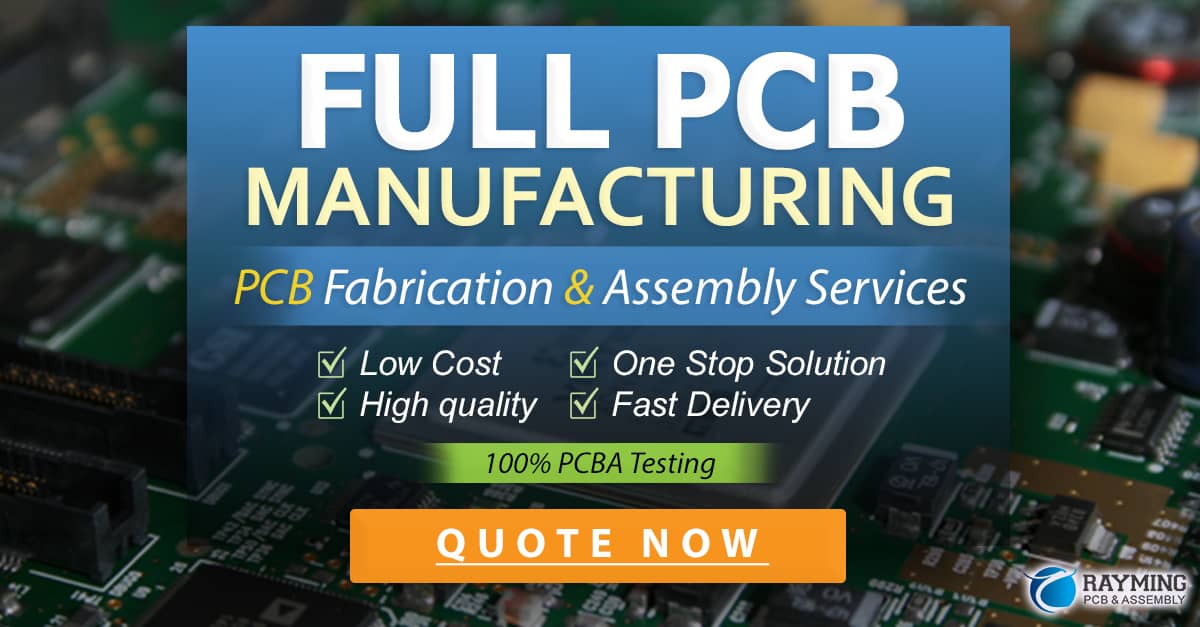
Applications of Multi-layer Boards
Consumer Electronics
Multi-layer boards are widely used in consumer electronics, such as smartphones, tablets, laptops, and wearable devices. The compact size and high functionality enabled by multi-layer boards are essential for creating feature-rich, portable devices that meet consumer demands.
Automotive Electronics
The automotive industry heavily relies on multi-layer boards for various electronic systems, including engine control units (ECUs), infotainment systems, and advanced driver assistance systems (ADAS). The harsh operating environment in vehicles necessitates the use of robust and reliable multi-layer boards that can withstand extreme temperatures, vibrations, and electromagnetic interference.
Medical Devices
Multi-layer boards are crucial components in medical devices, such as implantable devices, diagnostic equipment, and patient monitoring systems. The high reliability and signal integrity provided by multi-layer boards ensure the accurate and safe operation of these life-critical devices.
Aerospace and Defense
Aerospace and defense applications require multi-layer boards that can withstand extreme environmental conditions and meet stringent reliability requirements. These boards are used in avionics systems, communication equipment, and radar systems, where failure is not an option.
Challenges and Considerations in Multi-layer Board Design
Signal Integrity and Crosstalk
Maintaining signal integrity and minimizing crosstalk are significant challenges in multi-layer board design. As the number of layers increases, the potential for signal degradation and interference also rises. Designers must carefully consider factors such as trace routing, impedance matching, and layer stack-up to ensure optimal signal quality.
Thermal Management
Effective thermal management is essential in multi-layer boards, particularly those with high power densities. Designers must incorporate appropriate thermal management techniques, such as the use of thermal vias, heat spreaders, and adequate copper coverage, to dissipate heat efficiently and prevent component failure due to overheating.
Manufacturing Complexity and Cost
The complexity of multi-layer boards increases with the number of layers, leading to higher manufacturing costs compared to single-layer or double-layer boards. The lamination process, drilling, and plating require precise control and specialized equipment, which can impact production time and cost. Designers must strike a balance between functionality, reliability, and cost-effectiveness when developing multi-layer board solutions.
Future Trends in Multi-layer Board Technology
High-Density Interconnect (HDI) Boards
High-Density Interconnect (HDI) boards represent an advancement in multi-layer board technology. These boards feature finer trace widths, smaller vias, and higher layer counts, enabling even greater miniaturization and functionality. HDI boards are becoming increasingly popular in applications that demand ultra-compact and high-performance electronics.
Embedded Components
Embedding components within the layers of a multi-layer board is an emerging trend that offers several benefits. By placing components such as resistors, capacitors, and even active devices inside the board, designers can save space on the surface, reduce the overall package size, and improve signal integrity. Embedded component technology is expected to gain traction in the coming years.
3D Printing of Multi-layer Boards
3D printing technology is making inroads into the manufacturing of multi-layer boards. Additive manufacturing techniques, such as inkjet printing and aerosol jet printing, allow for the creation of complex, three-dimensional circuit structures. This approach offers greater design flexibility, faster prototyping, and the potential for customized, on-demand production of multi-layer boards.
Frequently Asked Questions (FAQ)
1. What is the difference between a multi-layer board and a single-layer board?
A single-layer board consists of a single conductive layer on one side of an insulating substrate, while a multi-layer board has multiple conductive layers separated by insulating layers. Multi-layer boards offer higher circuit density, improved signal integrity, and better thermal management compared to single-layer boards.
2. How many layers can a multi-layer board have?
The number of layers in a multi-layer board can vary depending on the application and design requirements. Commonly used multi-layer boards have four, six, or eight layers, but some complex designs may feature up to 50 layers or more.
3. What materials are used in the construction of multi-layer boards?
Multi-layer boards typically consist of copper foil for the conductive layers and a dielectric material, such as FR-4 (a glass-reinforced epoxy laminate), for the insulating layers. Other materials, such as polyimide or ceramic, may be used for specialized applications that require high temperature resistance or low dielectric constant.
4. How are the layers interconnected in a multi-layer board?
The layers in a multi-layer board are interconnected through vias, which are conductive pathways that run perpendicular to the layers. There are different types of vias, such as through-hole vias (which go through all layers), blind vias (which connect only some layers), and buried vias (which are hidden within the board and do not reach the surface).
5. What are the key factors to consider when designing a multi-layer board?
When designing a multi-layer board, several key factors must be considered, including:
- Layer stack-up and material selection
- Signal integrity and crosstalk prevention
- Impedance control and matching
- Thermal management and power distribution
- Component placement and routing
- Manufacturing feasibility and cost
Careful consideration of these factors is essential to ensure the optimal performance, reliability, and cost-effectiveness of the multi-layer board.
Conclusion
Multi-layer boards have revolutionized the electronics industry, enabling the development of smaller, faster, and more powerful devices. By offering high circuit density, improved signal integrity, and enhanced thermal management, multi-layer boards have become indispensable in a wide range of applications, from consumer electronics to aerospace and defense.
As technology continues to advance, the demand for even more complex and sophisticated multi-layer boards will grow. Emerging trends, such as High-Density Interconnect (HDI) boards, embedded components, and 3D printing, are expected to shape the future of multi-layer board technology, offering new opportunities for innovation and advancement.
Understanding the fundamentals of multi-layer boards, their manufacturing process, and the challenges and considerations in their design is essential for engineers, designers, and decision-makers in the electronics industry. By staying informed about the latest developments and best practices in multi-layer board technology, professionals can create cutting-edge electronic solutions that meet the ever-increasing demands of the modern world.
0 Comments